1. Características do Arco Plasma e seu Gerador
1. Formação do Arco Plasmático
Um arco de plasma é um arco de argônio com eletrodo de tungstênio comprimido com alta densidade de energia, temperatura e força de arco. O arco plasma é obtido através de três efeitos de compressão:
1) Compressão Mecânica: A expansão restrita da área da seção transversal da coluna do arco, causada pela abertura do bocal de cobre resfriado a água, é conhecida como compressão mecânica.
2) Compressão Térmica: A água de resfriamento no bocal forma uma camada de gás frio próximo à parede interna do bocal, reduzindo a área condutora efetiva da coluna de arco. Isto aumenta ainda mais a densidade de energia e a temperatura da coluna de arco. Este efeito, obtido através do resfriamento com água para aumentar ainda mais a temperatura e a densidade de energia da coluna do arco, é conhecido como compressão térmica.
3) Compressão Eletromagnética: Devido aos efeitos de compressão acima mencionados, a densidade da corrente do arco aumenta e a força de contração eletromagnética gerada pelo próprio campo magnético da corrente do arco torna-se mais forte. Isso resulta em compressão adicional do arco, conhecida como compressão eletromagnética.
2. Classificação do Arco Plasmático
(1) Arco não transferido
O arco não transferido queima entre o eletrodo de tungstênio e o bico. Durante a soldagem, o pólo positivo da fonte de energia é conectado ao bico de cobre resfriado a água, enquanto o pólo negativo é conectado ao eletrodo de tungstênio. A peça de trabalho não está conectada ao circuito de soldagem. O arco é realizado pela ejeção de gás plasma em alta velocidade. Este tipo de arco é adequado para soldar ou cortar metais e não metais mais finos.
(2) Arco Transferido
O arco transferido queima diretamente entre o eletrodo de tungstênio e a peça de trabalho. Durante a soldagem, o arco não transferido entre o eletrodo de tungstênio e o bico é primeiro aceso e, em seguida, o arco é transferido para o eletrodo de tungstênio e a peça de trabalho. O bico não está conectado ao circuito de soldagem durante a operação. Este tipo de arco é utilizado para soldagem de metais mais espessos.
(3) Arco Combinado
Um arco combinado refere-se a um arco onde coexistem o arco transferido e o arco não transferido. O arco misto pode manter a estabilidade em correntes muito baixas, tornando-o particularmente adequado para soldagem de placas finas e ultrafinas.
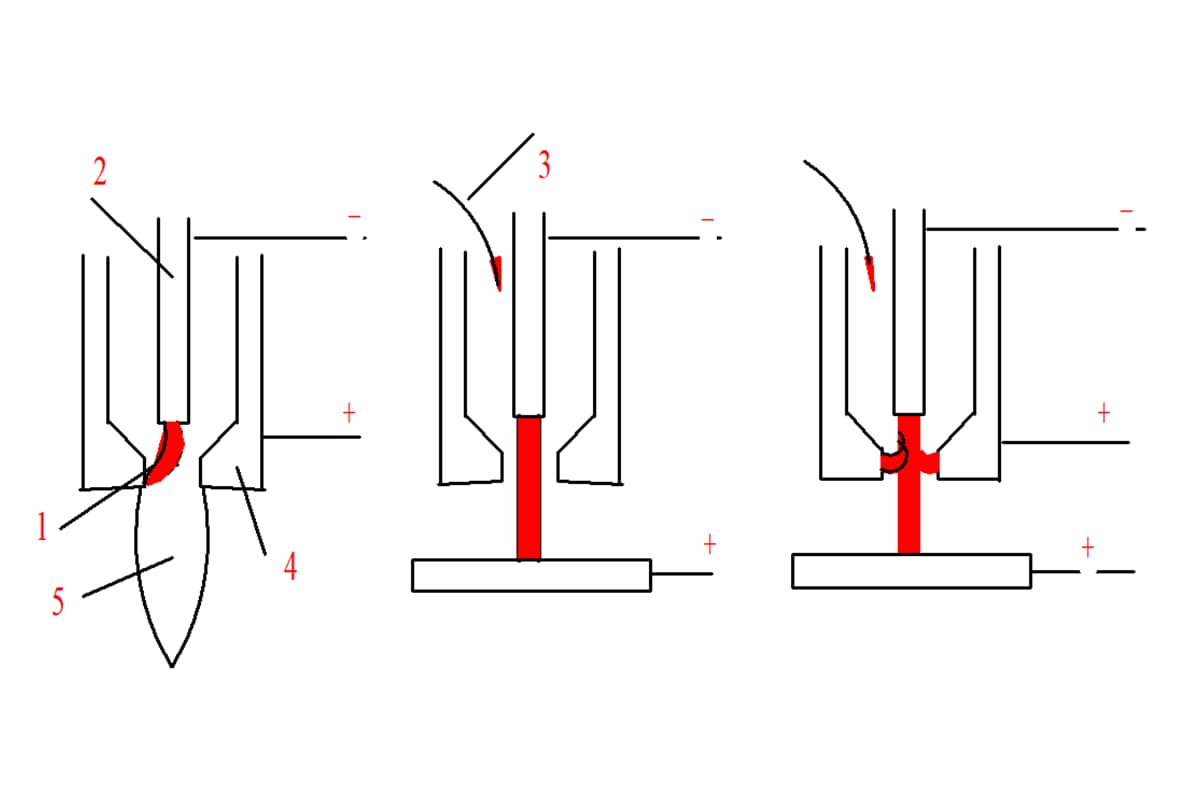
Arco Transferido
Arco Combinado
3. Características do Arco Plasma
(1) A curva característica estática do arco plasma é significativamente diferente daquela do arco TIG:
- 1.1 O valor E é maior, deslocando-se assim para cima. A seção reta torna-se mais estreita e a inclinação da seção ascendente aumenta.
- 1.2 A seção descendente do arco combinado não é óbvia; portanto, o pequeno arco de corrente é muito estável.
(2) A temperatura do arco é alta, variando de 24.000K a 50.000K, com alta densidade de potência e densidade de energia de 105-106W/cm2. Em contraste, o arco TIG tem uma faixa de temperatura de 10.000-24.000K e uma densidade de potência inferior a 104W/cm2.
(3) A rigidez é alta, com grande fator de concentração de arco.
(4) O calor gerado pela coluna de arco tem um efeito significativo no aquecimento da peça.
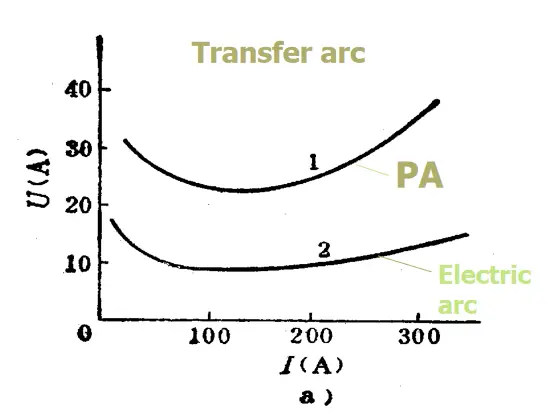
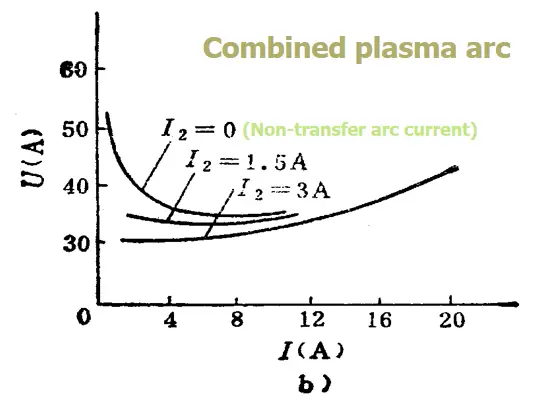
4. Características e aplicações da soldagem a arco plasma
(E) Características
Devido à sua alta densidade de energia, temperatura e rigidez, o arco plasma apresenta as seguintes vantagens em comparação à soldagem a arco convencional:
1) Forte capacidade de penetração, capaz de soldar placas de aço inoxidável com espessura de 8-10mm sem a necessidade de chanfro ou fio de enchimento.
2) A qualidade da costura de solda não é sensível a mudanças no comprimento do arco. Isso ocorre porque o formato do arco é quase cilíndrico e tem boa retilineidade. A variação no comprimento do arco tem impacto mínimo na área do ponto de aquecimento, facilitando a obtenção de formatos uniformes de cordões de solda.
3) O eletrodo de tungstênio é embutido em um bico de cobre resfriado a água, evitando o contato com a peça e evitando a ocorrência de inclusão de tungstênio no metal de solda.
4) O arco plasma possui alto grau de ionização, tornando-o estável mesmo em baixas correntes, permitindo a soldagem de peças de precisão em miniatura.
As desvantagens da soldagem a arco plasma são as seguintes:
1) Espessura de soldagem limitada, geralmente abaixo de 25 mm.
2) A pistola de soldagem e os circuitos de controle são complexos e o bico tem uma vida útil baixa.
3) Existem múltiplos parâmetros de soldagem, exigindo um alto nível de proficiência técnica do operador de soldagem.
(2) Formulários
A soldagem a arco de plasma pode ser usada para soldar vários metais que podem ser soldados com soldagem com gás inerte de tungstênio (TIG), como aço inoxidável, alumínio e ligas de alumínio, titânio e ligas de titânio, níquel, cobre e liga de Monel. Este método de soldagem pode ser aplicado nos setores aeroespacial, aviação, energia nuclear, eletrônica, construção naval e outros setores industriais.
5. Gerador de Arco Plasma
1. Classificação: Pistola de soldagem a arco de plasma, pistola de corte, pistola de pulverização.
2. Componentes
Os componentes principais incluem o eletrodo, o suporte do eletrodo, o bico comprimido, o isolador intermediário, o corpo superior da pistola, o corpo inferior da pistola e a luva de resfriamento. Os componentes mais críticos são o bico e o eletrodo.
1. Bocal
Classificação: Com base no número de furos do bico, existem dois tipos: furo único e furo múltiplo.
Nos bicos multifuros, além do furo central principal, existem vários pequenos furos nos lados esquerdo e direito do furo principal. O gás plasma ejetado desses pequenos orifícios tem um efeito compressivo adicional no arco plasma, fazendo com que a seção transversal do arco plasma se torne elíptica. Quando o longo eixo da elipse é paralelo à direção de soldagem, pode aumentar significativamente a velocidade de soldagem e reduzir a largura da zona afetada pelo calor.
Os parâmetros mais importantes do formato do bico são a abertura de compressão e o comprimento do canal de compressão.
1) Abertura do bico (dn):
O dn determina o diâmetro e a densidade de energia do arco plasma. Um diâmetro menor resulta em maior compressão do arco, mas se for muito pequeno, pode levar à diminuição da estabilidade do arco plasma, causando até mesmo arco duplo e danos ao bico. A seleção de dn deve ser baseada na corrente de soldagem, tipo de gás plasma e vazão.
2) Comprimento do canal do bico (l0):
Sob uma determinada abertura de compressão, um l0 mais longo proporciona uma compressão mais forte do arco plasma. Contudo, se l0 for muito grande, o arco plasma torna-se instável. Geralmente é necessário que a relação l0/dn esteja dentro de um determinado intervalo. Para arco de transferência, geralmente é 1,0-1,2, e para arco misto, é 2-6.
3) Ângulo cônico (α):
O ângulo cônico tem pouco impacto na compressão do arco plasma e pode variar de 30° a 180°. No entanto, é preferível combinar o formato da ponta do eletrodo para garantir a ancoragem estável do ponto anódico na ponta do eletrodo. Durante a soldagem, o ângulo é geralmente de 60° a 90°.
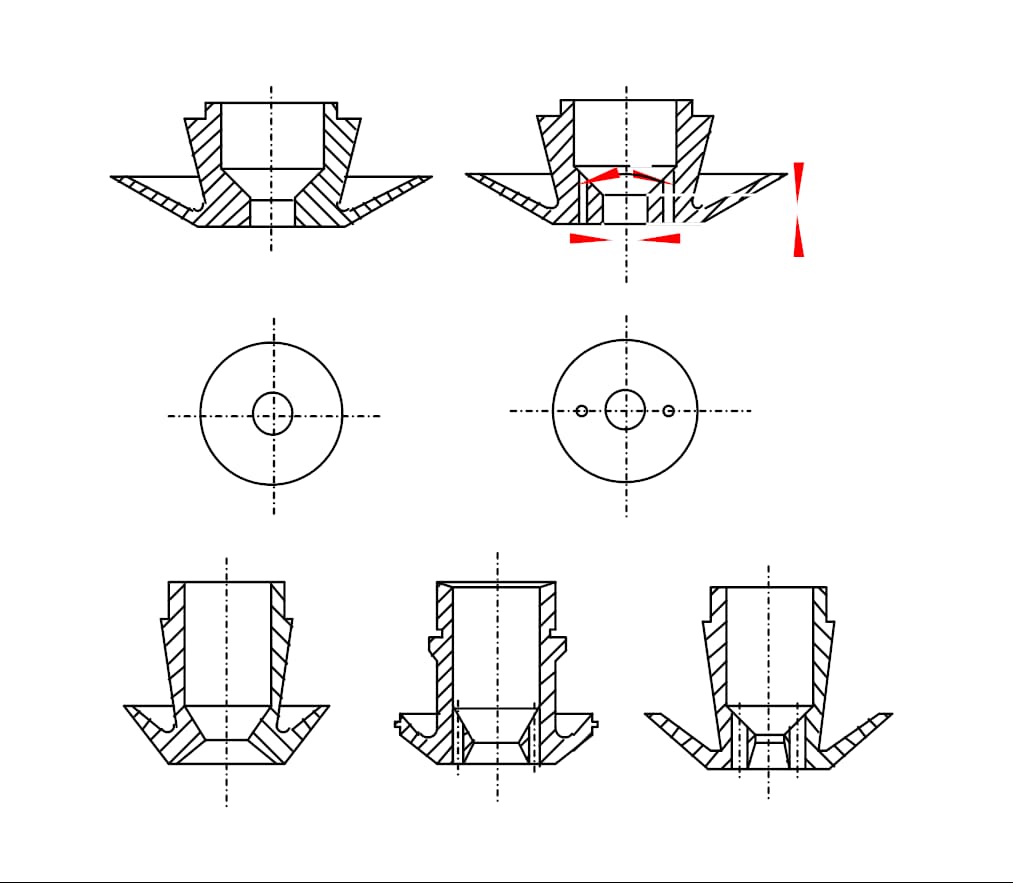
Material do bocal:
O bico é normalmente feito de cobre e é resfriado diretamente com água.
Eletrodo:
1) Materiais:
A soldagem a arco de plasma geralmente usa eletrodos de tungstênio toriados ou eletrodos de tungstênio ceriados. Em alguns casos, podem ser utilizados eletrodos de tungstênio zircônico ou eletrodos de zircônio. Eletrodos de tungstênio geralmente requerem resfriamento com água. Para aplicações de baixa corrente, é utilizado resfriamento indireto com água e o eletrodo de tungstênio tem a forma de uma haste. Para aplicações de alta corrente, é utilizado resfriamento direto com água e o eletrodo de tungstênio possui uma estrutura embutida.
2) Forma:
A ponta de um eletrodo em forma de bastão é geralmente retificada em um formato de cone afiado ou em formato de plataforma cônica. Para aplicações de corrente mais elevada, também pode ser retificado em formato esférico para reduzir a queima.
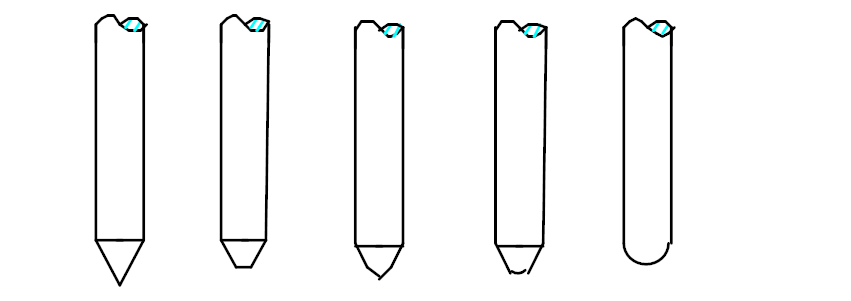
3) Comprimento e concentricidade da contração interna:
Ao contrário da soldagem TIG, na soldagem a plasma, o eletrodo de tungstênio geralmente é contraído dentro do bico comprimido. A distância da superfície externa do bocal até a ponta do eletrodo de tungstênio é conhecida como comprimento de contração interna (lg).
Para garantir a estabilidade do arco e evitar arco duplo, o eletrodo de tungstênio deve ser concêntrico com o bico, e o comprimento de contração interna (lg) do eletrodo de tungstênio deve ser apropriado (lg = l0 ± 0,2 mm).
3. Métodos de entrega de gás:
a) Tangencial: Este método proporciona alta compressão, com baixa pressão no centro e alta pressão na periferia. Ajuda a estabilizar o arco no centro.
b) Radial: Este método proporciona menor compressão em comparação ao método tangencial.
5. Arco Duplo e suas Medidas de Prevenção
1. Arco Duplo
Sob condições normais, um arco transferido é formado entre o eletrodo de tungstênio e a peça de trabalho.
Porém, em certas situações anormais, pode ocorrer um arco paralelo, conhecido como arco duplo, que queima entre o eletrodo de tungstênio e o bico, bem como entre o bico e a peça.
2. Mecanismo de geração de arco duplo
Teoria da quebra do filme de gás frio
3. Causas e medidas de prevenção para geração de arco duplo
1. Sob certas condições atuais, a abertura de compressão do bico é muito pequena ou o comprimento do canal de compressão é muito longo, resultando em comprimento excessivo de contração interna.
2. Fluxo insuficiente de gás plasma.
3. Desvio excessivo entre o eixo do eletrodo de tungstênio e o eixo do bico.
4. Bloqueio do bico devido a respingos de metal.
5. Características externas incorretas da fonte de alimentação.
6. Distância incorreta entre o bico e a peça de trabalho.
2. Soldagem e corte a arco iônico.
1. Processo de soldagem a arco de plasma
Existem três métodos: tipo de perfuração, tipo de fusão e soldagem a arco de plasma por microfeixe.
(1) Soldagem a arco de plasma tipo perfuração
Ao usar uma corrente de soldagem e fluxo de plasma maiores, o arco de plasma tem maior densidade de energia e força de fluxo de plasma. A peça é completamente derretida e forma um pequeno orifício que penetra na peça sob a ação da força do fluxo de plasma, enquanto o metal fundido é expelido ao redor do pequeno orifício.
À medida que o arco de plasma se move na direção da soldagem, o metal fundido se move ao longo das paredes do arco e cristaliza em uma costura de solda atrás da poça de fusão, enquanto o pequeno orifício avança com o arco de plasma.
É adequado para soldagem de um lado e formação de dois lados, e só pode ser usado para soldagem de um lado e formação de dois lados.
Ao soldar peças finas, isso pode ser obtido sem chanfro, placas de preenchimento ou enchimento de metal, obtendo-se formação de dupla face em uma passagem.
A geração de pequenos furos depende da densidade de energia do arco plasma. Quanto mais espessa for a placa, maior será a densidade de energia necessária. Para chapas mais espessas, a soldagem a arco plasma do tipo perfuração só pode ser usada para a primeira costura de solda.
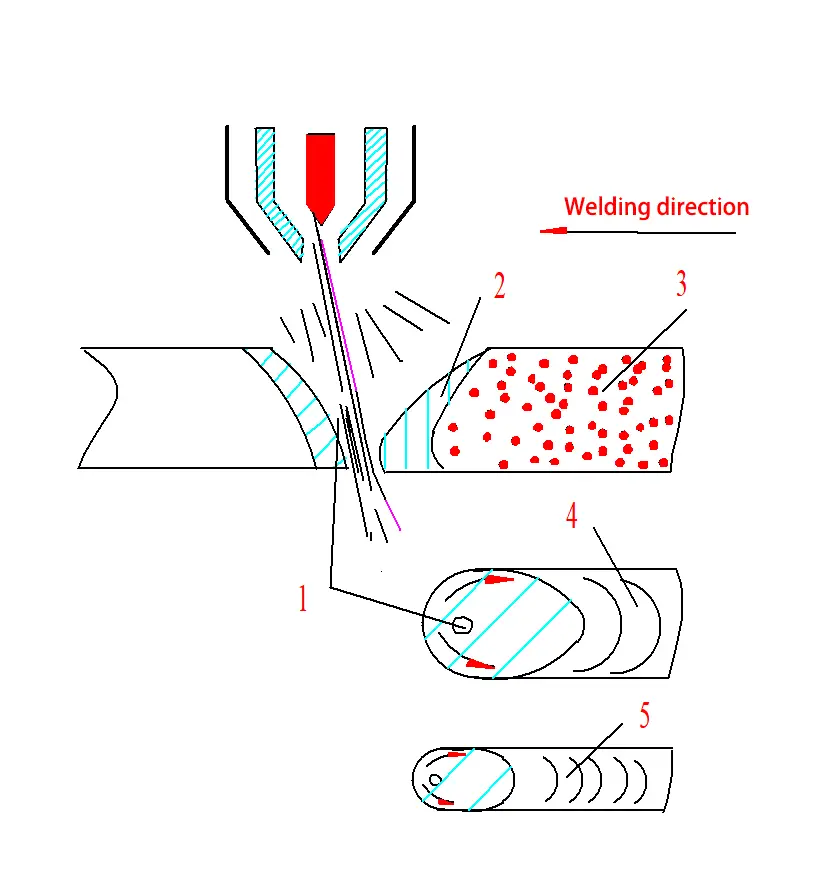
Tabela 6-1: Espessura aplicável para soldagem a arco plasma tipo perfuração
Material | Aço inoxidável | Titânio e ligas de titânio | Níquel e ligas de níquel | Aço de liga leve | Aço de baixo carbono |
Limite de espessura de soldagem /milímetros |
8 | 12 | 6 | 7 | 8 |
(2) Soldagem a arco de plasma tipo fusão
Usando uma taxa de fluxo de gás plasma mais baixa, a força do fluxo de plasma é menor e a capacidade de penetração do arco é baixa.
Características:
- Apenas derrete a peça e não forma pequenos furos, semelhante à soldagem TIG.
- Adequado para soldar placas finas, soldas de cobertura em múltiplas camadas e soldas de canto.
(3) Soldagem a arco plasma de microfeixe
Um processo de soldagem por fusão de baixa corrente (normalmente inferior a 30A).
Características do equipamento:
- Bocal de compressão de pequena abertura (0,6 mm a 1,2 mm).
- Arco combinado. O arco não transferido desempenha o papel de iniciação e manutenção do arco, garantindo que o arco transferido permaneça estável mesmo em correntes muito baixas (tão baixas quanto 0,5A).
Recursos do processo:
- 1) Pode soldar metais mais finos, com espessura soldável mínima de 0,01 mm.
- 2) O arco não atinge o ponto de equilíbrio com uma grande variação no comprimento do arco e o arco permanece colunar.
- 3) Velocidade de soldagem rápida, costura de solda estreita, pequena zona afetada pelo calor e distorção mínima de soldagem.
(4) Soldagem a arco de plasma pulsado
Usa corrente pulsada abaixo de 15 Hz em vez de corrente contínua estável. O arco é mais estável, resultando em uma zona afetada pelo calor (HAZ) menor e menos distorção.
(5) Soldagem a plasma em corrente alternada
Geralmente usa fonte de alimentação de onda quadrada para soldar ligas de alumínio.
(6) Arco de plasma transferido
Na verdade, é uma combinação de arco transferido e arco de plasma, e existem duas formas:
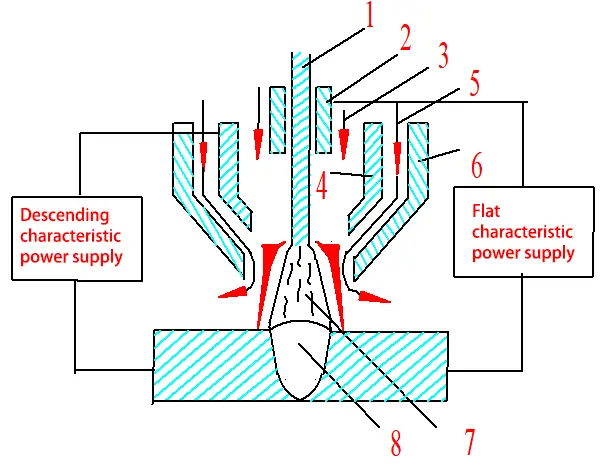
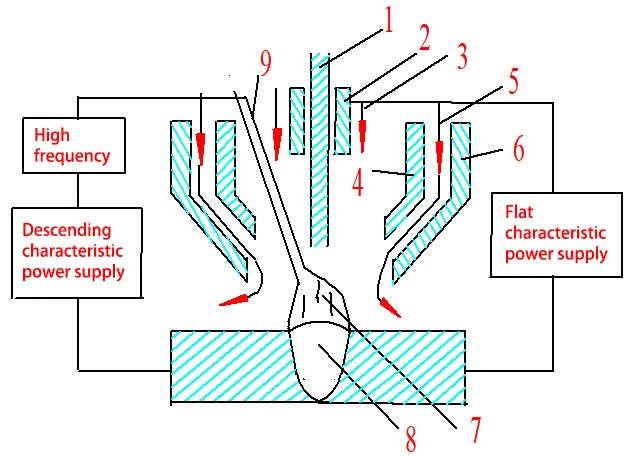
2. Processo e parâmetros de soldagem
(1) Forma de junta e chanfro
A forma da junta é selecionada com base na espessura da placa:
- Quando a espessura está entre 0,05 mm e 1,6 mm, normalmente é utilizada a forma de junta mostrada na figura abaixo, e a soldagem é feita por arco de plasma de microfeixes.
- Quando a espessura da placa é maior que 1,6 mm, mas menor que o material listado na Tabela 6-4, geralmente não é feito nenhum bisel e a soldagem é feita usando o método de perfuração.
- Quando a espessura da placa é maior que o limite da Tabela 6-4, um chanfro em forma de V ou em forma de U é necessário para soldagem multicamadas. Em comparação com a soldagem TIG, podem ser usados chanfros menores e faces de raiz maiores. O valor máximo permitido para a face raiz é igual à espessura máxima de soldagem para o método de perfuração. A primeira camada é soldada pelo método de perfuração e as outras camadas são soldadas pelo método de fusão ou outros métodos de soldagem.
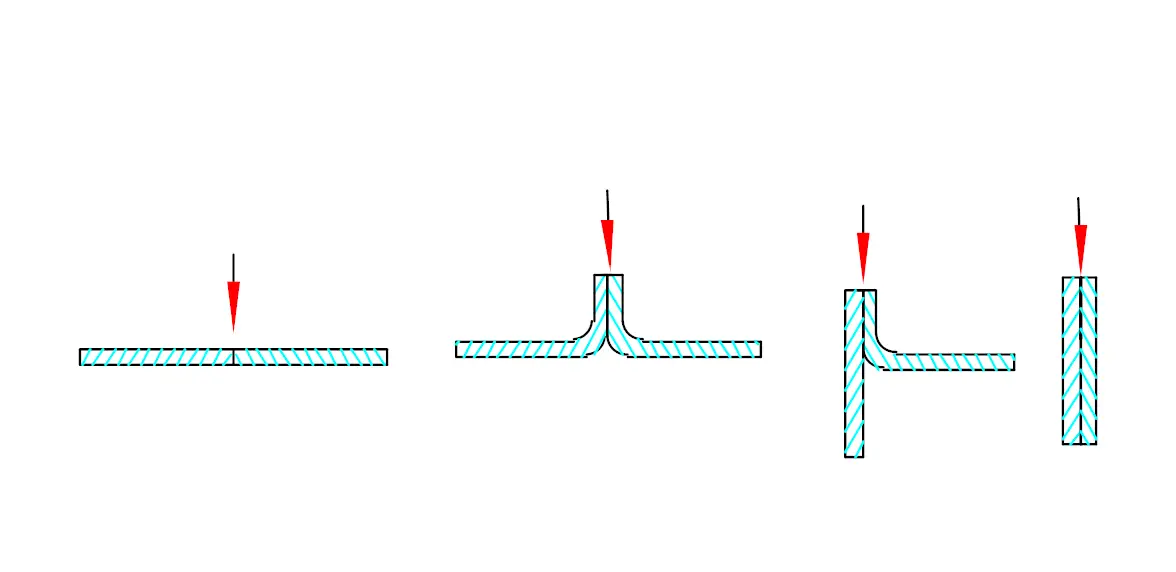
(2) Corrente de soldagem e abertura do bico
A corrente de soldagem é sempre selecionada com base na espessura da placa ou nos requisitos de penetração. Se a corrente for muito baixa, a solda pode não penetrar e nenhum pequeno furo será formado. Se a corrente de soldagem for muito alta, o metal fundido pode cair devido ao grande diâmetro do furo.
A abertura do bico é selecionada com base na corrente de soldagem e deve ser combinada adequadamente. Também está relacionado à vazão do gás plasma.
(3) Gás plasma
O gás de plasma e o gás de proteção são geralmente selecionados com base no metal a ser soldado e na magnitude da corrente. Ao usar altas correntes de soldagem na soldagem a arco de plasma, geralmente é aconselhável usar o mesmo gás para gás de plasma e gás de proteção, pois o uso de gases diferentes pode resultar em baixa estabilidade do arco.
A Tabela 6-5 lista os gases típicos usados para soldagem a arco plasma de alta corrente de vários metais. Para soldagem a arco de plasma de baixa corrente, o gás argônio puro é comumente usado como gás plasma. Isso ocorre porque o gás argônio tem uma tensão de ionização mais baixa, o que garante fácil ignição do arco.
Metal | Espessura/mm | Técnica de soldagem | |
Método de perfuração | Método de fusão | ||
Aço carbono (aço temperado com alumínio) | <3.2 | Ar | Ar |
>3.2 | Ar | 25%Ar+75%Ele | |
Aço de liga leve | <3,2 | Ar | Ar |
>3.2 | Ar | 25%Ar+75%Ele | |
Aço inoxidável | <3,2 | Ar ou 92,5% Ar + 7,5% H2 | Ar |
>3.2 | Ar ou 95% Ar + 5% H2 | 25%Ar+75%Ele | |
>3.2 | Ar ou 95% Ar + 5% H2 | 25%Ar+75%Ele | |
Metais reativos | <6,4 | Ar | Ar |
>6,4 | Ar+(50%-70%)Ele | 25%Ar+75%Ele |
A taxa de fluxo do gás plasma determina diretamente a força do fluxo de plasma e a capacidade de penetração. Quanto maior for a vazão do gás plasma, maior será a capacidade de penetração. No entanto, se a vazão do gás plasma for muito alta, o diâmetro do pequeno furo pode se tornar muito grande, o que pode afetar a formação da solda.
Portanto, é necessário selecionar uma vazão apropriada do gás plasma com base no diâmetro do bico, tipo de gás plasma, corrente de soldagem e velocidade de soldagem.
Ao usar o método de fusão, é necessário reduzir a taxa de fluxo do gás plasma de forma adequada para minimizar a força do fluxo de plasma.
(4) Velocidade de soldagem
A velocidade de soldagem deve ser selecionada com base na vazão do gás plasma e na corrente de soldagem, garantindo que todos os três parâmetros sejam adequadamente combinados. Quando outras condições são constantes, o aumento da velocidade de soldagem reduz o aporte de calor e diminui o diâmetro do pequeno furo até que desapareça.
Entretanto, o aumento excessivo na velocidade de soldagem pode resultar em rebaixamento ou porosidade.
Por outro lado, se a velocidade de soldagem for muito baixa, o metal base poderá superaquecer e o metal fundido poderá cair. Portanto, a velocidade de soldagem, a vazão do gás plasma e a corrente de soldagem devem ser bem combinadas.
(5) Distância do bico à peça de trabalho
Se a distância for muito grande, a capacidade de penetração diminui. Se a distância for muito pequena, poderá causar bloqueio do bico. Geralmente, a distância é definida entre 3 a 8 mm. Em comparação com a soldagem com gás inerte de tungstênio (TIG), a variação na distância do bico tem menos impacto na qualidade da soldagem.
(6) Taxa de fluxo do gás de proteção
A vazão do gás de proteção deve ser selecionada com base na corrente de soldagem e na vazão do gás plasma. Sob uma determinada taxa de fluxo de gás de plasma, uma taxa de fluxo excessiva do gás de proteção pode interromper o fluxo de gás, afetando a estabilidade do arco e a eficácia da proteção.
Por outro lado, uma vazão muito baixa do gás de proteção pode resultar em proteção inadequada. Portanto, a vazão do gás de proteção deve estar em uma proporção apropriada com a vazão do gás plasma.
Para soldagem do tipo perfuração, a vazão do gás de proteção está geralmente na faixa de 15 a 30 L/min.
(7) Iniciação e terminação do arco
Ao usar o método de perfuração para soldar placas espessas, defeitos como porosidade e rebaixamento são propensos a ocorrer nos pontos de iniciação e terminação do arco.
Para juntas de topo, são utilizadas placas de iniciação e terminação de arco. O arco é iniciado primeiro na placa de iniciação, depois transferido para a peça de trabalho e finalmente terminado na placa de terminação, fechando o pequeno orifício.
No entanto, para juntas circunferenciais, as placas de iniciação e terminação do arco não podem ser utilizadas. Em vez disso, um método de aumentar gradualmente a corrente de soldagem e a taxa de fluxo do gás plasma é usado para iniciar o arco na peça de trabalho, e o arco é fechado reduzindo gradualmente a corrente e a taxa de fluxo do gás plasma para fechar o pequeno orifício.
2. Corte por arco de plasma
1. Princípio de corte
Princípio de fusão e sopro: O arco de plasma derrete completamente a peça de trabalho e a força de lavagem mecânica de alta velocidade do fluxo de plasma sopra o metal fundido ou não metálico, formando um corte estreito.
Corte a gás: Utiliza combustão e sopro.
Vantagens:
- 1. Pode cortar qualquer metal: aço, alumínio, tungstênio, cobre, titânio, molibdênio, etc. Pode cortar não metais: como granito, tijolos refratários, concreto, etc.
- 2. Velocidade de corte rápida e alta produtividade.
- 3. Boa qualidade de corte: zona afetada pelo calor (HAZ) pequena e lisa, deformação mínima e o corte é quase vertical.
Desvantagens:
- Carga do equipamento, alta tensão sem carga.
2. Técnicas de corte
1. Gás Plasma
1) Tipos
- Gás argônio: Baixa tensão sem carga (70-80V), mas baixa temperatura do arco, adequado para cortar espessuras inferiores a 30mm.
- Gás nitrogênio: Devido à decomposição endotérmica do gás nitrogênio, o arco é ainda mais comprimido, resultando em uma temperatura de arco mais alta e maior capacidade de transporte de calor, permitindo maior espessura e velocidade de corte. Tensão sem carga superior a 165V.
- Gás nitrogênio + gás hidrogênio: Aumenta ainda mais a temperatura do arco e a capacidade de transporte de calor, permitindo maior espessura e velocidade de corte. Tensão sem carga superior a 300V.
- Gás nitrogênio + gás argônio
- Ar: Baixo custo, alta temperatura do arco devido às reações de oxidação exotérmica, permitindo grandes espessuras de corte e altas velocidades de corte. A qualidade do corte também é boa, mas o eletrodo de tungstênio é propenso à oxidação. Portanto, eletrodos de háfnio-cobre ou eletrodos compostos de zircônio-cobre são frequentemente usados, pois formam uma película de óxido que evita oxidação adicional.
2) Taxa de fluxo
A vazão do gás plasma é muito maior do que a usada na soldagem, pois o arco plasma requer um arco mais duro.
2. Parâmetros do Processo
1) Tensão sem carga:
Não só afeta o desempenho da ignição do arco, mas também influencia a rigidez do arco. Uma tensão sem carga mais alta resulta em um arco mais forte e maior força de descarga, permitindo maior velocidade de corte e espessura.
2) Corrente e tensão do arco:
Aumentar a corrente e a tensão do arco pode aumentar a espessura e a velocidade de corte, com a tensão tendo um efeito mais significativo. No entanto, o aumento da corrente pode levar à formação de um arco duplo e de um corte maior.
3) Velocidade de corte:
Recomenda-se maximizar a velocidade garantindo a penetração completa. Aumentar a velocidade de corte melhora a produtividade e reduz a deformação e a zona afetada pelo calor. Velocidades de corte lentas resultam em menor produtividade, maior risco de formação de escória e maior zona afetada pelo calor.
4) Distância do bico à peça:
Geralmente, é preferida uma distância de 8-10 mm. Aumentar a distância aumenta a potência do arco, mas também leva a uma maior dissipação de calor, menor eficiência do arco, redução da força de descarga e aumento do risco de formação de escória. Também é mais propenso a arcos duplos. Por outro lado, uma distância muito baixa pode resultar no bloqueio do bico.