Muitos leigos pensam que a impressão 3D consiste apenas em extrair material de um bico quente e empilhá-lo em formas, mas a impressão 3D vai muito além disso! Hoje, apresentamos sete tipos de processos de impressão 3D para ajudar a diferenciar as diversas técnicas de impressão 3D.
Na verdade, a impressão 3D, também conhecida como manufatura aditiva, é um termo geral que abrange vários processos de impressão 3D distintos. Essas tecnologias variam muito, mas os processos principais são os mesmos.
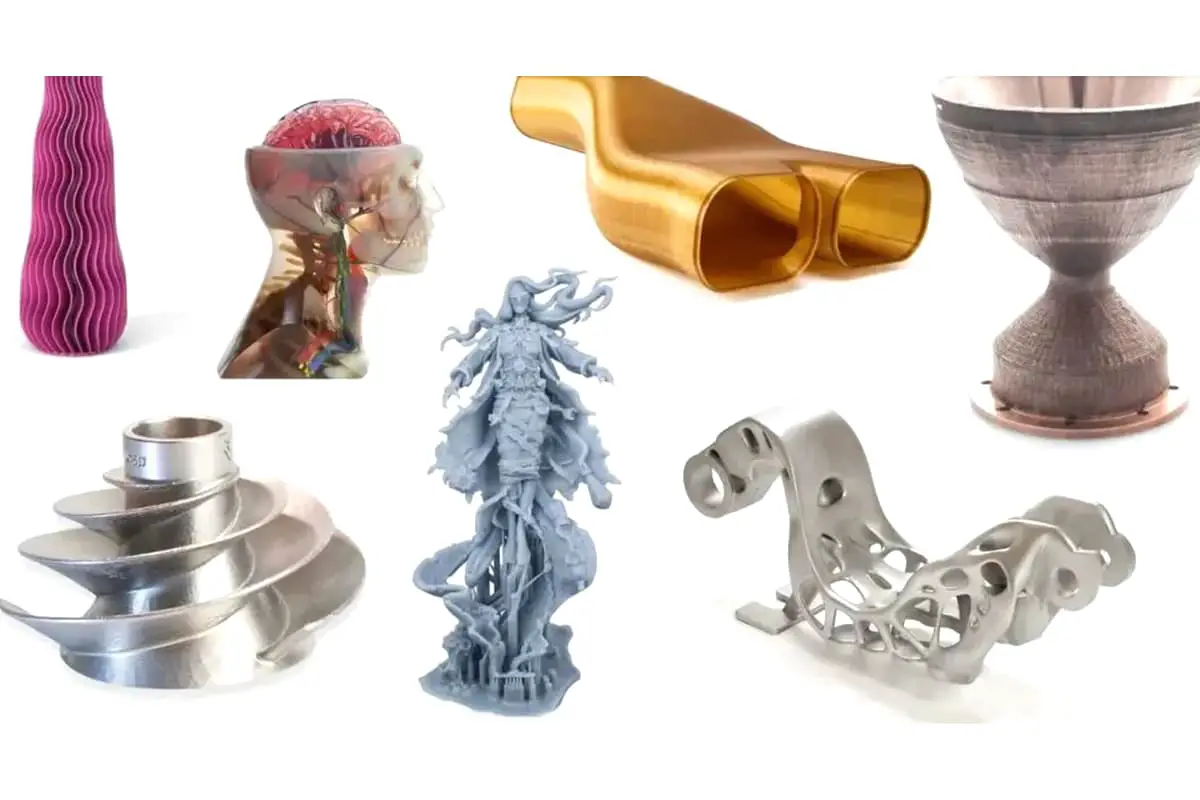
Por exemplo, toda impressão 3D começa com um modelo digital porque a tecnologia é essencialmente digital. A peça ou produto é inicialmente projetado usando software de design auxiliado por computador (CAD) ou proveniente de uma biblioteca de peças digitais.
O arquivo de design é então dividido em fatias ou camadas para impressão 3D por meio de um software específico de preparação de construção, gerando instruções de caminho a serem seguidas pela impressora 3D.
A seguir, você aprenderá as diferenças entre essas tecnologias e os usos típicos de cada uma.
Por que existem 7 tipos?
Os tipos de manufatura aditiva podem ser categorizados pelos produtos que produzem ou pelos tipos de materiais que utilizam. A Organização Internacional de Normalização (ISO) dividiu-as em sete tipos gerais (embora estas sete categorias de impressão 3D mal consigam cobrir o número crescente de subtipos e tecnologias híbridas).
- Extrusão de Materiais
- Fotopolimerização de cuba
- Fusão em Leito de Pó
- Jateamento de materiais
- Jateamento de encadernação
- Deposição dirigida de energia
- Laminação de Folhas
I. Extrusão de Material
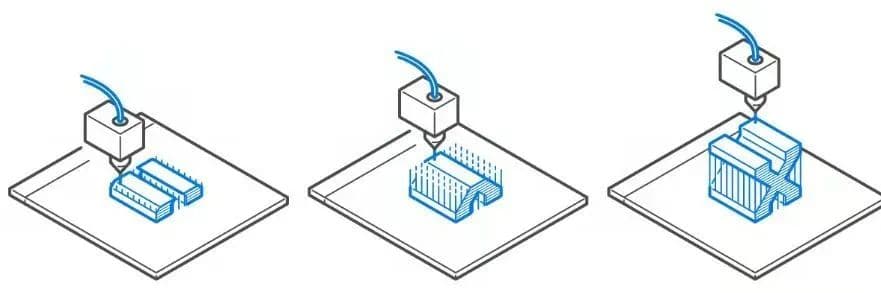
Como o nome sugere, a extrusão de material envolve a extrusão do material através de um bico.
Normalmente, este material é um filamento de plástico que é derretido e extrudado através de um bico aquecido. A impressora coloca o material na plataforma de construção ao longo do caminho do processo obtido através do software. O filamento então esfria e solidifica em um objeto sólido. Esta é a forma mais comum de impressão 3D.
Pode parecer simples à primeira vista, mas considerando os materiais extrudados, incluindo plástico, metal, concreto, biogéis e vários alimentos, é na verdade uma categoria muito ampla. O preço desse tipo de impressora 3D varia de US$ 100 a sete dígitos.
- Subtipos de extrusão de materiais: Modelagem de Deposição Fundida (FDM), Impressão 3D de Construção, Impressão Micro 3D, Impressão Bio 3D.
- Materiais: Plástico, Metal, Alimentos, Concreto, etc.
- Precisão dimensional: ±0,5% (limite inferior ±0,5 mm).
- Aplicações comuns: Protótipos, gabinetes elétricos, testes de forma e ajuste, gabaritos e acessórios, modelos de fundição de investimento, casas, etc.
- Vantagens: Método de impressão 3D de menor custo, ampla variedade de materiais.
- Desvantagens: Normalmente menor desempenho do material (resistência, durabilidade, etc.), geralmente sem alta precisão dimensional.
1. Modelagem de Deposição Fundida (FDM)
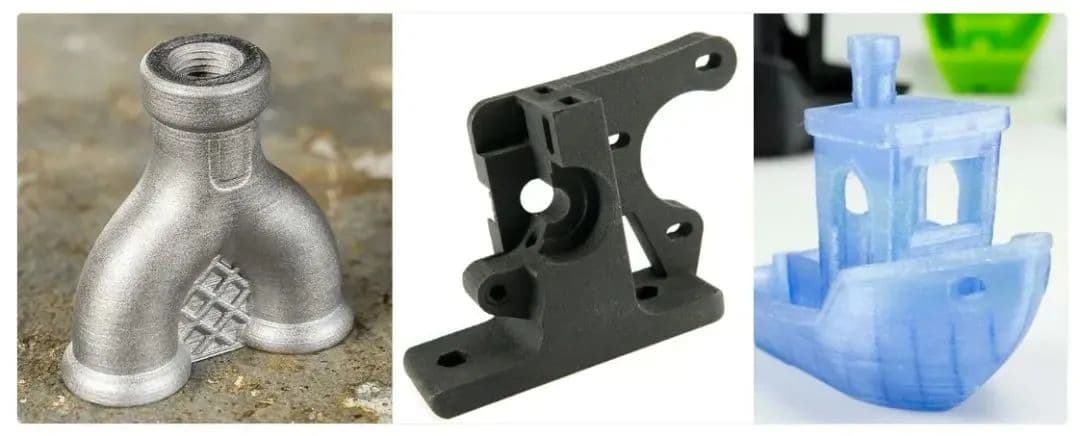
O mercado de impressoras 3D FDM vale bilhões de dólares, com milhares de máquinas que vão desde modelos básicos até modelos complexos de fabricantes. As máquinas FDM são chamadas de Fused Filament Fabrication (FFF), que é inteiramente a mesma tecnologia.
Como todas as tecnologias de impressão 3D, o FDM começa com um modelo digital e depois o converte em um caminho que a impressora 3D pode seguir. Com o FDM, um filamento (ou vários filamentos ao mesmo tempo) de uma bobina de linha é carregado na impressora 3D e depois alimentado no bocal da impressora na cabeça de extrusão.
O bocal da impressora ou vários bocais são aquecidos até a temperatura necessária para amolecer o filamento, permitindo que as camadas contínuas se unam para formar uma peça sólida.
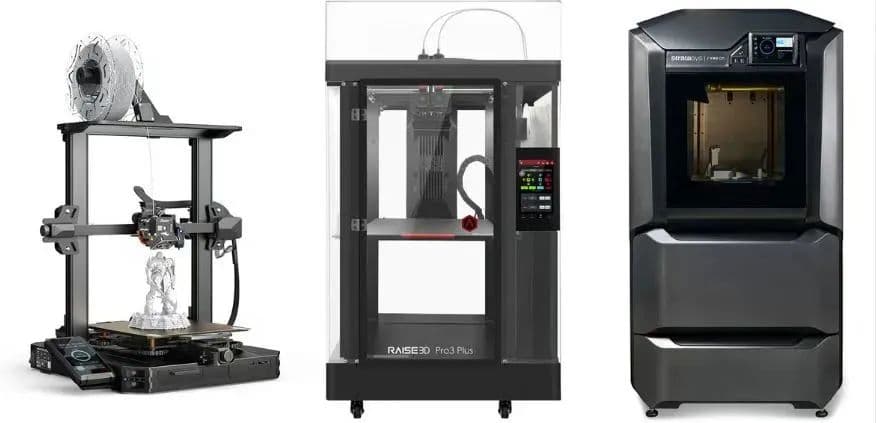
À medida que a impressora move a cabeça de extrusão ao longo das coordenadas especificadas no plano XY, ela continua a colocar a primeira camada. A cabeça de extrusão sobe então para a próxima altura (plano Z) e repete o processo de impressão de seções transversais, construindo camada por camada até que o objeto esteja totalmente formado.
Dependendo da geometria do objeto, às vezes pode ser necessário adicionar estruturas de suporte para apoiar o modelo durante a impressão, por exemplo, se o modelo tiver saliências íngremes. Esses suportes são removidos após a impressão. Alguns materiais de estrutura de suporte podem dissolver-se em água ou outra solução.
2. Bioimpressão 3D
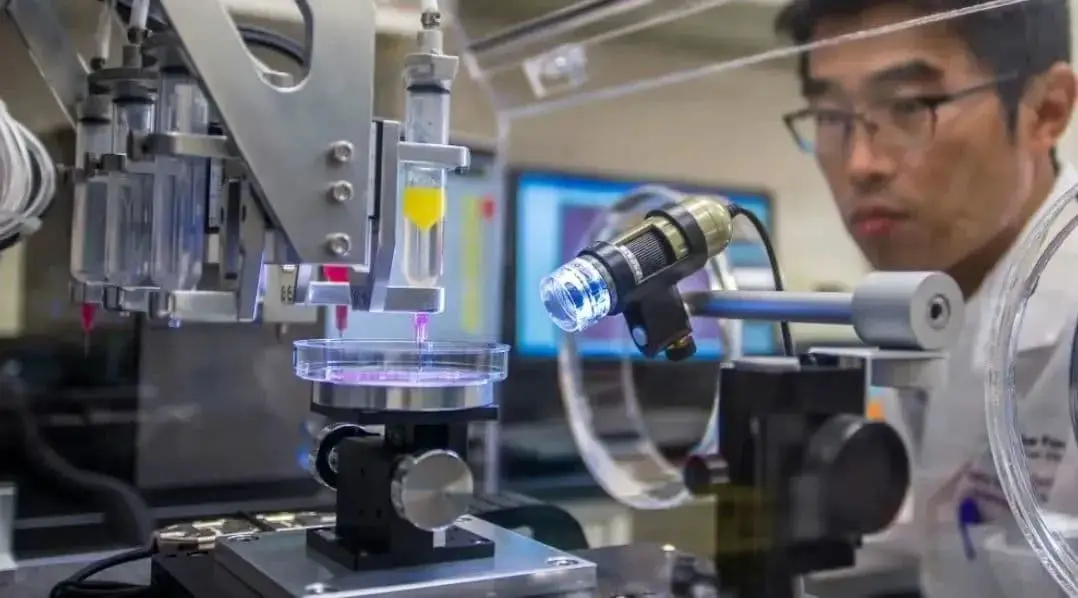
A bioimpressão 3D, ou bioimpressão 3D, é um processo de fabricação aditiva onde materiais orgânicos ou biológicos (como células vivas e nutrientes) são combinados para criar estruturas tridimensionais naturais semelhantes a tecidos.
Em outras palavras, a bioimpressão é uma forma de impressão 3D que pode produzir qualquer coisa, desde tecidos e vasos esqueléticos até tecidos vivos. É usado para diversas pesquisas e aplicações médicas, incluindo engenharia de tecidos, testes e desenvolvimento de medicamentos e terapias médicas regenerativas inovadoras. A definição real de bioimpressão 3D ainda está em evolução.
Essencialmente, a bioimpressão 3D funciona de forma semelhante à impressão 3D FDM e pertence à série de extrusão de materiais (embora a extrusão não seja o único método de bioimpressão).
A bioimpressão 3D utiliza material (biotinta) ejetado de agulhas para criar camadas impressas. Esses materiais, conhecidos como biotintas, consistem principalmente de matéria viva, como células em materiais transportadores – como colágeno, gelatina, ácido hialurônico, seda, alginato ou nanocelulose, atuando como estruturas moleculares para crescimento estrutural e nutrientes, fornecendo suporte.
3. Impressão 3D arquitetônica
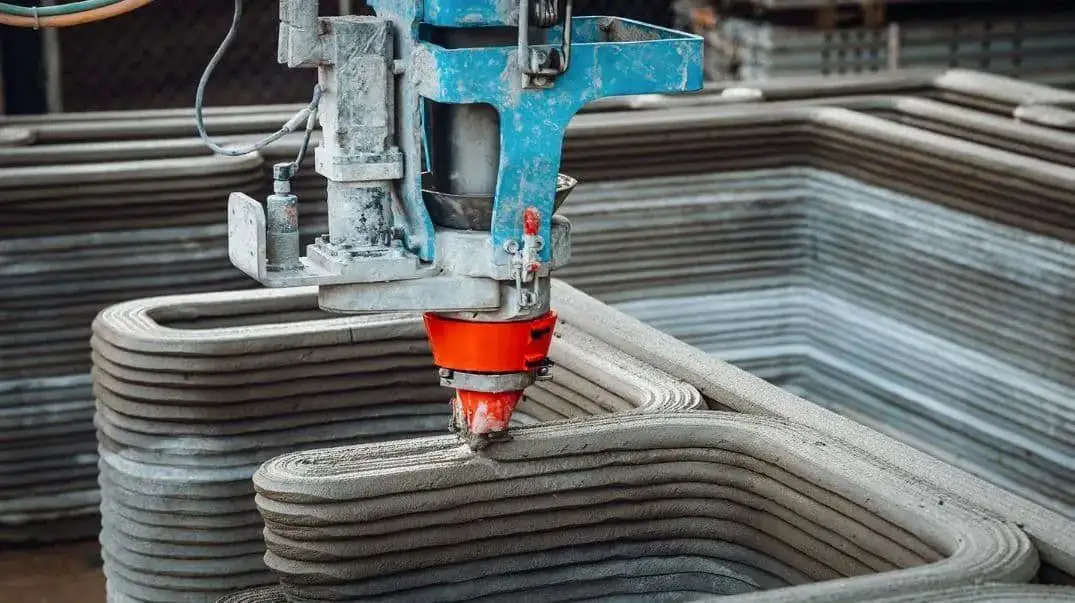
A impressão 3D arquitetônica é um campo de rápido avanço na extrusão de materiais. Essa tecnologia envolve o uso de impressoras 3D gigantescas, geralmente com vários metros de altura, para extrusar materiais de construção como concreto a partir de um bocal.
Essas máquinas normalmente aparecem em sistemas de pórtico ou de braço robótico. Hoje, a tecnologia de impressão arquitetônica 3D é usada em habitações, características arquitetônicas e vários projetos de construção, de poços a paredes. Os investigadores sugerem que tem potencial para transformar significativamente toda a indústria da construção, reduzindo a procura de mão-de-obra e minimizando o desperdício de construção.
Existem dezenas de casas impressas em 3D nos Estados Unidos e na Europa, e estão sendo conduzidas pesquisas sobre tecnologia de construção 3D que usaria materiais encontrados na Lua e em Marte para construir habitats para futuros exploradores. A substituição da impressão de concreto por solo local como método de construção mais sustentável também está ganhando atenção.
II. Agregação de Resina
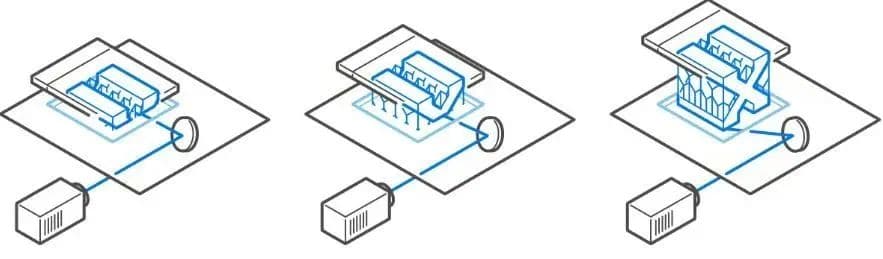
A polimerização de cuba (também conhecida como impressão 3D em resina) é uma série de processos de impressão 3D que cura (ou endurece) seletivamente a resina polimérica fotossensível em uma cuba usando uma fonte de luz. Em outras palavras, a luz é direcionada com precisão para pontos ou áreas específicas do plástico líquido para endurecê-lo.
Após a cura da primeira camada, a plataforma de construção move-se ligeiramente para cima ou para baixo (dependendo da impressora), geralmente entre 0,01 e 0,05 milímetros, e a próxima camada é curada e conectada à anterior.
Este processo é repetido camada por camada até que uma peça 3D seja formada. Após a conclusão do processo de impressão 3D, o objeto é limpo para remover qualquer resina líquida restante e pós-curado (à luz solar ou em câmara UV) para melhorar as propriedades mecânicas da peça.
As três formas mais comuns de polimerização em cuba são a estereolitografia (SLA), o processamento digital de luz (DLP) e o display de cristal líquido (LCD), também conhecido como estereolitografia mascarada (MSLA). A diferença fundamental entre estes tipos de tecnologias de impressão 3D reside na fonte de luz e na forma como ela é utilizada para curar a resina.

Vários fabricantes de impressoras 3D, especialmente aqueles que produzem impressoras 3D de nível profissional, desenvolveram variações exclusivas e patenteadas de fotopolimerização, portanto, você poderá ver diferentes nomes de tecnologia no mercado.
O fabricante de impressoras 3D industriais Carbon usa uma tecnologia de polimerização de cuba chamada Digital Light Synthesis (DLS), a Origin da Stratasys chama sua tecnologia de Fotopolimerização Programável (P3), a Formlabs oferece sua tecnologia chamada Low Force Stereolithography (LFS) e a Azul 3D é a primeira a comercializar polimerização de cuba em grande escala em uma forma chamada High Area Rapid Printing (HARP).
Outras tecnologias incluem Fabricação de Metal Baseada em Litografia (LMM), Micro Estereolitografia de Projeção (PμSL) e Fabricação de Composto Digital (DCM), uma tecnologia de fotopolímero preenchido que introduz aditivos funcionais (como fibras metálicas e cerâmicas) na resina líquida.
- Tipos de tecnologias de impressão 3D: Estereolitografia (SLA), Tela de Cristal Líquido (LCD), Processamento Digital de Luz (DLP), Micro Estereolitografia (μSLA), etc.
- Materiais: Resinas Fotopoliméricas (moldáveis, transparentes, industriais, biocompatíveis, etc.)
- Precisão dimensional: ±0,5% (com limite inferior de ±0,15 mm ou 5 nm, usando μSLA)
- Aplicações comuns: Protótipos de polímeros semelhantes a moldes de injeção e peças de uso final, fundição de joias, aplicações odontológicas, bens de consumo
- Vantagens: Acabamentos de superfície lisos, detalhes finos.
1. Estereolitografia (SLA)
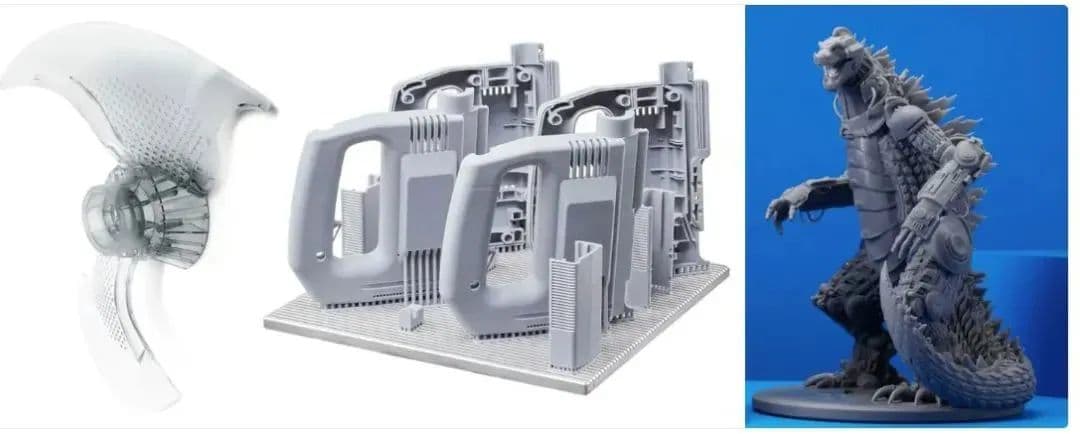
A estereolitografia, ou SLA, é a primeira tecnologia de impressão 3D do mundo. Inventado em 1986 por Chuck Hull, que patenteou a tecnologia e fundou a 3D Systems para comercializá-la, o SLA está agora disponível para entusiastas e profissionais de vários fabricantes de impressoras 3D.
O processo envolve direcionar um feixe de laser para um recipiente de resina, solidificando seletivamente seções transversais do objeto dentro da área de impressão em uma construção camada por camada. A maioria das impressoras SLA usa um laser de estado sólido para solidificar as peças.
Uma desvantagem dessa polimerização em cuba é que, em comparação com nosso próximo método (DLP), os lasers pontuais podem levar mais tempo para traçar a seção transversal do objeto, que emite luz para endurecer instantaneamente toda a camada. No entanto, os lasers podem produzir luz mais forte, o que é necessário para algumas resinas de nível de engenharia.
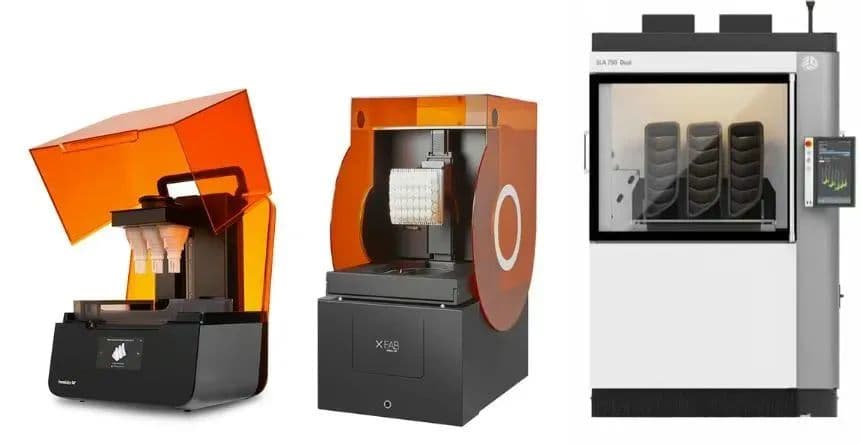
(1) Microestereolitografia (μSLA)
A tecnologia de microestereolitografia pode imprimir peças em miniatura com resolução entre 2 micrômetros (μm) e 50 μm. Para referência, a largura média de um fio de cabelo humano é de 75 μm. É uma das tecnologias de “micro impressão 3D”.
μSLA envolve a exposição de material fotossensível (resina líquida) a um laser ultravioleta. O que o diferencia é a resina especializada, a complexidade do laser e a adição de lentes que produzem pontos de luz incrivelmente pequenos.
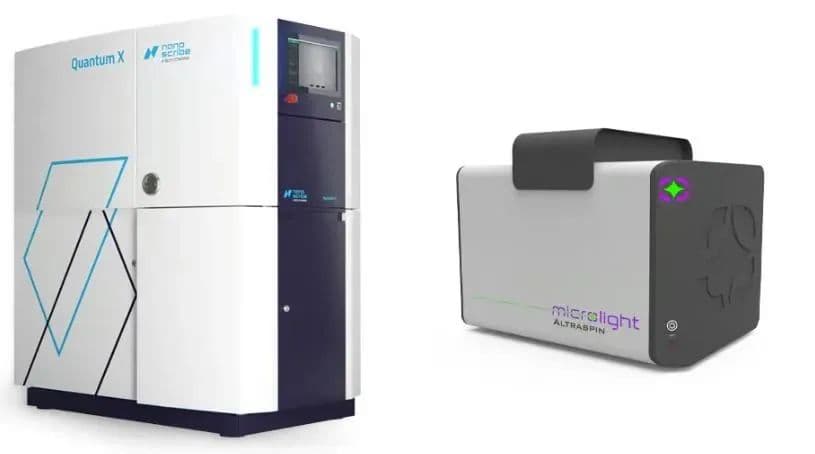
(2) Polimerização de Dois Fótons (TPP)
Outra tecnologia de microimpressão 3D, TPP (também conhecida como 2PP), pode ser categorizada em SLA porque também usa laser e resina fotossensível. Ele pode imprimir peças menores que μSLA, tão pequenas quanto 0,1 μm. O TPP usa um laser pulsado de femtosegundo focado em um ponto estreito dentro de um grande tanque de resina especial.
Esse ponto é então usado para solidificar pixels 3D únicos, ou voxels, dentro da resina. Esses minúsculos voxels, variando de tamanho nano a micro, são solidificados camada por camada ao longo de um caminho predefinido. O TPP é atualmente usado em pesquisa, aplicações médicas e na fabricação de micropeças, como microeletrodos e sensores ópticos.
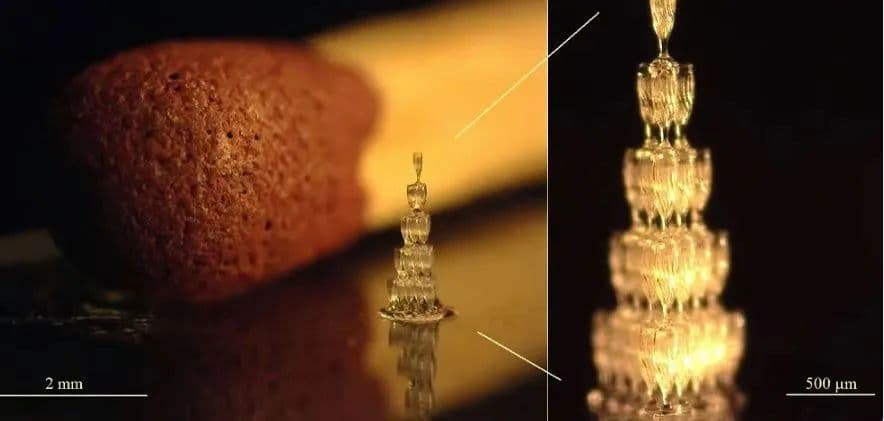
2. Processamento Digital de Luz (DLP)
A impressão 3D DLP usa um projetor de luz digital (em vez de um laser) para exibir a imagem de cada camada (ou múltiplas exposições para peças maiores) em uma camada ou recipiente de resina. O DLP (mais comum que o SLA) é usado para produzir peças maiores ou volumes maiores de peças em um único lote, pois a exposição de cada camada leva o mesmo tempo, independentemente do número de peças na construção, tornando-o mais eficiente do que o ponto. método laser em SLA.
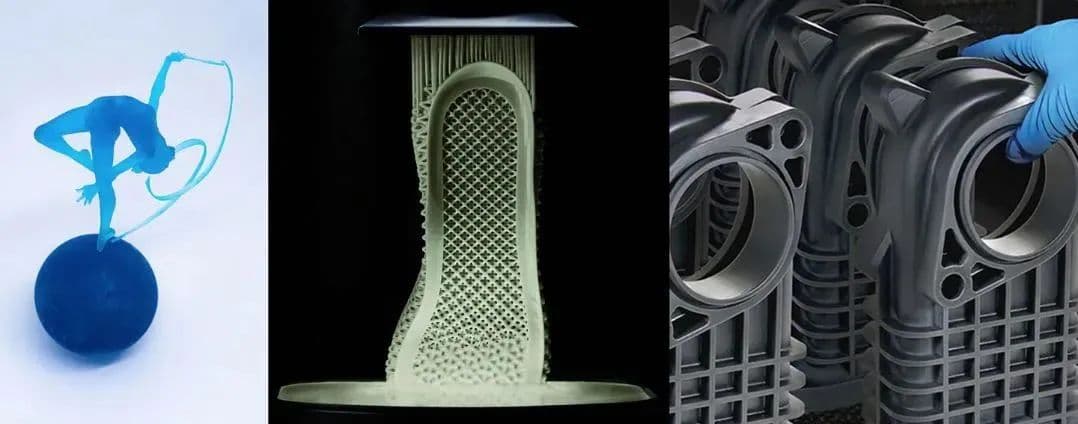
A imagem de cada camada é composta por pixels quadrados, resultando em uma camada composta por pequenos blocos retangulares chamados voxels. A luz é projetada na resina usando uma tela de diodo emissor de luz (LED) ou uma fonte de luz UV (lâmpada) e é projetada na superfície de construção através de um dispositivo de microespelho digital (DMD).
Os projetores DLP modernos normalmente possuem milhares de LEDs de tamanho micro como fontes de luz. Seus estados ligado/desligado são controlados individualmente, aumentando a resolução XY. Nem todas as impressoras 3D DLP são iguais, com diferenças significativas na potência da fonte de luz, nas lentes pelas quais ela passa, na qualidade do DMD e em muitos outros componentes que compõem uma máquina que vale US$ 300 em comparação com outras que valem mais de US$ 200.000.
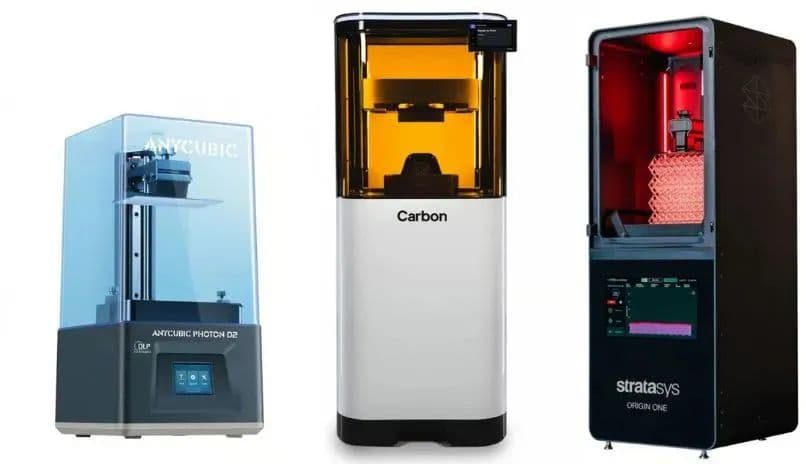
DLP de cima para baixo
Algumas impressoras DLP 3D montam a fonte de luz na parte superior da impressora, iluminando o recipiente de resina em vez de para cima. Essas máquinas “de cima para baixo” exibem uma imagem de uma camada de cima, solidificando uma camada de cada vez e, em seguida, devolvendo a camada solidificada ao grande tanque.
Cada vez que a plataforma de construção é abaixada, um repintador montado no topo do grande recipiente se move para frente e para trás na resina para uniformizar a nova camada. Os fabricantes afirmam que este método produz resultados de peças mais estáveis para impressões maiores porque o processo de impressão não luta contra a gravidade.
Há limites para a quantidade de peso que pode ser suspensa verticalmente na placa de construção durante a impressão de baixo para cima. A cuba de resina também dá sustentação à peça durante a impressão, diminuindo a necessidade de estruturas de sustentação.
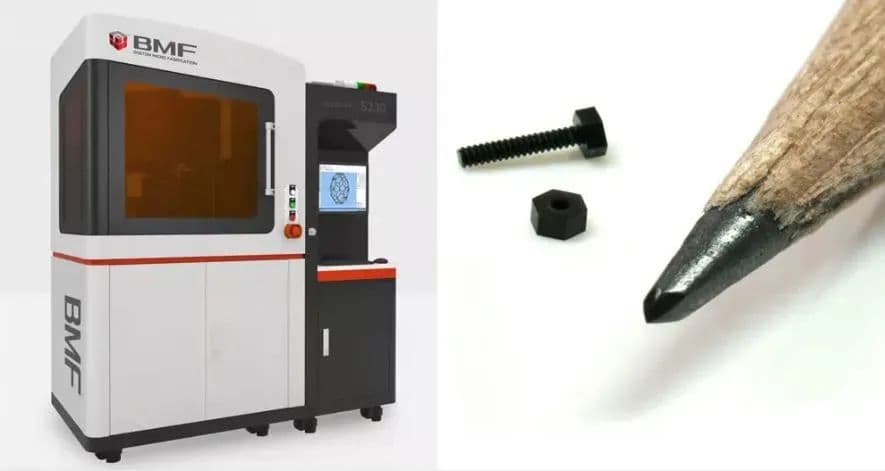
Microestereolitografia de projeção (PμSL)
Como um tipo distinto de polimerização em cuba, o PμSL é classificado em DLP como uma subcategoria. É outra tecnologia de micro impressão 3D. PμSL usa luz ultravioleta de um projetor para solidificar camadas de uma resina de fórmula especial na escala de mícron (resolução de 2 μm e altura de camada tão baixa quanto 5 μm).
Esta tecnologia de fabricação aditiva está evoluindo devido ao seu baixo custo, precisão, velocidade e variedade de materiais utilizáveis (incluindo polímeros, biomateriais e cerâmicas). Ele mostrou potencial para aplicações desde microfluídica e engenharia de tecidos até microóptica e microdispositivos biomédicos.
Fabricação de metal baseada em litografia (LMM)
Este parente distante do DLP é um método de impressão 3D com luz e resina que pode criar pequenas peças metálicas para aplicações como ferramentas cirúrgicas e peças micromecânicas. No LMM, o pó metálico é disperso uniformemente em uma resina fotossensível, que é polimerizada seletivamente por meio da exposição à luz azul de um projetor.
Após a impressão, o componente polimérico da peça verde é removido, restando uma peça desvinculada totalmente metálica que é finalizada em um processo de sinterização em forno. As matérias-primas incluem aço inoxidável, titânio, tungstênio, latão, cobre, prata e ouro.
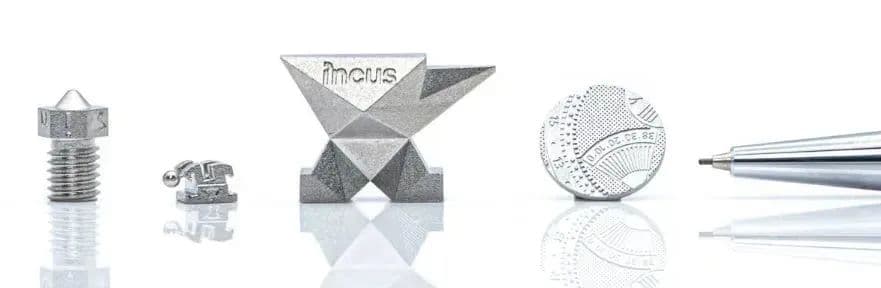
3. Tela de cristal líquido (LCD)
O Display de Cristal Líquido (LCD), também conhecido como Estereolitografia Mascarada (MSLA), é muito semelhante ao DLP mencionado. A diferença está na utilização de uma tela LCD em vez de um Digital Micromirror Device (DMD), o que afeta significativamente o preço das impressoras 3D.
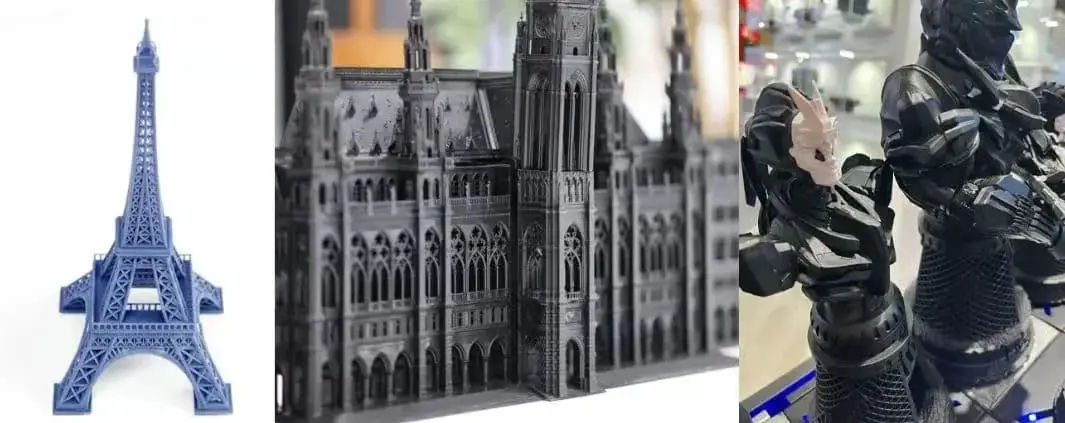
Assim como o DLP, a máscara de luz do LCD é exibida digitalmente e composta de pixels quadrados. O tamanho dos pixels na máscara de luz do LCD determina a granularidade da impressão. Como tal, a precisão XY é fixa e não depende do grau de zoom ou escala da lente, como é o caso do DLP.
Outra diferença entre as impressoras DLP e a tecnologia LCD é que esta última usa um conjunto de centenas de emissores individuais, em vez de uma fonte de luz pontual única, como diodos laser ou lâmpadas DLP.
Assim como o DLP, o LCD pode atingir tempos de impressão mais rápidos do que o SLA sob certas condições. Isso ocorre porque toda a camada é exposta de uma só vez, em vez de traçar a área da seção transversal com um ponto de laser.
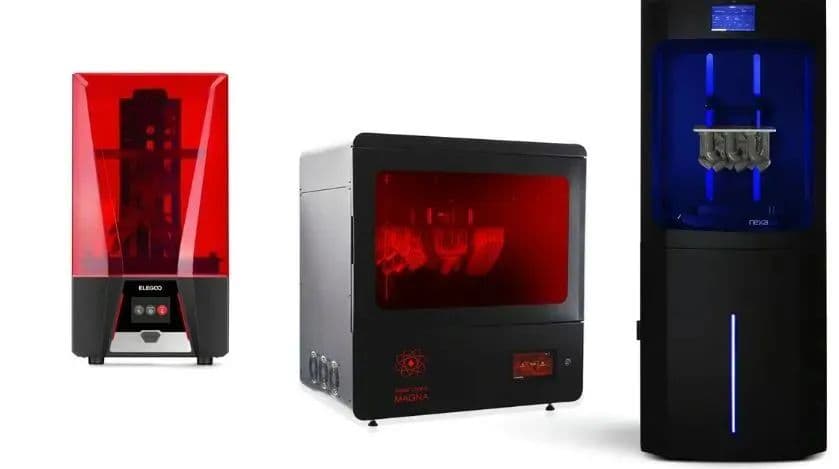
Devido ao baixo custo unitário dos LCDs, esta tecnologia tornou-se a tecnologia preferida no campo de impressoras de resina de mesa de baixo custo. No entanto, isso não significa que não seja usado profissionalmente. Alguns fabricantes de impressoras 3D industriais estão ultrapassando os limites tecnológicos e alcançando resultados impressionantes.
III. Fusão em Leito de Pó
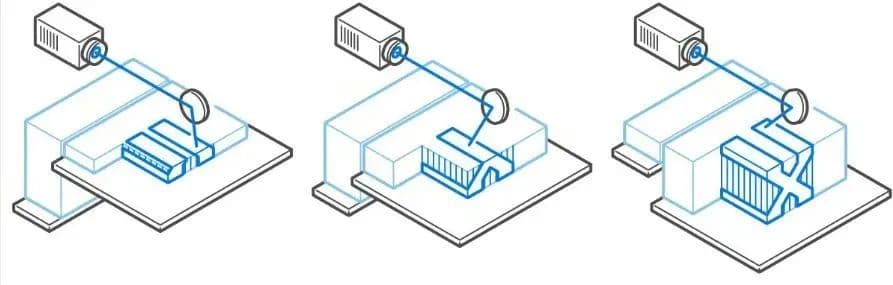
A fusão em leito de pó (PBF) é um processo de impressão 3D no qual uma fonte de energia térmica derrete seletivamente partículas de pó (plástico, metal ou cerâmica) dentro da área de construção para criar objetos sólidos camada por camada.
Uma impressora 3D PBF dispersa uma fina camada de material em pó na base de impressão, normalmente usando uma lâmina, rolo ou limpador. A energia de um laser funde pontos específicos da camada de pó e, em seguida, outra camada de pó é depositada e fundida à camada anterior. Esse processo se repete até que todo o objeto seja fabricado, com o produto final envolto e sustentado por pó não fundido.
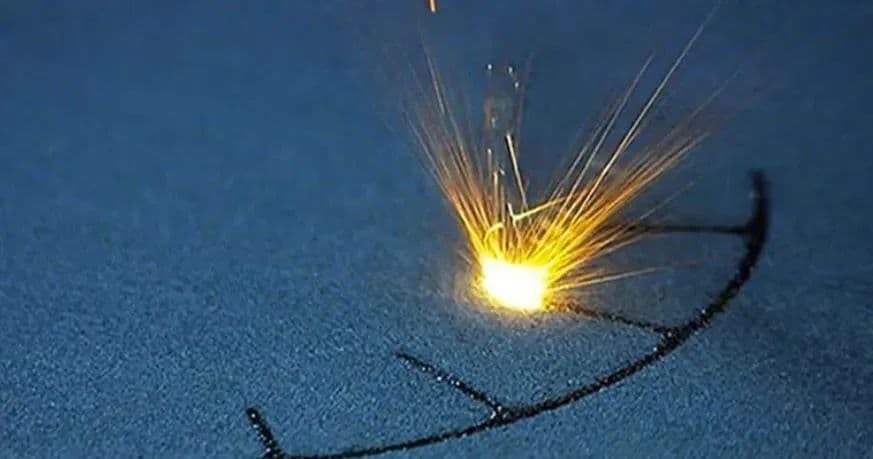
A PBF pode produzir peças com alto desempenho mecânico (incluindo resistência, resistência ao desgaste e durabilidade) para uso final em bens de consumo, máquinas e ferramentas. As impressoras 3D neste submercado estão se tornando mais baratas (a partir de cerca de US$ 25 mil), mas são consideradas uma tecnologia industrial.
- Tipos de tecnologia de impressão 3D: Sinterização seletiva a laser (SLS), fusão em leito de pó a laser (LPBF), fusão por feixe de elétrons (EBM)
- Materiais: Pó plástico, pó metálico, pó cerâmico
- Precisão dimensional: ±0,3% (limite inferior ±0,3 mm)
- Aplicações comuns: Peças funcionais, tubulações complexas (design oco), produção de peças em pequenos lotes
- Vantagens: Peças funcionais, excelente desempenho mecânico, formas geométricas complexas
- Desvantagens: Altos custos de máquinas, normalmente materiais de alto custo, velocidade de construção lenta
1. Sinterização Seletiva a Laser (SLS)
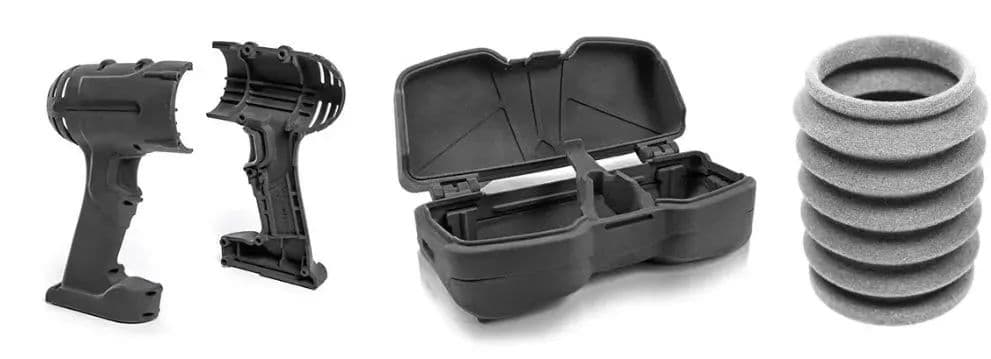
A Sinterização Seletiva a Laser (SLS) usa um laser para fabricar objetos a partir de pó plástico. Primeiro, uma caixa de pó de polímero é aquecida logo abaixo do ponto de fusão do polímero. Em seguida, uma lâmina de repintura ou limpador deposita uma camada muito fina de material em pó (geralmente com 0,1 mm de espessura) na plataforma de construção.
O laser começa a escanear a superfície de acordo com o padrão apresentado no modelo digital. O laser sinteriza seletivamente o pó e solidifica a seção transversal do objeto. Ao digitalizar toda a seção transversal, a plataforma de construção desce uma espessura de camada. A lâmina de repintura deposita uma nova camada de pó sobre a camada escaneada mais recentemente e o laser sinteriza a próxima seção transversal do objeto na seção transversal previamente solidificada.
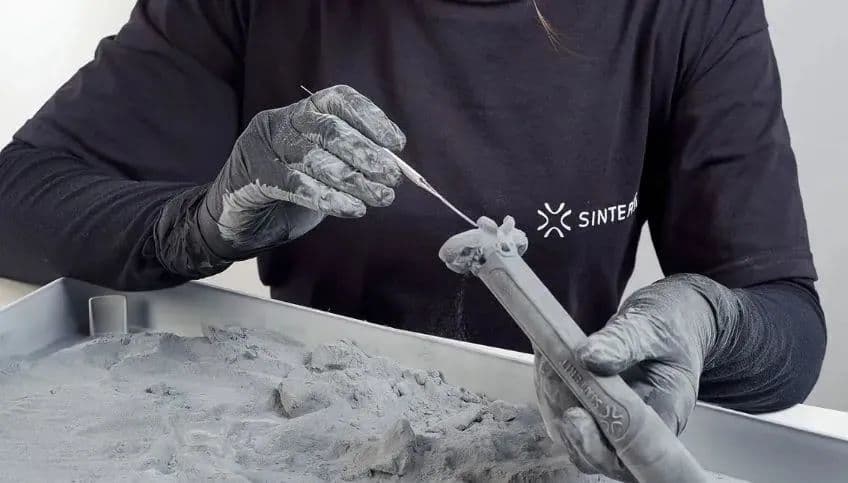
Essas etapas são repetidas até que todos os objetos sejam fabricados. O pó não sinterizado permanece no local para apoiar o objeto, reduzindo ou eliminando a necessidade de estruturas de suporte. Depois que a peça é removida do leito de pó e limpa, nenhuma outra etapa necessária de pós-processamento é necessária.
A peça pode ser polida, revestida ou colorida. Existem muitos fatores de diferenciação entre as impressoras 3D SLS, não apenas o tamanho, mas também a potência e o número de lasers, o tamanho do ponto do laser, o tempo e a forma de aquecimento da cama e a distribuição do pó. O material mais comum na impressão 3D SLS é o náilon (PA6, PA12), mas o TPU e outros materiais também podem ser usados para imprimir peças flexíveis.
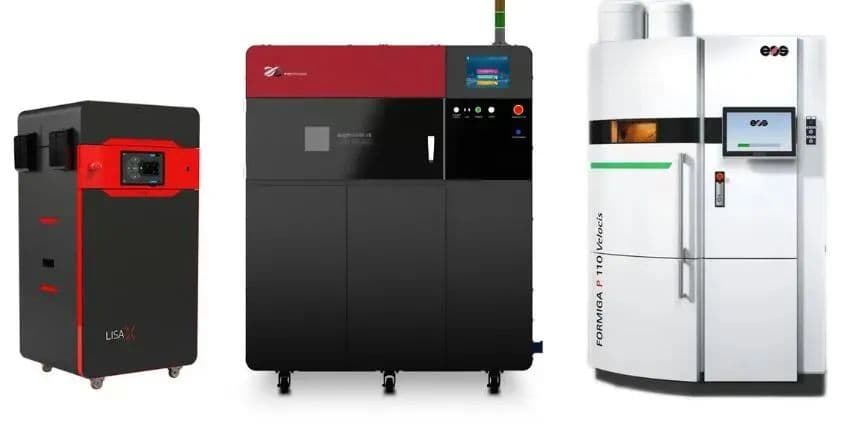
2. Sinterização Microsseletiva a Laser (μSLS)
μSLS pertence à tecnologia de SLS ou Laser Powder Bed Fusion (LPBF) mencionada abaixo. Ele usa um laser para sinterizar material em pó, como o SLS, mas esse material é normalmente metal em vez de plástico, por isso é mais parecido com o LPBF. É outra tecnologia de micro impressão 3D que pode criar peças com micro resolução (abaixo de 5 μm).
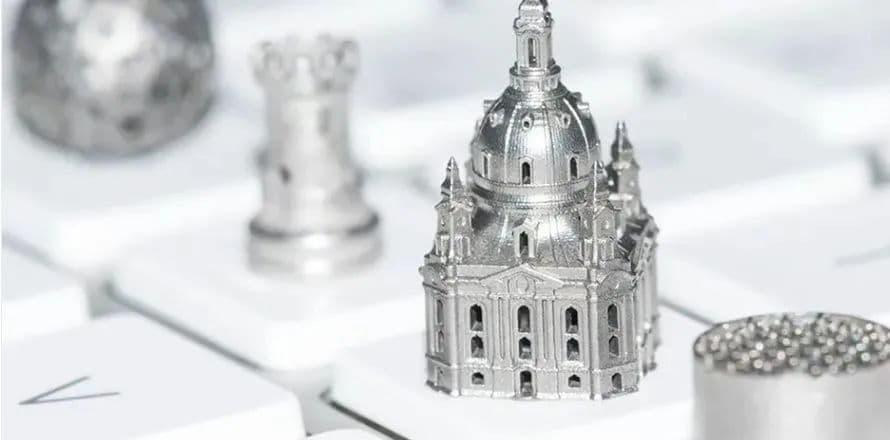
No μSLS, uma camada de tinta de nanopartículas metálicas é revestida no substrato e depois seca para produzir uma camada uniforme de nanopartículas. Em seguida, um laser padronizado de um conjunto de microespelhos digitais é usado para aquecer as nanopartículas e sinterizá-las no padrão desejado. Este conjunto de etapas é repetido para construir cada camada da peça 3D no sistema μSLS.
3. Fusão de leito de pó a laser (LPBF)
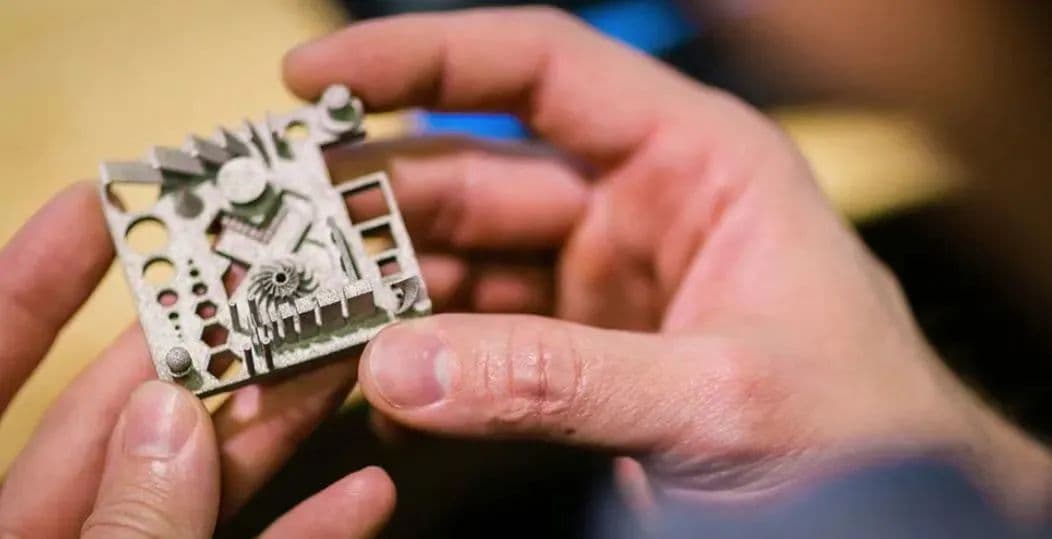
Entre todas as tecnologias de impressão 3D, esta é a que possui mais aliases. O nome formal deste método de impressão 3D de metal é Laser Powder Bed Fusion (LPBF), mas também é amplamente conhecido como Direct Metal Laser Sintering (DMLS) e Selective Laser Melting (SLM).
No início do desenvolvimento desta tecnologia, os fabricantes de máquinas criaram seus próprios nomes para o mesmo processo, e esses nomes têm sido usados desde então. Notavelmente, os três termos acima referem-se ao mesmo processo, mesmo que alguns detalhes mecânicos sejam diferentes.
Como um subtipo de fusão em leito de pó, o LPBF utiliza um leito de pó metálico e um ou mais (até 12) lasers de alta potência. As impressoras 3D LPBF usam lasers para fundir seletivamente pós metálicos em uma base molecular, camada por camada, até que o modelo esteja completo. LPBF é um método de impressão 3D altamente preciso, normalmente usado para criar peças metálicas complexas para aplicações aeroespaciais, médicas e industriais.
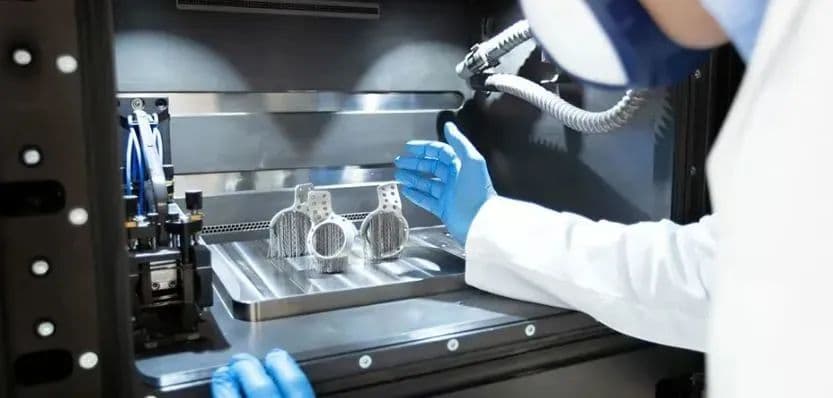
Assim como o SLS, as impressoras 3D LPBF começam com um modelo digital dividido em fatias. A impressora carrega o pó na câmara de construção e, em seguida, usa um raspador (como um limpador de para-brisa) ou rolo para espalhá-lo em uma camada fina na placa de construção. O laser traça a camada no pó.
Em seguida, a plataforma de construção desce, outra camada de pó é aplicada e fundida com a primeira camada até que todo o objeto esteja construído. A câmara de construção é fechada, selada e muitas vezes preenchida com uma mistura de gás inerte, como nitrogênio ou argônio, para garantir que o metal não oxide durante o processo de fusão e ajuda a limpar os detritos do processo de fusão.
Após a impressão, a peça é removida do leito de pó, limpa e muitas vezes passa por tratamento térmico secundário para eliminar o estresse. O pó restante é reciclado e reutilizado.
Os fatores de diferenciação das impressoras 3D LPBF incluem o tipo, a resistência e o número de lasers. As impressoras LPBF pequenas e compactas podem ter um laser de 30 watts, enquanto as versões industriais podem ter 12 lasers de 1.000 watts. As máquinas LPBF usam ligas de engenharia comuns, como aço inoxidável, superligas de níquel e ligas de titânio. Existem dezenas de metais disponíveis para o processo LPBF.
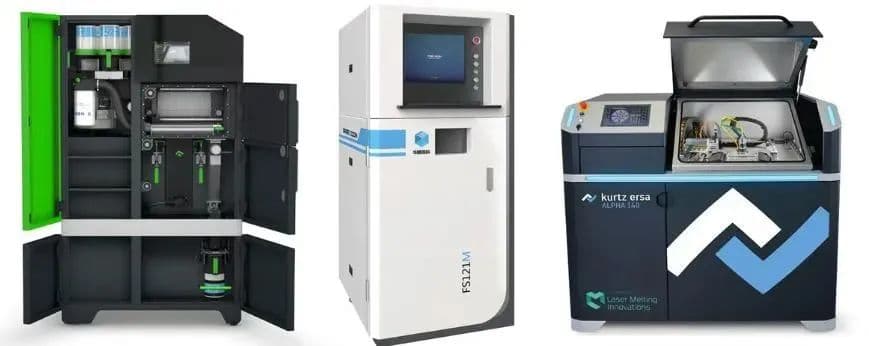
4. Fusão por feixe de elétrons (EBM)
EBM, também conhecido como Electron Beam Powder Bed Fusion (EB PBF), é um método de impressão 3D de metal semelhante ao LPBF, mas usa um feixe de elétrons em vez de um laser de fibra. Essa tecnologia é utilizada na fabricação de peças, como implantes ortopédicos de titânio, pás de turbinas para motores a jato e bobinas de cobre.
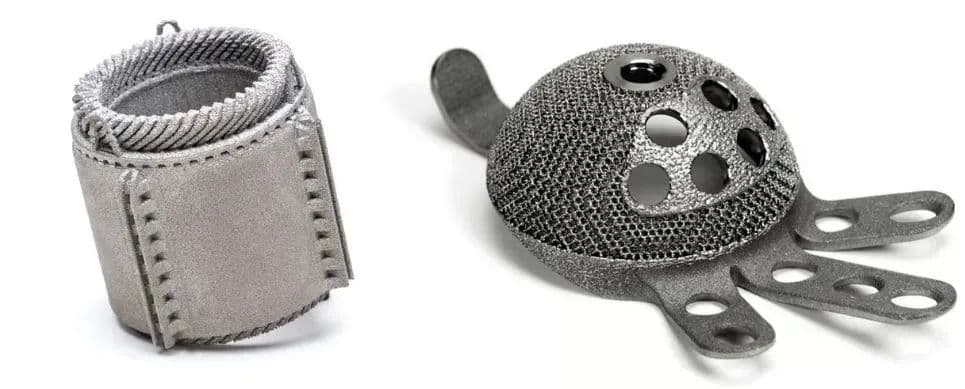
O feixe de elétrons gera mais energia e calor, necessários para alguns metais e aplicações. Além disso, o EBM não é um ambiente de gás inerte, mas é realizado numa câmara de vácuo para evitar a dispersão do feixe. A temperatura da câmara de construção pode atingir até 1.000 °C, e até mais alta em alguns casos. Como o feixe de elétrons utiliza controle de feixe eletromagnético, sua velocidade de movimento é mais rápida que a do laser e pode até ser dividida para expor múltiplas áreas simultaneamente.
Uma das vantagens do EBM sobre o LPBF é a sua capacidade de lidar com materiais condutores e metais reflexivos, como o cobre. Outra característica do EBM é sua capacidade de aninhar ou empilhar peças separadas dentro da câmara de construção, já que elas não precisam necessariamente ser fixadas na placa de construção, aumentando significativamente a produção de volume.
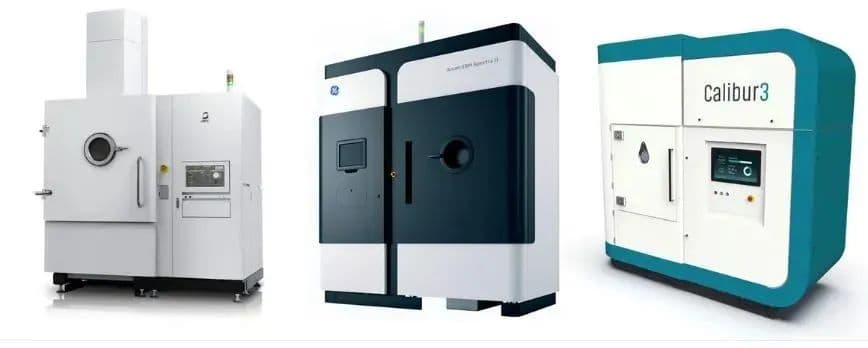
Comparados aos lasers, os feixes de elétrons geralmente produzem camadas mais espessas e superfícies mais ásperas. Devido à alta temperatura na câmara de construção, as peças impressas em EBM podem não exigir tratamento térmico pós-impressão para eliminar o estresse.
4. Jateamento de materiais
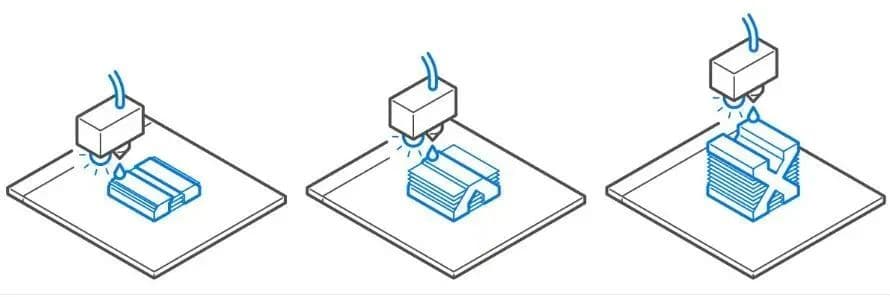
O jateamento de material é um processo de impressão 3D onde pequenas gotas de material são depositadas e depois solidificadas ou curadas em uma placa de construção. Este processo utiliza um polímero fotossensível ou gotículas de cera que solidificam quando expostas à luz, construindo objetos uma camada de cada vez.
A natureza do processo de jateamento de material permite que diferentes materiais sejam impressos no mesmo objeto. Uma aplicação dessa tecnologia é a fabricação de peças com cores e texturas variadas.
- Tipos de tecnologia de impressão 3D: Jateamento de materiais (MJ), Jateamento de nanopartículas (NPJ)
- Materiais: Resina fotossensível (padrão, fundida, transparente, resistente a altas temperaturas), cera
- Precisão dimensional: ±0,1mm
- Aplicações comuns: Protótipos de produtos coloridos, protótipos semelhantes a moldes de injeção, moldes de injeção de baixo rendimento, modelos médicos, moda
- Vantagens: Textura de superfície lisa, colorida e vários materiais disponíveis
- Desvantagens: Materiais limitados, não adequados para peças mecânicas de precisão, mais caros do que outras tecnologias de resina usadas para fins visuais
1. Jateamento de Material (M-Jet)
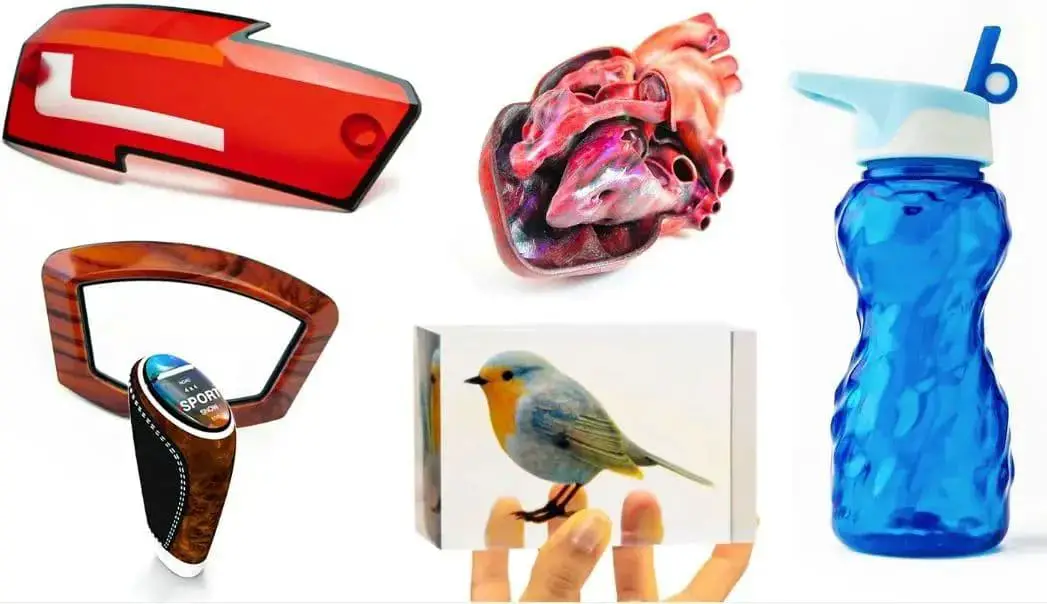
O Material Jetting (M-Jet) de polímeros é um processo de impressão 3D onde uma camada de resina fotossensível é depositada seletivamente em uma placa de construção e curada usando luz ultravioleta (UV).
Depois que uma camada é depositada e curada, a plataforma de construção abaixa uma espessura de camada e o processo é repetido para construir um objeto 3D. M-Jet combina a alta precisão da impressão 3D em resina com a velocidade da impressão 3D em filamento (FDM) para criar peças e protótipos com cores e texturas realistas.
Todas as tecnologias de impressão 3D de jato de material não são totalmente idênticas. Existem diferenças entre fabricantes de impressoras e materiais proprietários. As máquinas M-Jet depositam materiais de construção linha por linha a partir de múltiplas fileiras de cabeçotes de impressão.
Este método permite que a impressora fabrique vários objetos em uma linha sem afetar a velocidade de construção. Contanto que o modelo esteja corretamente organizado na plataforma de construção e o espaço dentro de cada linha de construção seja otimizado, a M-Jet pode produzir peças mais rapidamente do que muitos outros tipos de impressoras 3D de resina.
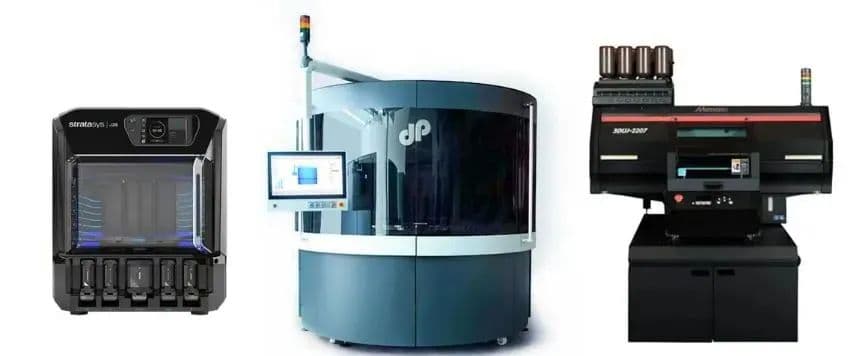
Os objetos fabricados com M-Jet necessitam de suporte, que é simultaneamente impresso com material solúvel durante o processo de construção e removido na fase de pós-processamento. M-Jet é uma das poucas tecnologias de impressão 3D que oferece objetos feitos a partir de impressão multimaterial e colorida.
As máquinas de jateamento de material não estão disponíveis em versões amadoras; essas máquinas são mais adequadas para profissionais da fabricação de automóveis, empresas de design industrial, estúdios de arte, hospitais e todos os tipos de fabricantes de produtos que desejam criar protótipos precisos para testar conceitos e trazer produtos ao mercado com mais rapidez.
Ao contrário da tecnologia de polimerização em cubas, o M-Jet não requer pós-cura, pois a luz UV na impressora cura completamente cada camada.
Jateamento de aerossol
A Optomec desenvolveu o Aerosol Jet, uma tecnologia exclusiva usada principalmente para impressão 3D de produtos eletrônicos. Resistores, capacitores, antenas, sensores e transistores de filme fino são todos impressos usando a tecnologia Aerosol Jet. Pode ser aproximadamente comparado à pintura em spray, mas difere dos processos de revestimento industrial porque pode ser usado para imprimir objetos 3D completos.
A tinta eletrônica é colocada em um atomizador, que produz gotas com diâmetros entre 1 e 5 mícrons. A névoa de aerossol é então entregue à cabeça de deposição, focada por um gás de bainha, criando uma pulverização de partículas em alta velocidade.
Como todo o processo utiliza energia, essa tecnologia às vezes também é chamada de Deposição de Energia Direcionada, mas como o material neste caso está na forma de gotículas, nós a incluímos no jateamento de material.
Moldagem de plástico de forma livre
A empresa alemã Arburg criou uma tecnologia chamada moldagem de plástico de forma livre (APF), uma combinação de tecnologias de extrusão e jateamento de material. Utiliza grânulos de plástico disponíveis comercialmente, que são derretidos no processo de moldagem por injeção e transportados para a unidade de descarga.
Movimento rápido de abertura e fechamento do bico de alta frequência, produzindo até 200 gotas de plástico por segundo com diâmetros entre 0,2 e 0,4 mm. As gotículas se ligam ao material em solidificação durante o resfriamento. O pós-processamento geralmente não é necessário. Caso tenha sido utilizado material de suporte, ele deverá ser removido.
2. Jateamento de nanopartículas (NPJ)
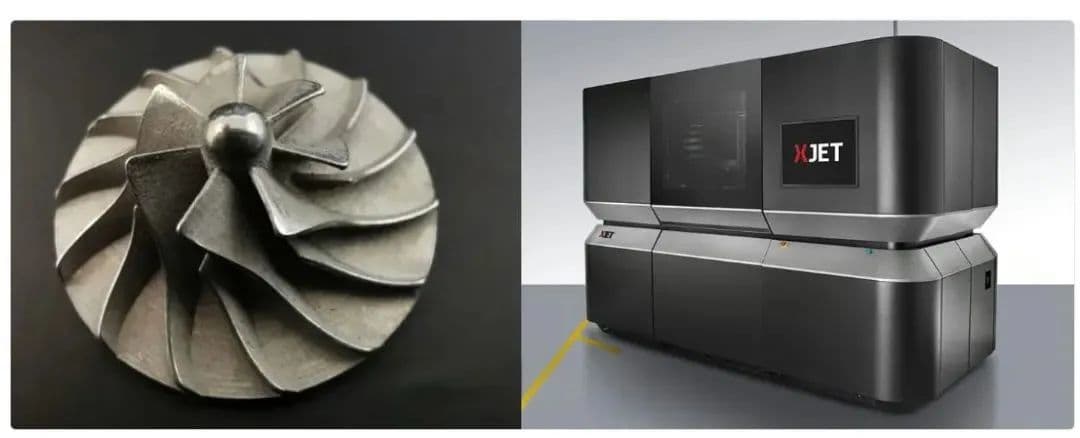
NanoParticle Jetting (NPJ) é uma das poucas tecnologias proprietárias difíceis de classificar, desenvolvida por uma empresa chamada XJet. Ele usa um conjunto de cabeçotes de impressão com milhares de bicos de jato de tinta que podem simultaneamente injetar milhões de gotículas de material ultrafino em uma camada superfina da bandeja de construção, ao mesmo tempo em que injeta material de suporte.
Partículas metálicas ou cerâmicas ficam suspensas no líquido. O processo acontece em altas temperaturas, onde o líquido evapora ao ser jateado, restando principalmente material metálico ou cerâmico. As peças 3D resultantes possuem apenas uma pequena quantidade de agente ligante, que é removido no pós-processamento da sinterização.
V. Jateamento de encadernação
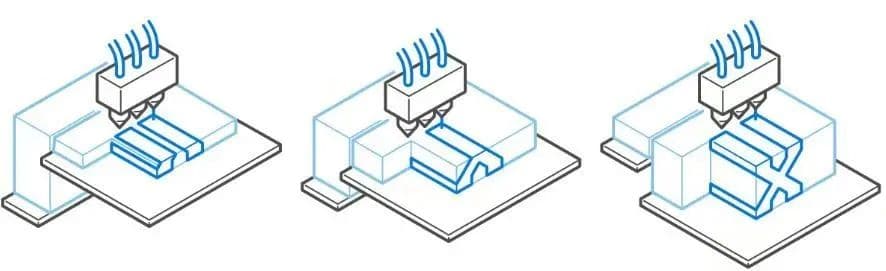
Binder jetting é um processo de impressão 3D que une seletivamente uma camada de pó em áreas específicas usando um adesivo líquido. Este tipo de tecnologia combina as características de fusão em leito de pó e jateamento de material.
Semelhante ao PBF, o jateamento de ligante utiliza material em pó (metais, plásticos, cerâmica, madeira, açúcar, etc.) e, assim como o jateamento de material, o polímero adesivo líquido é depositado a partir de um jato de tinta. O processo de jateamento de aglutinante permanece o mesmo, seja metal, plástico, areia ou outros materiais em pó.
Primeiramente, uma lâmina de revestimento espalha uma fina camada de pó na plataforma de construção. Em seguida, uma cabeça de impressão equipada com um bico de jato de tinta passa sobre a base, depositando seletivamente gotículas de adesivo para unir as partículas de pó. Assim que a camada estiver concluída, a plataforma de construção se move para baixo e a lâmina reveste novamente a superfície. Este processo é repetido até que toda a peça esteja finalizada.
A singularidade do jato de ligante reside na ausência de calor durante o processo de impressão. O adesivo atua como uma cola que mantém o pó do polímero unido. Após a impressão, a peça é envolta em pó não utilizado, que normalmente é deixado para solidificar. A peça é então retirada do depósito de pó, o excesso de pó é coletado e pode ser reaproveitado.
A partir daqui, o pós-processamento é necessário dependendo do material, exceto a areia, que geralmente pode ser utilizada diretamente da impressora como macho ou molde. Quando o pó é metálico ou cerâmico, o pós-processamento envolvido pelo calor derrete o adesivo, deixando apenas o metal. O pós-processamento de peças plásticas geralmente inclui revestimento para melhorar a suavidade da superfície. Polimento, pintura e lixamento também podem ser feitos em peças de jato de ligante de polímero.
O jateamento de ligante é rápido e tem uma alta taxa de produção, portanto, em comparação com outros métodos AM, pode produzir um grande número de peças com melhor custo-benefício. O jateamento de ligante de metal é aplicável a uma variedade de metais e é popular em bens de consumo de uso final, ferramentas e peças sobressalentes em lote.
No entanto, a seleção de materiais para jateamento de ligantes poliméricos é limitada e o desempenho estrutural das peças produzidas é inferior. Seu valor reside na capacidade de criar protótipos e modelos coloridos.
- Subtipos de tecnologia de impressão 3D: Jateamento de ligante de metal, jateamento de ligante de polímero, jateamento de ligante de areia
- Materiais: Areia, polímeros, metais, cerâmicas, etc.
- Precisão dimensional: ±0,2 mm (metal) ou ±0,3 mm (areia)
- Aplicações comuns: Peças metálicas funcionais, modelos coloridos, peças fundidas em areia e moldes
- Vantagens: Baixo custo, grande volume de construção, peças metálicas funcionais, excelente reprodução de cores, rápida velocidade de impressão, flexibilidade de design sem suportes
- Desvantagens: É um processo de várias etapas para metais, as peças de polímero não são duráveis
1. Jateamento de ligante de metal
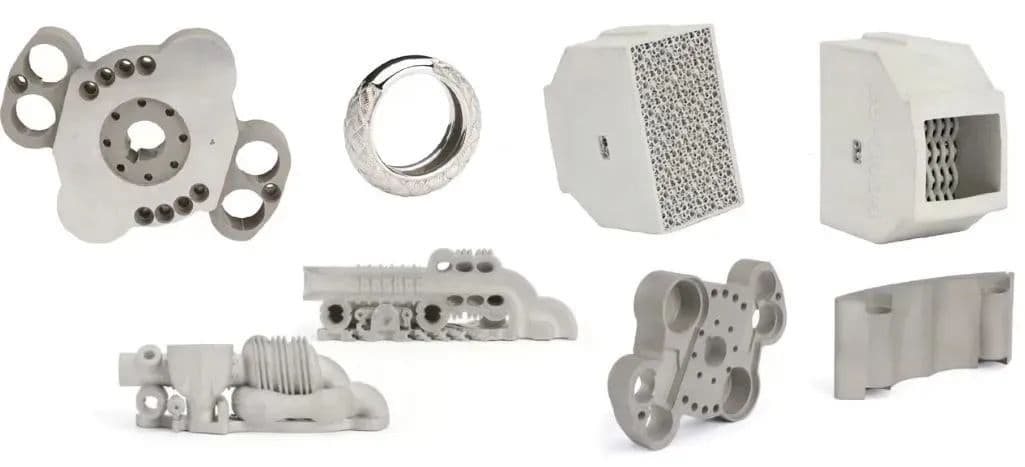
O Binder Jetting também pode ser usado para fabricar objetos de metal sólido com formas geométricas complexas, muito além da capacidade das tecnologias de fabricação tradicionais. O jateamento de ligante de metal é uma tecnologia muito atraente para a produção em massa de peças metálicas e para obter leveza.
Como o jato de ligante pode imprimir peças com preenchimentos de padrões complexos em vez de sólidos, as peças resultantes são significativamente mais leves, mas mantêm sua resistência. As características de porosidade do jato de ligante também podem ser usadas para criar peças finais mais leves para aplicações médicas, como implantes.
Em geral, o desempenho do material das peças jateadas com ligante metálico é comparável ao das peças metálicas produzidas com moldagem por injeção de metal, um dos métodos de fabricação mais amplamente utilizados na produção em massa de peças metálicas. Além disso, as peças jateadas com ligante apresentam maior suavidade superficial, especialmente em canais internos.
As peças jateadas com ligante de metal precisam de processamento secundário após a impressão para obter boas propriedades mecânicas. Recém-saídas da impressora, as peças consistem essencialmente em partículas metálicas unidas por um aglutinante de polímero.
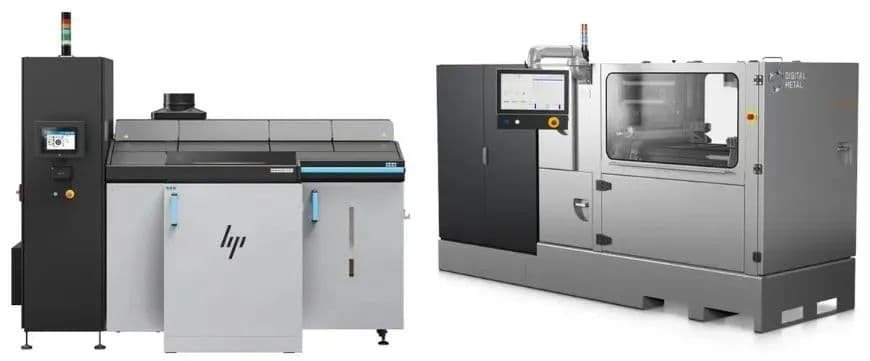
Estas chamadas “partes verdes” são demasiado frágeis para serem utilizadas tal como estão. Depois que as peças impressas são removidas do leito de pó metálico (processo denominado despulverização), elas passam por tratamento térmico (processo denominado sinterização) em um forno.
Tanto os parâmetros de impressão quanto os parâmetros de sinterização são ajustados para a geometria específica, material e densidade necessária da peça. Às vezes, bronze ou outros metais são usados para infiltrar os vazios nas peças jateadas com ligante, alcançando assim porosidade zero.
2. Jateamento de pasta de plástico
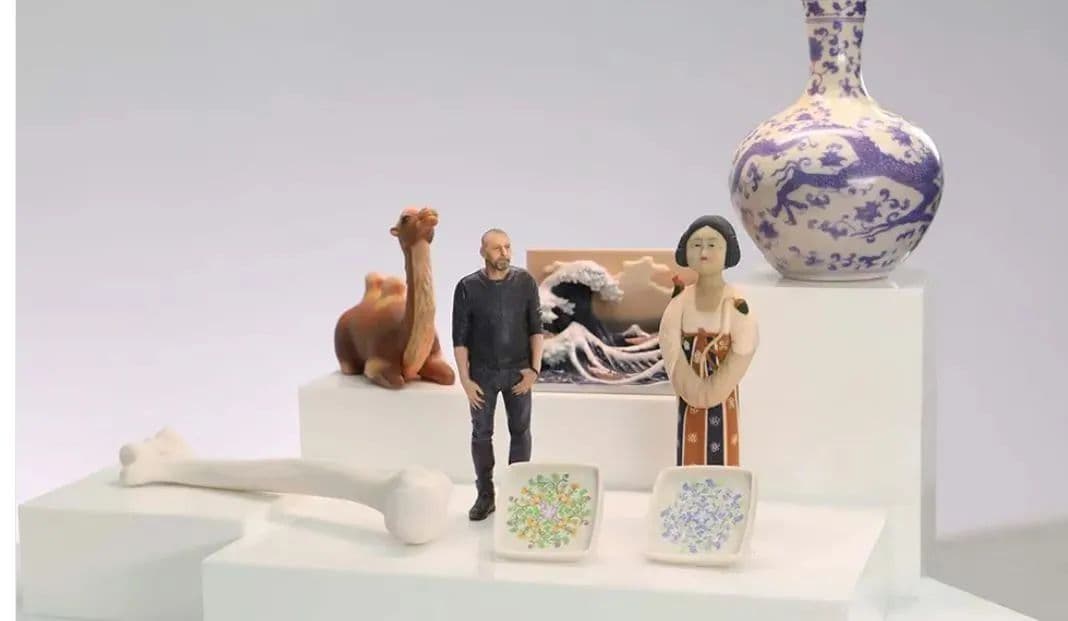
O jateamento de ligante plástico é um processo muito semelhante ao jateamento de ligante metálico, pois também utiliza ligante em pó e líquido, mas as aplicações são bem diferentes. Uma vez concluída a impressão, as peças plásticas são removidas do leito de pó e limpas, geralmente prontas para uso sem processamento adicional, mas essas peças não possuem a resistência e a durabilidade encontradas em outros processos de impressão 3D.
As peças jateadas com ligante de plástico podem ser infundidas com outro material para aumentar sua resistência. O jateamento de ligantes com polímeros é preferido por sua capacidade de produzir peças multicoloridas para modelagem médica e prototipagem de produtos.
3. Jateamento com adesivo de areia
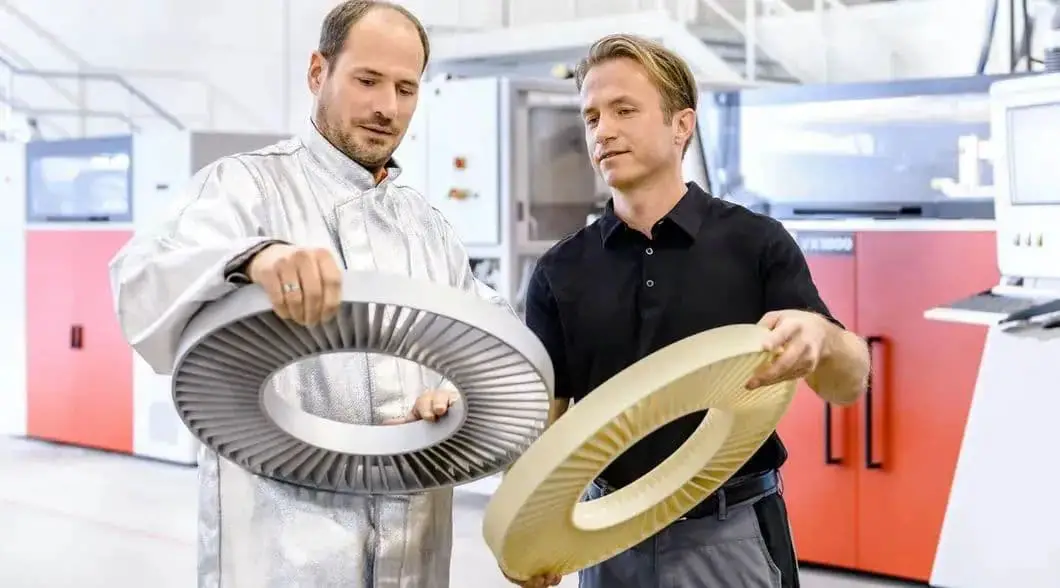
O jateamento com adesivo em areia difere do jateamento com adesivo em plástico em termos da máquina de impressão e do processo utilizado, daí a separação. Um dos usos mais comuns da tecnologia de jato de adesivo é a produção de grandes moldes, modelos e núcleos para fundição em areia. O baixo custo e a velocidade desse processo o tornam uma excelente solução para fundições, pois é um desafio produzir designs de padrões complexos em poucas horas usando tecnologias tradicionais.
O futuro do desenvolvimento industrial impõe constantemente altas exigências aos empreiteiros e fornecedores. A impressão 3D em areia está apenas começando a explorar seu potencial. Após a impressão, o operador precisa remover os machos e moldes da área de construção e limpá-los para remover qualquer areia solta. Os moldes geralmente podem ser preparados para fundição imediatamente. Após a fundição, o molde é aberto e a peça metálica final é removida.
4. Fusão Multijato (MJF)
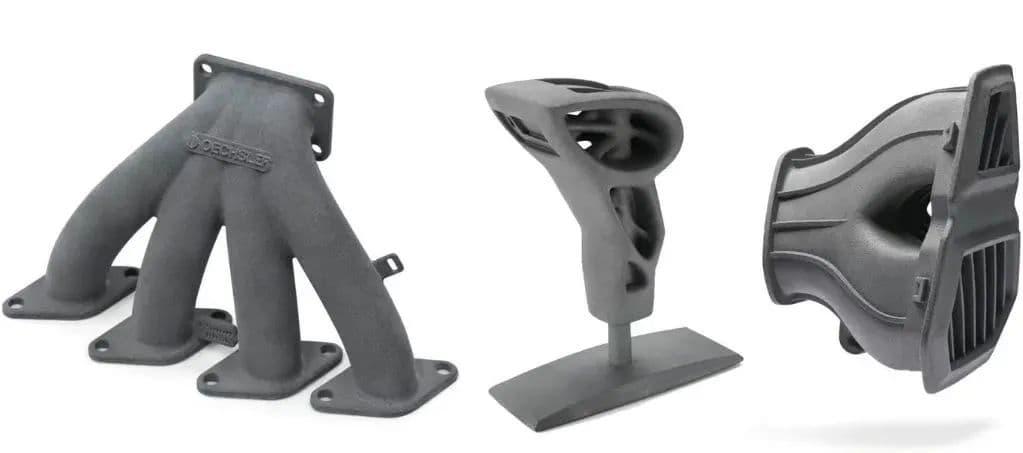
Outro processo de impressão 3D exclusivo e específico da marca que não se enquadra facilmente em nenhuma categoria existente e, na verdade, não é jato de adesivo, é o Multi Jet Fusion da HP. MJF é uma tecnologia de impressão 3D de polímero que utiliza material em pó, material de fusão líquida e um agente de detalhamento.
Não é considerado jateamento de adesivo porque nesse processo é adicionado calor, produzindo peças com maior resistência e durabilidade, e o líquido não é inteiramente um adesivo. O nome desse processo vem dos vários cabeçotes de jato de tinta usados no processo de impressão.
Durante o processo de impressão Multi Jet Fusion, a impressora coloca uma camada de material em pó, geralmente náilon, na base de impressão. Depois disso, as cabeças do jato de tinta passam sobre o pó e depositam nele o agente de fusão e o agente de detalhamento. Um dispositivo de aquecimento infravermelho se move sobre a impressão. Onde quer que o agente de fusão seja adicionado, as camadas subjacentes fundem-se, enquanto as áreas com o agente de detalhamento permanecem pulverulentas.
As partes pulverulentas caem, produzindo a forma geométrica desejada. Isso também elimina a necessidade de suporte de modelagem, pois as camadas inferiores sustentam as camadas impressas sobre elas. Para completar o processo de impressão, todo o leito de pó e as peças impressas dentro dele são movidos para uma estação de processamento separada, onde a maior parte do pó solto e não derretido é aspirado para reutilização.
Multi Jet Fusion é uma tecnologia versátil que tem sido aplicada em vários setores, incluindo automotivo, saúde e bens de consumo.
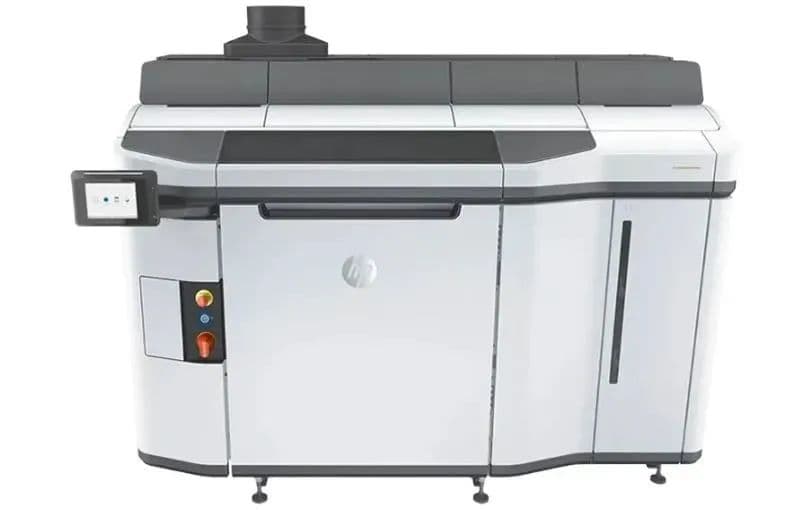
VI. Deposição de energia dirigida por pó
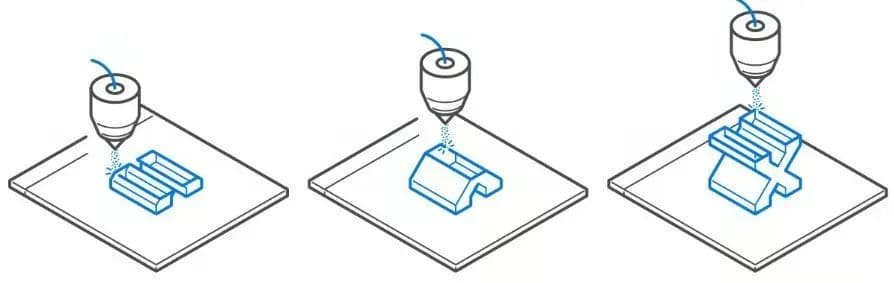
A Deposição de Energia Direcionada (DED) é um processo de impressão 3D onde o material metálico é fornecido e derretido simultaneamente com um poderoso fornecimento de energia. É uma das categorias mais amplas de impressão 3D, abrangendo muitas subcategorias, dependendo da forma do material (fio ou pó) e do tipo de energia (laser, feixe de elétrons, arco, supersônico, térmico, etc.). Essencialmente, tem muitas semelhanças com a soldagem.
Esta tecnologia é usada para impressão camada por camada, geralmente seguida de usinagem CNC para obter tolerâncias mais restritas. A combinação de DED e CNC é muito comum, existindo um subtipo de impressão 3D denominado Impressão 3D Híbrida, que inclui unidades DED e CNC na mesma máquina.
Esta tecnologia é considerada uma alternativa mais rápida e barata à fundição e forjamento de metais em pequenos lotes, e um reparo fundamental para aplicações na indústria offshore de petróleo e gás, bem como nos setores aeroespacial, de geração de energia e de serviços públicos.
- Subtipos de Deposição Dirigida de Energia: Deposição de energia a laser em pó, fabricação de aditivos de arco de fio (WAAM), deposição de energia por feixe de elétrons de fio, revestimento por pulverização a frio
- Materiais: Vários metais, em fio e em pó
- Precisão dimensional: ±0,1mm
- Aplicações comuns: Reparação de peças automotivas/aeroespaciais de alta qualidade, protótipos funcionais e peças finais
- Vantagens: Alta taxa de deposição, capacidade de adicionar metal aos componentes existentes
- Desvantagens: Não é possível produzir formas complexas devido à incapacidade de fazer estruturas de suporte, normalmente com pior acabamento superficial e precisão.
1. Deposição de energia dirigida a laser
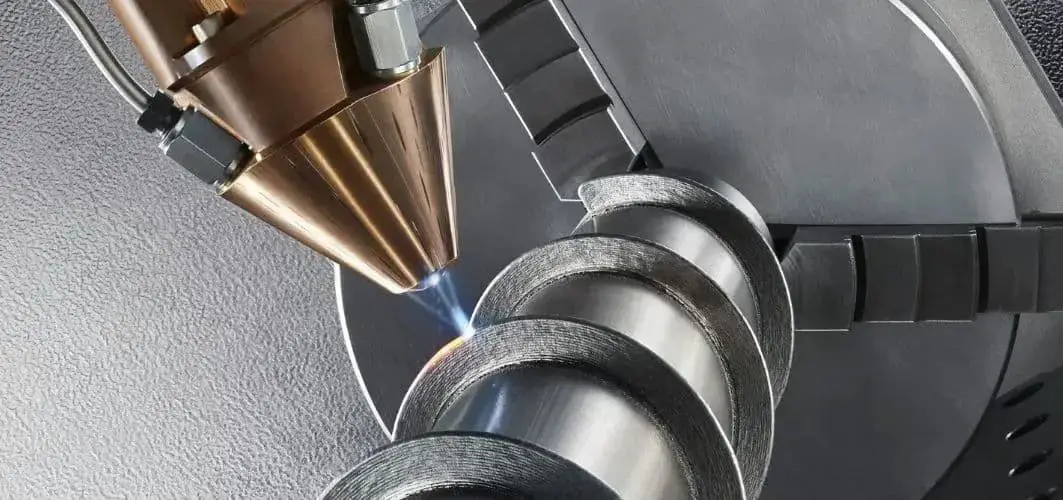
A Deposição de Energia Direcionada a Laser (L-DED), também conhecida como Deposição de Metal a Laser (LMD) ou Modelagem de Rede Projetada a Laser (LENS), usa pó de metal ou fio entregue através de um ou mais bicos e derretido em uma plataforma de construção ou peça de metal por um laser poderoso. À medida que o bico e o laser se movem, ou a peça se move em uma mesa giratória multieixos, o objeto é construído camada por camada.
A velocidade de construção é mais rápida do que a fusão em leito de pó, mas resulta na redução da qualidade da superfície e na precisão significativamente reduzida, normalmente exigindo um pós-processamento substancial. As impressoras laser DED geralmente têm uma câmara selada cheia de gás argônio para evitar oxidação. Ao manusear metais menos reativos, eles podem operar usando apenas gás argônio ou nitrogênio local.
Os metais comuns usados neste processo incluem aço inoxidável, titânio e ligas de níquel. Esse método de impressão é normalmente usado para reparar peças aeroespaciais e automotivas de alta qualidade, como pás de motores a jato, mas também é usado para produzir peças inteiras.
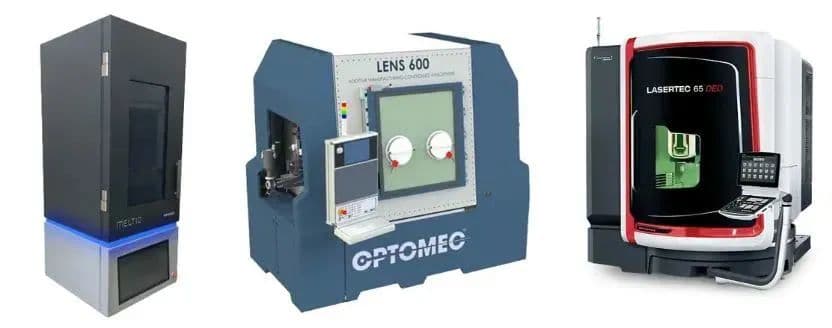
2. Deposição de energia dirigida por feixe de elétrons
Electron Beam DED, também conhecido como Wire Electron Beam Energy Deposition, é um processo de impressão 3D muito semelhante ao Laser DED. É conduzido em uma câmara de vácuo e pode produzir metais muito limpos e de alta qualidade. À medida que um fio metálico passa por um ou mais bicos, ele é derretido por um feixe de elétrons.
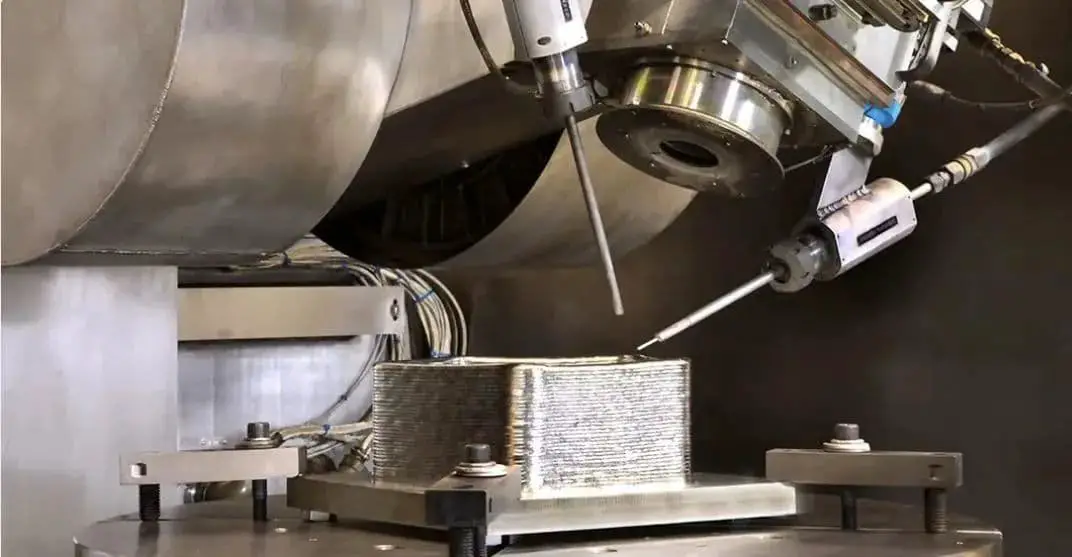
As camadas são construídas individualmente, com o feixe de elétrons formando uma pequena poça de fusão na qual o arame é alimentado por um alimentador de arame. Ao manusear metais ativos e de alto desempenho (como cobre, titânio, cobalto e ligas de níquel), o feixe de elétrons é escolhido para DED.
As máquinas DED são efetivamente ilimitadas em termos de tamanho de impressão. Por exemplo, o fabricante de impressoras 3D Sciaky possui uma máquina EB DED capaz de produzir peças de quase 6 metros de comprimento a uma taxa de 3 a 9 quilogramas de material por hora.
O Electron Beam DED é apontado como um dos métodos mais rápidos para a fabricação de peças metálicas, embora não seja o mais preciso, tornando-o uma tecnologia de usinagem ideal para a construção de grandes estruturas (como fuselagens) ou peças de reposição (como pás de turbinas).
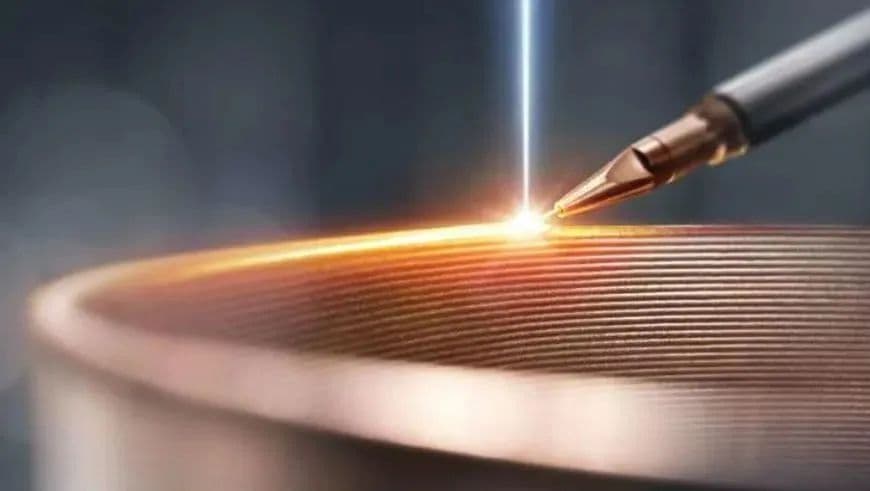
3. Deposição de energia dirigida por fio
A Deposição de Energia Direcionada por Fio, também conhecida como Fabricação Aditiva de Arco de Fio (WAAM), é uma forma de impressão 3D que usa energia na forma de plasma ou arco elétrico para derreter metal na forma de fio, que é então depositado camada por camada em um superfície, como uma plataforma giratória multieixo, por um braço robótico para formar uma forma.
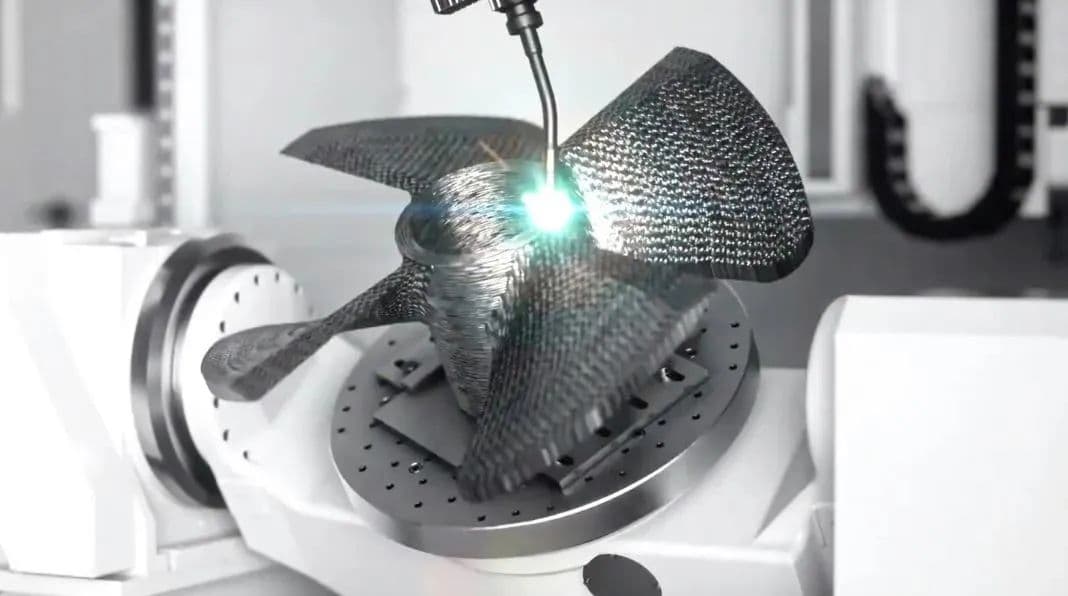
Este método é escolhido em detrimento de tecnologias semelhantes que utilizam lasers ou feixes de elétrons porque não requer uma câmara selada e pode usar metais idênticos aos usados na soldagem tradicional (às vezes até exatamente o mesmo material).
A Deposição Elétrica Direta de Energia é considerada a escolha mais econômica na tecnologia DED, pois pode usar robôs e fontes de energia de soldagem a arco existentes, tornando a barreira de entrada relativamente baixa.
Ao contrário da soldagem, no entanto, esta técnica utiliza software complexo para controlar uma variedade de variáveis durante o processo, incluindo gerenciamento de calor e caminhos da ferramenta do braço robótico. Esta técnica não possui estruturas de suporte a serem removidas, e as peças acabadas são comumente usinadas em CNC quando necessário para obter tolerâncias rígidas ou polimento superficial.
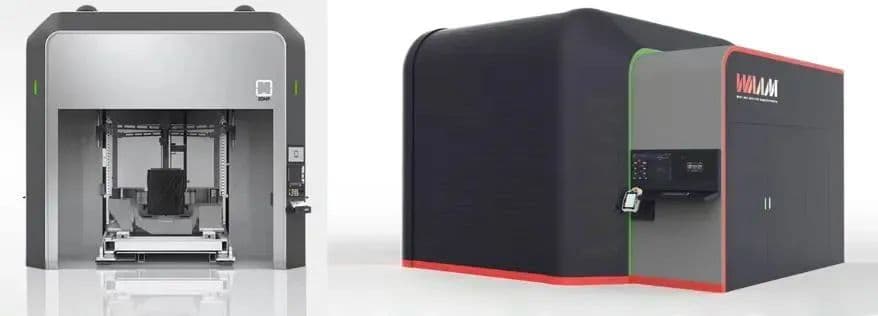
4. Revestimento em spray frio
Cold Spray Coating é uma tecnologia de impressão 3D DED que usa pulverização supersônica de pó metálico para uni-los sem derreter, praticamente eliminando rachaduras térmicas ou tensão.
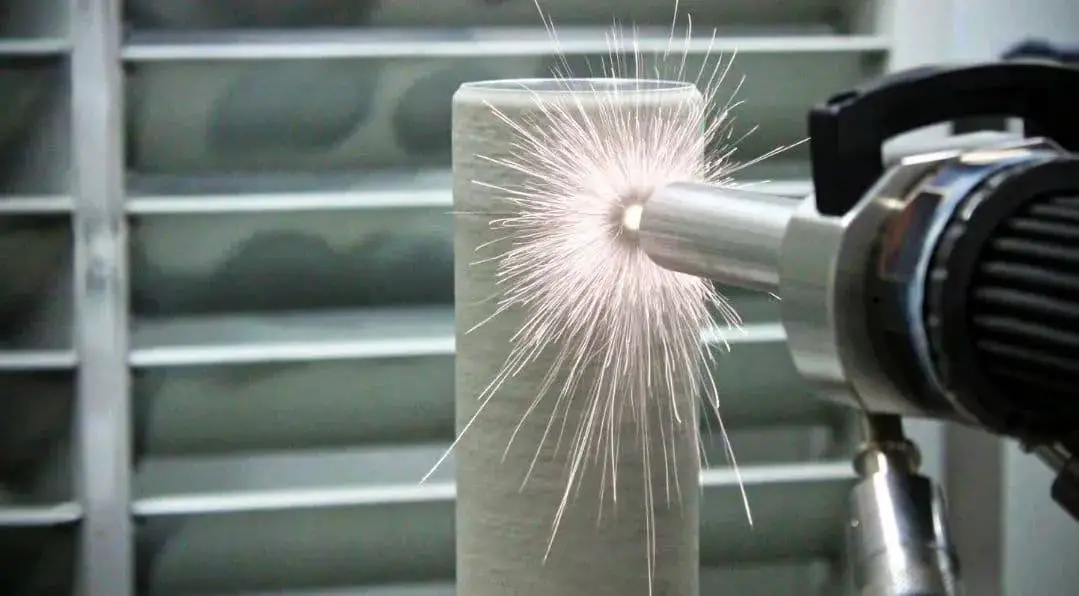
Desde o início dos anos 2000, tem sido usado como processo de revestimento, mas recentemente várias empresas começaram a usar revestimento por spray a frio para fabricação aditiva porque pode imprimir em velocidades 50 a 100 vezes mais rápidas do que os processos típicos de metal 3D e não requer gás inerte ou uma câmara de vácuo.
Como todos os processos DED, o Cold Spray Coating não produz impressões com boa qualidade de superfície ou detalhes, mas as peças podem ser usadas diretamente da mesa de impressão.
5. Deposição de energia dirigida por fusão
A deposição de energia dirigida por fusão é um processo de impressão 3D que usa calor para derreter metal (geralmente alumínio), que é então depositado camada por camada em uma placa de construção para formar um objeto 3D. A diferença entre esta tecnologia e a impressão 3D de extrusão de metal é que a extrusão utiliza matéria-prima metálica com uma pequena quantidade de polímero em seu interior, permitindo que o metal seja extrudado.
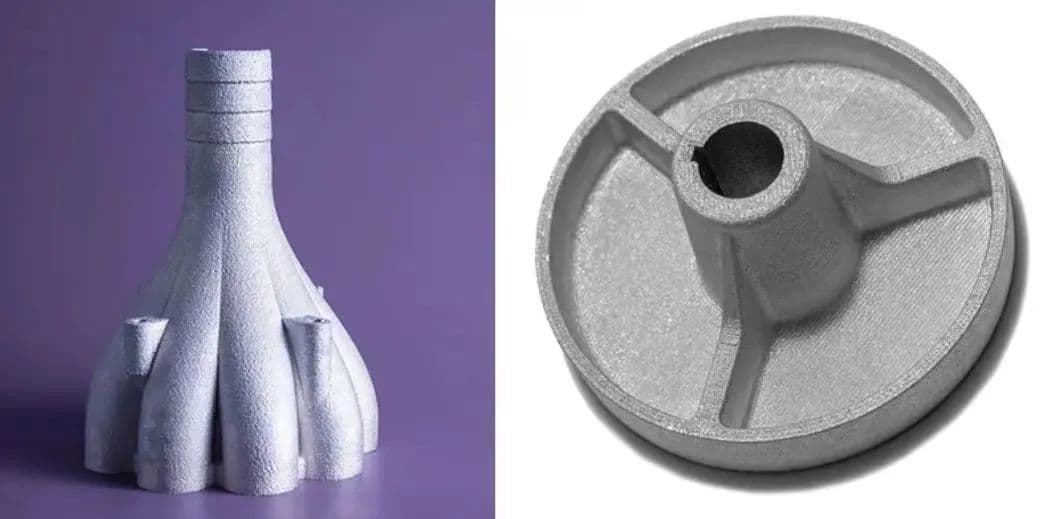
O polímero é então removido em uma etapa de tratamento térmico, enquanto o Melt DED utiliza metal puro. O DED fundido ou líquido também pode ser comparado ao jateamento de material, mas em vez de uma série de bicos depositando gotículas, o metal líquido normalmente flui para fora de um bico.
Variações dessa tecnologia estão sendo desenvolvidas e as impressoras 3D Melt Metal são raras. A vantagem de usar calor para derreter e depois depositar metal é que ele usa menos energia do que outros processos DED e pode potencialmente usar metal reciclado como matéria-prima, em vez de fio metálico ou pó metálico altamente processado.
VII. Laminação de Folhas
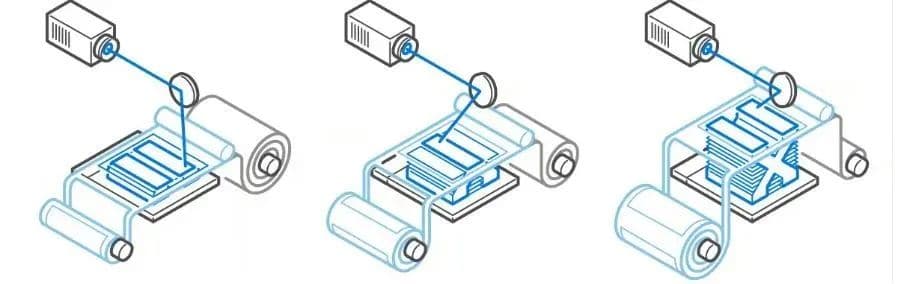
A laminação de folhas é tecnicamente uma forma de impressão 3D, mas difere significativamente das técnicas mencionadas acima. Sua função é empilhar e laminar folhas de materiais muito finos para produzir objetos ou pilhas 3D, que são então cortados mecanicamente ou a laser para formar a forma final.
As camadas de material podem ser fundidas usando vários métodos, incluindo calor e som, dependendo do material, com materiais que vão desde papel e polímeros até metais. Quando as peças são laminadas e depois cortadas a laser ou usinadas no formato desejado, são gerados mais resíduos do que com outras tecnologias de impressão 3D.
Os fabricantes utilizam laminação de folhas finas para produzir protótipos não funcionais a uma velocidade relativamente alta e com boa relação custo-benefício, adequado para a tecnologia de baterias e a produção de materiais compósitos, uma vez que os materiais utilizados podem ser trocados durante o processo de impressão.
- Tipos de tecnologia de impressão 3D: Fabricação de Objetos Laminados (LOM), Consolidação Ultrassônica (UC)
- Materiais: Papel, polímeros e chapas metálicas
- Precisão dimensional: ±0,1mm
- Aplicações comuns: Protótipos não funcionais, impressão multicolorida, moldes de fundição.
- Vantagens: Produção rápida, impressão composta
- Desvantagens: Baixa precisão, alto desperdício, algumas peças requerem pós-produção
Fabricação de Aditivos Laminados
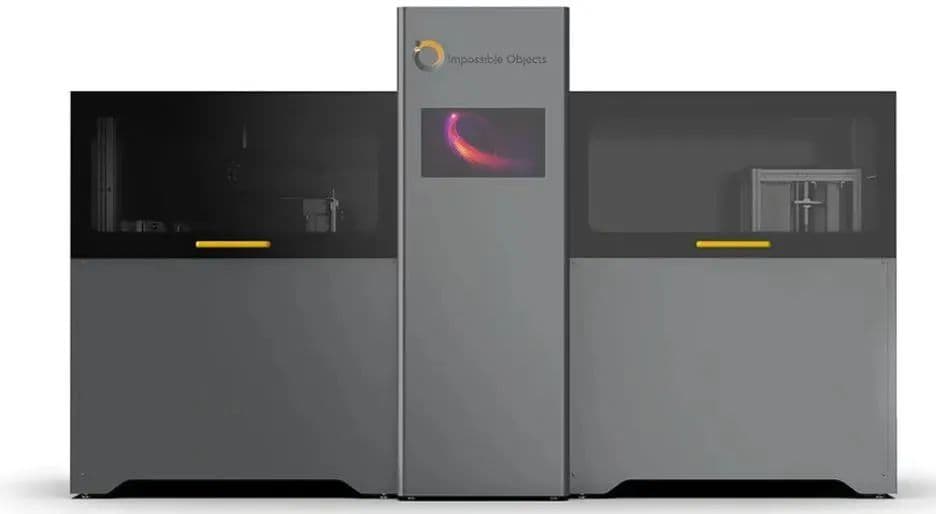
Laminação é uma forma de tecnologia de impressão 3D em que folhas de material são empilhadas e coladas e, em seguida, o objeto em camadas é cortado no formato correto usando uma faca (ou laser ou fresadora CNC). Esta tecnologia é menos comum hoje em dia, uma vez que o custo de outras tecnologias de impressão 3D diminuiu e a sua velocidade e facilidade de utilização aumentaram significativamente.
Fabricação de litografia viscosa (VLM): VLM é o processo de impressão 3D patenteado da BCN3D que lamina camadas finas de resina fotossensível de alta viscosidade em um filme de transferência transparente. O sistema mecânico permite que a resina seja laminada em ambos os lados do filme, possibilitando a combinação de diferentes resinas para obter peças multimateriais e estruturas de suporte facilmente removíveis. Esta tecnologia ainda não foi comercializada, mas pode ser considerada um tipo de tecnologia de impressão 3D laminada.
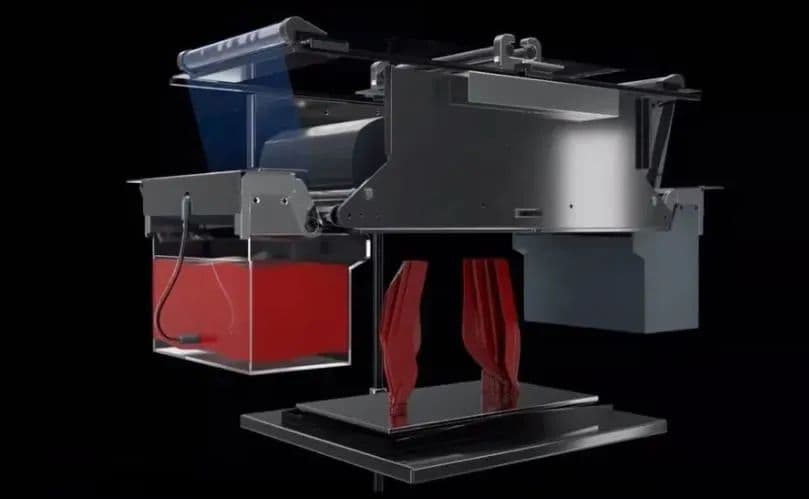
Fabricação Aditiva Baseada em Compostos (CBAM): A Start-up Impossible Objects patenteou esta tecnologia, que funde almofadas de carbono, vidro ou Kevlar com plástico termoplástico para fabricar peças.
Fabricação de material compósito de laminação seletiva (SLCOM): A EnvisionTEC, agora conhecida como ETEC e de propriedade da Desktop Metal, desenvolveu esta tecnologia em 2016, que utiliza plástico termoplástico como material base e material compósito de fibra tecida.
Nota: Existem muitos tipos de tecnologias de impressão 3D; os acima são os sete tipos mais comuns de tecnologias de fabricação aditiva na impressão 3D e não cobrem todas as tecnologias de impressão 3D no mercado.