Na produção de peças de locomotivas usando dobra de chapas metálicas, muitas peças não podem ser produzidas diretamente de acordo com os desenhos de projeto. Como resultado, torna-se necessário adicionar esticadores, posicionamento ou conjuntos especiais de dobra durante o blanking e removê-los após a dobra para alcançar o resultado desejado.
Esta postagem aborda principalmente os problemas e soluções relacionados ao processo no processamento de dobra, que está dividido em três seções.
A primeira seção fornece uma visão geral dos métodos de processamento de dobra, a segunda seção discute possíveis problemas relacionados ao processo e suas soluções correspondentes no processamento de dobra, e a seção final resume os pontos principais.
Visão geral dos métodos de processamento de dobra
A flexão é essencialmente um processo de deformação a frio usado para moldar placas em formatos específicos. É um método de processamento de pressão realizado à temperatura ambiente. A dobra pode ser usada em uma variedade de materiais, incluindo materiais metálicos, não metálicos e compósitos.
Durante este processo, a peça é processada por uma matriz de dobra e uma prensa dobradeira hidráulica. A precisão dimensional das peças dobradas é garantida por matrizes superiores e inferiores e equipamentos de dobra. O processo envolve a aplicação de força de flexão à matriz superior da chapa metálica, gerando uma força de reação no ponto de suporte da matriz inferior e forçando a deformação da chapa metálica, criando um momento fletor.
O ângulo de curvatura final da chapa metálica é determinado pela profundidade da matriz superior na matriz inferior. A Figura 1 ilustra as principais peças de trabalho da prensa dobradeira NC, incluindo o batente traseiro, a matriz superior e a matriz inferior.
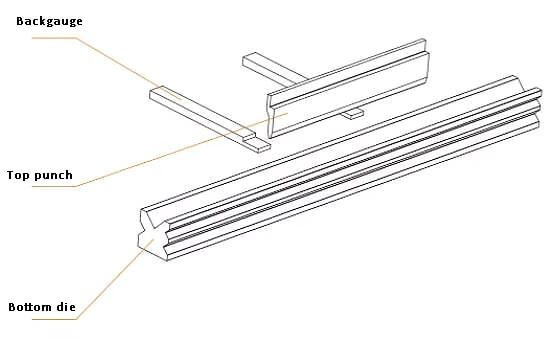
Fig. 1 Principais peças de trabalho da dobradeira
O medidor traseiro é um componente operacional que regula o posicionamento da linha de dobra.
As matrizes superior e inferior são utilizadas para gerenciar o ângulo de curvatura e o raio interno da peça de trabalho.
A qualificação da peça é determinada principalmente por estas três partes.
Possíveis problemas de processo em dobra e suas soluções
Na produção de peças de locomotivas, muitas peças dobradas não podem ser produzidas diretamente de acordo com os desenhos de projeto. Portanto, torna-se necessário adicionar alguns esticadores, posicionamentos ou moldes especiais durante o blanking, que podem ser removidos após a dobra para obter o produto desejado.
As situações típicas que requerem macas de processo estão resumidas abaixo.
Geração e prevenção de colapso de borda
Conforme Figura 2, a insuficiência de material em um dos lados da peça impede a colocação do material na matriz inferior, resultando no colapso de algumas estruturas durante a flexão. Isto claramente não atende aos requisitos de projeto.
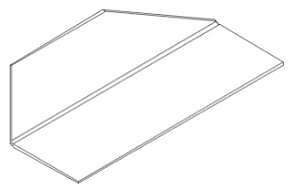
Fig. 2 Estrutura de borda dobrável
Conforme mostrado no detalhe estrutural da Fig. 3, geralmente, quando este ângulo α for menor que 50°, haverá um problema que não pode ser dobrado. Medidas de processo devem ser tomadas para evitá-lo e garantir que a peça de trabalho seja qualificada.
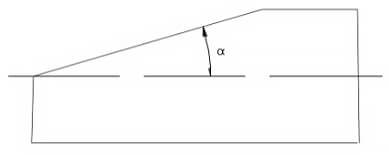
Fig. 3 Peça de trabalho com borda de fácil colapso
Esquema de processo para resolver colapso de borda
A Figura 4 mostra o esquema geral de amarração do processo, e a parte da linha pontilhada dupla é a amarração do processo definida.
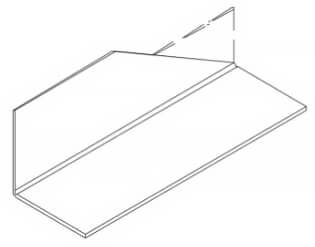
Fig. 4 Esquema de reforço do processo
A Figura 5 mostra o desenho detalhado do processo de amarração.
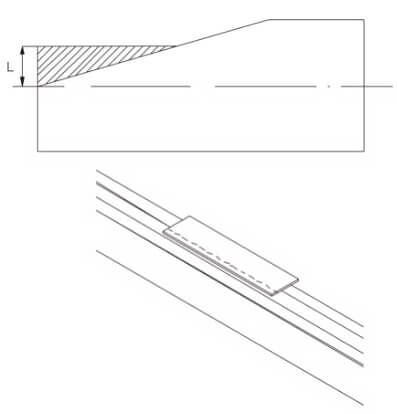
Fig. 5 Detalhe da estrutura do processo de peças fáceis de colapsar
Se o comprimento da peça for suficiente para retenção e posicionamento do material após o processo de dobra, normalmente é definido como L ≥ 0,6 mm (onde V é o tamanho da abertura da matriz inferior).
É essencial garantir que a folha possa ser colocada na matriz inferior e se estender além da borda da matriz em pelo menos 3 mm.
Se o comprimento da peça de trabalho for insuficiente, geralmente é adicionada uma barra de ligação para corresponder à largura da estrutura original da peça de trabalho. Esta abordagem não apenas resolve problemas de dobramento, mas também garante um posicionamento preciso.
Solução para a dificuldade de posicionamento da linha de dobra
Conforme ilustrado na Figura 6, algumas peças projetadas para posicionamento possuem cantos vivos ou suas bordas retas, destinadas ao posicionamento, são muito curtas. Isto torna difícil localizar a linha de dobra com precisão durante o processo de dobra.
Para obter um posicionamento preciso da linha de dobra, é necessário adicionar uma estrutura de processo.
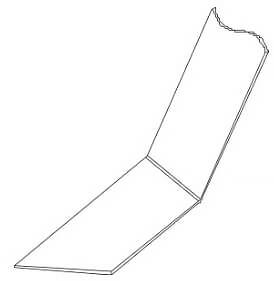
Fig. 6 Posicionamento da linha de flexão
Solução: Fig. 7 e fig. 8 são dois esquemas de alongamento do processo para resolver o difícil posicionamento da linha de dobra, em que a linha pontilhada dupla é o alongamento do processo.
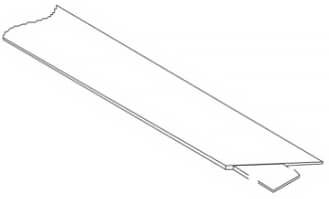
Fig. 7 Esquema I para resolver a dificuldade de posicionamento da linha de dobra
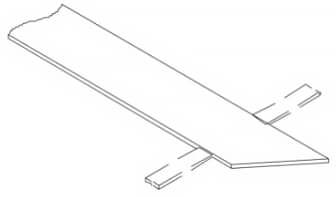
Fig. 8 Solução para o difícil posicionamento da linha de dobra figura 2
A Figura 9 mostra o diagrama de processamento do esquema 1. Ao adotar este esquema, a peça pode ser bem posicionada.
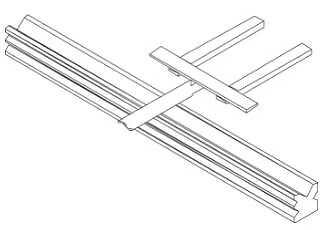
Fig. 9 Diagrama de processamento do esquema I
A Figura 10 mostra o diagrama esquemático de processamento do esquema 2. Neste esquema, placas laterais são adicionadas em ambos os lados da peça de trabalho, o que pode garantir que a peça processada atenda aos requisitos do projeto.
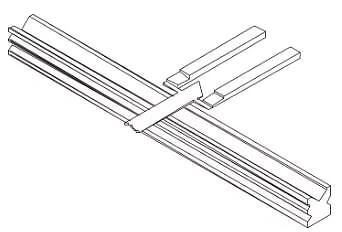
Fig. 10 Diagrama de processamento do esquema II
Solução para fácil deformação da peça
De acordo com a Figura 11, a máquina de corte a laser molda a peça quando sua espessura é baixa.
Vale ressaltar que o corte a laser se enquadra na categoria de corte por fusão, gerando altas temperaturas.
No entanto, no caso da estrutura da peça representada na figura, ela pode sofrer deformação, resultando em posicionamento de flexão impreciso. Para evitar tais problemas, devem ser tomadas medidas de processo apropriadas.
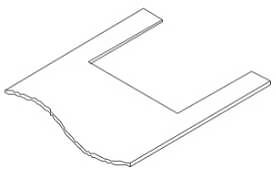
Fig. 11 Estrutura facilmente deformada
Solução: conforme mostrado na Fig. 12, para a grande folga mostrada na figura, a peça é fácil de deformar durante o manuseio ou posicionamento, resultando em posicionamento de flexão impreciso.
Geralmente, o alongamento do processo mostrado na figura será adicionado.
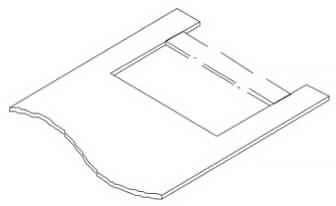
Fig. 12 Adicionando macas de processo
A incorporação de macas no entalhe pode aumentar a rigidez geral da peça e evitar deformações.
Após a conclusão do processo de dobra, utilize plasma manual para cortar as macas.
Para peças grandes e compridas, é necessário reter as macas para evitar deformações durante o levantamento ou instalação no processo subsequente. As macas deverão ser retiradas somente após a soldagem no próximo processo.
Solução que a largura da ranhura da peça é muito estreita para dobrar
Conforme ilustrado na Figura 13, a largura da ranhura da peça de trabalho é muito estreita, fazendo com que ela interfira na matriz superior durante a dobra. Isso, por sua vez, leva à deformação da peça, o que impossibilita a conclusão do processamento, e o tamanho final da peça não atende aos requisitos especificados no desenho.
Para resolver este problema, recomendamos a solução mostrada na Figura 14. Antes de dobrar a peça de trabalho, é aconselhável dobrar inversamente um determinado ângulo no meio da peça de trabalho. Posteriormente, a peça pode ser dobrada de acordo com as especificações do desenho.
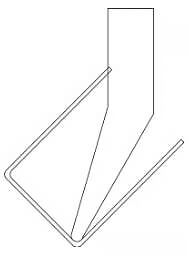
Fig. 13 Interferência entre a peça e a matriz superior
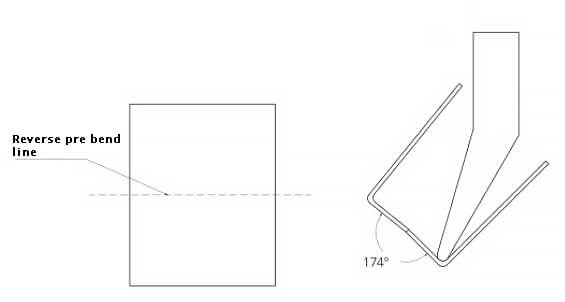
Fig. 14 Após a pré-dobra, a matriz superior não interfere mais na peça de trabalho
Depois que a peça de trabalho for dobrada, pressione a dobra pré-dobrada com uma matriz de achatamento (Fig. 15) e garanta o nivelamento e os requisitos de tamanho da peça de trabalho.
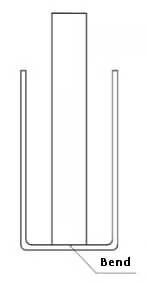
Fig. 15 Pressão de ponto e achatamento com matriz de achatamento na pré-dobragem
Solução para o problema de a peça de trabalho ser muito longa e a largura da ranhura ser muito estreita para dobrar
Com base na Figura 16, o comprimento desenvolvido mede 2.500 mm, a largura da ranhura é de 100 mm e a altura da perna é de 64 mm. Esses parâmetros são inseridos de acordo com os requisitos do cartão de processo. Para prosseguir, é escolhida uma matriz superior com R8 V60° e altura de 134mm, e uma matriz inferior com nº V07, com abertura de 35mm e profundidade de 65mm.
Vários parâmetros de deflexão de flexão são então inseridos e a peça de trabalho é colocada na mesa de trabalho para realizar a flexão necessária. No entanto, durante o processo de dobragem, surge um problema. Como a matriz superior do pescoço de ganso R8 é espessa e o pescoço de ganso é muito pequeno, a primeira borda de dobra interfere no molde quando a dobra unilateral do segundo lado é rápida para atingir 90°. Esta interferência impossibilita garantir o ângulo de curvatura.
A tentativa de forçar a flexão pode causar vários problemas, incluindo deformação da peça, danos ao molde e não conformidade do tamanho da peça com o desenho.
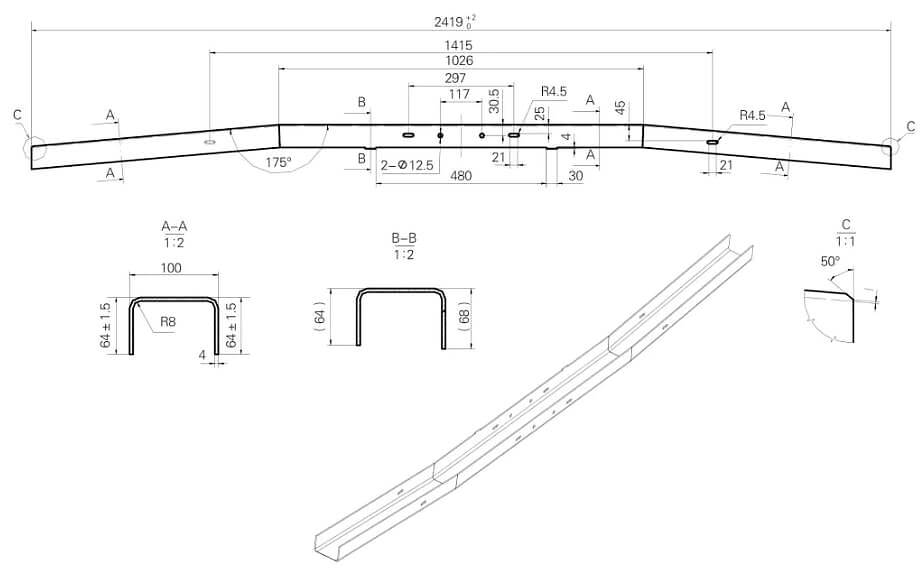
Fig. 16 A largura da ranhura da peça é muito estreita para ser dobrada
Solução para peças muito longas e largura de canal muito estreita
Após realizar pesquisas in loco e estudar os parâmetros da máquina-ferramenta, além de observar o molde existente, descobrimos que a abertura do pescoço de ganso do molde superior R6 é maior do que o necessário. No entanto, após testes, descobrimos que atende aos requisitos do processo.
Seguindo o fluxo de trabalho acima, realizamos operações síncronas sem qualquer interferência entre o molde e a peça, o que atendeu aos requisitos.
Após vários ajustes nos parâmetros do eixo Y e do eixo X, as dimensões de cada ponto da peça atenderam aos requisitos do desenho.
Após a identificação, confirmamos que atende aos requisitos do processo.
Conclusão
O alongamento do processo e as ranhuras anti-rachaduras são indispensáveis na dobra de chapas metálicas e são cruciais para garantir a qualidade da peça e a eficiência do processamento.
Vale a pena notar que, ao mesmo tempo que garante a qualidade do produto, também vale a pena discutir a aplicação flexível de alongamento do processo e ranhuras anti-rachaduras, juntamente com a redução das taxas de desperdício de chapa.