I. Definição
A galvanoplastia é um tipo de processo de eletrodeposição de metal. Envolve a redução da descarga de íons metálicos simples ou íons complexos por meio de métodos eletroquímicos na superfície de um sólido (condutor ou semicondutor), resultando na aderência de átomos metálicos à superfície do eletrodo para formar uma camada metálica.
II. Propósito
A galvanoplastia altera as propriedades da superfície dos sólidos, alterando assim sua aparência, aumentando a resistência à corrosão, a resistência ao desgaste e a dureza, e conferindo propriedades especiais de superfície óptica, elétrica, magnética e térmica.
III. Introdução à galvanoplastia terminal
A maioria dos conectores e terminais eletrônicos passam por tratamento de superfície, normalmente galvanoplastia, por dois motivos principais: primeiro, para proteger o material da mola do terminal contra corrosão; segundo, otimizar o desempenho da superfície terminal, estabelecendo e mantendo a interface de contato entre os terminais, especialmente em termos de controle da camada de filme. Em outras palavras, para facilitar o contato metal com metal.
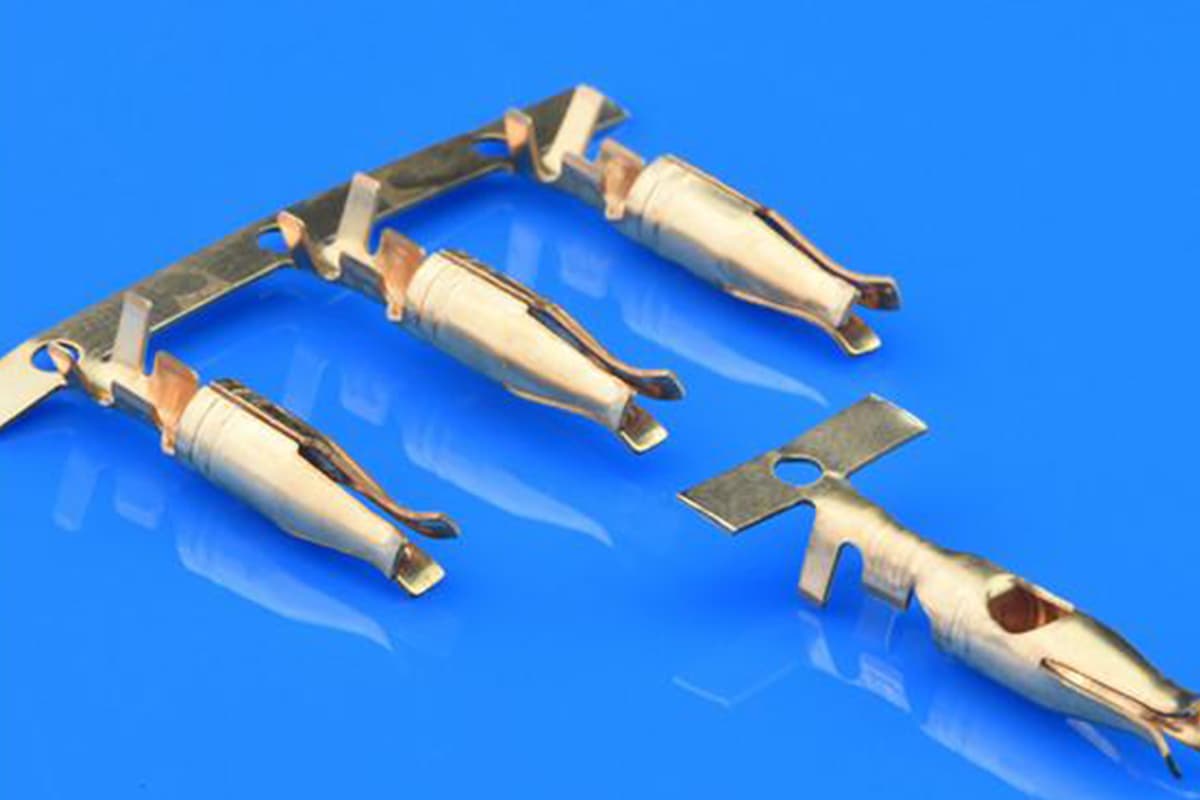
Prevenção de corrosão:
A maioria das molas do conector é feita de liga de cobre, que pode sofrer corrosão no ambiente operacional, como por oxidação e sulfetação. A galvanoplastia terminal isola a mola do ambiente, evitando corrosão. Os materiais de galvanoplastia devem ser resistentes à corrosão, pelo menos dentro do ambiente de aplicação.
Otimização de superfície:
A otimização das propriedades da superfície terminal pode ser alcançada de duas maneiras. Uma delas é através do design do conector, estabelecendo e mantendo uma interface de contato estável. A outra é estabelecendo contato metálico, exigindo que qualquer filme superficial seja inexistente ou se rompa na inserção. A distinção entre não ter filme e ruptura do filme diferencia o revestimento de metais preciosos do revestimento de metais não preciosos.
O revestimento de metais preciosos, como ouro, paládio e suas ligas, é inerte e não possui camada de filme inerente. Portanto, para estes tratamentos de superfície, o contato metálico é “automático”. A consideração então passa a ser como manter a nobreza da superfície terminal, protegendo-a de fatores externos como contaminação, difusão do substrato e corrosão terminal.
O revestimento de metais não preciosos, particularmente estanho e chumbo e suas ligas, é coberto por uma película de óxido que se rompe facilmente após a inserção, estabelecendo assim uma área de contato metálico.
(1) Revestimento terminal de metal precioso
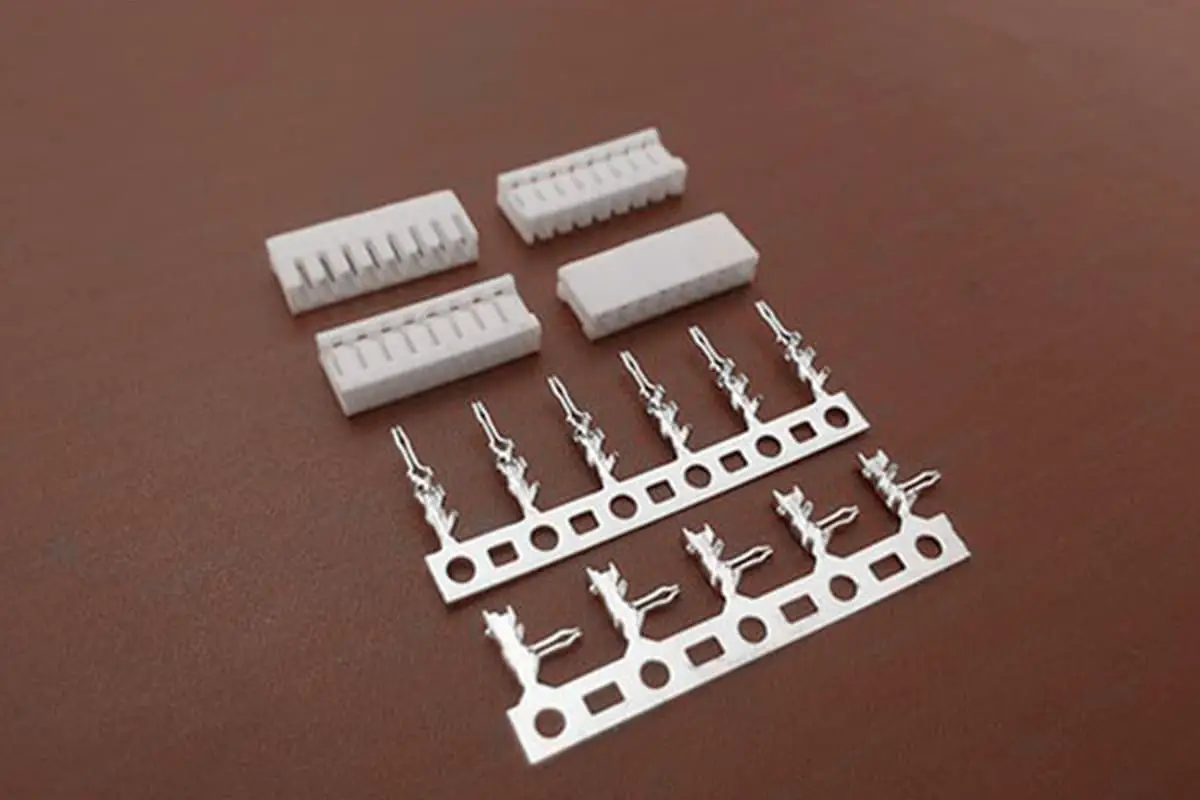
O revestimento terminal de metal precioso envolve cobrir a superfície subjacente, normalmente níquel, com um metal precioso. As espessuras padrão do revestimento do conector são de 15 a 50 mícrons para ouro e de 50 a 100 mícrons para níquel. Os metais preciosos mais comumente usados para revestimento são ouro, paládio e suas ligas.
O ouro é o material de revestimento ideal devido à sua excelente condutividade e propriedades térmicas, bem como à sua resistência à corrosão em qualquer ambiente. Devido a essas vantagens, o revestimento de ouro é predominantemente usado em conectores para aplicações que exigem alta confiabilidade, embora o ouro seja caro.
O paládio, também um metal precioso, possui maior resistência, menor transferência térmica e menor resistência à corrosão em comparação ao ouro, mas oferece resistência superior ao desgaste. Ligas de paládio-níquel (proporção 80-20) são geralmente usadas nos terminais de conectores.
Ao projetar o revestimento de metais preciosos, os seguintes fatores devem ser considerados:
a. Porosidade
Durante o processo de galvanização, o ouro nuclea em numerosos contaminantes da superfície exposta. Esses núcleos continuam a crescer e a se espalhar pela superfície, eventualmente colidindo e cobrindo completamente a superfície, resultando em um revestimento poroso.
A porosidade de uma camada de ouro está relacionada com a sua espessura. Abaixo de 15 mícrons, a porosidade aumenta rapidamente, enquanto acima de 50 mícrons, a porosidade permanece baixa e a taxa de diminuição é insignificante. Isso explica por que a espessura do revestimento de metal precioso está normalmente na faixa de 15 a 50 mícrons.
A porosidade também está relacionada a defeitos do substrato como inclusões, laminação, marcas de carimbo, limpeza inadequada após a estampagem e lubrificação incorreta.
b. Vestir
O desgaste na superfície chapeada pode levar à exposição do material de base. O desgaste ou longevidade da superfície revestida depende de duas características do tratamento superficial: o coeficiente de atrito e a dureza. À medida que a dureza aumenta e o coeficiente de atrito diminui, a vida útil do tratamento de superfície melhora.
O ouro galvanizado é geralmente ouro duro, contendo ativadores de endurecimento como o cobalto (Co), o agente de endurecimento mais comum, que aumenta a resistência ao desgaste do ouro. A escolha do revestimento de paládio-níquel pode melhorar significativamente a resistência ao desgaste e a longevidade do revestimento de metal precioso.
Normalmente, uma camada de ouro de 3 mícrons é aplicada sobre uma liga de paládio-níquel de 20-30 mícrons, proporcionando boa condutividade e alta durabilidade. Além disso, uma camada inferior de níquel é frequentemente usada para prolongar ainda mais a vida útil.
c. Camada inferior de níquel
A camada inferior de níquel é uma consideração primária no revestimento de metais preciosos, fornecendo diversas funções importantes para garantir a integridade da interface de contato do terminal.
Ao oferecer uma camada de barreira eficaz através de uma superfície positivamente oxidada, o níquel reduz o potencial de corrosão por porosidade e fornece uma camada de suporte rígida sob o revestimento de metal precioso, aumentando assim a vida útil do revestimento. Qual é a espessura adequada para esta camada?
Quanto mais espessa a camada inferior de níquel, menor o desgaste, mas em termos de custo e controle da rugosidade da superfície, geralmente é escolhida uma espessura de 50-100 mícrons.
(2) Revestimento de metais não preciosos
O revestimento de metais não preciosos difere daquele de metais preciosos, pois sempre envolve um certo número de camadas de película superficial. Para conectores que visam fornecer e manter uma interface de contato metálica, a presença destas películas deve ser levada em consideração.
Normalmente, para revestimentos de metais não preciosos, é necessária uma alta força de contato para quebrar o filme, garantindo assim a integridade da interface de contato do terminal. A ação de esfrega também é crucial para superfícies terminais com camadas de filme.
Existem três tipos de tratamentos de superfície sem ouro no revestimento de terminais: estanho (liga de estanho-chumbo), prata e níquel. O estanho é o mais comumente usado, a prata se destaca em aplicações de alta corrente e o níquel é reservado para ambientes de alta temperatura.
a. Tratamento de superfície de estanho
O estanho também se refere a ligas de estanho-chumbo, especialmente a liga de estanho 93-chumbo 3.
O uso do tratamento superficial do estanho decorre do fato de que a película de óxido de estanho é facilmente rompida. Um revestimento de estanho terá uma camada de filme de óxido duro, fino e quebradiço em sua superfície. Abaixo da camada de óxido está o estanho macio. Quando uma força positiva atua sobre o filme, o óxido de estanho, por ser fino, não suporta a carga e, devido à sua fragilidade, racha facilmente.
Nessas condições, a carga é transferida para a camada de estanho, que, por ser macia e maleável, flui facilmente sob pressão. À medida que o estanho flui, as fissuras no óxido aumentam. Através dessas rachaduras e da camada intermediária, o estanho é espremido para a superfície, proporcionando contato metálico. Nas ligas de estanho-chumbo, o papel do chumbo é reduzir a formação de bigodes de estanho.
Os bigodes de estanho se formam como fios monocristalinos na superfície do estanho folheado sob tensão, podendo causar curtos-circuitos entre os terminais. Adicionar 2% ou mais de chumbo pode reduzir a formação de bigodes. Outra proporção comum de liga de estanho-chumbo é 60:40, semelhante à proporção da composição da solda (63:37), usada principalmente em conectores que requerem soldagem.
No entanto, a legislação recente exige cada vez mais a redução do teor de chumbo em produtos electrónicos e eléctricos, levando a um aumento na procura de revestimentos sem chumbo, tais como estanho puro, estanho/cobre e estanho/prata. O crescimento dos bigodes de estanho pode ser retardado pelo revestimento de uma camada de níquel entre as camadas de cobre e estanho ou usando uma superfície de estanho fosca e não brilhante.
b. Revestimento de superfície prateado
A prata é considerada um tratamento de superfície de metal não precioso porque reage com enxofre e cloro para formar uma película de sulfeto. Este filme de sulfeto atua como um semicondutor e pode exibir características semelhantes às do diodo.
A prata também é macia, comparável ao ouro macio. Como o sulfeto não é facilmente rompido, a prata está livre de corrosão por atrito. Com excelente condutividade elétrica e térmica, a prata não derrete sob altas correntes, tornando-a uma excelente escolha para tratamentos de superfície de terminais de alta corrente.
(3) Lubrificação Terminal
A lubrificação desempenha diferentes funções dependendo do tratamento superficial do terminal, servindo principalmente duas funções: reduzir o coeficiente de atrito e proporcionar isolamento ambiental.
A redução do coeficiente de atrito traz dois benefícios: primeiro, diminui a força de inserção necessária para os conectores; em segundo lugar, prolonga a vida útil do conector, minimizando o desgaste. A lubrificação terminal pode formar uma camada protetora que evita ou retarda a degradação ambiental da interface de contato, proporcionando assim isolamento.
Normalmente, para tratamentos de superfície de metais preciosos, a lubrificação é usada para reduzir o atrito e aumentar a longevidade do conector. No caso de tratamentos de superfície de estanho, proporciona isolamento ambiental para evitar corrosão por contato. Embora lubrificantes possam ser aplicados no processo de pós-galvanização, trata-se apenas de uma medida adicional.
Para conectores que precisam ser soldados em placas PCB, o processo de limpeza da soldagem pode remover o lubrificante. Os lubrificantes atraem poeira, que, em um ambiente empoeirado, pode levar ao aumento da resistência elétrica e à redução da vida útil. Por último, a resistência à temperatura dos lubrificantes também pode limitar a sua aplicação.
(4) Resumo dos Tratamentos de Superfície Terminal
Presume-se que o revestimento de metais preciosos seja colocado sobre uma base de níquel de 50 mícrons. O ouro é o material mais comum, com espessura variando de acordo com os requisitos de vida útil, mas é suscetível a problemas de porosidade.
O paládio não é recomendado para situações que requerem proteção de soldabilidade. A prata é sensível a manchas e migração, usada principalmente em conectores de energia, mas sua vida útil pode ser significativamente melhorada através da lubrificação. O estanho apresenta excelente estabilidade ambiental, mas a estabilidade mecânica deve ser garantida.
4. As dez regras rígidas de revestimento de estanho para terminais
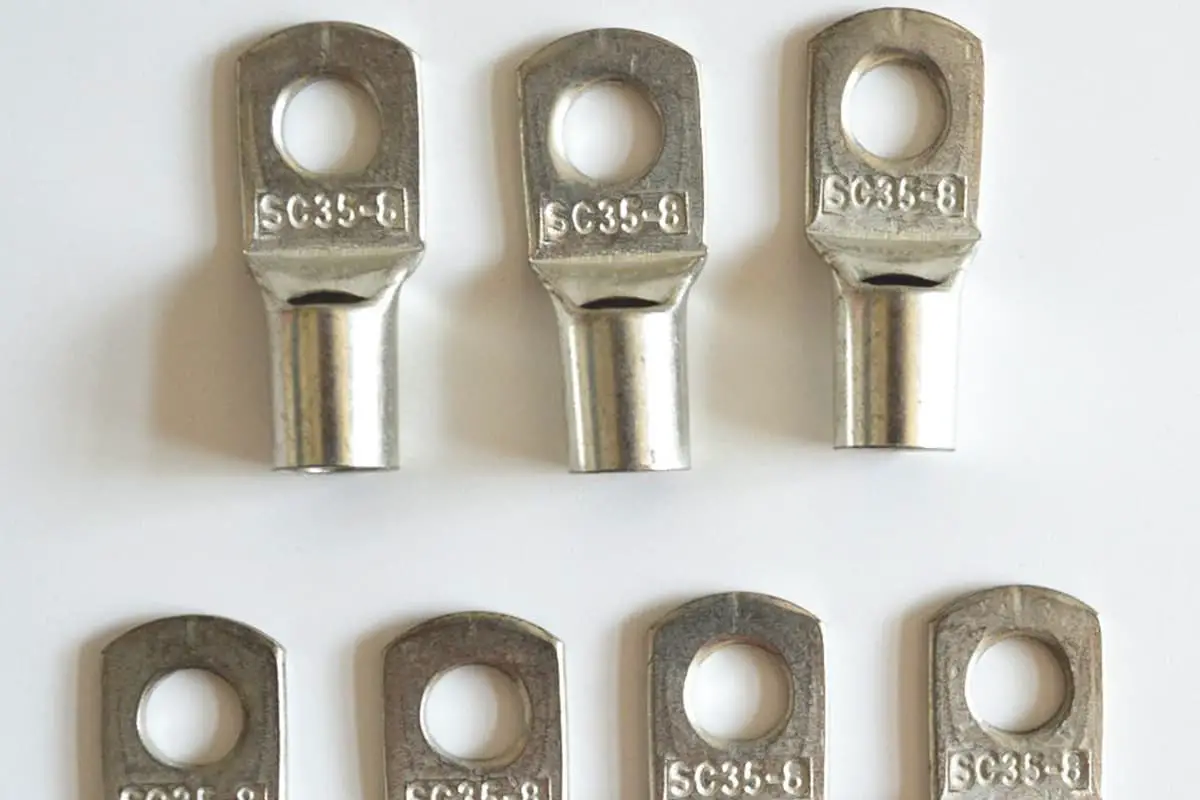
Materiais de estanho ou ligas de estanho estão entre as melhores opções para galvanoplastia de terminais, oferecendo uma solução econômica com baixa resistência de contato e excelente soldabilidade. Esses materiais atendem aos requisitos de desempenho de diversas aplicações, tornando-os um substituto ideal para ouro e outros metais preciosos no revestimento.
Abaixo estão dez regras constantes, embora à medida que surgem novas aplicações, mais princípios aguardam serem descobertos.
- Ao utilizar materiais estanhados, certifique-se de que os terminais macho e fêmea mantenham uma boa estabilidade mecânica depois de conectados.
Evite usar terminais estanhados em ambientes vibrantes. A expansão térmica diferencial (DTE) entre os metais terminais pode levar à corrosão por atrito dentro de uma faixa de 10 a 200 micrômetros, danificando o revestimento, expondo o material de base e aumentando significativamente a resistência de contato devido à oxidação.
- Para manter um contato estável entre os terminais estanhados, aplique uma força mínima de 100 gramas na direção axial.
- Terminais estanhados requerem lubrificação.
Seguindo a segunda regra, com o aumento da pressão axial, torna-se necessária uma lubrificação adequada para reduzir o atrito. Os terminais macho e fêmea devem ser lubrificados, ou pelo menos uma extremidade.
- Materiais estanhados não são recomendados para ambientes contínuos de alta temperatura.
As altas temperaturas aceleram a formação de compostos intermetálicos entre o cobre e o estanho, resultando em camadas intermediárias frágeis e duras que afetam a funcionalidade. Uma camada de niquelagem é recomendada como intermediária, uma vez que os compostos intermetálicos de níquel-estanho crescem mais lentamente.
- Vários processos de estanhagem têm impacto mínimo no desempenho elétrico.
O revestimento de estanho brilhante é esteticamente agradável; o estanho fosco deve manter uma superfície limpa para não afetar a soldabilidade. O revestimento de estanho de latão deve incluir uma camada inferior de níquel para evitar a perda de zinco do material de base, o que degradaria a soldabilidade.
- Procure uma espessura de estanho entre 100 e 300 micropolegadas.
Espessuras abaixo de 100 micropolegadas são normalmente usadas para produtos sensíveis ao custo com requisitos de soldabilidade mais baixos.
- A combinação de terminais banhados a estanho e banhados a ouro não é recomendada.
Esta prática leva ao aumento da oxidação e corrosão. O estanho migra para a superfície do ouro, eventualmente causando um acúmulo de óxidos de estanho no substrato de ouro mais duro. É mais difícil romper o óxido de estanho no ouro do que penetrar diretamente na camada de óxido do estanho. No entanto, a corrosão por atrito entre o estanhado e o prateado é semelhante à dos terminais revestidos com estanho em ambas as extremidades.
- É aconselhável unir inicialmente os terminais estanhados duas ou três vezes.
Este procedimento remove a camada de óxido da estanhagem, garantindo um contato confiável de metal com metal. Isto também é recomendado para terminais ZIF (Zero Insertion Force).
- Os terminais banhados em estanho ou liga de estanho não são adequados para aplicações com interrupções frequentes do circuito.
Devido ao baixo ponto de fusão do estanho, não é aconselhável utilizar estes materiais em situações propensas a formação de arco, como pontos de contato.
- Terminais estanhados são melhor utilizados em circuitos secos e aplicações com requisitos moderados.