1. Quais são as características da estrutura cristalina primária da solda?
Responder:
A solidificação de uma poça fundida de soldagem também segue os princípios fundamentais da solidificação geral de metal líquido, que envolve a formação de núcleos cristalinos e seu crescimento.
À medida que o metal líquido na poça de fusão esfria e solidifica, os grãos parcialmente derretidos no metal base na zona de fusão normalmente servem como locais para a nucleação do cristal.
Esses núcleos cristalinos subsequentemente atraem e absorvem os átomos do líquido circundante, levando ao crescimento do cristal.
Como os cristais crescem na direção oposta da condução de calor e em duas direções opostas, mas são obstruídos por cristais vizinhos em crescimento, os cristais resultantes assumem uma forma colunar e são chamados de cristais colunares.
Sob circunstâncias específicas, o metal líquido na poça fundida também pode sofrer nucleação espontânea durante a solidificação.
Se a dissipação de calor ocorrer em todas as direções, os cristais crescerão uniformemente em todas as direções, formando cristais equiaxiais.
Embora os cristais colunares sejam normalmente observados na costura de solda, cristais equiaxiais também podem aparecer no centro da solda sob certas condições.
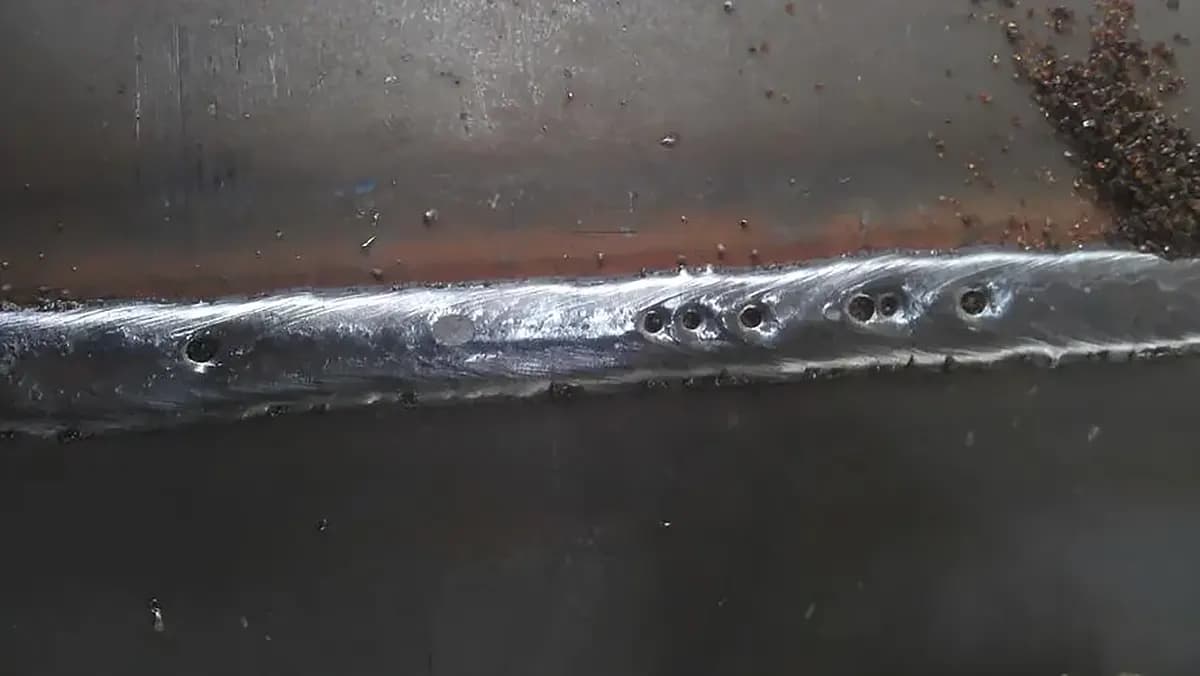
2. Quais são as características da estrutura de cristalização secundária da solda?
Responder:
Após a cristalização primária, o metal de solda continua a esfriar abaixo da temperatura de transformação de fase, causando uma alteração na sua estrutura metalográfica.
Por exemplo, ao soldar aço de baixo carbono, os grãos cristalinos primários são austeníticos. À medida que a temperatura cai abaixo do ponto de transformação, a austenita se decompõe em ferrita e perlita. Consequentemente, a estrutura após a cristalização secundária é composta principalmente de ferrita com uma pequena quantidade de perlita.
Porém, devido à rápida taxa de resfriamento da solda, o teor de perlita obtido é geralmente superior ao encontrado na estrutura de equilíbrio. Quanto maior a velocidade de resfriamento, mais significativo será o teor de perlita.
O teor reduzido de ferrita resulta em maior dureza e resistência, mas uma diminuição na plasticidade e tenacidade. A estrutura real à temperatura ambiente é obtida após a cristalização secundária.
Diferentes condições de soldagem e tipos de aço podem produzir microestruturas de solda variadas.
3. Tomemos como exemplo o aço de baixo carbono para explicar qual estrutura é obtida após a cristalização secundária do metal de solda?
Responder:
Tomemos como exemplo o aço de baixo plástico, que possui uma estrutura cristalina primária austenítica.
O processo de transformação da fase sólida no metal de solda é conhecido como cristalização secundária do metal de solda, que resulta em uma microestrutura de ferrita e perlita.
Na estrutura de equilíbrio do aço de baixo carbono, o teor de carbono no metal de solda é muito baixo, resultando em uma estrutura colunar grosseira de ferrita com uma pequena quantidade de perlita.
Porém, devido à alta taxa de resfriamento durante a soldagem, a ferrita não pode precipitar completamente de acordo com o diagrama de fases ferro-carbono, resultando em um maior teor de perlita do que na estrutura plana.
A taxa de resfriamento durante a soldagem também determina o tamanho do grão, a dureza e a resistência do metal. Grãos mais finos são obtidos com taxas de resfriamento mais altas, resultando em maior dureza e resistência, mas a diminuição da ferrita e o aumento do teor de perlita podem levar à redução da plasticidade.
Portanto, a microestrutura final da solda é determinada pela composição do metal e pelas condições de resfriamento durante a soldagem.
Devido à natureza do processo de soldagem, a estrutura do metal de solda é fina, resultando em melhores microestruturas e propriedades do que no estado de fundição.
4. Quais são as características da soldagem de metais diferentes?
Responder:
1)As características da soldagem de metais diferentes são definidas principalmente pelas diferenças significativas na composição da liga do metal depositado e da solda. O comportamento da poça de soldagem varia dependendo do formato da solda, da espessura do metal base, do revestimento ou fluxo do eletrodo e do tipo de gás de proteção utilizado.
Como resultado, a quantidade de fusão do metal base é diferente e a diluição mútua da concentração de componentes químicos na área de fusão do metal depositado e do metal base também é afetada. Portanto, o grau de não uniformidade das juntas soldadas de metais diferentes em relação à composição química regional depende não apenas da composição original das soldagens e dos materiais de enchimento, mas também do processo de soldagem utilizado.
2)Após o ciclo térmico de soldagem, diferentes estruturas metalográficas aparecerão em cada área da junta soldada devido à falta de homogeneidade da estrutura. Isto está relacionado à composição química, método de soldagem, camada de soldagem, processo de soldagem e tratamento térmico do metal base e material de enchimento.
3)A não uniformidade de desempenho, resultante das diferentes composições químicas e estrutura metálica da junta, leva a diferenças significativas nas propriedades mecânicas da junta.
A resistência, dureza, plasticidade e tenacidade de cada área ao longo da junta podem ser muito diferentes. Na zona afetada pelo calor em ambos os lados da solda, o valor do impacto pode diferir várias vezes. O limite de fluência e a resistência à alta temperatura também podem variar muito devido a diferenças na composição e estrutura.
4)A não uniformidade da distribuição do campo de tensão e da distribuição da tensão residual na junta metálica diferente é determinada principalmente pela plasticidade diferente de cada área da junta.
Além disso, a diferença na condutividade térmica do material pode causar uma alteração no campo de temperatura do ciclo térmico de soldagem. Os diferentes coeficientes de expansão linear em cada região e outros fatores são razões para a distribuição desigual do campo de tensões.
5. Quais são os princípios de seleção de materiais de soldagem para soldagem de aços diferentes?
Responder:
Os princípios de seleção para materiais de soldagem de aço diferentes incluem principalmente os quatro pontos a seguir:
- Quando a resistência e a plasticidade do metal de solda não forem críticas, selecione materiais de soldagem com boa plasticidade, garantindo que a junta soldada não desenvolva trincas ou outros defeitos.
- As propriedades do metal de solda de materiais de soldagem de aço diferentes devem atender aos requisitos técnicos de pelo menos um dos dois metais básicos.
- Os materiais de soldagem devem ter bom desempenho de processo e produzir soldas visualmente atraentes. Os materiais de soldagem devem ser acessíveis e prontamente disponíveis.
Leitura relacionada: Soldabilidade de materiais metálicos
6. E quanto à soldabilidade do aço perlítico e do aço austenítico?
Responder:
O aço perlítico e o aço austenítico são dois tipos distintos de aço com diferentes estruturas e componentes. Ao soldar esses dois tipos de aço, o metal de solda é criado pela fusão de dois tipos diferentes de metais básicos e materiais de enchimento, o que pode levar a desafios de soldabilidade.
1) Diluição de soldas.
O aço perlítico contém elementos de baixa liga, que podem diluir a liga geral do metal de solda.
O efeito de diluição do aço perlítico reduz o teor de elementos formadores de austenita na solda.
Como consequência, a solda pode desenvolver uma estrutura martensítica, o que pode impactar negativamente a qualidade da junta e até mesmo causar fissuras.
2) Formação de camadas de transição.
Durante o ciclo térmico de soldagem, o grau de mistura entre o metal base fundido e o metal de adição varia na borda da poça fundida.
Neste local, o metal líquido é caracterizado por baixa temperatura, baixa fluidez e curto tempo de permanência no estado líquido.
Devido às diferenças significativas na composição química entre o aço perlítico e o aço austenítico, o metal base fundido e o metal de adição não podem ser adequadamente fundidos na borda da poça fundida no lado perlítico.
Consequentemente, as soldas no lado do aço perlítico contêm uma proporção significativa de metal base perlítico, com a proporção aumentando próximo à linha de fusão.
Isto cria uma camada de transição com diferentes componentes internos do metal de solda.
3) É formada uma camada de difusão na zona de fusão.
No metal de solda composto por esses dois tipos de aços, o aço perlítico apresenta maior teor de carbono, mas menor teor de elementos de liga que o aço austenítico.
Por outro lado, na zona de fusão, a diferença de concentração dos elementos formadores de carbono e carboneto é formada em ambos os lados do aço perlítico no caso do aço austenítico.
Quando a junta trabalha a uma temperatura superior a 350-400 ℃ por um longo período, a zona de fusão exibirá uma difusão óbvia de carbono, ou seja, difusão do lado do aço perlítico para a solda austenítica através da zona de fusão.
Como resultado, uma camada descarbonetada e amolecida é formada no metal base do aço perlítico próximo à zona de fusão, e uma camada descarbonetada correspondente à descarbonetação é formada em um lado da solda austenítica.
4) Como as propriedades físicas do aço perlítico e do aço austenítico são muito diferentes, a composição da solda também é muito diferente.
Este tipo de junta não pode ser tratada termicamente para eliminar o estresse da soldagem. O tratamento térmico só pode causar redistribuição de tensões, o que é muito diferente da soldagem do mesmo metal.
5) Rachadura retardada.
Durante o processo de cristalização, a poça fundida criada pela soldagem de aços diferentes contém estruturas de austenita e ferrita que estão intimamente relacionadas entre si.
Como o gás pode se difundir facilmente neste processo, o hidrogênio difusível pode se acumular e levar ao craqueamento retardado.
7. Quais são as medidas para evitar trincas durante a soldagem de reparo de ferro fundido?
Responder:
(1) Pré-aquecimento antes da soldagem e resfriamento lento após a soldagem
Pré-aquecer a soldagem como um todo ou parcialmente antes da soldagem, e resfriá-la lentamente após a soldagem, pode reduzir a tendência de porosidade da solda e minimizar o estresse de soldagem, evitando assim que a soldagem rache.
(2) A soldagem a arco frio é adotada para reduzir o estresse de soldagem.
Para evitar rachaduras, materiais de soldagem com boa plasticidade, como níquel, cobre, níquel-cobre e aço com alto teor de vanádio, são selecionados como metais de adição. Isso permite que o metal de solda alivie a tensão através da deformação plástica.
A redução do estresse de soldagem pode ser alcançada usando eletrodos de diâmetro fino, corrente pequena, soldagem intermitente e técnicas de soldagem dispersa para diminuir a diferença de temperatura entre a solda e o metal base. Além disso, martelar a solda pode ajudar a eliminar o estresse e prevenir rachaduras.
(3) Outras medidas: ajustar a composição química do metal de solda para estreitar sua faixa de temperatura frágil;
Para potencializar a reação metalúrgica de dessulfuração e desfosforização na solda, devem ser adicionados elementos de terras raras. Além disso, a adição de elementos de grãos refinados de Zengna irá refinar os grãos de solda.
Em alguns casos, o método da zona de tensão de aquecimento é utilizado para reduzir a tensão na área onde a solda está sendo reparada. Este método também é eficaz na prevenção da ocorrência de fissuras.
Leitura relacionada: Como soldar ferro fundido?
8. O que é concentração de estresse? Quais são os fatores que causam concentração de estresse?
Responder:
Devido às características desconhecidas do formato do cordão de solda e do próprio cordão de solda, ocorre uma descontinuidade no formato coletivo, o que leva à concentração de tensões quando carregado. Esta concentração de tensões provoca uma distribuição desigual da tensão de trabalho da junta soldada, resultando num pico de tensão local σmax que é muito superior à tensão média σm.
Existem muitas razões para a concentração de tensões na soldagem, sendo os defeitos do processo um contribuinte significativo. Entradas de ar, inclusões de escória, trincas e penetração incompleta na solda podem causar concentração de tensões, sendo trincas de soldagem e penetração incompleta as mais severas.
Outros fatores que contribuem para a concentração de tensão incluem a aparência irracional da solda, como reforço excessivo de soldas de topo e pontas altas de soldas de filete, e projeto de rua irracional, como mudanças repentinas nas interfaces das ruas ou o uso de juntas de topo com placas de cobertura.
Arranjos de juntas de solda não razoáveis também podem causar concentração de tensão. Por exemplo, juntas em T com apenas soldas podem levar à concentração de tensões.
9. O que é falha plástica e quais são os seus perigos?
Responder:
A falha plástica pode resultar em instabilidade plástica (rendimento ou deformação plástica significativa) ou fratura plástica (fratura de borda ou fratura dúctil).
O processo começa com a deformação elástica da estrutura soldada sob carga, seguida de escoamento, deformação plástica (instabilidade plástica), microfissuras ou vazios, macrofissuras, crescimento instável e, finalmente, fratura.
Em comparação com a fratura frágil, a fratura plástica é menos provável de ocorrer em ambientes frios, pelas seguintes razões:
(1) A deformação plástica irrecuperável ocorre após o escoamento, inutilizando estruturas soldadas com requisitos de tamanho elevados.
(2) Para vasos de pressão feitos de materiais de alta tenacidade e baixa resistência, a falha não é controlada pela tenacidade à fratura dos materiais, mas é causada pela instabilidade plástica devido à resistência insuficiente.
Danos plásticos podem invalidar a estrutura soldada, conduzindo a acidentes catastróficos que afectam a produção empresarial, resultam em vítimas desnecessárias e prejudicam seriamente o desenvolvimento económico nacional.
10. O que é fratura frágil e quais são os seus malefícios?
Responder:
Fratura frágil geralmente se refere à fratura de dissociação (incluindo fratura de quase dissociação) e fratura de limite de grão (intergranular) que se divide ao longo de um determinado plano cristalino.
A fratura por clivagem, por outro lado, é um tipo de fratura intragranular que ocorre quando os materiais se separam ao longo de um plano cristalográfico específico dentro do cristal.
Sob certas condições, como baixa temperatura, alta taxa de deformação e alta concentração de tensão, os materiais metálicos podem sofrer fratura por clivagem quando a tensão atinge um determinado valor.
Existem vários modelos que explicam a geração de fratura por clivagem, muitos dos quais estão relacionados à teoria das luxações.
Acredita-se geralmente que quando o processo de deformação plástica dos materiais é severamente prejudicado, os materiais não podem se conformar às tensões externas através da deformação e, em vez disso, sofrem separação, levando a fissuras de clivagem.
Inclusões, precipitados frágeis e outros defeitos em metais também desempenham um papel importante na geração de fissuras de clivagem.
A fratura frágil normalmente ocorre quando a tensão não é superior à tensão admissível de projeto da estrutura e não há deformação plástica significativa. Pode propagar-se rapidamente por toda a estrutura, causando danos repentinos que são difíceis de detectar e prevenir antecipadamente, resultando muitas vezes em ferimentos pessoais e perda de propriedade.
11. Qual o papel da trinca de soldagem na fratura frágil estrutural?
Responder:
De todos os defeitos, as rachaduras são as mais perigosas. Quando submetido a cargas externas, uma pequena deformação plástica ocorre próximo à frente da trinca, e uma certa quantidade de deslocamento de abertura ocorre na ponta, fazendo com que a trinca se desenvolva gradualmente.
Se a carga externa aumentar para um nível crítico, a trinca se expandirá em alta velocidade. Neste ponto, se a fissura estiver situada numa zona de tensão de tração de alto valor, muitas vezes resulta na fratura frágil de toda a estrutura.
No entanto, se a trinca estendida entrar em uma área com baixa tensão de tração, haverá energia suficiente para manter a expansão adicional da trinca, ou a trinca entrar em um material com melhor tenacidade (ou no mesmo material com temperatura mais alta e maior tenacidade) onde recebe maior resistência.
Se a fissura não puder continuar a expandir-se, os danos causados pela fissura serão reduzidos em conformidade.
12. Quais são as causas das fraturas frágeis de estruturas soldadas?
Responder:
As causas da fratura podem ser resumidas em três aspectos:
(1) A humanidade dos materiais é insuficiente
A capacidade de deformação microelástica do material é particularmente fraca, especialmente na ponta do entalhe.
A falha frágil sob baixa tensão geralmente ocorre em temperaturas mais baixas, e a tenacidade dos materiais diminui drasticamente à medida que a temperatura diminui.
Além disso, com o avanço dos aços de baixa liga e alta resistência, o índice de resistência está aumentando, enquanto a plasticidade e a tenacidade estão diminuindo.
Em muitos casos, a fratura frágil se origina na zona de soldagem, tornando a falta de tenacidade na solda e na zona afetada pelo calor a principal causa da falha frágil sob baixa tensão.
13. Quais os principais fatores que devem ser considerados no projeto de estruturas soldadas?
Responder:
As principais considerações para juntas soldadas são as seguintes:
- A junta soldada deve possuir tensão e rigidez suficientes para garantir uma longa vida útil.
- O meio de trabalho e as condições das juntas soldadas devem ser considerados, como temperatura, corrosão, vibração e fadiga.
- A carga de trabalho de pré-aquecimento pré-soldagem e tratamento térmico pós-soldagem deve ser minimizada para grandes membros estruturais.
- A soldagem deve exigir pouca ou nenhuma usinagem.
- O trabalho de soldagem deve ser minimizado.
- A deformação e a tensão das estruturas soldadas devem ser reduzidas ao mínimo.
- A estrutura soldada deve ser fácil de construir e criar boas condições de trabalho para a construção.
- Devem ser adoptadas novas tecnologias e soldadura mecanizada e automática para melhorar a produtividade do trabalho.
- A solda deve ser facilmente inspecionada para garantir a qualidade da junta.
14. Descreva as condições básicas do corte a gás. O cobre vermelho pode ser cortado com chama de oxigênio e acetileno? Por que?
Responder:
Os requisitos básicos para corte a gás são os seguintes:
(1) O ponto de ignição do metal deve ser inferior ao seu ponto de fusão.
(2) O ponto de fusão do óxido metálico deve ser inferior ao do próprio metal.
(3) A queima de metal em oxigênio deve produzir uma quantidade substancial de calor.
(4) A condutividade térmica do metal deve ser baixa.
O cobre vermelho não pode ser cortado com chama de oxigênio-acetileno porque a quantidade de calor gerada pelo óxido de cobre (CuO) é muito pequena e a condutividade térmica do cobre é muito alta. Como resultado, o calor não pode ser concentrado próximo à incisão, impossibilitando o corte com gás.
15. Qual é a principal função do pó para soldagem a gás?
Responder:
O objetivo principal do pó de soldagem é gerar escória através da reação com óxidos metálicos ou impurezas não metálicas presentes na poça fundida, facilitando assim o processo de escória.
Simultaneamente, a escória gerada cobre a superfície da poça fundida e atua como uma barreira, isolando a poça fundida do ar circundante. Este isolamento evita que o metal presente na poça de fusão oxide continuamente em altas temperaturas.
16. Quais são as medidas de processo para evitar a porosidade da solda na soldagem a arco manual?
Responder:
(1) As hastes de soldagem e os fluxos devem ser armazenados em ambiente seco e secos antes do uso, se necessário.
(2) O fio de soldagem e as superfícies soldadas devem ser mantidas limpas, livres de água, óleo, ferrugem ou quaisquer outros contaminantes.
(3) A especificação de soldagem deve ser selecionada com precisão, levando em consideração fatores como corrente de soldagem e velocidade de soldagem apropriadas.
(4) O método de soldagem correto deve ser empregado, incluindo o uso de eletrodos alcalinos para soldagem a arco manual e soldagem a arco curto, reduzindo a faixa de oscilação do eletrodo, diminuindo a velocidade de movimento do eletrodo e controlando a partida e a parada do arco curto.
(5) A folga de montagem da soldagem de controle não deve ser muito grande.
(6) Varetas de soldagem com revestimentos rachados, descascamento, deterioração, excentricidade e núcleos corroídos não devem ser usados.
17. Quais são as principais medidas para evitar o frio durante a soldagem do ferro fundido?
Responder:
(1) O uso de eletrodos grafitados é altamente recomendado. Esses eletrodos são fabricados em ferro fundido com alta concentração de elementos grafitados (como carbono, silício, etc.) adicionados ao revestimento ou fio de soldagem. Alternativamente, eletrodos de ferro fundido à base de níquel ou cobre também podem ser usados.
(2) Antes da soldagem, é necessário pré-aquecimento para preparar os materiais. Durante a soldagem, é importante manter a preservação do calor e, após a soldagem, recomenda-se um resfriamento lento para reduzir a taxa de resfriamento da zona de solda. Ao fazer isso, prolonga-se o tempo em que a zona de fusão está no estado incandescente, tornando a grafitização suficiente e reduzindo o estresse térmico.
(3) Considere usar um processo de brasagem para obter resultados ideais.
18. Tente descrever o papel do fluxo no processo de soldagem?
Responder:
O fluxo desempenha um papel crucial na garantia da qualidade da soldagem. Serve as seguintes funções:
- Após a fusão, o fluxo flutua na superfície do metal fundido para proteger a poça fundida e evitar a erosão de gases nocivos no ar.
- O fluxo de soldagem auxilia na desoxidação e na formação de ligas e, em conjunto com o fio de soldagem, garante que o metal de solda atinja a composição química e as propriedades mecânicas necessárias.
- Garante que a solda tenha uma aparência bem formada.
- Retarda a taxa de resfriamento do metal fundido, reduzindo assim defeitos como porosidade e inclusão de escória.
- Evita respingos, reduz perdas e aumenta o coeficiente de ligação.
19. O que deve ser prestado atenção no uso e manutenção da máquina de solda a arco AC?
Responder:
(1) A máquina de solda deve ser operada de acordo com sua corrente nominal de soldagem e duração de carga e não deve ser sobrecarregada.
(2) Deve-se evitar curto-circuito prolongado da máquina de solda.
(3) A corrente reguladora deve ser operada sem qualquer carga.
(4) Inspecione regularmente o contato do fio, o fusível, o aterramento e o mecanismo de regulação e certifique-se de que estejam em boas condições.
(5) Mantenha a máquina de solda limpa, seca e bem ventilada para evitar a entrada de poeira e chuva.
(6) Coloque a máquina em uma posição estável e desligue a fonte de alimentação após o uso.
(7) É necessário realizar manutenção e inspeção regulares da máquina de solda.
20. Quais são os perigos da fratura frágil?
Responder:
A fratura frágil é um fenômeno repentino que não pode ser detectado e evitado a tempo. Quando ocorre, as consequências podem ser graves, conduzindo a perdas económicas significativas e pondo em perigo a segurança humana.
Como resultado, a questão da fratura frágil em estruturas soldadas deve receber maior atenção.
21. Características e aplicação da pulverização de plasma?
Responder:
A pulverização de plasma é caracterizada por uma alta temperatura de chama de plasma que pode derreter quase todos os materiais refratários, tornando-a adequada para uma ampla gama de aplicações de pulverização. Ele também possui alta velocidade de fluxo de chama de plasma, excelente efeito de aceleração de partículas de pó e resistência superior de colagem de revestimento.
Devido à sua versatilidade, a pulverização a plasma é ideal para diversos materiais cerâmicos e possui uma ampla gama de aplicações, tornando-se o melhor método para pulverização de materiais cerâmicos.
22. Procedimento de preparação do cartão de procedimento de soldagem?
Responder:
Para preparar o cartão de procedimento de soldagem, a qualificação do procedimento de soldagem correspondente deve ser identificada e um esboço da junta deve ser elaborado com base no desenho de montagem do produto, desenho de processamento de peças e seus requisitos técnicos.
O cartão de procedimento de soldagem deve incluir o número de qualificação do procedimento de soldagem, número do cartão de procedimento de soldagem, número do desenho, nome da junta, número da junta e itens do certificado do soldador.
A sequência de soldagem deve ser preparada com base na qualificação do procedimento de soldagem, nas condições reais de produção, no pessoal técnico e na experiência de produção.
Parâmetros específicos do processo de soldagem também devem ser incluídos com base na qualificação do processo de soldagem.
A autoridade de inspeção, o método de inspeção e a proporção de inspeção dos produtos devem ser determinados de acordo com os requisitos dos desenhos e padrões do produto.
23. Por que uma certa quantidade de silício e manganês deve ser adicionada ao fio de soldagem com proteção de gás CO2?
Responder:
O dióxido de carbono é um gás oxidante que pode queimar os elementos de liga de uma costura de soldagem durante o processo de soldagem, reduzindo significativamente as propriedades mecânicas da solda. Esta oxidação pode resultar na formação de poros e salpicos.
Para resolver esses problemas, silício e manganês podem ser adicionados ao fio de soldagem para desempenhar um papel desoxidante, evitando a oxidação e respingos da soldagem.
24. Qual é o limite de explosão da mistura combustível e quais fatores o afetam?
Responder:
A faixa de concentração de gás combustível, vapor ou poeira presente em uma mistura combustível que pode causar uma explosão é chamada de limite de explosão.
O limite inferior de concentração é conhecido como limite inferior de explosão, e o limite superior é conhecido como limite superior de explosão.
Vários fatores como temperatura, pressão, teor de oxigênio, diâmetro do recipiente e outros podem influenciar o limite de explosão. Um aumento na temperatura resulta numa diminuição do limite de explosão, e o mesmo ocorre quando há um aumento na pressão.
Além disso, um aumento na concentração de oxigênio na mistura gasosa causa uma diminuição no limite inferior de explosão.
Para poeira combustível, fatores como dispersão, umidade e temperatura também podem afetar seu limite de explosão.
25. Que medidas devem ser tomadas para evitar choques elétricos durante a soldagem em tambor de caldeira, condensador, tanque de óleo, tanque de óleo e outros recipientes metálicos?
Responder:
(1) Os soldadores devem evitar o contato com peças de ferro durante a soldagem elétrica. Eles devem ficar sobre almofadas de isolamento de borracha ou usar sapatos de isolamento de borracha e roupas de trabalho secas.
(2) Deve haver um supervisor fora da embarcação que possa observar e ouvir o trabalho do soldador. Um interruptor deve ser instalado para cortar a alimentação com base no sinal do soldador.
(3) A tensão das lâmpadas portáteis utilizadas em recipientes não deve exceder 12V. O invólucro do transformador da lâmpada portátil deve ser aterrado de forma confiável e o uso de um autotransformador é proibido.
(4) Transformadores para lâmpadas portáteis e transformadores de soldagem não devem ser colocados em caldeiras e recipientes metálicos.
26. Como distinguir a soldagem por fusão da brasagem? Quais são as características de cada um?
Responder:
A soldagem por fusão envolve a ligação de átomos entre as soldagens, enquanto a brasagem conecta as soldagens usando metal de adição, um meio intermediário com um ponto de fusão inferior ao da soldagem.
A soldagem por fusão oferece diversas vantagens, como altas propriedades mecânicas de juntas soldadas e alta produtividade na união de peças grossas e grandes. No entanto, também apresenta algumas desvantagens, como grandes tensões e deformações e alterações microestruturais na zona afetada pelo calor.
A brasagem, por outro lado, apresenta vantagens como baixa temperatura de aquecimento, juntas planas e lisas e bela aparência. Também resulta em pequenas tensões e deformações. No entanto, suas desvantagens incluem baixa resistência da junta e altos requisitos de folga de montagem durante a montagem.
27. Tanto o dióxido de carbono como o argônio pertencem a gases protetores. Quais são suas propriedades e usos?
Responder:
O dióxido de carbono é um gás oxidante. Quando usado como gás de proteção na soldagem, pode causar oxidação severa de gotículas fundidas e metal da poça, resultando na perda por queima de elementos de liga. Além disso, possui baixa processabilidade e pode causar poros e grandes respingos.
Portanto, atualmente é adequado apenas para soldagem de aços de baixo carbono e aços de baixa liga, e não é recomendado para aços de alta liga e metais não ferrosos. Principalmente na soldagem de aço inoxidável, pode causar carburação da solda e reduzir a resistência à corrosão intergranular, tornando-o menos utilizado.
O argônio, por outro lado, é um gás inerte que não reage quimicamente com o metal fundido, resultando em alterações mínimas na composição química da costura de solda. As costuras soldadas produzidas com argônio têm boa qualidade e podem ser utilizadas em diversos aços-liga, aços inoxidáveis e metais não ferrosos.
À medida que o preço do argônio diminui gradualmente, ele está se tornando uma opção popular para soldar um grande número de aços de baixo carbono.
28. Tente descrever a soldabilidade e as características de soldagem do aço 16Mn?
Responder:
O aço 16Mn contém aproximadamente 1% de Mn além do aço Q235A, resultando em um carbono equivalente de 0,345%~0,491%. Como resultado, o aço apresenta bom desempenho de soldagem. Porém, a tendência de endurecimento do aço 16Mn é ligeiramente superior à do aço Q235A, portanto, ao soldar estruturas espessas e rígidas, parâmetros menores devem ser utilizados para evitar trincas, principalmente em baixas temperaturas. Nesses casos, o pré-aquecimento adequado pode ser aplicado antes da soldagem.
Para soldagem a arco manual, recomenda-se o uso de varetas de solda E50. Nos casos em que a ranhura não pode ser aberta para soldagem automática por arco submerso, pode-se utilizar fio de solda H08MnA com fluxo 431. No biselamento deve-se utilizar fio de solda H10Mn2 com fluxo 431. Durante a soldagem com proteção de gás CO2, deve-se usar fio de soldagem H08Mn2SiA ou H10MnSi.