Resumo:
Conectar alumínio e aço pode produzir peças automotivas leves. No entanto, a fissuração de compostos intermetálicos causada pela soldagem destes metais diferentes pode impactar significativamente o desempenho da junta.
Este post apresenta os principais métodos de soldagem para soldagem a laser de alumínio e aço e explica o status da pesquisa nos últimos anos.
O aço galvanizado é um substrato de aço revestido com camadas de zinco de diferentes espessuras. O processo de zincagem é categorizado em galvanoplastia e galvanização a quente.
A camada de zinco não apenas fornece blindagem física, mas também oferece proteção eletroquímica ao substrato de aço.
Devido à sua excelente resistência à corrosão, o aço galvanizado é amplamente utilizado em diversos setores, como transporte, energia elétrica, construção, instalações de aquecimento, instrumentos e móveis.
Em particular, a aplicação de aço galvanizado comum, aço galvanizado de alta resistência e aço galvanizado de ultra-alta resistência na indústria automobilística melhora a resistência à corrosão e prolonga a vida útil da carroceria e de outras peças.
No entanto, a presença de uma camada de zinco torna a soldagem por fusão de placas de aço galvanizado um desafio. Isso ocorre porque o ponto de fusão do zinco é 420 ℃, seu ponto de ebulição é 908 ℃, enquanto o ponto de fusão do aço base é 1300 ℃ e seu ponto de ebulição é 2861 ℃.
Durante o processo de fusão e soldagem, o zinco tende a evaporar e oxidar extensivamente, levando a defeitos como poros, fusão incompleta e rachaduras.
O alumínio e suas ligas são conhecidos por suas propriedades de leveza (com densidade de 2,7g/cm3), alta resistência específica, excelente condutividade elétrica e térmica, resistência à corrosão e capacidade de reter boas propriedades mecânicas mesmo em baixas temperaturas.
No mundo de hoje, a energia, a segurança e a proteção ambiental tornaram-se questões cruciais. Com a crescente preocupação com a poluição ambiental e a crise energética, conseguir veículos leves tornou-se um foco global.
Consequentemente, extensas pesquisas foram conduzidas em estruturas compostas de alumínio/magnésio, alumínio/titânio, titânio/alumínio e alumínio/aço em todo o mundo.
As estruturas compostas de alumínio/aço aproveitam ao máximo as vantagens de ambos os materiais para reduzir o peso e a poluição, e encontraram amplas aplicações nas indústrias automotiva, de aviação e de construção naval.
A aplicação de conexões alumínio-aço no painel da porta do automóvel está ilustrada na figura abaixo.
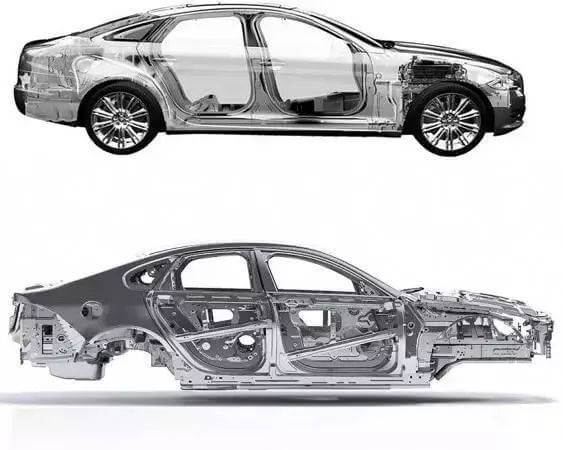
A tecnologia de soldagem híbrida a arco laser, conforme mostrado no diagrama esquemático experimental da Fig. 2, é um método de soldagem novo e eficiente desenvolvido na década de 1970.
A alta densidade de energia do laser permite uma penetração mais profunda, mas a ponte da lacuna é ruim e a precisão da montagem deve ser alta.
A faixa de aquecimento do arco é ampla, o que permite obter uma solda mais ampla, mas a ponte do arco até a folga é boa.
Ao utilizar suas respectivas características, a tecnologia de soldagem híbrida a arco laser pode obter uma solda de topo amplo e grande penetração.
O plasma produzido pelo laser pode estabilizar o arco, tornando o processo de soldagem híbrida adaptável e eficiente.
Honggang Donga et al. inventou um método para conectar metais diferentes usando grandes fontes de calor compostas de laser e arco.
A patente se concentra na soldagem híbrida com fonte de calor a arco laser com um pequeno ponto, que não pode ser aplicada à conexão entre aço e alumínio, aço e cobre e outros metais diferentes.
Neste método, o laser tem um efeito estabilizador óbvio no arco, que é usado para derreter o metal de adição e o metal base de baixo ponto de fusão.
O laser de ponto grande pode controlar com precisão a entrada de calor.
Testes de propriedade de tração em juntas de liga de alumínio 5A02 e aço galvanizado obtidos por este método mostram que a posição de falha da amostra ocorre na zona afetada pelo calor de soldagem em um lado do metal base da liga de alumínio, e não na zona de conexão de brasagem. A resistência da junta pode chegar a 153,1 MPa. Qin e outros adotam soldagem composta MIG a laser de aço galvanizado/liga de alumínio e fio de soldagem AlSi5.
Resultados experimentais mostram que a interface de brasagem produz 2 a 4 μm e os grupos de fases são FeAl2, Fe3Al5 e Fe4Al13. A resistência máxima à tração da junta é 247,3 MPa.
Wangshujun et al. também utilizou tecnologia de soldagem híbrida MIG a laser e fez experiências com três soldas diferentes: AlSi5, AlSi12 e AlMg5 para estudar os efeitos de compostos intermetálicos, microestrutura da solda e formação após a adição de Si e Mg.
Os resultados mostram que o aumento do teor de Si pode refinar os grãos na zona de fusão e aumentar a microdureza da zona de fusão. A microdureza da solda Al-Si na zona de fusão é maior que a da solda Al-Mg.
A espessura média da camada de composto intermetálico para soldas AlSi12, AlSi5 e AlMg5 é 0,90 μm, 1,49 μm e 2,64 μm, respectivamente.
Concluiu-se que a presença de Si nas soldas inibe a difusão do Fe e reduz a formação de compostos intermetálicos.
A análise XRD da camada intermediária revela que as camadas de compostos intermetálicos correspondentes a AlSi5 e AlSi12 consistem nas fases Fe2Al5, Fe4Al13 e Al0,5Fe3Si0,5, enquanto aquelas correspondentes a AlMg5 consistem nas fases FeAl2, Fe2Al5 e Fe4Al13.
A resistência da junta das soldas AlMg5, AlSi5 e AlSi12 é 178,9 MPa, 172,43 MPa e 144 MPa, respectivamente.
Concluiu-se que um aumento no teor de Si é prejudicial à resistência da junta, enquanto a adição de Mg aumenta a resistência da junta. No entanto, não foi explicado como o Si e o Mg afetam a resistência da junta.
Thomy et al. conduziu um estudo sobre a interação entre laser e arco plasma durante soldagem híbrida a arco laser e desenvolveu um cabeçote de soldagem híbrido a arco laser coaxial.
eubrasagem a laser
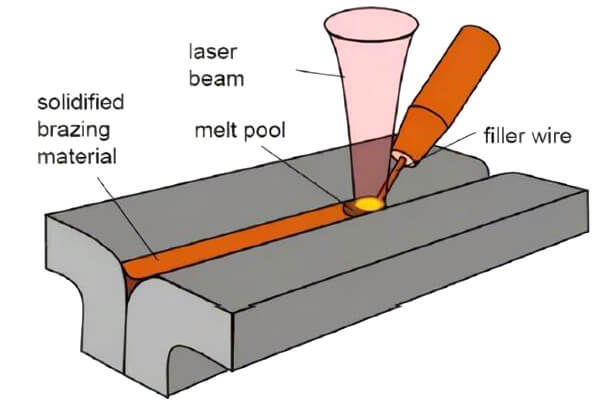
A brasagem envolve o uso de solda com ponto de fusão inferior ao do metal base. Ao aquecer a uma temperatura superior ao ponto de fusão da solda e inferior ao ponto de fusão do metal base, a solda derrete enquanto o metal base permanece sólido.
A solda líquida então umedece o metal base e, sob a ação capilar da lacuna de brasagem, preenche automaticamente quaisquer lacunas no metal base e se difunde com ela para criar uma junta forte.
A brasagem por fusão combina as características da brasagem e da soldagem por fusão, tornando-a ideal para conectar materiais diferentes com grandes diferenças nas propriedades físicas.
Quando o aço e o alumínio são brasados, o aço permanece sólido enquanto o alumínio e a solda derretem. A conexão de brasagem resultante é formada no lado aço/solda, enquanto a soldagem por fusão ocorre no lado solda/alumínio.
O princípio básico da brasagem por fusão para aço e alumínio é combinar alumínio fundido e solda com aço sólido por meio de uma reação de interface.
Neste método, a solda pode ou não ser adicionada para fins de soldagem.
Peyre et al. conduziram um estudo sobre a ligação de aço galvanizado e liga de alumínio usando brasagem por fusão a laser sem solda.
Suas descobertas indicam que uma camada de interface de 2 a 20 μm de espessura se forma ao longo da interface aço-alumínio.
A camada consiste principalmente na fase Fe2Al5, com dureza de até 1200HV. Isto leva a fissuras na junta, causando uma redução significativa nas propriedades mecânicas da junta.
A evaporação do zinco produz poros, mas um revestimento de zinco com 10 μm de espessura promove a umedecimento e espalhamento do alumínio no aço.
Testes de tração indicam que o fluxo de revestimento na superfície do aço galvanizado pode inibir a evaporação do zinco. O aço não galvanizado, entretanto, apresenta baixa resistência mecânica.
Para controlar a formação de compostos intermetálicos Fe-Al e melhorar o desempenho da junta, alguns pesquisadores usaram solda durante a brasagem a laser para alterar a composição química da junta.
Serra et al. utilizou solda 4047 (Al-12Si) na conexão de brasagem por fusão a laser de alumínio/aço, resultando em uma junta contínua sem defeitos macro significativos e uma fina camada de composto intermetálico Fe Al-Si na interface aço/solda.
O efeito do Si no crescimento de compostos intermetálicos Fe-Al foi investigado utilizando solda Al-12Si. O mecanismo proposto sugere que o Si reduz a temperatura de fusão do alumínio, influencia a viscosidade e a tensão superficial do alumínio fundido e, subsequentemente, afeta o ângulo e a largura de molhamento da solda.
Além disso, alguns estudiosos adicionaram Mg, Cu e outros elementos à solda para explorar o efeito da liga da solda na microestrutura e nas propriedades da solda.
Dharmendra et al. conduziu um teste de brasagem por fusão em uma junta sobreposta feita de aço galvanizado DP600 e liga de alumínio AA6016 usando laser Nd:YAG de pulso contínuo.
Eles usaram arame de soldagem Zn-Al contendo 85% Zn e 15% Al no teste e variaram a potência do laser, a velocidade de soldagem e a velocidade de alimentação do arame.
Os pesquisadores descobriram que a espessura da camada de reação estava entre 3 e 23μm.
Quando o aporte térmico ficou entre 60 e 110J/mm, a resistência à tração da junta atingiu 220MPa, com a posição de fratura localizada longe da solda e próxima ao lado da liga de alumínio.
Nas velocidades de soldagem de 0,5 e 0,8m/min, as espessuras correspondentes dos compostos intermetálicos foram de 8 e 12μm, respectivamente.
Os testes de tração mostraram que a junta apresentou maior resistência mecânica quando a espessura do composto intermetálico estava entre 8 e 12μm.
Se a espessura fosse inferior a 8μm, a resistência mecânica aumentava à medida que a camada intermetálica aumentava, enquanto que se fosse superior a 12μm, a resistência mecânica diminuía.
Foi explicado que quando a camada de composto é fina, a fissura inicia-se ao longo da frágil camada de composto intermetálico, resultando numa resistência à fractura muito baixa.
Por outro lado, quando a camada composta é espessa, a resistência mecânica também é baixa devido à fragilidade da camada em relação a outras áreas.
Laukant et al. conduziu um teste de brasagem por fusão a laser usando solda ZnAl2 em alumínio/aço. Os resultados mostraram que foram produzidas camadas de compostos intermetálicos de cerca de 5μm FeAl, e a força de cisalhamento da junta atingiu até 9 KN.
Da mesma forma, Rajashekhara Shabadi et al. conduziu um teste de brasagem por fusão a laser usando solda ZnAl30 em AA6016 e aço galvanizado com baixo teor de carbono. O composto intermetálico formado nos resultados do teste é principalmente Fe2Al5Znx, que também pode conter ZnFeAl3, com espessura de cerca de 10μm.
Recentemente, alguns estudiosos conduziram experimentos de brasagem por fusão a laser em aço aluminizado de alta resistência e liga de alumínio.
Por exemplo, Windmann et al. realizaram um teste de brasagem por fusão a laser usando solda AlSi3Mn e descobriram a formação da fase Al8Fe2Si na interface AlSi3Mn/Mn22B5.
Além disso, a espessura do composto intermetálico criado na interface Mn22B5/AlSi3Mn é de 2 a 7μm, e a resistência ao cisalhamento da junta é de 21 a 74MPa.
Ao pré-aquecer a superfície do aço antes da soldagem, a resistência da junta pode aumentar para 210 a 230MPa.
Pesquisas recentes mostraram que tanto a solda Al-Si quanto a solda Zn-Al criam inevitavelmente compostos intermetálicos.
No entanto, a sequência de crescimento dos compostos intermetálicos Fe Al-Si e a identificação da fase de reação da solda Zn-Al requerem investigação adicional.
A soldagem por fusão a laser é uma tecnologia promissora para conectar aço e alumínio.
Conclusão
A soldagem híbrida a arco laser é usada principalmente para soldar placas mais espessas devido à sua alta eficiência de soldagem.
A brasagem por fusão a laser possui grande potencial para aplicação na produção de automóveis leves.
O processo de brasagem por fusão a laser foi usado para conectar metais finos e diferentes feitos de alumínio e aço, utilizando soldas Al-Si e Zn-Al.
No entanto, ainda existem vários desafios na soldagem a laser de aço galvanizado/ligas de alumínio para fabricação de automóveis. Por exemplo, a baixa absortividade do material à energia do laser resulta na geração de plasma, o que pode impactar a estabilidade do processo de soldagem.
Além disso, o processo de conexão do alumínio e do aço pode produzir compostos intermetálicos de Fe-Al frágeis. Além disso, a compatibilidade metalúrgica da solda fundida com o metal base da liga de alumínio e sua molhabilidade com o aço do metal base precisam ser consideradas.
Finalmente, é crucial controlar e prevenir defeitos de soldagem como poros, trincas, fusão incompleta e inclusão de escória.