Existem basicamente três métodos para processamento de bordas de componentes de navios:
1. Método de cisalhamento mecânico
(1) Princípio do cisalhamento mecânico
(2) Tecnologia de processamento de cisalhamento mecânico
2. Método de corte a gás (método de corte químico)
(1) Princípio do corte a gás
(2) Processo de tecnologia de corte de gás
3. Método de corte a plasma CNC
A seguir, será apresentado principalmente o princípio básico do corte a plasma e sua aplicação na construção naval.
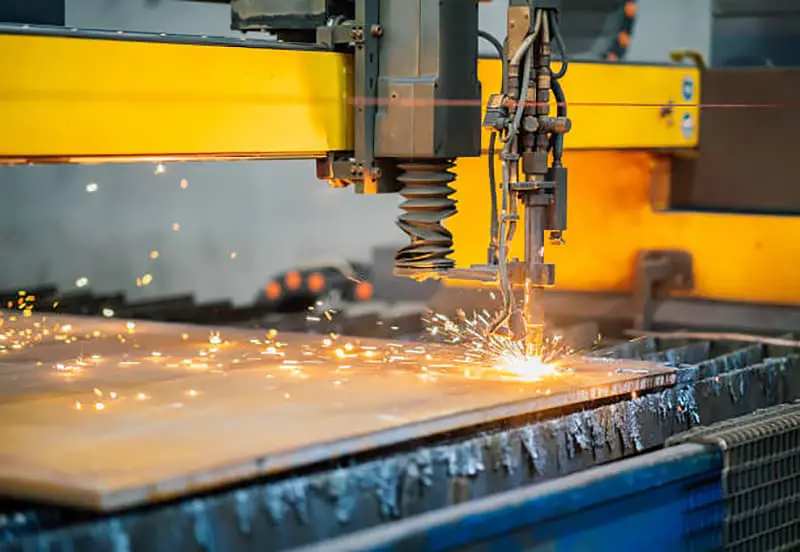
Método de corte a plasma:
Existe uma diferença essencial entre o processo de corte a plasma e o princípio do corte a gás. É um processo de corte físico que utiliza a alta temperatura do arco de plasma para derreter o metal na costura de corte e, em seguida, sopra-o com uma chama de alta velocidade para formar uma lacuna estreita que separa o material à medida que o bico se move.
O arco plasma também é conhecido como arco comprimido, que possui uma área de seção transversal condutora relativamente pequena e, portanto, concentra a energia de forma mais eficaz.
(1) Princípio do Corte por Arco Plasma
1. Geração de Arco Plasmático
O princípio da geração do arco plasma é basicamente o mesmo do arco de soldagem. O arco é uma forma estável de descarga de gás, que é o fenômeno da corrente que passa pelo gás. Em circunstâncias normais, o gás é um bom isolante. Com a ação da energia externa, alguns átomos do gás emitem elétrons e se transformam em íons positivos – ionização.
O Princípio da Geração de Arco.
A magnitude da energia externa é representada pelo potencial de ionização. De acordo com a forma como a energia externa é fornecida, a ionização gasosa pode ser dividida em três formas: fotoionização, ionização por colisão e ionização térmica. A ionização do gás no arco é principalmente ionização térmica.
O grau de ionização do gás é expresso pelo grau de ionização: a razão entre a densidade de íons ou elétrons e a densidade das partículas neutras antes da ionização.
Um gás com grau de ionização inferior a 0,1% é denominado gás fracamente ionizado, cujas propriedades são semelhantes às do gás não ionizado.
Propriedades do gás ionizado.
Quando o grau de ionização atinge 1%, a condutividade do gás é próxima da do gás totalmente ionizado. A temperatura e o grau de ionização do arco plasma são significativamente mais elevados do que os do arco de soldagem comum, mas a condutividade do arco plasma não muda significativamente.
O tamanho da seção transversal da coluna do arco de plasma é relativamente pequeno e sua resistência costuma ser grande. O principal fator que determina o grau de ionização do gás é a temperatura.
Definição de Plasma
A 30.000K, quase todos os gases tornam-se ionizados e ficam em estado de ionização completa. O gás no estado de ionização completa é denominado “plasma”.
Este gás é composto inteiramente de partículas carregadas, tem forte condutividade e exibe propriedades eletromagnéticas significativas, mas como um todo permanece eletricamente neutro. Este é considerado o quarto estado da matéria.
2. Princípio do Dispositivo Gerador de Arco Plasma.
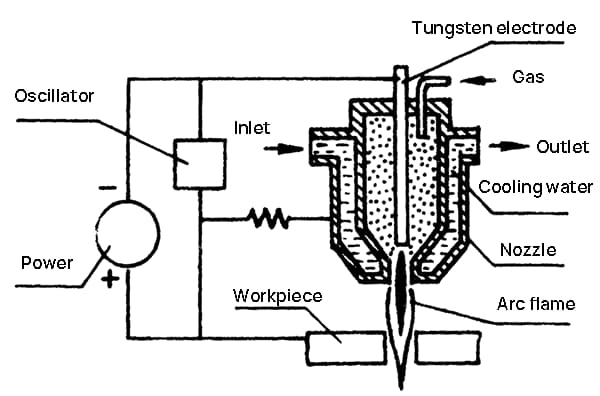
Efeito de Constrição Térmica (1)
O arco queima através do orifício do bocal entre o eletrodo de tungstênio e o metal que está sendo cortado. A coluna de arco é resfriada pelo fluxo de ar frio e pela parede do orifício do bocal resfriada a água. Este efeito de resfriamento causa a ocorrência de uma constrição da coluna do arco de plasma, o que aumenta a densidade de energia e a temperatura do arco na região estreita no centro da coluna do arco de plasma. Este fenômeno é conhecido como efeito de constrição térmica.
Este efeito faz com que a área da seção transversal da coluna do arco diminua e a densidade de corrente aumente.
A energia de toda a coluna do arco está concentrada na região central.
Efeito de constrição térmica (2).
Este efeito de resfriamento é chamado de “efeito de constrição térmica”. Com uma área de seção transversal reduzida, a mesma corrente requer uma tensão de alimentação aumentada.
Neste ponto, a intensidade do campo elétrico da coluna do arco aumenta.
O valor da intensidade do campo elétrico reflete em grande parte o grau de compressão ao qual o arco está sujeito.
Efeito de constrição magnética
Quando a corrente do arco de plasma atinge um determinado valor, o campo magnético gerado pela corrente do arco comprime ainda mais a área da seção transversal da coluna do arco. Este efeito é denominado “efeito de constrição magnética”.
Arcos de queima livre também exibem efeitos de constrição magnética. O arco de plasma tem maior densidade de corrente e é baseado na constrição térmica, portanto o efeito de constrição magnética é mais forte.
Efeito de Constrição Mecânica
A abertura do orifício do bocal exerce um efeito de compressão forçada na coluna do arco. O fluxo de gás comprimido ou fluxo de água ao redor do arco também exerce um efeito de compressão forçada na coluna do arco, que é conhecido como efeito de constrição mecânica.
Esta compressão do arco é chamada de “efeito de constrição mecânica”.
Implementação de Corte Plasma
A pressão dos três efeitos de constrição e a difusão térmica dentro do arco de plasma atingem um equilíbrio, formando um fluxo de plasma de alta velocidade e alta temperatura que é pulverizado para fora do orifício do bico.
Quando o fluxo de plasma encontra metal de baixa temperatura, ele se recombina em átomos ou moléculas e libera energia, fazendo com que o metal na costura de corte aqueça e derreta rapidamente. A forte força mecânica do fluxo de plasma empurra o metal derretido para conseguir o corte.
Dispositivo de geração de plasma para jato de água
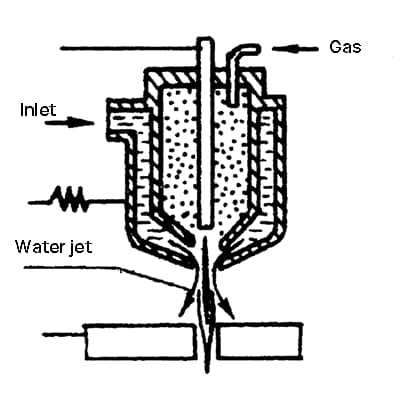
A figura ilustra um diagrama esquemático de um dispositivo de geração de plasma para corte por jato de água, que difere do corte convencional por arco de plasma principalmente na estrutura do bico.
Estrutura do Dispositivo de Geração de Plasma para Jato de Água
Adicione um círculo de orifícios para jato de água na saída da coluna de arco no bico. Jatos de água disparam de todos os lados em direção ao arco, aumentando o efeito de retração térmica. A coluna do arco é ainda mais reduzida pelo resfriamento com água.
A densidade de energia do arco é mais concentrada, o que aumenta ainda mais a velocidade de corte.
Tipos de arco plasma:
O dispositivo de geração de arco de plasma é formado com base na prática de soldagem a arco de argônio com eletrodo de tungstênio. De acordo com o modo de conexão da fonte de alimentação, o arco plasma pode ser dividido em três tipos: arco transferido, arco não transferido e arco híbrido.

Geração de Arco Plasmático Transferido:
O eletrodo está conectado ao pólo negativo e a peça de trabalho está conectada ao pólo positivo. O arco é formado primeiro entre o eletrodo e o bico e, em seguida, uma tensão relativamente alta é aplicada entre o eletrodo e a peça de trabalho. Como resultado, o arco plasma é transferido do eletrodo para a peça de trabalho.
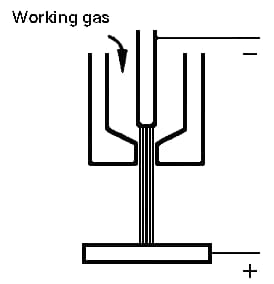
Aplicações do Arco Plasma Transferido:
O ponto catódico e o ponto anódico do arco de plasma transferido caem sobre o eletrodo e a peça de trabalho, respectivamente. Isso resulta em muita geração de calor que se concentra no ponto de contato entre o arco e a peça. Este tipo de arco plasma pode ser usado tanto para aplicações de corte quanto de soldagem.
Como o arco de plasma transferido ocorre entre o eletrodo e a peça de trabalho, é necessário que a peça de trabalho seja condutora.
Arco de Plasma Não Transferido:
No caso do arco plasma não transferido, apenas o bocal é conectado ao pólo positivo. O arco de plasma é gerado entre o eletrodo e o bico, e a chama de alta temperatura flui através do bico. O ponto anódico fica no bico, o que causa maior perda de calor e leva à diminuição da temperatura do arco plasma.

O arco de plasma não transferido é adequado para cortar e soldar metais finos e materiais não metálicos.
Arco de Plasma Híbrido:
Ambos os arcos de plasma de transferência e não transferência estão presentes simultaneamente. Este tipo de arco de plasma é utilizado principalmente em soldagem por microarco e pulverização de material em pó.
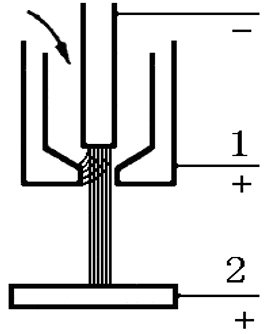
Características físicas do arco plasma
(1) As características térmicas do arco plasma.
As características térmicas são propriedades importantes de uma fonte de calor. A temperatura, potência térmica e eficiência térmica do arco plasma são:
① A temperatura do arco de plasma
A temperatura do arco plasma refere-se principalmente à temperatura da coluna do arco. A temperatura da coluna do arco geralmente está relacionada à potência do arco, gás, materiais do eletrodo e outras condições de trabalho.
O efeito do potencial de ionização do gás na temperatura.
A composição dos gases no espaço tem um impacto substancial na temperatura da coluna do arco. Um potencial de ionização mais alto do gás normalmente leva a uma temperatura mais alta da coluna do arco.
Além disso, o potencial de ionização do vapor dos materiais dos eletrodos pode afetar significativamente a temperatura da coluna do arco quando esta é mais baixa.
Ao usar um arco de eletrodo de metal fundido, o vapor metálico resultante tem um baixo potencial de ionização e a temperatura varia de 5.000K a 6.000K. Após a geração do plasma, os eletrodos de tungstênio são comumente usados e não evaporam.
A temperatura do arco de plasma
A temperatura da coluna do arco de plasma pode variar entre 15.000K-50.000K, e há um gradiente de temperatura extremamente alto do centro para a borda. Em comparação com os outros dois tipos de arco plasma, o arco plasma de transferência tem uma temperatura mais elevada.
Sob as condições de I=300A, U=250V, d=2,8mm de abertura do bocal e uma vazão de gás de Q=50l/min, utilizando nitrogênio como gás de trabalho, a temperatura máxima próxima ao bocal atinge Tmáx.=30000℃. Em I = 1500A e d = 2,5 mm, Tmáx.=52.000 ℃, e a concentração de energia atinge 1,1×109 W/cm2.
② A potência térmica do arco de plasma
Uma fonte de calor de alta temperatura não significa necessariamente uma maior capacidade de aquecimento. A capacidade de aquecimento de uma fonte de calor depende da sua potência térmica – a quantidade de energia térmica que ela pode transferir por unidade de tempo.
A potência térmica de um arco é a quantidade de energia elétrica convertida em energia térmica em um determinado tempo, também conhecida como consumo de energia. Isto representa a quantidade de calor gerada pelo arco por unidade de tempo.
Cálculo da potência térmica de um arco plasma.

Devido à sua alta tensão operacional (V) e corrente (I), um arco plasma gera uma quantidade significativa de energia térmica. Como resultado, a potência térmica de um arco de plasma pode ser ajustada ajustando vários parâmetros.
Parâmetros influentes na energia térmica
A corrente de trabalho de um arco de plasma depende de vários fatores, como a geometria e o tamanho do bico, a composição e a vazão do gás de trabalho e o material do eletrodo.
Esses parâmetros desempenham um papel crítico na determinação da corrente operacional de um arco plasma. Além disso, a influência da composição do gás pode orientar a seleção do gás de trabalho.
Quando utilizado como fonte de calor, um arco de plasma gera uma quantidade substancial de calor. O gás desempenha um papel crucial na transmissão de uma proporção significativa deste calor para a peça de trabalho.
O gás de trabalho de um arco de plasma
Durante os processos de aquecimento, decomposição e ionização que ocorrem dentro da coluna de arco, o gás absorve calor e atinge temperaturas extremamente altas.
A quantidade de calor absorvida pelo gás aumenta à medida que sofre decomposição térmica e ionização ou experimenta um aumento de temperatura, o que acaba por aumentar a sua capacidade de transferência de calor.
Do ponto de vista da decomposição térmica, apenas gases em estado molecular podem estar sujeitos a este processo. Os gases de trabalho para arcos de plasma incluem H2, N2, ar, vapor de água, argônio e outros.
À medida que a temperatura do gás usado na combustão do arco de plasma aumenta, também aumenta a sua entalpia.
A eficiência térmica de um arco de plasma
A energia elétrica é transformada em energia térmica na pistola de plasma, mas nem toda ela é utilizada para aquecer a peça. Parte é removida pelo resfriamento da água e pela radiação. Com o arco transferido, há menos perda de calor e a peça pode receber 60% da energia térmica.
A quantidade real de energia térmica recebida pela peça é a potência térmica efetiva do arco plasma.

(2) Velocidade da chama do arco de plasma
A velocidade da chama do arco de plasma é extremamente rápida, atingindo velocidades supersônicas de até 300-1000m/s e possui forte força de sopro. O gás da peça é rapidamente expandido devido ao aquecimento no canal do bico, resultando em uma velocidade de jato rápida devido à aceleração térmica.
Nos processos de corte, os arcos plasma com velocidades de chama rápidas e altas forças de impacto são conhecidos como arcos rígidos. Bicos de pequena abertura e gases de trabalho de grande vazão são fáceis de obter arcos rígidos.
(3) As características elétricas do arco plasma
As características estáticas de volt-ampère do arco de plasma, também conhecidas como característica estática.
As características estáticas do arco de plasma
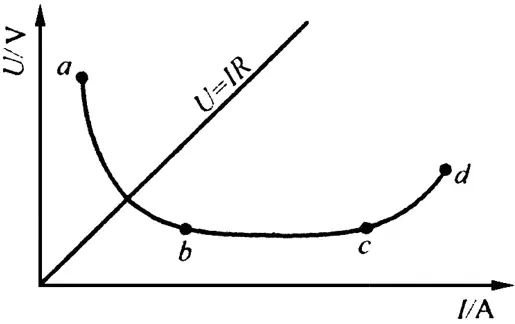
O bico limita o aumento da área da seção transversal da coluna do arco de plasma. A diferença entre as características estáticas do arco plasma e as de um arco elétrico comum se manifesta em dois aspectos: uma tensão mais alta e uma tendência a exibir uma característica plana ou ascendente.
As características estáticas do arco plasma estão relacionadas ao tipo e vazão do gás de trabalho, tamanho do bico, espaçamento dos eletrodos e outros fatores.
(4) A estabilidade de combustão do arco plasma.
Ao usar um plasma de arco transferido, pode ocorrer um fenômeno chamado arco duplo, que pode perturbar a estabilidade da combustão do arco de plasma.

O arco duplo pode atrapalhar o progresso normal do processo de corte e causar danos ao bico.
Fenômeno de arco duplo
Sob certas condições atuais e externas, a tensão do arco tende sempre a manter um valor mínimo. Esta é uma regra importante na física do arco, conhecida como princípio da tensão mínima.
Quando ocorre arco duplo, a tensão de A1+A2 é menor que a do arco plasma, portanto, a queda de tensão no canal do bocal está diretamente relacionada ao fenômeno do arco duplo.
Arco duplo e a tensão do arco de plasma
Para aumentar o grau de compressão do arco, é desejável reduzir a abertura do bico e alongar o arco plasma, aumentando assim a tensão e o efeito de contração magnética.
A tensão é diretamente proporcional ao comprimento do arco, portanto aumentos excessivos no comprimento do arco devem ser limitados na perspectiva de prevenir o fenômeno de arco duplo. Existem também outros fatores que podem afetar o fenômeno do arco duplo.
(2) Equipamento e processo de corte por arco de plasma
1. Fonte de alimentação de arco de plasma.
A relação entre a corrente de saída e a tensão nos terminais da fonte de alimentação é conhecida como características externas da fonte de alimentação.
O arco plasma requer que a fonte de alimentação tenha uma característica externa de queda acentuada.
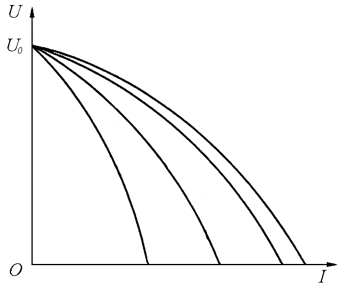
A tensão de circuito aberto (U0) da fonte de alimentação.
Para facilitar a ignição e a combustão estável do arco plasma, o requisito U0 para a fonte de alimentação é relativamente alto.
Para soldagem, pulverização térmica e outros processos, U0 > 80V é suficiente, enquanto corte e pulverização requerem U0 > 180V. A magnitude da tensão de circuito aberto depende principalmente da espessura do material a ser cortado, sendo que materiais mais espessos requerem U0 mais elevado.
A fonte de alimentação para corte a arco plasma
A fonte de alimentação comumente usada para corte a arco plasma é principalmente uma fonte de alimentação para soldagem a arco CC com características externas de queda acentuada, e existem modelos específicos disponíveis. Às vezes, fontes de alimentação CA são usadas para determinados processos ou materiais, o que é comum na soldagem a arco plasma.
Em alguns casos, máquinas de soldagem a arco de uso geral podem ser usadas conectando várias máquinas de soldagem com o mesmo tipo de corrente e características externas em série.
A tensão de circuito aberto das máquinas de corte a plasma produzidas internamente é geralmente 120V-300V, com uma corrente de trabalho de 320A-500A e uma tensão de trabalho de 60V-150V.
2. Material do eletrodo de arco de plasma
Os materiais do eletrodo para o eletrodo traseiro são os mesmos da soldagem TIG, incluindo eletrodos de tungstênio, eletrodos de tungstênio toriados e eletrodos de tungstênio ceriados.
O tungstênio puro com ponto de fusão de 3.400 ℃ e ponto de ebulição de 5.000 ℃ geralmente pode atender aos requisitos, mas deve ser bem resfriado para reduzir o desgaste. A adição de 1-2% de óxido de tório ao tungstênio puro produz eletrodos de tungstênio toriados, que têm maior capacidade de emissão de elétrons do que os eletrodos de tungstênio puro.
Sob as mesmas condições de diâmetro do eletrodo, eletrodos de tungstênio toriados podem ser usados em correntes mais altas com taxas de queima mais lentas.
Eletrodos de tungstênio ceriados e eletrodos zircônicos.
Os eletrodos de tungstênio toriado são radioativos e podem ser prejudiciais à saúde. Eletrodos de tungstênio ceriados são produzidos pela adição de 2% de cério ao tungstênio puro, o que pode reduzir a contaminação radioativa e, ao mesmo tempo, melhorar ainda mais a capacidade de emissão de elétrons e o desempenho do processo.
Esta é uma escolha mais ideal para o material do eletrodo traseiro, pois reduz as taxas de queima do eletrodo. Eletrodos zirconiados podem usar ar como gás de trabalho e têm uma vida útil próxima à dos eletrodos de tungstênio toriado quando trabalham em gás misto N2+H2.
3. Gás de trabalho do arco de plasma.
Os gases de trabalho comumente usados para corte a arco plasma são nitrogênio (N2), argônio (Ar), hidrogênio (H2) ou suas misturas. O N2 tem uma entalpia relativamente alta, propriedades químicas estáveis, baixo risco e baixo custo, tornando-o um gás de trabalho amplamente utilizado.
O nitrogênio pode se dissolver no aço para formar nitreto de ferro, o que aumenta a resistência, mas diminui a ductilidade. A pureza do nitrogênio não deve ser inferior a 99,5%. Se houver muito O2 ou água no gás, isso pode causar queimadura grave do eletrodo de tungstênio.
Gás de trabalho – Argônio
O argônio tem uma entalpia mais baixa e, conseqüentemente, a tensão do arco plasma também é baixa. Por ser um gás monoatômico, o argônio não se decompõe nem tem efeito de absorção de calor em altas temperaturas.
Sua capacidade térmica específica e condutividade térmica são pequenas, resultando em perda mínima de energia ao queimar o arco em gás argônio.
No entanto, devido ao elevado potencial de ionização do argônio, tanto o arco voltaico quanto a combustão requerem maior energia. Medidas especiais de formação de arco devem ser tomadas para resolver o problema de combustão difícil.
O argônio é um gás inerte que não reage com vários metais nem se dissolve neles. Para cortar metais quimicamente ativos, o gás argônio de alta pureza é um bom meio de proteção.
O gás argônio é mais pesado que o ar e ocorre naturalmente em concentração de cerca de 1% na atmosfera, mas extraí-lo pode ser caro. Geralmente, o argônio é um subproduto da produção de oxigênio, e o argônio de nível industrial produzido internamente já atingiu 99,99% de pureza.
O hidrogênio (H2) é o gás com maior entalpia e condutividade térmica e tem maior capacidade de transferir energia térmica.
A mistura de hidrogênio no gás de trabalho pode aumentar significativamente a potência térmica do arco de plasma, tornando-o uma escolha comum para pulverização em materiais difíceis de derreter ou corte de peças espessas.
Para a maioria dos materiais metálicos, o hidrogênio é um gás redutor que pode prevenir eficazmente a oxidação do material.
Gás de trabalho – Hidrogênio, Ar
O hidrogênio é um gás combustível que pode facilmente inflamar e explodir quando misturado ao ar.
O hidrogênio pode se dissolver em muitos metais fundidos em altas temperaturas, o que às vezes pode afetar o desempenho do processo, e o hidrogênio que penetra no aço pode facilmente causar fragilização por hidrogênio.
O ar tem uma alta capacidade de transferir energia térmica como gás de trabalho e é relativamente barato e conveniente de usar, comprimindo-o.
Gás de trabalho – Gases mistos
Além de usar ar para eletrodos de zircônio, os eletrodos de tungstênio também podem usar ar como gás de trabalho.
Ao usar ar com eletrodo de tungstênio, uma pistola de plasma de fluxo de ar de camada dupla deve ser usada, e a camada interna deve usar gases como argônio ou nitrogênio para proteger o eletrodo de tungstênio da oxidação pelo ar.
Os gases mistos comumente usados são nitrogênio-hidrogênio e argônio-hidrogênio, que combinam as vantagens de ambos os gases.
Considerações para gases mistos
Proporção de mistura:
A proporção de gases misturados utilizados pode afetar significativamente a velocidade de corte, a qualidade do corte e a vida útil do bico.
Para mistura de hidrogênio-argônio, a proporção recomendada é (20-40)% H2 para (80-60)% Ar, enquanto para mistura hidrogênio-nitrogênio, a proporção recomendada é (10-25)% H2 para (90-75) % N2.
Problema de inicialização do arco:
Iniciar arcos em misturas contendo uma grande quantidade de gás diatômico pode ser difícil. No entanto, geralmente é possível iniciar um arco com argônio puro ou gás nitrogênio puro.
4. Processo de corte por arco de plasma.
Os parâmetros do processo de corte por arco de plasma incluem:
- Tensão sem carga (U0)
- Corrente de corte (I)
- Tensão operacional (U)
- Taxa de fluxo de gás (Q)
- Velocidade de corte (v)
- Distância entre o bico e a peça de trabalho (h)
- Distância entre o eletrodo de tungstênio e a ponta do bico (l)
- Diâmetro do orifício do bico (d)
(1) Tensão sem carga (U0)
Para acender e manter um arco plasma estável, recomenda-se uma tensão mínima sem carga de 150V. Ao cortar materiais mais espessos (acima de 200 mm), é necessária uma tensão sem carga mais alta, superior a 200 V.
Para cortar materiais muito espessos, a tensão sem carga pode chegar a 300-400V. A alta tensão sem carga pode aumentar o risco de choque elétrico, por isso é importante tomar medidas de segurança adequadas ao trabalhar com equipamento de corte a plasma.
(2) Corrente de corte (I) e tensão de operação (U)
A corrente de corte e a tensão operacional determinam a potência do arco plasma. Aumentar a corrente de corte e a tensão operacional pode aumentar a potência térmica do arco plasma, permitindo velocidades de corte mais altas e maior eficiência ao cortar materiais mais espessos.
À medida que a corrente de corte aumenta, a velocidade de corte também pode aumentar significativamente. Contudo, o efeito do aumento da corrente de corte na velocidade de corte torna-se menos significativo à medida que a espessura do material a ser cortado aumenta.
Maneiras eficazes de aumentar a potência:
Aumentar a corrente fará com que a coluna do arco fique mais espessa, resultando em um corte mais amplo e queima mais fácil do bico do eletrodo de tungstênio. Aumentar a tensão é uma forma eficaz de aumentar a potência do arco plasma, especialmente ao cortar materiais espessos. A tensão de trabalho U está relacionada à composição do gás e à vazão. O U para N2 é maior que o de Ar. H2 requer U mais alto devido à sua forte capacidade de dissipação de calor.
Tensão de trabalho do arco plasma
Quando U > 0,65U0, o arco plasma exibirá um fenômeno instável conhecido como arco duplo. Ao aumentar a tensão de trabalho do arco plasma, é necessário aumentar também a tensão sem carga da fonte de alimentação. U também está relacionado à forma geométrica do bico, especialmente à abertura do bico d.
Taxa de fluxo de gás Q
Quando outras condições são iguais, um aumento em Q aumentará o efeito de contração térmica da coluna do arco, resultando em energia mais concentrada. À medida que Q aumenta, U aumenta, levando a um aumento na potência do arco plasma, na temperatura da coluna do arco e na velocidade v.
Ao mesmo tempo, a velocidade do jato do arco aumenta, a força de corte é aumentada e a qualidade do corte também é melhorada.
No entanto, se Q for muito grande, parte da energia será retirada pelo ar frio, resultando numa diminuição na quantidade de calor disponível para derreter o metal, o que pode afetar a estabilidade da combustão do arco e do corte normal.
(4) Velocidade de corte v
Uma velocidade de corte apropriada v pode melhorar a qualidade da superfície do corte.
Quando a potência é constante, aumentar v diminuirá a área aquecida da peça e o tamanho da zona afetada pelo calor.
Se v for muito alto, o material a ser cortado poderá não derreter. Se v for muito lento, a produtividade diminuirá, a superfície do corte ficará áspera, as rebarbas aumentarão na parte inferior e a peça de trabalho se deformará mais significativamente.
Desde que a qualidade do corte seja garantida, a velocidade de corte v deve ser aumentada tanto quanto possível.
(5) Distância do bico à peça de trabalho h
Para utilizar totalmente o calor gerado pelo arco plasma e facilitar sua operação, a distância h entre o bico e a superfície da peça deve ser controlada dentro de 10 mm. Normalmente, essa distância é definida para 4-7 mm.

O impacto de h no arco plasma
Aumentar h equivale a aumentar o comprimento do arco, o que leva a um aumento em U.
No entanto, à medida que o comprimento do arco aumenta, a eficiência diminui e a energia da radiação térmica aumenta, o que pode causar uma diminuição em v. Se h for muito alto, a força de sopro e a capacidade de corte diminuirão, levando a um aumento nas rebarbas inferiores e à possibilidade de duplicação. arco. Se h for muito pequeno, existe um risco aumentado de curto-circuito.
(6) Parâmetros do bico – l, d
l refere-se à distância entre a extremidade do eletrodo de tungstênio e a extremidade do bico, que está relacionada ao fato de o arco poder ser comprimido adequadamente.
Se l for muito grande, destruirá a estabilidade do arco. Se l for muito pequeno, pode causar um curto-circuito entre o eletrodo de tungstênio e o bico, podendo queimar o bico.
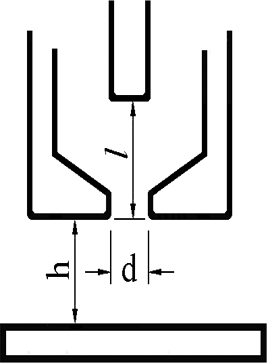
O diâmetro do bocal d afeta o diâmetro e a temperatura da coluna do arco. Um aumento em d resultará em uma diminuição na compressão, na densidade de energia, na força de corte e na velocidade de corte v. Isso também pode causar uma diminuição na capacidade de corte.
Em geral, d menor está associado a U maior, enquanto d maior está associado a U menor.
5. Características de corte de peças grossas.
À medida que a espessura t aumenta, a quantidade de material fundido também aumenta, o que requer um aumento de potência.
Para reduzir o esgotamento, recomenda-se aumentar U mantendo a potência constante. À medida que t aumenta, a faixa de saltos pontuais do ânodo também aumenta e, portanto, U deve ser maior que 220 V para garantir a estabilidade do arco. É necessário calor suficiente para cortar o fundo, resultando em um arco fino e alongado com um pequeno gradiente de temperatura axial.
Recomenda-se gás de trabalho com alta entalpia e condutividade térmica, como N2+H2.
Método de corte a laser
(1) Introdução ao princípio do corte a laser
O feixe de laser horizontal emitido pelo cortador a laser.
Depois de ser refletido por um espelho de 45 graus, o feixe de laser é redirecionado verticalmente para baixo.
O feixe de laser é então focado por uma lente, criando um ponto extremamente pequeno no ponto focal.
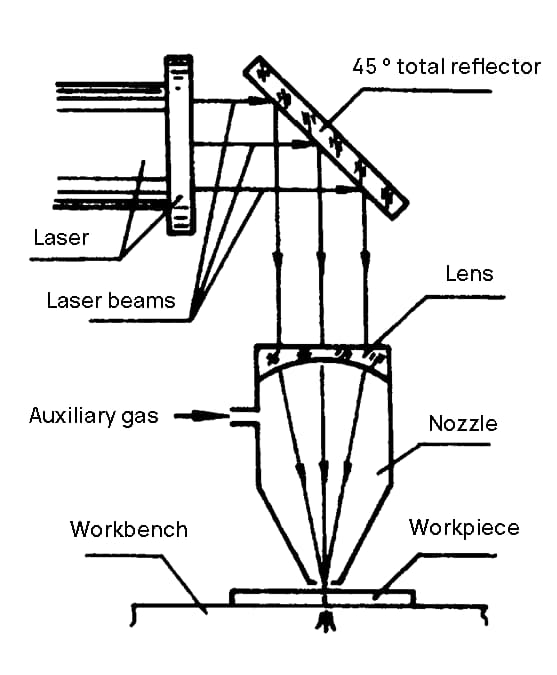
Corte a laser
A densidade de potência do spot chega a 106-109 C/cm2. Quando a peça de trabalho é irradiada pelo ponto de laser, gera uma alta temperatura localizada (acima de 10.000 ℃), fazendo com que a peça de trabalho derreta ou vaporize instantaneamente. À medida que o bico de corte se move, um corte é formado na peça de trabalho.
Enquanto isso, um gás auxiliar com uma certa pressão é usado para soprar a escória fundida no corte, cortando assim a peça de trabalho.
Potência laser
O feixe de laser é um feixe paralelo ideal (com ângulo de divergência θ <0,001 radianos). Após focar, o diâmetro do ponto pode ser representado por dó = fθ (onde θ ≠ 0), onde f é a distância focal da lente. Se a potência do laser for W, então a densidade de potência do ponto é:
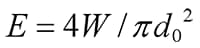
Características do corte a laser
Comparado ao corte a gás e ao corte a arco de plasma, o corte a laser tem as seguintes vantagens:
- Velocidade de corte mais rápida
- Largura de corte mais estreita (cerca de 0,2-0,3 mm)
- Zona afetada pelo calor menor (com uma largura de cerca de 0,1 mm)
- Melhor perpendicularidade na borda do corte
- Maior qualidade de acabamento superficial da aresta de corte
Aplicações de corte a laser
O corte a laser apresenta vantagens notáveis no corte de chapas finas, melhorando a eficiência do corte e reduzindo a deformação térmica.
Ele pode cortar vários materiais de alto ponto de fusão, ligas resistentes ao calor e materiais superduros, bem como semicondutores, materiais não metálicos e materiais compósitos.
Ao cortar metais espessos, gás comprimido é soprado para auxiliar no corte, reduzindo a largura do corte e a zona afetada pelo calor.
(2) Aplicações práticas de corte a laser
A aplicação da tecnologia de corte a laser remonta à década de 1970. Atualmente, a Marinha dos EUA é líder no uso de tecnologia laser para pesquisas em construção naval. Nos últimos anos,
O Japão produziu e vendeu máquinas de corte a laser CNC com potência abaixo de 5 kW, que podem cortar aço de baixo carbono de até 32 mm de espessura com alta qualidade. Ao cortar uma placa de 12 mm, a velocidade de corte é de cerca de 2,5 m/min, o que é comparável às máquinas de corte a arco de plasma existentes.
O corte a laser tem muitas aplicações em estaleiros, incluindo:
O Estaleiro Tamano da Mitsui Zosen Corporation constrói principalmente navios de guerra e também graneleiros de 40.000 toneladas. A maioria das espessuras de chapas para componentes de navios é de cerca de 10 mm e é necessária uma proporção significativa de processamento de chapas de aço finas. As estruturas dos navios requerem baixa deformação térmica e alta precisão de corte devido à estrutura relativamente fina das placas de aço utilizadas. A utilização de máquinas de corte a laser na produção de chapas de aço para carrocerias de navios tem alcançado resultados significativos.
Máquina de corte a laser do estaleiro Yunao
A máquina de corte a laser CO2 de fabricação japonesa para aeronaves, com bitola de 7,5 m, tem potência máxima de 3,5 kW (potência nominal de 3 kW). Possui uma largura de corte efetiva de 5,4 m, comprimento de corte efetivo de 29,1 m e pode cortar até uma espessura máxima de 19 mm. A velocidade de corte para chapas com espessura de 8-10 mm está entre 900-1000 mm/min. A largura da incisão é inferior a 0,5 mm e a deformação do corte é mínima. Não há colapso da borda superior ou escória da borda inferior e a precisão do corte é muito maior do que o corte por arco de plasma.