A fundição é o método mais flexível para a fabricação de peças complexas.
A aplicação de tecnologia avançada de fundição trouxe uma nova vitalidade à indústria manufatureira.
Com o advento de inúmeros programas de software e o rápido desenvolvimento da tecnologia informática, agora é possível fornecer informações precisas e confiáveis para a produção de peças fundidas que atendam aos requisitos em termos de geometria, tamanho e desempenho de serviço.

Cerca de 15% a 20% das peças automotivas são fabricadas utilizando diferentes métodos de fundição, que incluem principalmente componentes-chave do sistema de energia e peças estruturais importantes.
Atualmente, os países desenvolvidos na indústria automotiva empregam tecnologia avançada de produção para peças fundidas de automóveis, resultando em produtos de alta qualidade, eficiência de produção e poluição ambiental mínima.
As matérias-primas e auxiliares utilizadas na fundição foram padronizadas e serializadas, e todo o processo produtivo foi mecanizado, automatizado e inteligente.
À medida que a tecnologia automotiva continua a avançar rapidamente, a tecnologia de moldagem rápida, a tecnologia CAE, a modelagem 3D, a tecnologia CNC e outras tecnologias estão sendo adotadas para fornecer suporte confiável para encurtar o período de preparação da produção de peças fundidas e reduzir o risco de desenvolvimento de novos produtos.
Tecnologia de fundição de automóveis
1. Processo de fundição
A fundição abrange principalmente fundição em areia e fundição especializada.
Fundição em molde de areia comum
A fundição em areia é um processo que utiliza areia como material de molde. É composto por três tipos de moldes: molde de areia úmida, molde de areia seca e molde de areia endurecida quimicamente. É importante ressaltar que nem toda areia pode ser utilizada para fundição.
A vantagem da fundição em areia é o baixo custo, pois a areia utilizada no molde pode ser reaproveitada. No entanto, a produção do molde de fundição pode ser demorada e o próprio molde não pode ser reutilizado. Terminada a fundição, o molde deve ser destruído para a recuperação do produto acabado.
Fundição especial
A fundição especial é ainda categorizada em dois tipos com base nos materiais de moldagem utilizados. O primeiro tipo usa areia mineral natural e pedra como materiais de moldagem primários e inclui métodos como fundição de precisão, fundição em molde de lama, fundição em molde de casca, fundição sob pressão negativa, fundição em molde completo e fundição em molde cerâmico. O segundo tipo de fundição especial utiliza metal como principal material de moldagem e abrange técnicas como fundição em molde de metal, fundição sob pressão, fundição contínua, fundição de baixa pressão e fundição centrífuga.

Fig. 1 Classificação do processo de fundição
Na indústria automotiva, os processos de fundição primária utilizados se enquadram nas duas categorias a seguir:
1.1 Gfundição de ravity (GDC)
A fundição por gravidade, também conhecida como fundição por gravidade, refere-se ao processo em que o metal fundido é derramado em um molde e preenche a cavidade sob a influência da gravidade da Terra.
Nos casos em que o produto final necessita de um espaço oco, um núcleo de areia é colocado dentro da cavidade do molde.
Para garantir o fluxo adequado do metal fundido, o dispositivo de vazamento pode ser inclinado, o que é conhecido como “GDC inclinado”.
A fundição por gravidade abrange várias técnicas, como fundição em molde de areia, fundição em molde de metal, fundição de precisão, fundição de espuma perdida e fundição em molde de lama.
Destas técnicas, a fundição em molde de areia é a mais comumente utilizada na indústria automotiva.
1.1.1 Se fundição
Atualmente, as peças automotivas de ferro fundido mais comumente utilizadas são produzidas por moldagem em areia úmida, principalmente por meio do uso de pressão estática ou moldagem por impacto de ar com fluxo de ar pré-compactado. Este método tem inúmeras vantagens, incluindo baixo consumo de energia, baixo ruído, poluição reduzida, alta eficiência e operação confiável.
Os fabricantes de equipamentos estrangeiros têm melhorado continuamente suas máquinas de moldagem, incorporando vários métodos de melhoria, como compactação por impacto de ar, impacto de ar mais compactação com aumento do fluxo de ar, pressão estática com compactação, compactação multicontato ativa e compactação por extrusão de moldagem para obter um produto mais uniforme. dureza do molde de areia.

Fig. 2 processo de fundição em areia
Com os avanços em componentes semicondutores de alta potência, computadores e tecnologia microeletrônica, servos sistemas elétricos estão sendo usados para substituir acionamentos hidráulicos e pneumáticos em linhas de moldagem, acelerando assim o ritmo de produção e aumentando significativamente a confiabilidade operacional.
Ao mesmo tempo, o sistema de controle hidráulico é significativamente simplificado, reduzindo os requisitos de manutenção.
Usando uma máquina de queda de areia de cano duplo, a peça fundida e o portão podem ser pré-limpos simultaneamente.
O processo de vazamento nas linhas de moldagem pode muitas vezes limitar a taxa geral de produção, portanto, recomenda-se o uso de equipamento de vazamento automático.
Alguns fabricantes utilizam panelas de pressão de ar e técnicas de vazamento por contato para economizar ferro fundido, manter a qualidade e proteger a caixa de areia.
No processo de vazamento, a inoculação em fluxo é comumente usada e alguns empregam uma combinação de inoculação no molde e filtração.
No processo de fundição, diferentes fábricas utilizam métodos diferentes para a produção de núcleos de areia. A caixa de núcleo frio, caixa de núcleo quente ou núcleo de casca podem ser utilizadas dependendo das condições.
Núcleos de areia, como núcleo de areia do cárter, cilindro, núcleo de areia superior e núcleo de areia frontal das faces dianteira e traseira, geralmente são feitos com a caixa de núcleo frio para garantir precisão dimensional e economizar energia.
A caixa de núcleo frio está se tornando cada vez mais popular.
O núcleo frio é produzido principalmente usando o método de endurecimento de trietilamina com cura ISO, e um método avançado conhecido como ISO Max foi desenvolvido nos Estados Unidos.
Para melhorar a qualidade da superfície interna e a limpeza da cavidade interna da peça fundida, são utilizados revestimentos à base de água em vez de revestimentos à base de álcool para evitar poluição.
A secagem por microondas após o revestimento é um método altamente eficiente e que economiza energia, e a qualidade do núcleo de areia produzido é melhor do que a obtida através da secagem tradicional com gás ou gás natural.
O processo KCY-CORE é empregado, onde furos de processo são abertos no núcleo de areia para preenchimento e solidificação secundária da areia, resultando na integração de múltiplos núcleos de areia em um núcleo de areia combinado. O núcleo de areia combinado é então revestido e seco, melhorando significativamente a precisão dimensional da peça fundida com um erro dimensional geral inferior a 0,3 mm.
O sistema de moldagem de areia inclui equipamento de separação magnética de areia antiga, equipamento de britagem de bloco de areia, equipamento de triagem e equipamento de resfriamento de areia antiga para garantir a qualidade da areia velha reciclada.
Areia nova, pó de carvão, bentonita e outros materiais adicionados são alimentados de forma precisa e quantitativa no sistema de acordo com uma proporção predeterminada, e a adição de água é ajustada em tempo real com base em dados de controle para manter o desempenho da areia de moldagem.
Há também um controle de circuito fechado em tempo real do desempenho da areia de moldagem de todo o sistema ou um sistema especializado on-line para controlar a qualidade da areia de moldagem.
Ressalta-se que o sistema de areia de moldagem possui grande rotatividade e forte inércia, portanto o ajuste do desempenho da areia de moldagem deve ser baseado na tendência, com medidas previsíveis tomadas para garantir a estabilidade da qualidade da areia de moldagem.
As peças fundidas comuns incluem: bloco do motor, cabeçote, caixa de câmbio, coletor de admissão, etc.
1.2 Dou seja, elenco
Quando a peça fundida necessária tem uma seção transversal complexa ou paredes finas em áreas específicas (como mostrado na Figura 3), a gravidade por si só pode não ser suficiente para garantir que o metal fundido preencha completamente a cavidade do molde.
Nestes casos, pode-se aplicar pressão ao líquido metálico para garantir o preenchimento completo da cavidade do molde.
Isto pode ser conseguido através de fundição sob pressão de alta pressão (HPDC) ou fundição sob pressão de baixa pressão (LPDC).
As peças fundidas produzidas pelo processo HPDC apresentam boa consistência dimensional e tolerâncias semelhantes, em torno de +/- 0,2 mm, o que não pode ser alcançado por fundição por gravidade (GDC) ou mesmo fundição sob pressão (LPDC).
Com o rápido avanço da tecnologia automotiva, a tecnologia de fundição sob pressão de alta pressão tornou-se um foco na fundição automotiva.

Fig.3 peças complexas de paredes finas
1.2.1 Fundição de alta pressão
A fundição de alta pressão é um processo em que o metal líquido ou semilíquido é rapidamente injetado em um molde sob alta pressão, solidificando e cristalizando sob pressão para formar a peça fundida.
O processo de fundição de alta pressão pode ser dividido em três etapas: fechamento do molde, injeção e ejeção.

Fig. 4 Fluxo do processo de fundição de alta pressão
No processo de fundição sob pressão, os parâmetros de injeção têm um grande impacto na porosidade das peças fundidas sob pressão e devem ser ajustados adequadamente.
Usando um sistema fechado de controle de tempo de término da injeção, é possível obter fundição sob pressão sem rebarbas.
A qualidade das peças fundidas pode ser verificada através da detecção de falhas por raios X e testes ultrassônicos.
A fundição a vácuo e a fundição sob pressão com oxigênio, que são baseadas na tecnologia de fundição de alta pressão, visam eliminar defeitos de fundição, melhorar a qualidade interna e expandir a aplicação da fundição sob pressão.
A fundição por compressão envolve o enchimento e solidificação do fundido sob pressão, oferecendo estabilidade, redução de respingos de metal, perda mínima de oxidação do metal fundido, economia de energia, operação segura e redução de defeitos nos furos de fundição.
Este processo tem sido amplamente utilizado no desenvolvimento e aplicação de peças fundidas de liga de alumínio de alto desempenho, como chassis auxiliares de liga de alumínio.
Fundição a vácuo
Para minimizar ou eliminar a porosidade nas peças fundidas causada pela rápida mistura do gás com o metal fundido durante o processo de fundição sob pressão, é comum utilizar a fundição a vácuo do molde antes da fundição sob pressão.
Com base no grau de vácuo na câmara de pressão e na cavidade, a fundição sob pressão a vácuo pode ser dividida em fundição sob pressão a vácuo regular e fundição sob pressão a alto vácuo.

Fig. 5 fluxograma do processo de fundição sob pressão a vácuo
A chave para a fundição sob pressão de alto vácuo é atingir um alto nível de vácuo em um curto espaço de tempo.
A Figura 6 mostra o diagrama do princípio de funcionamento da máquina de fundição sob pressão de alto vácuo do tipo sucção.
Ele usa vácuo para atrair o líquido metálico para a câmara de pressão e, em seguida, injeta-o rapidamente para atingir um alto grau de vácuo no processo de fundição sob pressão.
O princípio da fundição sob pressão de alto vácuo envolve bombear o ar de toda a câmara de pressão e cavidade através de um tubo de vácuo antes da fundição sob pressão.
O processo de bombeamento a vácuo deve ser concluído o mais rápido possível, criando uma grande diferença de pressão entre o líquido metálico no cadinho e a câmara de pressão, fazendo com que o líquido metálico flua para a câmara de pressão através do riser de líquido e, em seguida, o punção de injeção de pressão começa a aplicar pressão para injeção.

Fig. 6 Máquina de fundição sob pressão de alto vácuo e sucção
Fundição sob pressão cheia de oxigênio
A fundição sob pressão cheia de oxigênio envolve o enchimento de oxigênio seco na câmara de pressão e na cavidade do molde de fundição sob pressão para substituir o ar e outros gases presentes.
O processo de fundição sob pressão cheia de oxigênio é mostrado na Figura 7.
Este método de fundição só é aplicável a ligas de alumínio.
Quando o líquido da liga de alumínio é injetado na câmara de pressão e na cavidade do molde de fundição, ele reage com o oxigênio para formar Al2Ó3o que resulta em partículas pequenas e uniformemente distribuídas de Al2O3 (com diâmetro inferior a 1um), reduzindo ou eliminando a porosidade e melhorando a compactação da peça fundida.
Essas pequenas partículas ficam dispersas por toda a peça fundida, representando cerca de 0,1% a 0,2% da massa total e não afetam a usinagem.

Fig. 7 Diagrama esquemático de fundição sob pressão cheia de oxigênio
2. Equipamento de fundição
Os equipamentos utilizados na indústria de fundição automotiva devem ser rápidos, eficientes e confiáveis, capazes de operar continuamente.
Dados os rigorosos padrões de qualidade para peças fundidas de automóveis, estas máquinas de fundição também devem possuir alta precisão.
Alguns dos principais equipamentos de fundição incluem: máquinas de moldagem, misturadores de areia, máquinas de fabricação de machos, equipamentos de moldagem, equipamentos de extração de pó, fornos de fundição, máquinas de fundição sob pressão, ferramentas de usinagem, máquinas de jateamento, máquinas de limpeza e equipamentos de teste.
Em particular, destacam-se a máquina de fundição sob pressão e o forno de fundição.
2.1 Sforno de fusão
O forno de fundição emprega fonte de alimentação de média frequência para estabelecer um campo magnético de média frequência, induzindo assim uma corrente parasita dentro do material ferromagnético e gerando calor, atingindo assim o objetivo de aquecer o material.
O forno elétrico de média frequência utiliza uma fonte de alimentação de média frequência de 200-2500 Hz para aquecimento por indução, fusão e manutenção de temperatura.
Este forno de fundição é usado principalmente para fundir aço carbono, ligas de aço e aços especiais, bem como para fundir e aumentar a temperatura de metais não ferrosos, como cobre e alumínio.
Leitura relacionada: Metais Ferrosos vs Não Ferrosos
O equipamento é compacto, leve e altamente eficiente, com baixo consumo de energia, rápidas velocidades de fusão e aquecimento, fácil controle de temperatura e alta eficiência de produção.
O conjunto completo de equipamentos do forno de fundição consiste em um gabinete de energia de frequência intermediária, capacitor de compensação, dois corpos do forno, cabos resfriados a água e um redutor.
O corpo do forno consiste em quatro partes: a carcaça do forno, a bobina de indução, o revestimento do forno e a engrenagem de redução de inclinação.
A carcaça do forno é feita de materiais não magnéticos.
A bobina de indução é um cilindro espiral construído a partir de tubos retangulares ocos, através dos quais a água de resfriamento circula durante o processo de fundição. A barra de cobre que sai da bobina é conectada ao cabo resfriado a água.
O revestimento do forno, localizado próximo à bobina de indução, é feito de areia de quartzo.
A inclinação do corpo do forno é realizada pela rotação direta da engrenagem redutora de inclinação.
Esta engrenagem apresenta uma mudança de velocidade da turbina em dois estágios e oferece rotação confiável e estável com excelente desempenho de travamento automático. No caso de uma falha de energia, o mecanismo de inclinação irá parar automaticamente para evitar qualquer perigo potencial.
Os motores das engrenagens de redução de inclinação de ambos os fornos podem ser controlados através da chave de seleção do forno, com uma caixa de distribuição e fio de borracha de quatro núcleos, permitindo que o operador fique em um local conveniente enquanto controla a inclinação e o reajuste do corpo do forno.
Atualmente, muitas fábricas de fundição permanecem num estado industrial 2.0 e necessitam urgentemente de atualizações no que diz respeito à proteção ambiental, automação, inteligência e segurança.
Com o advento da Indústria 4.0, todos os parâmetros de fundição serão registrados através de sensores capazes de funcionar em ambientes com temperaturas extremamente altas.
Dados como o nível de enchimento do forno de aquecimento e o nível de poluição na poça de fusão se tornarão informações cruciais para a construção de um forno de fundição inteligente e em rede.
No futuro, uma fábrica de fornos de fundição poderá utilizar um robô para operações de limpeza.
O robô terá acesso a todos os parâmetros do forno e poderá tomar medidas imediatas antes que a poluição atinja níveis críticos.
2.2 Dou seja, máquina de fundição
A máquina de fundição sob pressão é uma máquina que utiliza fundição sob pressão. É composto por uma câmara de compressão a quente e uma câmara de compressão a frio, sendo ainda dividido em dois tipos: reto e horizontal.
Sob a pressão da máquina de fundição sob pressão, o metal fundido é injetado hidraulicamente no molde, onde esfria e solidifica.
Após a abertura do molde, uma peça fundida de metal sólido pode ser recuperada.
A máquina de fundição sob pressão é composta por um mecanismo de fixação, mecanismo de injeção, sistema hidráulico e sistema de controle elétrico.
Além disso, a máquina também inclui vários componentes e bases, dispositivos auxiliares e outras peças.

Fig. 8 estrutura básica da máquina de fundição sob pressão
Nos últimos 30 anos, a máquina de fundição sob pressão passou por avanços significativos em termos de tamanho, automação, modularidade e flexibilidade.
Nos últimos tempos, a integração e a redução do peso da fundição sob pressão automotiva geraram requisitos novos e mais elevados para máquinas de fundição sob pressão, sendo a tecnologia de conformação integrada à carroceria um tema particularmente quente.
Isto colocou as máquinas de fundição sob pressão para serviços pesados na vanguarda da inovação. Por exemplo, a Tesla comprou recentemente uma máquina de fundição sob pressão de 8.000 toneladas da empresa italiana DRA, que é 30% maior do que a máquina de fundição sob pressão de 6.000 toneladas usada no Modelo Y.
Prevejo que esse recorde será continuamente quebrado à medida que a indústria evolui.
Vamos examinar por que as máquinas de fundição sob pressão para serviços pesados são o futuro da indústria e quais vantagens elas oferecem.
Vantagem 1: Vantagem de custo de formação de material de estação única
A Figura 9 mostra a estrutura do quadro Tesla Model Y. O componente amarelo representa uma grande parte integrada da carroceria traseira e do arco da roda no topo da torre do eixo traseiro.
Com a ajuda de uma máquina de fundição sob pressão de grande escala, este componente complexo que normalmente requer múltiplas estações e processos pode ser concluído em uma única operação.
Como resultado, oferece uma vantagem de custo significativa.
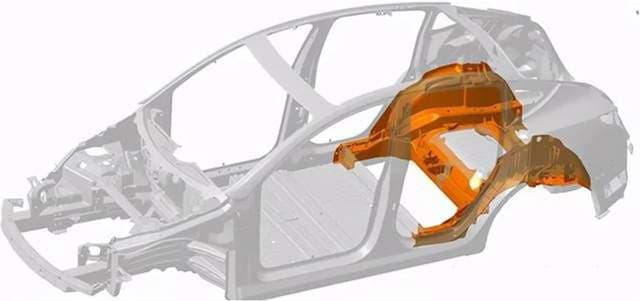
Fig. 9 diagrama estrutural do quadro modelo Y
Vantagem 2: Integração de Estamparia e Soldagem e Otimização do Ritmo Geral de Produção
A Tesla pretende tornar-se o Toyota ou Volkswagen da nova indústria energética, tornando o ritmo de produção um factor crítico.
Para aumentar o ritmo da máquina de fundição sob pressão de 8.000 toneladas, a tecnologia pode ser utilizada para criar uma cavidade entre os meios-filmes fundidos em ambos os lados durante o processo de vedação sob pressão das peças fundidas e para injetar metal fundido com proteção de temperatura no cavidade.
Como a cavidade está em estado de pressão negativa, ela elimina efetivamente as bolhas de ar geradas pela turbulência de fundição, contribuindo para a consistência do material e a velocidade de fundição durante a fundição sob pressão.
De acordo com os dados da Tesla, cada operação de fundição envolve a injeção de cerca de 80 kg de líquido de liga de alumínio no molde da câmara fria a uma velocidade de 10 metros por segundo.
O tempo do ciclo de produção é de cerca de 85 segundos, com uma taxa de produção de 42 peças por hora, representando uma otimização do tempo de ciclo atual.
No entanto, estas vantagens são acompanhadas por alguns desafios, tais como a mecânica do exercício e o design de moldes, que terão de ser abordados à medida que a indústria continua a desenvolver máquinas de fundição sob pressão em grande escala.
3. Materiais de fundição
3.1 Cbloco de cilindro
Tradicionalmente, o material utilizado nos blocos de motores automotivos era o ferro fundido, que ainda hoje detém uma posição dominante na indústria.
No entanto, com a melhoria contínua do desempenho do motor e a procura por redução de peso, o material do bloco do motor está a sofrer rápidas inovações.
Existem três áreas principais de desenvolvimento:
- Melhorar a qualidade do ferro fundido para aumentar a resistência e o desempenho do cilindro.
- Utilizando ferro fundido de grafite vermicular para produzir blocos de cilindros de motor, que oferecem maior resistência e melhor desempenho à fadiga, suportam projetos de paredes finas, suportam maior pressão de ruptura, reduzem a deformação do cilindro e aumentam a potência em 10% a 20%.
- Blocos de cilindros de liga de alumínio, que estão se desenvolvendo rapidamente e representam a direção principal para blocos de cilindros de automóveis de passageiros.
Geralmente, o uso de liga de alumínio é favorecido para redução de peso e consumo de energia dos veículos.
No entanto, as limitações de resistência e desempenho à fadiga térmica da liga de alumínio dificultam sua aplicação em blocos de motores de alta potência e seu custo é relativamente alto.
3.2 Ccabeça do cilindro
A cabeça do cilindro do motor é uma importante área de aplicação para ligas de alumínio, especialmente no mercado de cabeças de cilindro para automóveis de passageiros, que é amplamente dominado por materiais de liga de alumínio.
No mercado de caminhões, o uso de ferro fundido para cabeçotes de motores de alta potência é raro, e cabeçotes de ferro vermicular tornaram-se a opção preferencial, capaz de resolver o problema de trincas em cabeçotes de ferro fundido cinzento.
3.3 Ceixo de classificação
A aplicação da tecnologia de sobrealimentação de motores é um processo crítico na melhoria do desempenho dos automóveis para eficiência energética e redução de emissões.
Seja para motores a gasolina ou a diesel, principalmente no mercado de caminhões, o uso de Virabrequins de Ferro Nodular Pearlite, amplamente utilizados no passado, não atende aos requisitos devido ao aumento da pressão de explosão do motor, e foram substituídos por materiais de aço forjado como 40Cr.
No entanto, com os avanços em tecnologias como laminação de filetes e endurecimento por indução de virabrequins de ferro nodular Pearlite, os virabrequins de ferro nodular continuam a deter uma participação de mercado significativa nos mercados de automóveis de passageiros e caminhões com motor de potência média-baixa.
Além disso, virabrequins de motores feitos de ferro dúctil temperado isotermicamente também foram estudados no país e no exterior.
3.4 Óoutros
Outras peças fundidas automotivas, como peças de suporte e componentes estruturais de motores e chassis, incluindo vários suportes, discos, carcaças e peças de direção, são feitas de materiais de ferro fundido para atender aos requisitos de desempenho.
À medida que os requisitos de proteção ambiental automotiva continuam a evoluir, o uso de ferro fundido cinzento e aço fundido está diminuindo gradualmente, enquanto ferro dúctil de alto desempenho, liga de magnésio, liga de alumínio e materiais especiais de ferro fundido estão se tornando cada vez mais predominantes.
3.5 Dtendência de desenvolvimento
Atualmente, o ferro fundido é o principal material utilizado em peças fundidas automotivas. Em particular, o uso de ferro dúctil substituiu muitas peças fundidas de aço e ferro cinzento, e o uso de ferro maleável em peças automotivas diminuiu. Sua resistência e tenacidade superiores, bem como facilidade de produção, aumentaram sua aplicação.
A pesquisa e o desenvolvimento de ferro dúctil de alta resistência e tenacidade serão fundamentais para seu uso contínuo na indústria. Outro material promissor, o ferro dúctil temperado isotermicamente, possui excelentes propriedades mecânicas e tem visto rápido desenvolvimento e aplicação bem-sucedida no exterior, principalmente na produção de virabrequins, engrenagens, suportes e peças estruturais.
O ferro fundido de grafite vermicular, inventado em 1948, tem uma faixa de produção estreita e desempenho limitado, portanto seu uso tem sido limitado. No entanto, com os avanços na tecnologia de controle de produção, o ferro fundido de grafite vermicular pode ter futuro na produção de peças fundidas complexas. Possui maior resistência à tração, módulo de elasticidade e resistência à fadiga do que o ferro fundido e o alumínio, tornando-o um material ideal para blocos e cabeçotes de cilindros de motores.
A tendência de redução do peso dos veículos levou ao uso de ligas de magnésio e alumínio em peças fundidas automotivas. Por cada 10% de redução no peso do veículo, o consumo de combustível é reduzido em 5,5% e as emissões são reduzidas em cerca de 10%. As ligas de alumínio têm densidade mais leve (1/3 do ferro) e resistência equivalente à do ferro fundido cinzento, o que as torna ideais para a fabricação de blocos e cabeçotes de motores.
As ligas de alumínio tiveram um rápido crescimento nos últimos anos e as ligas de magnésio, com sua densidade mais leve, foram aplicadas em volantes de automóveis, estruturas de assentos, painéis de instrumentos, tampas e outras peças, à medida que a pesquisa e a aplicação continuam a avançar.
Direção de desenvolvimento de fundição de automóveis
1. Direção de desenvolvimento de peças fundidas
Projeto integrado de peças fundidas automotivas
Com as crescentes exigências de eficiência energética e proteção ambiental na indústria automóvel, bem como a necessidade de reduzir custos de produção, os benefícios da moldagem por fundição estão a ser aproveitados para alcançar a integração de peças através de design e estrutura otimizados. Isso envolve a combinação de diversas peças formadas por estampagem, soldagem, forjamento e fundição, o que resulta na redução do peso das peças e em menos etapas de processamento, resultando em componentes mais leves e de alto desempenho.
A tendência de integração da fundição na indústria automotiva é particularmente pronunciada na fundição de ligas não ferrosas.
Para utilizar plenamente o processo de fundição para a produção de peças fundidas estruturais complexas, tem havido um aumento no uso de peças fundidas de alta pressão com design integrado, como painéis internos de portas, molduras de assentos, molduras de painéis de instrumentos, molduras frontais e firewalls. .
Essas peças fundidas são significativamente maiores em tamanho em comparação com as produzidas atualmente e requerem uma máquina de fundição sob pressão de 4.000 a 5.000 toneladas ou até maior para produção.

Fig. 10 Corpo fundido integrado Tesla Model Y
Leveza de peças fundidas automotivas
Para melhorar o desempenho de potência, reduzir o consumo de combustível e diminuir a poluição dos gases de escape, mantendo ao mesmo tempo a resistência e a segurança do veículo, é importante minimizar ao máximo o peso total do veículo.
Por cada redução de 100 kg na tara do veículo, o consumo de combustível por 100 km pode ser reduzido em 0,3 a 0,6 litros.
Uma redução de 10% no peso do veículo pode resultar num aumento de 6% a 8% na eficiência de combustível.
Devido às crescentes preocupações com a proteção ambiental e a conservação de energia, a redução de peso tornou-se uma tendência na indústria automóvel global, com as peças fundidas de automóveis leves a tornarem-se uma direção de desenvolvimento crucial.
A realização da redução de peso será alcançada principalmente através dos três pontos seguintes:
1) Design leve
Uma das principais desvantagens do projeto de espessura igual é que ele não consegue explorar totalmente o desempenho estrutural e leva a um aumento no peso da peça fundida.
Para otimizar o projeto de peças e componentes, são empregados análise CAE, otimização topológica e outros métodos para que os valores de tensão de cada peça sejam equalizados, resultando em uma espessura de parede inconsistente. A espessura do material das peças com baixa tensão é reduzida para diminuir o peso da peça.
A moldagem por fundição tem a vantagem de produzir peças fundidas estruturais complexas e várias seções transversais irregulares. Durante o processo de projeto, CAE ou otimização topológica é usada para analisar a tensão dos componentes.
Com base na distribuição de forças, são determinadas a forma das peças e a espessura específica do material local. O peso das peças pode ser reduzido significativamente através de reforço, abertura de buracos e alteração da seção.
2) Aplicação de materiais de liga leve
O uso de materiais de liga leve, como alumínio e magnésio, é a principal medida de redução de peso adotada pelos fabricantes de automóveis em todo o mundo.
O alumínio tem uma densidade que é apenas um terço da do aço e possui excelente resistência à corrosão e ductilidade. O magnésio tem uma densidade ainda mais baixa, apenas dois terços da do alumínio, e possui excelente fluidez sob condições de fundição de alta pressão.
Tanto o alumínio como o magnésio têm uma elevada resistência específica (a relação entre resistência e massa), o que os torna cruciais para reduzir o peso do veículo e melhorar a eficiência do combustível.
No entanto, vale ressaltar que o custo das matérias-primas para ligas leves, como alumínio e magnésio, é significativamente superior ao dos materiais siderúrgicos, o que limita sua aplicação mais ampla na indústria automotiva.
Apesar do alto custo da matéria-prima, o uso de peças fundidas de magnésio e alumínio em cada veículo continua a aumentar ano após ano. Por um lado, este aumento de custos é compensado pelos avanços tecnológicos e, por outro lado, a concorrência no mercado está a forçar os fabricantes de automóveis a reduzirem as suas margens e a adoptarem mais ligas leves.
No entanto, o desenvolvimento de tecnologia de conformação avançada é fundamental para aumentar significativamente o uso de ligas leves e reduzir o custo dos lingotes de magnésio e alumínio.
3) Alto desempenho de materiais de fundição
Melhorar o desempenho dos materiais e permitir que as peças suportem cargas maiores por unidade de peso é um dos métodos eficazes para reduzir o peso das peças fundidas.
As peças fundidas estruturais de suporte constituem uma parcela significativa das peças fundidas automotivas, tornando o desenvolvimento de suas peças fundidas um foco principal.
Através de tratamento térmico e outras técnicas, a microestrutura do material pode ser alterada para melhorar a resistência, rigidez ou tenacidade das peças e reduzir efetivamente o seu peso.
O ferro dúctil temperado isotermicamente tem maior resistência do que o aço fundido comum e menor densidade. Sua densidade é 7,1 g/cm3enquanto o do aço fundido é de 7,8 g/cm3. Este material tem sido amplamente recomendado nos últimos anos.
Ao adotar ferro dúctil temperado isotermicamente, as peças fundidas podem ser 10% mais leves que as peças fundidas de aço do mesmo tamanho.
Tabela 1 Efeito de leveza da substituição de material de ferro dúctil temperado isotermicamente
Peças de reposição | Peso de ferro dúctil temperado isotermicamente (kg) | Peso em aço fundido/kg | Taxa de redução de peso /% |
Cruz superior da suspensão dianteira | 10h25 | 25 | 59,00 |
Cruzeta inferior da suspensão dianteira | 32,46 | 64 | 49,28 |
Suporte superior da mola da suspensão dianteira | 21h28 | 34,6 | 38,50 |
Suporte inferior da mola da suspensão traseira | 20,74 | 33.16 | 37,45 |
Travessa inferior da suspensão traseira | 9h32 | 50.16 | 84,58 |
Em termos de peças fundidas em ligas de alumínio e magnésio, materiais de alta resistência e tenacidade também são usados como substitutos.
Com base na redução de peso alcançada com as ligas leves originais, o uso de materiais de alto desempenho leva a uma maior redução de peso.
Por exemplo, a General Motors nos Estados Unidos usa a liga AE44 de alto desempenho para substituir a liga de alumínio original e emprega fundição de alta pressão para produzir a estrutura. Isto resulta numa redução de peso adicional de 6 kg, além da redução de peso obtida com a liga de alumínio.
Desenvolvimento digital de peças fundidas automotivas
A integração do desenvolvimento de fundição de automóveis e da tecnologia digital aumenta muito o nível da tecnologia de fundição e encurta o ciclo de design do produto e de produção de protótipos.
Atualmente, a tecnologia de fabricação digital é amplamente utilizada no desenvolvimento de peças fundidas automotivas.
Durante o estágio de projeto de estruturas e processos de fundição, softwares de design 3D como Pro/E, CATIA e UG são comumente usados, e algumas empresas de fundição avançadas implementaram projetos sem papel.
Softwares como Magma, ProCAST e Huazhu CAE são utilizados para simular o processo de solidificação, microestrutura, segregação de componentes e propriedades de materiais de peças fundidas automotivas. Essas simulações também incluem o campo de velocidade, campo de concentração, campo de temperatura, campo de fase e campo de tensão no processo de fundição, permitindo um esquema de processo otimizado antes da produção em massa.
Para acompanhar o ritmo acelerado de desenvolvimento de peças fundidas automotivas, a Rapid Prototyping Technology (RP) é amplamente utilizada para prototipagem rápida de peças fundidas automotivas com base em design e desenvolvimento CAD/CAE.
Os dados CAD/CAE originais são usados para criar um protótipo de fundição ou protótipo de molde por meio de empilhamento camada por camada por meio de ligação, fusão ou sinterização. O primeiro pode ser usado para amostras de fundição de protótipos por meio de microfusão ou fundição de gesso, enquanto o último pode ser usado como molde para fabricação de núcleos de areia e vazamento de fundição por meio de moldagem de montagem de núcleo.
Além disso, o método de sinterização a laser de pó (SLS) pode ser utilizado para produzir diretamente núcleos de areia e moldes para a produção experimental de peças fundidas.
Para moldes externos com uma estrutura relativamente simples, uma máquina-ferramenta CNC também pode ser usada para processamento de came com plástico usinável para obter a caixa de núcleo e o padrão necessários para a produção experimental de fundição, ou o bloco de areia pode ser processado diretamente para produzir o molde de areia para o molde externo.
Em geral, a tecnologia digital permeia o projeto, o desenvolvimento e a produção experimental de peças fundidas, resultando em uma melhoria significativa na velocidade e eficiência do desenvolvimento de peças fundidas.
Atualmente, o principal desafio é que as tecnologias digitais para projeto, análise e fabricação rápida são separadas. A conversão de dados de uma etapa para outra ainda exige muito trabalho tedioso.
No futuro, espera-se que uma plataforma unificada de interface de dados para as tecnologias digitais aplicadas em cada estágio do desenvolvimento de fundição possa ser desenvolvida, um padrão padronizado de conversão de dados possa ser estabelecido e uma conversão de dados contínua entre diferentes softwares possa ser alcançada, melhorando ainda mais a velocidade de desenvolvimento do elenco.
2. Direção de desenvolvimento da tecnologia de fundição de automóveis
Tecnologia de produção de fundição de estrutura complexa de parede fina
À medida que a indústria automóvel evolui e a necessidade de eficiência energética e redução de emissões aumenta, as peças dos automóveis tornam-se cada vez mais leves.
Alcançar leveza por meio de um design de paredes finas é uma direção crucial de desenvolvimento para blocos de motores.
O design de parede fina de 3 mm do bloco de cilindros impõe requisitos rigorosos para a fabricação e montagem do núcleo na montagem do núcleo e no processo de fundição vertical.
O centro de fabricação de núcleos pode alcançar alta inteligência e automação na produção de núcleos.
Todo o processo, desde a adição de areia bruta e resina até a mistura de areia, fabricação de machos, reparo de machos, montagem, revestimento, secagem, moldagem, montagem de machos e rebaixamento, pode ser altamente automatizado, garantindo qualidade estável de fabricação de machos e montagem. , precisão dimensional e qualidade de secagem do revestimento, evitando assim riscos de qualidade e dimensionais causados por fatores humanos e atendendo às necessidades de produção de núcleos de cilindros em grande escala.
Isso resolve efetivamente o problema da taxa de desperdício instável e alta durante a produção em massa.
Além disso, a melhoria na precisão dimensional do núcleo de areia reduz bastante a carga de trabalho e o custo de limpeza, garantindo efetivamente o requisito de espessura de parede de 3 mm.
Tecnologia de fabricação de grandes peças estruturais de liga de alumínio e magnésio
A fundição estrutural em larga escala de liga de alumínio e magnésio tornou-se uma tendência crucial em resposta à crescente demanda por eficiência energética, proteção ambiental e redução de custos em componentes. Sua tecnologia de fabricação também se tornou um ponto focal do desenvolvimento atual.
Atualmente, os principais métodos de produção de peças estruturais de liga de alumínio e magnésio em grande escala incluem fundição de alta pressão, fundição por compressão e fundição de baixa pressão.
A fundição de alta pressão é o processo de produção dominante devido à sua alta eficiência e excelente qualidade do produto.
Os esforços para melhorar a tecnologia de fabricação de peças estruturais de liga de alumínio e magnésio em grande escala concentram-se principalmente na redução do aprisionamento de ar durante a fundição de alta pressão, minimizando a formação de bolsas de ar e abordando problemas de tratamento térmico.
Uma solução para o problema de aprisionamento de ar é a fundição sob pressão de alto vácuo, que pode efetivamente impedir a formação de bolsas de ar.
Esta tecnologia de fundição sob pressão a vácuo foi aplicada com sucesso na produção em massa de peças fundidas estruturais automotivas, fornecendo técnicas e processos avançados de conformação para a produção de peças fundidas de liga leve de alta qualidade.
Tecnologia de fundição de precisão para peças fundidas
Com o avanço da tecnologia de fundição de automóveis, a moldagem de precisão de fundição tornou-se um método de fundição popular. As peças fundidas produzidas através deste método podem ser utilizadas sem muito corte ou mesmo sem corte algum.
Nos últimos anos, o desenvolvimento da tecnologia de moldagem de precisão de fundição tem sido rápido devido a melhorias na precisão dimensional das peças fundidas. Vários métodos de formação de fundição surgiram, incluindo fundição em areia de precisão, fundição de espuma perdida, fundição sob pressão controlável e fundição sob pressão.
Para eliminar defeitos de fundição, melhorar a qualidade interna e expandir a aplicação de fundição sob pressão, vários métodos de processo foram desenvolvidos com base na tecnologia de fundição de alta pressão, como fundição a vácuo, fundição sob pressão cheia de oxigênio, matriz reológica ou tixotrópica de metal semissólido. fundição.
A fundição por compressão, na qual o fundido é preenchido e solidificado sob pressão, é amplamente utilizada na produção de peças fundidas de liga de alumínio de alto desempenho, como chassis auxiliares de liga de alumínio. A fundição por compressão tem as vantagens de estabilidade, sem respingos de metal, redução da perda de oxidação do metal fundido, eficiência energética, operação segura e redução de defeitos nos furos de fundição.
A crescente demanda pela produção de automóveis exige que as peças fundidas sejam de alta qualidade, excelente desempenho, formato quase final, múltiplas variedades, baixo consumo e baixo custo. As peças fundidas representam cerca de 15% a 20% de um veículo completo, o que significa que a indústria de fundição deve adotar continuamente novas tecnologias e materiais para melhorar o nível geral de fundição.
A tecnologia de fundição de precisão atende aos requisitos de peças fundidas automotivas e sua aplicação abrangerá diversos processos de produção de peças fundidas automotivas.