1. Breve introdução aos modos de corrosão do aço inoxidável
Em uma ampla gama de aplicações industriais, o aço inoxidável oferece resistência à corrosão satisfatória.
Com base na experiência, a corrosão do aço inoxidável, além de falhas mecânicas, manifesta-se principalmente como corrosão localizada, que inclui corrosão sob tensão (SCC), corrosão por pite, corrosão intergranular, fadiga por corrosão e corrosão em frestas.
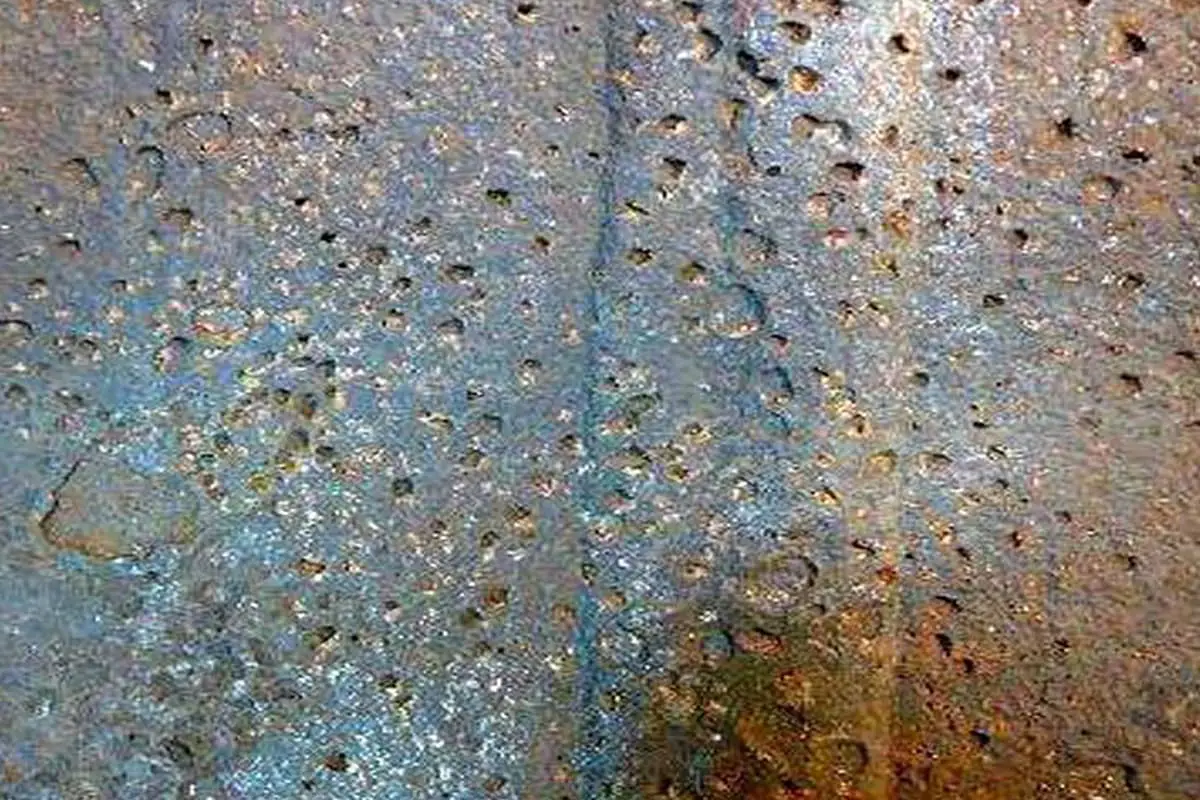
1.1 Fissuração por Corrosão sob Tensão (SCC)
A corrosão sob tensão é um tipo de falha que ocorre em ligas sob tensão em ambientes corrosivos devido à propagação de trincas. O CAA apresenta características de superfície de fratura frágil, mas também pode ocorrer em materiais com alta tenacidade.
As condições necessárias para a ocorrência do SCC incluem tensão de tração (seja tensão residual, tensão aplicada ou ambas) e a presença de um meio corrosivo específico. A formação e propagação de fissuras geralmente ocorrem perpendicularmente à direção da tensão de tração.
O nível de tensão que causa a SCC é significativamente menor que o nível de tensão necessário para fraturar o material na ausência de um meio corrosivo.
Em escala microscópica, as trincas que passam através dos grãos são denominadas trincas transgranulares, enquanto aquelas que se propagam ao longo dos limites dos grãos são chamadas de trincas intergranulares.
Quando o CAA progride até uma certa profundidade (onde a tensão na seção transversal do material carregado atinge sua tensão de fratura no ar), o material quebra normalmente (em materiais tenazes, geralmente através da agregação de defeitos microscópicos).
Portanto, a superfície de fratura de um componente que falha devido ao SCC conterá áreas características do SCC, bem como áreas de “ondulações dúcteis” associadas à agregação de defeitos microscópicos.
As condições primárias para a corrosão sob tensão normalmente envolvem um meio corrosivo fraco, uma certa tensão de tração e um sistema corrosivo específico composto de certos materiais metálicos. Este tópico será discutido em detalhes abaixo.
a. A fissuração por corrosão sob tensão pode ocorrer apenas quando a corrosão fraca forma uma película protetora instável na superfície do metal.
Resultados experimentais indicam que uma diminuição no valor do pH reduz a suscetibilidade do aço inoxidável austenítico à corrosão sob tensão.
O aço estrutural geral, em meios neutros e de pH alto, sofrerá fissuração por corrosão sob tensão através de diferentes mecanismos.
b. A corrosão tende a ocorrer sob certas condições de tensão de tração.
Para a corrosão sob tensão do aço inoxidável Cr-Ni, a relação entre a tensão (σ) e o tempo de fissuração (ts) é geralmente considerada como seguindo a equação 1gts=a+bσ, onde a e b são constantes.
Isto sugere que quanto maior a tensão, menor o tempo antes que o aço inoxidável sofra fissuras por corrosão sob tensão.
Estudos sobre corrosão sob tensão em aços inoxidáveis mostram que existe um valor de tensão crítico para a ocorrência de corrosão sob tensão, comumente representado por σSCC.
Se a tensão estiver abaixo deste valor, a fissuração por corrosão sob tensão não ocorrerá. O valor σSCC varia com o tipo de meio, concentração, temperatura e diferentes composições do material. O ambiente que causa a falha na trinca por corrosão sob tensão é bastante complexo.
As tensões envolvidas não são apenas tensões operacionais, mas uma combinação dessas tensões e das tensões residuais geradas no metal devido à fabricação, soldagem ou tratamento térmico.
c. Os sistemas de meio metálico são propensos à destruição por corrosão sob tensão.
Os meios que mais comumente causam corrosão sob tensão são cloretos, soluções alcalinas e sulfeto de hidrogênio.
Os resultados da pesquisa sobre o efeito dos íons metálicos em vários cloretos levaram à corrosão sob tensão no aço inoxidável Cr + Ni. O efeito dos diferentes cloretos diminui na ordem dos íons Mg2+, Fe3+, Ca2+, Na+, Li+.
d. A influência dos materiais, estrutura e condições de tensão.
Os elementos de impureza afetam muito a sensibilidade à corrosão sob tensão. No aço inoxidável, um teor de nitrogênio superior a 30×10^-6 pode aumentar significativamente a sensibilidade à fragilidade por cloreto.
A sensibilidade do aço à corrosão sob tensão varia com o teor de carbono.
Quando o teor de carbono é baixo, a sensibilidade do aço aumenta à medida que o teor de carbono aumenta. Quando ω(C) é maior que 0,2%, a resistência à corrosão sob tensão tende a se estabilizar. Quando ω(C) é 0,12%, a sensibilidade à corrosão sob tensão é maior.
O estado estrutural do material afeta significativamente a sensibilidade à corrosão sob tensão. Quanto maior a heterogeneidade do material, mais fácil é gerar canais catódicos ativos e causar corrosão sob tensão. À medida que o tamanho do grão aumenta, a sensibilidade do aço à corrosão sob tensão aumenta.
Quanto maior a concentração do meio e a temperatura ambiente, mais fácil será a ocorrência de fissuras por corrosão sob tensão. A corrosão sob tensão causada por cloretos geralmente ocorre acima de 60 ℃ e a sensibilidade aumenta acentuadamente com a temperatura.
A corrosão sob tensão causada por soluções alcalinas geralmente ocorre a 130°C ou temperaturas mais altas. A corrosão sob tensão em solução de sulfeto de hidrogênio ocorre principalmente em baixas temperaturas.
O efeito da resistência e dureza do material na sensibilidade à corrosão sob tensão depende do estado real do componente. Sob as mesmas condições de controle de deformação (deformação), quanto maior a resistência e a dureza do material, maior será a tensão de seu componente e maior será a sensibilidade à fissuração por corrosão sob tensão.
Sob o mesmo controle de tensão, à medida que a resistência e a dureza do material aumentam, a sensibilidade do componente à fissuração por corrosão sob tensão diminui.
Geralmente, quando a carga externa (tensão causada por deformação ou carga externa) atinge mais de 85% da resistência ao escoamento do material, a probabilidade de o componente sofrer fissuração por corrosão sob tensão aumenta significativamente.
O método mais eficaz para prevenir fissuras por corrosão sob tensão é selecionar materiais que sejam resistentes a tais fissuras em um determinado ambiente.
1.2 Corrosão por picada
A corrosão por pites, também conhecida como corrosão por cavidade, é uma forma de corrosão eletroquímica e é um tipo comum de corrosão localizada em aço inoxidável.
Conforme mencionado anteriormente, a excelente resistência à corrosão do aço inoxidável se deve a uma película oxidada invisível que o torna passivo. Se esta película passiva for destruída, o aço inoxidável sofrerá corrosão. A aparência característica da corrosão por pites são pontos de corrosão localizados na superfície.
A remoção da camada superficial da fossa revela graves crateras de corrosão, às vezes cobertas por uma camada de produtos de corrosão. Uma vez removidos, os graves poços de corrosão são revelados. Além disso, sob condições ambientais específicas, os poços de corrosão podem apresentar uma morfologia especial semelhante à de um pagode.
Os fatores que contribuem para a corrosão por pites incluem:
a) O meio ambiental que causa a corrosão por pite é a presença de íons metálicos centrais, como Fe3+, Cu2+, Hg2+ em soluções de Cl-, Br-, I- e ClO-4, ou íons de metais alcalinos e alcalinos Na+, Ca2+ em soluções contendo H2O2, O2.
A taxa de corrosão aumentará com o aumento da temperatura. O estado fluido da solução também afeta a ocorrência de corrosão por pites. Quando a taxa de fluxo atinge um certo nível, a corrosão por pites não ocorre.
b) A adição de Mo ao aço inoxidável pode produzir uma película passiva densa e robusta na superfície do aço inoxidável, levando a um aumento no potencial de corrosão por pites e aumentando a capacidade de resistir à corrosão por pites. À medida que o teor de Cr aumenta, a taxa de corrosão por pites do aço inoxidável diminui.
c) O processo de tratamento térmico do aço inoxidável afeta muito a corrosão por pites. O tratamento térmico em temperaturas comparáveis à precipitação de carboneto pode aumentar o número de eventos de corrosão por pite.
d) O processamento e a deformação também aumentarão a sensibilidade à corrosão por pites.
As seguintes medidas podem prevenir a corrosão por pites:
- Evite a concentração de íons haleto.
- Adicione uma quantidade adequada de molibdênio e aumente o teor de cromo no aço inoxidável austenítico. Adote um processo de tratamento térmico razoável.
- Garanta a uniformidade da solução oxidante. Aumente a concentração de oxigênio ou remova o oxigênio.
- Aumente o valor do pH da solução.
- Opere na temperatura mais baixa possível.
- Adicione passivadores ao meio corrosivo.
- Use proteção catódica para manter o potencial do material abaixo do potencial crítico de corrosão por pites.
1.3 Corrosão Intergranular
A corrosão intergranular do aço inoxidável é um tipo de corrosão que ocorre ao longo ou imediatamente adjacente aos limites dos grãos.
Esta corrosão é causada pela precipitação de carbonetos de cromo ao longo dos limites dos grãos sob certas condições de tratamento térmico, que forma zonas desprovidas de cromo perto dos limites dos grãos e preferencialmente se dissolve no meio corrosivo.
A corrosão que ocorre entre os grãos é uma forma grave de degradação, pois resulta na perda da resistência de ligação entre os grãos, eliminando quase completamente a resistência do material.
Após o metal ter sofrido corrosão intergranular, praticamente não há alterações na aparência – as dimensões geométricas e o brilho da superfície metálica permanecem inalterados – mas o comprimento e o alongamento diminuem significativamente.
Após exposição à flexão a frio, impacto mecânico ou choque intenso com fluidos, aparecem rachaduras na superfície do metal, que podem até se tornar quebradiças. Com uma leve força, os grãos caem sozinhos, perdendo o som metálico.
O exame metalográfico revela corrosão uniforme ao longo dos limites dos grãos e, em alguns casos, pode ser observado deslocamento dos grãos. Quando examinada com um microscópio eletrônico de varredura, a superfície da fratura exibe uma morfologia semelhante a açúcar granulado.
A causa geralmente aceita da corrosão intergranular é a existência de inclusões ou a precipitação de certos compostos (como carbonetos ou fase sigma) nos contornos de grão, o que reduz o potencial do eletrodo do metal base no contorno de grão.
Quando um dielétrico elétrico está presente na superfície, a corrosão se origina nos limites dos grãos e se desenvolve gradualmente para dentro. Se um determinado material sofrerá corrosão intergranular depende das características do material e do sistema médio.
Nesse sistema, a taxa de dissolução da região do limite de grão do material é maior que a do corpo de grão, levando à corrosão intergranular.
As medidas preventivas para corrosão intergranular são as seguintes.
a. Redução do teor de carbono: Ao reduzir o teor de carbono no aço abaixo do limite de solubilidade, evita-se a precipitação de carbonetos. Alternativamente, uma ligeira elevação acima do limite de solubilidade permite que apenas vestígios de carbonetos precipitem nos limites dos grãos, o que é insuficiente para representar um risco de corrosão intergranular.
b. Adição de elementos formadores de carboneto fortes: Liga com elementos estabilizadores como Titânio (Ti) e Nióbio (Nb), ou vestígios de elementos adsorventes de contorno de grão, como Boro (B). Esses elementos exibem forte afinidade com o carbono, formando carbonetos insolúveis pela combinação de carbono, níquel e nióbio nas formas TiC e NbC. Isto evita eficazmente o esgotamento do cromo causado pela precipitação de compostos Cr23C6.
c. Empregar métodos de tratamento térmico apropriados: Isto evita ou altera o tipo de precipitados formados nos limites dos grãos. O tratamento em solução permite a redissolução de carbonetos precipitados, eliminando a tendência à corrosão intergranular após a sensibilização. Prolongar o tratamento de sensibilização permite que o cromo tenha bastante tempo para se difundir nas regiões dos limites dos grãos, mitigando o esgotamento localizado do cromo.
1.4 Corrosão em fendas
a. Causas da corrosão em frestas:
Em um eletrólito, uma célula de concentração é formada devido a pequenas fendas entre o aço inoxidável e outro metal ou não metal. Isso resulta em corrosão localizada dentro ou perto da fenda, conhecida como corrosão em fenda. A corrosão em frestas pode ocorrer em vários meios, mas é mais severa em soluções de cloreto.
Na água do mar, o mecanismo de corrosão em frestas difere da corrosão por pite, mas seus mecanismos de difusão são semelhantes, ambos envolvendo processos autocatalíticos. Isto reduz o valor do pH dentro da fenda e acelera a migração de íons cloreto em direção à área de corrosão.
b. Medidas preventivas para corrosão em frestas:
Em meios corrosivos, fissuras podem ser formadas por depósitos na superfície do aço, produtos de corrosão e outras substâncias fixas. Sempre existem fendas nas juntas de flange e nas conexões aparafusadas, portanto, para mitigar os danos causados pelas fendas, é preferível usar a soldagem em substituição às conexões aparafusadas ou rebites.
Além disso, os depósitos na superfície metálica devem ser removidos regularmente. Áreas de vedação à prova d'água devem ser usadas nas juntas de flange. Melhorar os elementos de liga resistentes à corrosão por pites geralmente beneficia a resistência à corrosão em frestas. Para melhorar a resistência à corrosão em frestas, pode-se empregar aço inoxidável cromo-níquel contendo molibdênio.
1.5 Corrosão Galvânica
A corrosão galvânica é a corrosão causada pela conexão de dois ou mais metais diferentes, também conhecida como corrosão bimetálica.
a. Causas da corrosão galvânica:
A corrosão galvânica ocorre quando um componente metálico imerso em uma solução eletrolítica entra em contato com outros componentes com potenciais de eletrodo diferentes, ou quando há uma diferença de potencial em diferentes partes do mesmo componente metálico.
O metal ou peças com menor potencial de eletrodo corrói mais rapidamente, levando à corrosão galvânica. O grau de corrosão galvânica depende da diferença de potencial de corrosão entre os dois metais antes do curto-circuito, que varia com os diferentes meios.
b. Medidas preventivas para corrosão galvânica:
Para evitar a corrosão galvânica, o número de células primárias deve ser reduzido tanto quanto possível e a diferença de potencial do eletrodo deve ser reduzida. Devem ser feitos esforços para formar uma película de passivação estável, completa, densa e firmemente combinada na superfície do aço.
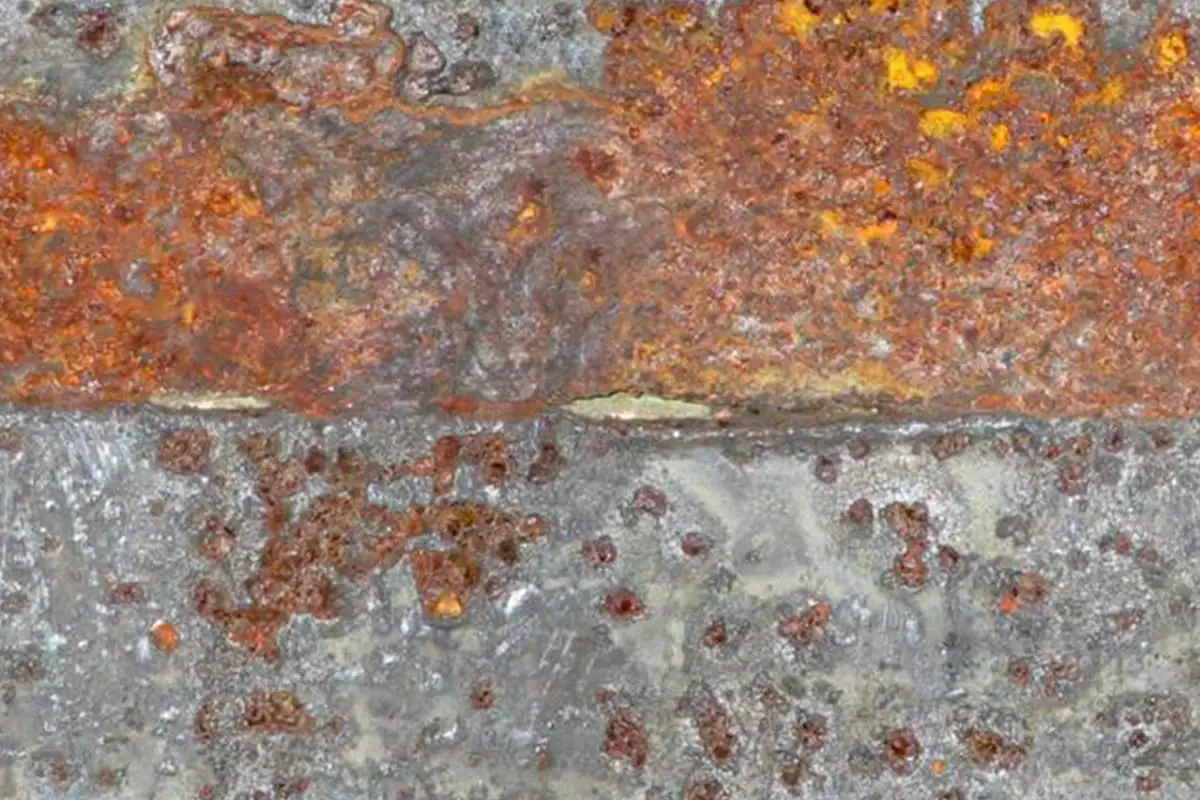
2. Resistência à corrosão do aço inoxidável em ambientes corrosivos
2.1 Corrosão Atmosférica
A resistência do aço inoxidável à corrosão atmosférica varia basicamente com o teor de cloretos na atmosfera. Em ambientes atmosféricos gerais, a resistência à corrosão do aço inoxidável é geralmente classificada da seguinte forma: Cr13, Cr17 e 18-8.
Em ambientes atmosféricos rurais, os aços Cr13 e Cr17 podem atender aos requisitos de resistência à corrosão. Em ambientes urbanos ou industriais, o aço Cr13 ou Cr17 pode ser escolhido para uso interno; O aço Cr17 deve ser escolhido pelo menos para uso externo.
Quando a atmosfera contém C12, H2S e CO2, o aço 18-8 e o aço inoxidável austenítico 18-14-2 podem atender aos requisitos de resistência à corrosão.
Em ambientes atmosféricos marinhos, a corrosão por íons cloreto é particularmente proeminente. Os aços Cr13 e Cr17 não podem atender aos requisitos de resistência à corrosão. A ferrugem e a corrosão por pites ocorrerão em muito pouco tempo.
A resistência à corrosão do aço 18-8 neste ambiente também não é ideal, como evidenciado pelo aparecimento de ferrugem fina e facilmente removível. A resistência à corrosão do aço 18-12-2 é comparativamente ideal.
Este aço geralmente tem uma taxa de corrosão muito baixa (0,0254 μm/a) e corrosão por pite superficial (0,024 cm). Sob condições atmosféricas marítimas, os aços inoxidáveis contendo molibdênio oCr17Ni12Mo2 e 30Cr-2Mo atendem basicamente aos requisitos de resistência à corrosão.
2.2 Meio Água
Com base no teor de sal, a água é classificada em água de alta pureza, água doce (teor de sal abaixo de 0,05%), água do mar (teor de sal entre 3,0% e 3,5%), água salobra (teor de sal entre água doce e água do mar) e água ácida.
A taxa de corrosão do aço inoxidável em água de alta pureza é a mais baixa (abaixo de 0,01 mm/a). O ambiente de água de alta pureza é frequentemente a indústria nuclear. Geralmente, os aços 0Cr19Ni9, 00CrNi11, 0Cr17Ni12Mo2, 0Cr17Ni14Mo2 atendem aos requisitos de resistência à corrosão.
Sob condições de água industrial (água doce), os aços Cr13, Cr17 e 18-8 geralmente atendem aos requisitos de resistência à corrosão. As peças que trabalham em meios aquáticos estão sujeitas à cavitação. Cr13Ni4, M50NiL, 16CrNi4Mo são aços inoxidáveis de alta resistência e resistentes à cavitação.
Os aços inoxidáveis 0Cr13, Cr13, Cr17, 0Cr18Ni9 ou 0Cr18Ni11Ti são comumente usados para produtos expostos à atmosfera e frequentemente sujeitos à corrosão por água doce. Os equipamentos médicos geralmente usam aços inoxidáveis martensíticos 3Cr13, 4Cr13, 9Cr18.
As principais formas de danos ao aço inoxidável na água do mar são corrosão por pites, corrosão em frestas e corrosão sob tensão. Também é influenciado por muitos fatores, como o teor de oxigênio da água do mar, concentração de íons cloreto, temperatura, vazão e poluição.
Geralmente, em água do mar abaixo de 30 ℃, o aço inoxidável ω (Mo) 2% -4% pode atender aos requisitos de resistência à corrosão.
Água ácida refere-se à água natural contaminada que é lixiviada de minérios e diversas substâncias. A água ácida geralmente contém uma grande quantidade de ácido sulfúrico livre e uma grande quantidade de sulfato de ferro. Sob tais condições, o aço inoxidável austenítico apresenta maior resistência à corrosão.
2.3 Solo
Os metais enterrados no solo estão sujeitos a mudanças constantes devido ao clima e a vários outros fatores. Os aços inoxidáveis austeníticos normalmente apresentam resistência à corrosão na maioria dos solos.
Os aços dos tipos 1Cr13 e 1Cr17 tendem a sofrer corrosão por pites em muitos solos. O aço inoxidável 0Cr17Ni12Mo2 demonstra resistência à corrosão por pite em todos os tipos de solo.
2.4 Ácido Nítrico
Quase todos os aços inoxidáveis passivam prontamente em ácido nítrico diluído, mostrando uma resistência à corrosão bastante boa. Os aços inoxidáveis ferríticos e os aços inoxidáveis austeníticos com teor de cromo não inferior a 14% apresentam excelente resistência à corrosão por ácido nítrico.
Sob condições de trabalho com menos de 65% (em peso) de ácido nítrico diluído, geralmente é usado aço inoxidável tipo 18-8. Em condições com 65% a 85% (em peso) de ácido nítrico diluído, o aço inoxidável Cr25Ni20 pode atender aos requisitos de resistência à corrosão.
Quando a concentração de ácido nítrico é muito alta, os aços inoxidáveis de Si (como 0Cr13Si4NbRE, 1Cr17Ni11Si4, 00Cr17Ni17Si6, etc.) podem atender aos requisitos de resistência à corrosão.
Os aços inoxidáveis contendo Mo geralmente não são resistentes à corrosão por ácido nítrico, mas às vezes são usados para prevenir a corrosão por pite em condições que envolvem ácido nítrico com íons cloreto.
2,5 ácido sulfúrico
Classes de aço inoxidável padrão raramente são usadas em soluções de ácido sulfúrico. À temperatura ambiente, o aço inoxidável 0Cr17Ni12Mo2 é resistente à corrosão quando a concentração de ácido sulfúrico excede 85% ou é inferior a 15%.
Os aços inoxidáveis austeníticos e os aços inoxidáveis duplex ferrítico-austeníticos contendo Mo, Cu, Si (com uma porcentagem em peso de 3% a 4%) apresentam a melhor resistência à corrosão ao ácido sulfúrico.
2.6 Meio de Ácido Fosfórico
Os aços inoxidáveis austeníticos apresentam boa resistência à corrosão em soluções de ácido fosfórico. No entanto, em aplicações práticas, o ácido fosfórico frequentemente contém várias impurezas, como flúor, íons cloreto e íons metálicos como alumínio, magnésio e íons sulfato, os quais tendem a acelerar a corrosão do aço inoxidável.
Os aços inoxidáveis austeníticos 00Cr27Ni31Mo3Cu e 00CtNi35Mo3Cu são os melhores aços inoxidáveis em termos de desempenho abrangente e resistência à corrosão de impurezas de ácido fosfórico, como íons de flúor e cloreto.
Sob essas condições de trabalho, 0Cr17Ni14Mo2, 00Cr19Ni13Mo3 e outros com teor de Mo de 2% a 4% em peso, aço duplex com alto Cr 00Cr26Ni6Mo2Cu3 e aço inoxidável com alto Mo 00Cr20Ni25Mo4.5Cu e aços inoxidáveis super ferríticos com alto Cr 00Cr26Mo1, 00Cr30Mo2, etc. ., todos apresentam boa resistência à corrosão por ácido fosfórico.
Os aços inoxidáveis martensíticos e ferríticos apresentam notavelmente menor resistência à corrosão do ácido fosfórico em comparação com os aços inoxidáveis austeníticos.
2.7 Ácido Clorídrico
À temperatura ambiente, o ácido clorídrico em várias concentrações pode corroer rapidamente o aço inoxidável, portanto o aço inoxidável não pode ser usado sob condições que envolvam ácido clorídrico.
2.8 Ácido Acético
Os aços inoxidáveis austeníticos geralmente apresentam excelente resistência à corrosão por ácido acético. À medida que o teor de molibdênio (Mo) no aço aumenta, sua resistência à corrosão melhora. No entanto, em ácido acético contendo íons cloreto, a taxa de corrosão acelera significativamente.
Aços inoxidáveis como 0Cr17Ni12Mo2 e 00Cr18Ni16Mo5 com teor de molibdênio de 2% a 4%, duplex 00Cr18Ni16Mo3N e algumas ligas à base de níquel apresentam excelente resistência à corrosão.
2.9 Ácido Fórmico
À temperatura ambiente, os aços inoxidáveis austeníticos apresentam excelente resistência à corrosão por ácido fórmico. Mas sob condições que envolvem ácido fórmico quente, ele pode corroer rapidamente o aço inoxidável sem molibdênio.
O 0Cr17Ni12Mo2 e 0Cr19Ni13Mo3 possuem propriedades de corrosão por ácido fórmico resistentes ao calor. O ácido fórmico é corrosivo para os aços inoxidáveis martensíticos e ferríticos em todas as temperaturas.
2.10 Ácido Oxálico
O aço inoxidável apresenta excelente resistência à corrosão em temperatura ambiente com concentração de 50%.
Em temperaturas mais altas ou concentração de 100%, todos os aços inoxidáveis apresentam baixa resistência à corrosão do ácido oxálico.
2.11 Ácido Lático
A uma temperatura máxima de cerca de 38°C, o aço inoxidável 0Cr18Ni9 apresenta excelente resistência à corrosão.
Tipos resistentes a temperaturas mais altas incluem 0Cr17Ni12Mo2 e 0Cr19Ni13Mo3. Geralmente, os aços inoxidáveis martensíticos e ferríticos apresentam baixa resistência à corrosão do ácido láctico.
2.12 Ácido Fluorídrico
A maioria dos aços inoxidáveis não é resistente à corrosão do ácido fluorídrico. Quando oxigênio e oxidantes estão presentes no ácido fluorídrico, a resistência à corrosão dos aços inoxidáveis austeníticos com alto teor de níquel, molibdênio e cobre melhora significativamente.
2.13 Álcalis
Os aços inoxidáveis geralmente apresentam boa resistência a álcalis fracos. Tanto o cromo quanto o níquel no aço contribuem positivamente para a resistência à corrosão alcalina. O aço inoxidável ferrítico com 26% a 30% de cromo e o aço inoxidável austenítico com mais de 20% de níquel apresentam forte resistência à corrosão alcalina.
2.14 Ureia
Aços inoxidáveis austeníticos e aços inoxidáveis ferríticos, como Cr-Ni e Cr-Mn-N com teor de níquel de 2% a 4% (por exemplo, 0-1Cr18Ni12Mo2Ti, grau de uréia 001Cr17Ni14Mo2, 00Cr25Ni22Mo2N) são usados na produção de uréia. Eles possuem excelente resistência à corrosão em soluções de ureia.