Antes de selecionar um PLC, é importante determinar o esquema do sistema. Uma vez determinado o esquema do sistema, você pode escolher o fabricante e o modelo que melhor se adapta às suas necessidades.
Este artigo fornece informações detalhadas sobre fabricantes, modelos, contagem de pontos de entrada/saída (E/S), funções de controle e muito mais, para ajudá-lo a selecionar o PLC mais adequado para suas necessidades.
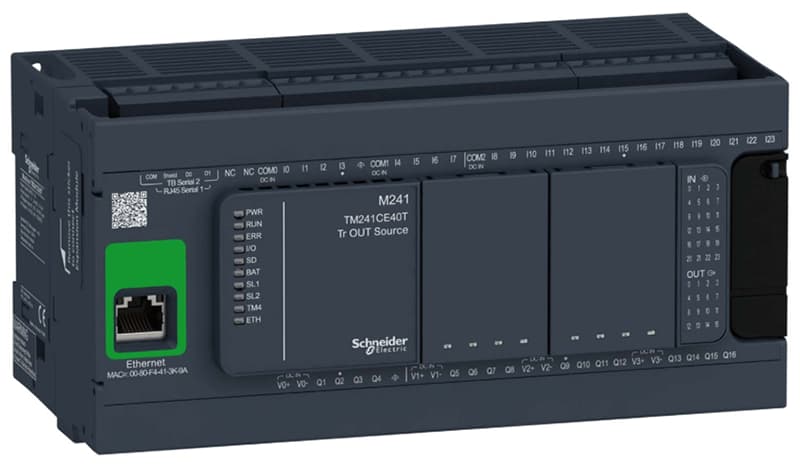
1. Fabricantes de CLPs
Ao selecionar um fabricante para o seu CLP, é importante considerar fatores como requisitos do usuário do equipamento, familiaridade do projetista com CLPs e hábitos de projeto de diferentes fabricantes, consistência de produtos compatíveis e serviços técnicos.
Do ponto de vista da confiabilidade do próprio PLC, em princípio, não deveria haver problemas com a confiabilidade dos produtos de grandes empresas estrangeiras. De modo geral, para controlar equipamentos independentes ou sistemas de controle mais simples, os produtos PLC japoneses têm certas vantagens de custo.
Para sistemas de controle distribuído em larga escala com altos requisitos de comunicação e abertura de rede, os CLPs europeus e americanos apresentam vantagens na funcionalidade de comunicação em rede.
Além disso, para algumas indústrias especiais (como metalurgia e tabaco), devem ser seleccionados sistemas PLC com desempenho operacional maduro e fiável no campo industrial relevante.
2. Contagem de pontos de entrada/saída (E/S)
A contagem de pontos de E/S de um CLP é um de seus parâmetros básicos. A determinação da contagem de pontos de E/S deve ser baseada no número total de pontos de E/S necessários para o equipamento de controle.
Em geral, os PLCs devem ter margens apropriadas para pontos de E/S. Normalmente, depois de adicionar 10% a 20% de margens expansíveis com base nas estatísticas calculadas de pontos de entrada/saída, esses dados podem então ser usados como uma contagem estimada de pontos de entrada/saída.
Ao fazer pedidos reais, a contagem de pontos de entrada/saída precisa ser ajustada com base nas características específicas do produto PLC do fabricante.
3. Capacidade de armazenamento
A capacidade de armazenamento refere-se ao tamanho da unidade de armazenamento de hardware que o controlador lógico programável pode fornecer, enquanto a capacidade do programa refere-se ao tamanho da unidade de armazenamento usada pelo projeto de aplicação do usuário na memória.
Portanto, a capacidade do programa é menor que a capacidade de armazenamento. Durante a fase de design, como o programa aplicativo do usuário ainda não foi compilado, a capacidade do programa é desconhecida e só pode ser determinada após a depuração do programa.
Para estimar a capacidade do programa durante o processo de seleção do projeto, a capacidade de armazenamento estimada é normalmente usada como um substituto. Não existe uma fórmula fixa para estimar a capacidade de memória do CLP e muitas fontes da literatura fornecem fórmulas diferentes.
Geralmente, o número total de palavras na memória é estimado em 10-15 vezes a contagem de pontos de E/S digital mais 100 vezes a contagem de pontos de E/S analógica (cada palavra tem 16 bits), e uma margem adicional de 25% também deve ser considerado.
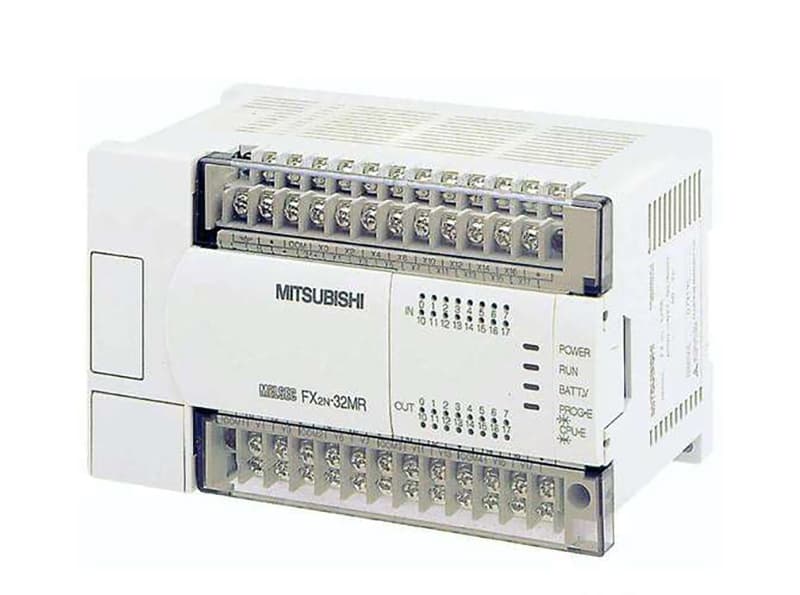
4. Função de controle
Esta seleção inclui a escolha de recursos operacionais, de controle, comunicação, programação, diagnóstico e velocidade de processamento.
1. Função Operacional
As funções operacionais de um PLC simples incluem operações lógicas, temporização e funções de contagem. As funções operacionais de um PLC normal também incluem mudança de dados, comparação e outras funções operacionais.
Funções operacionais mais complexas incluem operações algébricas, transferência de dados, etc. CLPs grandes também possuem funções operacionais avançadas, como operação PID para sinais analógicos.
Com o surgimento de sistemas abertos, a maioria dos PLCs agora possui funções de comunicação, alguns produtos possuem comunicação com máquinas de nível inferior, alguns possuem comunicação com computadores pares ou superiores e alguns até possuem funções de comunicação de dados com fábricas ou redes empresariais.
Ao selecionar o PLC com base nos requisitos reais, é importante selecionar razoavelmente as funções operacionais necessárias.
Na maioria dos cenários de aplicação, apenas operações lógicas e funções de tempo/contagem são necessárias.
Algumas aplicações requerem transferência e comparação de dados, e operações algébricas, conversão numérica e operações PID são usadas apenas para detecção e controle de sinais analógicos. Alguns aplicativos também exigem operações de decodificação e codificação para exibir dados.
2. Função de controle
As funções de controle incluem operações de controle PID, operações de controle de compensação feed-forward, operações de controle de relação, etc., que devem ser determinadas com base nos requisitos de controle. Como o PLC é usado principalmente para controle lógico sequencial, controladores de loop único ou multiloop são frequentemente usados para resolver o controle analógico na maioria dos cenários.
Às vezes, unidades de entrada/saída inteligentes dedicadas são usadas para completar as funções de controle necessárias, melhorando a velocidade de processamento do PLC e economizando capacidade de armazenamento. Por exemplo, utilizando unidades de controle PID, contadores de alta velocidade, unidades analógicas com compensação de velocidade, unidades de conversão ASCII, etc.
3. Função de comunicação
Os sistemas PLC de médio a grande porte devem suportar vários barramentos de campo e protocolos de comunicação padrão (como TCP/IP) e devem ser capazes de se conectar a redes de gerenciamento de fábrica (TCP/IP) quando necessário.
O protocolo de comunicação deve estar em conformidade com os padrões de comunicação ISO/IEEE e deve ser uma rede de comunicação aberta.
A interface de comunicação do sistema PLC deve incluir interfaces de comunicação serial e paralela (RS2232C/422A/423/485), portas de comunicação RIO, Ethernet industrial, interfaces DCS comumente usadas, etc.
O barramento de comunicação de CLPs de médio a grande porte (incluindo dispositivos de interface e cabos) deve considerar configuração redundante, e o barramento de comunicação deve estar em conformidade com os padrões internacionais. A distância de comunicação deve atender aos requisitos reais do dispositivo.
Na rede de comunicação do sistema PLC, a taxa de comunicação da rede de nível superior deve ser superior a 1Mbps e a carga de comunicação não deve exceder 60%.
A rede de comunicação do sistema PLC possui diversas formas:
- O PC é a estação principal e vários CLPs do mesmo modelo são as subestações, formando uma rede simples de CLPs;
- Um CLP é a estação principal e os demais CLPs do mesmo modelo são subestações, formando uma rede CLP mestre-escravo;
- A rede PLC está conectada a um DCS de grande escala através de uma interface de rede específica como uma sub-rede do DCS;
- Uma rede PLC dedicada (rede de comunicação PLC dedicada de vários fabricantes).
Para reduzir a tarefa de comunicação da CPU, diferentes processadores de comunicação com diferentes funções de comunicação (como ponto a ponto, fieldbus, Ethernet industrial) devem ser selecionados com base nas necessidades reais da composição da rede.
4. Função de programação
Programação off-line:
O PLC e o programador compartilham uma CPU. No modo de programação, a CPU atende apenas o programador e não controla o dispositivo de campo. Após a conclusão da programação, o programador muda para o modo de execução e a CPU controla o dispositivo de campo, mas não pode realizar a programação.
A programação offline reduz os custos do sistema, mas é inconveniente de usar e depurar.
Programação on-line:
A CPU e o programador possuem suas próprias CPUs. A CPU principal é responsável pelo controle de campo e troca dados com o programador em um ciclo de varredura. O programador envia o programa ou dados programados on-line para o host, e o host é executado de acordo com o novo programa recebido no próximo ciclo de digitalização.
Este método tem um custo mais elevado, mas a depuração e operação do sistema são convenientes e são comumente usadas em PLCs de médio a grande porte.
Cinco linguagens de programação padronizadas:
Gráfico de Funções Sequenciais (SFC), Diagrama Ladder (LD), Diagrama de Blocos de Funções (FBD), três linguagens gráficas, e Lista de Instruções (IL) e Texto Estruturado (ST), duas linguagens de texto.
A linguagem de programação selecionada deve estar em conformidade com seu padrão (IEC6113123) e suportar múltiplas formas de programação de linguagem, como C, Basic, Pascal, etc., para atender aos requisitos de controle de cenários de controle especiais.
5. Função de diagnóstico
A função de diagnóstico do PLC inclui diagnósticos de hardware e software. Os diagnósticos de hardware determinam a localização das falhas de hardware através de julgamentos lógicos de hardware, enquanto os diagnósticos de software incluem diagnósticos internos e externos.
Diagnosticar o desempenho e as funções do PLC internamente por meio de software é um diagnóstico interno, enquanto diagnosticar a CPU e a função de troca de informações de componentes externos de entrada/saída por meio de software é um diagnóstico externo.
A força da função de diagnóstico do PLC afeta diretamente as capacidades técnicas exigidas dos operadores e do pessoal de manutenção e afeta o tempo médio de reparo.
6. Velocidade de processamento
O PLC funciona em modo de varredura. Do ponto de vista dos requisitos em tempo real, a velocidade de processamento deve ser a mais rápida possível. Se a duração do sinal for menor que o tempo de varredura, o PLC não será capaz de varrer o sinal, resultando na perda dos dados do sinal.
A velocidade de processamento está relacionada à duração do programa do usuário, velocidade de processamento da CPU, qualidade do software, etc.
Atualmente, o tempo de resposta e a velocidade dos contatos do PLC são rápidos e o tempo de execução de cada instrução binária é de cerca de 0,2 ~ 0,4 μs, o que pode atender aos requisitos de aplicações de alto controle e resposta rápida.
O ciclo de varredura (ciclo de varredura do processador) deve atender aos seguintes critérios: o tempo de varredura do PLC pequeno não deve exceder 0,5 ms/K, e o tempo de varredura do PLC de médio a grande escala não deve exceder 0,2 ms/K.
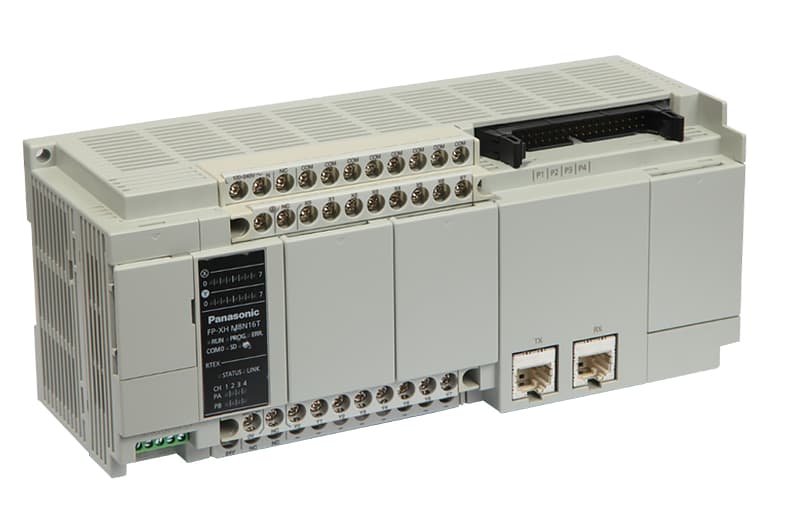
7. Modelos CLP
Os CLPs podem ser classificados em dois tipos: integrais e modulares, com base em suas estruturas.
Os CLPs integrais possuem um número relativamente fixo e pequeno de pontos de E/S, o que limita as escolhas dos usuários e é normalmente usado em pequenos sistemas de controle. Exemplos deste tipo incluem a série Siemens S7-200, a série Mitsubishi FX e a série Omron CPM1A.
Os CLPs modulares fornecem vários módulos de E/S que podem ser conectados à placa de base do CLP, permitindo que os usuários selecionem e configurem o número de pontos de E/S de acordo com suas necessidades.
Isso torna as configurações modulares do PLC mais flexíveis e é comumente usado em sistemas de controle de médio a grande porte. Exemplos deste tipo incluem as séries Siemens S7-300 e S7-400, série Mitsubishi Q e série Omron CVM1.
8. Seleção de vários módulos
1. Módulo de E/S digital
A seleção de módulos de entrada/saída digital deve considerar os requisitos da aplicação. Por exemplo, para módulos de entrada, as considerações devem incluir níveis de sinal de entrada, distâncias de transmissão, etc.
Existem também muitos tipos de módulos de saída, como saída de contato de relé, saída de tiristor bidirecional AC120V / 23V, tipo de unidade de transistor DC24V, tipo de unidade de transistor DC48V, etc.
Normalmente, os módulos de saída a relé têm as vantagens de baixo custo e ampla faixa de tensão. No entanto, eles têm vida útil mais curta, tempo de resposta mais longo e requerem circuitos de absorção de surtos quando usados com cargas indutivas.
Os módulos de saída tiristores bidirecionais têm um tempo de resposta mais rápido e são adequados para comutação frequente e ocasiões de carga de baixo fator de potência, mas são mais caros e têm menor capacidade de sobrecarga.
Além disso, os módulos de entrada/saída podem ser divididos em especificações como 8 pontos, 16 pontos, 32 pontos, etc., de acordo com o número de entradas/saídas, e devem ser razoavelmente equipados de acordo com as necessidades reais.
2. Módulo de E/S analógica
Os módulos de entrada analógica podem ser divididos em tipo de entrada de corrente, tipo de entrada de tensão, tipo de entrada de termopar, etc., de acordo com o tipo de sinal de entrada analógica.
O nível de sinal de um módulo de entrada de corrente é geralmente 4 ~ 20 mA ou 0 ~ 20 mA, enquanto o de um módulo de entrada de tensão é geralmente 0 ~ 10 V, -5 V ~ + 5 V, etc. sinais de entrada atuais.
Os módulos de saída analógica também possuem tipo de saída de tensão e tipo de saída de corrente. A faixa do sinal de saída de corrente é geralmente 0 ~ 20 mA, 4 ~ 20 mA, enquanto a dos sinais de saída de tensão é geralmente 0 ~ 0 V, -10 V ~ + 10 V, etc.
Os módulos de entrada/saída analógica podem ser divididos em especificações como 2 canais, 4 canais, 8 canais, etc., de acordo com seus números de canais de entrada/saída.
3. Módulos de Função
Os módulos de função incluem módulos de comunicação, módulos de posicionamento, módulos de saída de pulso, módulos de contagem de alta velocidade, módulos de controle PID, módulos de controle de temperatura, etc.
Na escolha de um CLP deve-se considerar a possibilidade de correspondência de módulos funcionais, o que envolve aspectos de hardware e software.
8. Regras Gerais
Depois que o modelo e as especificações do PLC forem determinados aproximadamente, as especificações básicas e os parâmetros de cada componente do PLC podem ser determinados um por um de acordo com os requisitos de controle, e os modelos de cada módulo componente podem ser selecionados.
Ao selecionar modelos de módulos, os seguintes princípios devem ser seguidos:
1. Economia
Ao selecionar um PLC, a relação desempenho-preço deve ser considerada. Ao considerar a economia, fatores como escalabilidade da aplicação, operabilidade, relação entrada-saída, etc. devem ser comparados e equilibrados para escolher um produto satisfatório.
O número de pontos de entrada/saída tem impacto direto no preço. Aumentar o número de cartões de entrada/saída requer custos adicionais. Quando o número de pontos aumenta para um determinado valor, a capacidade de memória, rack, placa-mãe, etc. correspondente também deve ser aumentada.
Portanto, aumentar o número de pontos tem impacto na seleção da CPU, na capacidade de memória e no escopo da função de controle. Deve ser totalmente considerado na estimativa e seleção para fazer com que todo o sistema de controle tenha uma relação desempenho-preço mais razoável.
2. Conveniência
Geralmente, existem muitos tipos de módulos que podem atender aos requisitos de controle de um PLC. Ao selecionar, deve-se seguir o princípio de simplificação do projeto do circuito, conveniência de uso e minimização de componentes de controle externo.
Por exemplo, para módulos de entrada, a forma de entrada que pode ser conectada diretamente a elementos de detecção externos deve ser priorizada para evitar o uso de circuitos de interface.
Para módulos de saída, os módulos de saída que podem acionar cargas diretamente devem ser priorizados e os relés intermediários e outros componentes devem ser minimizados.
3. Generalidade
Ao selecionar, a uniformidade e generalidade de cada módulo componente do PLC deve ser considerada para evitar muitos tipos de módulos.
Isto não só favorece a aquisição, reduzindo peças sobressalentes, mas também pode aumentar a intercambialidade de vários componentes do sistema, proporcionando conveniência para projeto, comissionamento e manutenção.
4. Compatibilidade
Ao selecionar cada módulo componente do sistema PLC, a compatibilidade deve ser totalmente considerada para evitar problemas de compatibilidade deficiente.
Os fabricantes de produção dos principais componentes do sistema PLC não devem ser muitos. Se possível, devem ser selecionados produtos do mesmo fabricante.