I. Remoção de Resíduos
Depois de soldar a peça de trabalho, se forem utilizadas soldaduras a gás ou varetas de soldadura fluxadas, é necessário limpar imediatamente o fluxo residual e a escória da soldadura e da área circundante antes de realizar a inspeção visual e os testes não destrutivos.
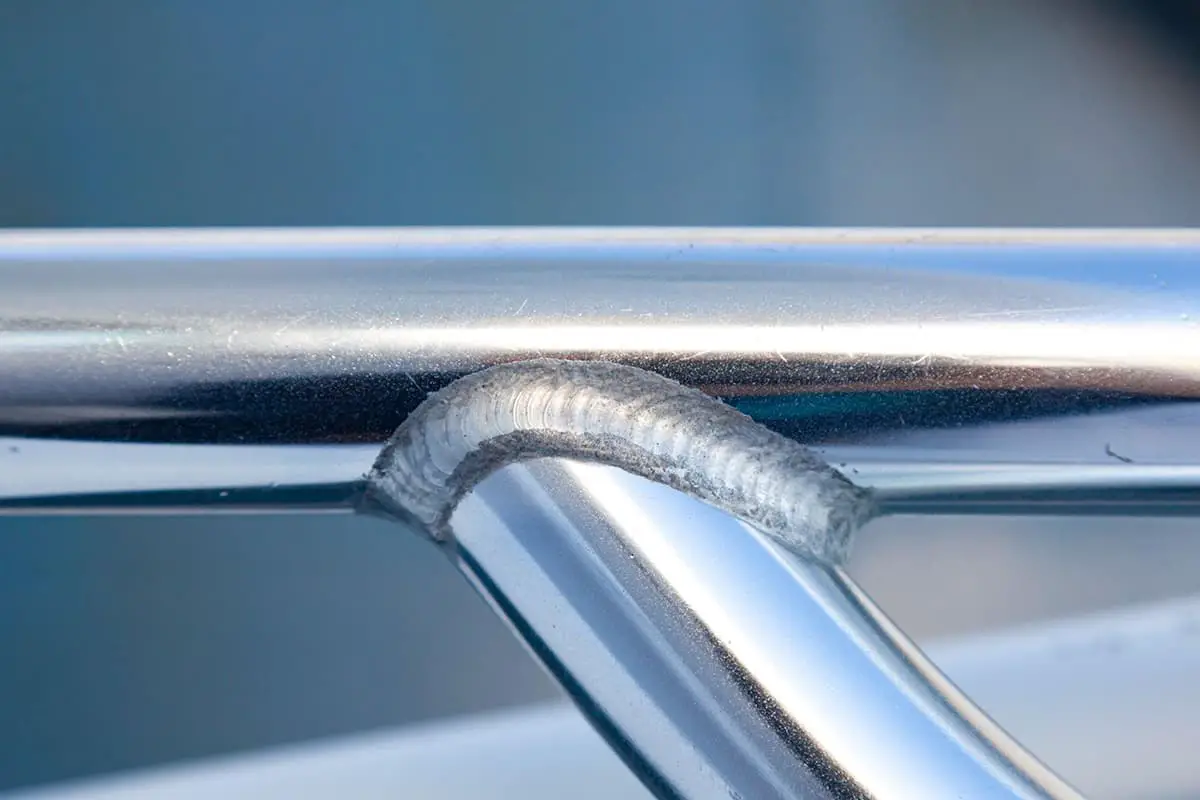
Esta etapa evita a corrosão da solda e de sua superfície por escória e fluxo residual, evitando consequências indesejáveis. Os métodos comuns para limpeza pós-soldagem são os seguintes:
(1) Esfregar em água quente entre 60°C e 80°C;
(2) Imersão em dicromato de potássio (K2Cr2O2) ou anidrido crômico 2% a 3% (Cr2O2);
(3) Enxágue adicional em água quente entre 60°C e 80°C;
(4) Secagem em estufa ou ao ar.
Para testar a eficácia da remoção do fluxo residual, água destilada pode ser colocada na solda da peça de trabalho. A água destilada é então coletada e colocada em um tubo de ensaio contendo uma solução de ácido nítrico a 5%. Se aparecer um precipitado branco, indica que o fluxo residual não foi totalmente removido.
II. Tratamento de Superfície de Soldagens
Através do processo de soldagem adequado e técnicas de operação corretas, a superfície das soldas de alumínio e ligas de alumínio após a soldagem apresenta uma aparência uniforme, sem ondulações e lisa.
A anodização, principalmente quando combinada com técnicas de polimento e tingimento, resulta em superfícies decorativas de alta qualidade. A zona afetada pelo calor da soldagem pode ser minimizada, reduzindo ao mínimo as alterações de cor induzidas pela anodização. Processos rápidos de soldagem podem reduzir significativamente a zona afetada pelo calor. Conseqüentemente, a qualidade do tratamento de anodização em costuras soldadas por flash é boa.
Especialmente para peças de soldagem de ligas que não podem ser tratadas termicamente para reforço no estado recozido, o contraste de cor entre a base metálica e a zona afetada pelo calor é mínimo após a anodização. A brasagem por forno e por imersão, que não envolve aquecimento localizado, produz uma aparência de cor metálica muito uniforme.
As ligas que podem ser tratadas termicamente para reforço, frequentemente utilizadas em peças estruturais de edifícios, são frequentemente anodizadas após a soldagem. Nessas ligas, o calor da soldagem forma precipitados nos elementos da liga.
Após a anodização, aparecerão diferenças entre a zona afetada pelo calor e a costura de solda. Estas zonas de halo próximas à área de soldagem podem ser minimizadas por soldagem rápida ou pelo uso de blocos de resfriamento e placas de fixação. Estas zonas halo, antes da anodização e após a soldagem, podem ser eliminadas através do tratamento de endurecimento por precipitação.
No tratamento químico de peças soldadas, podem ocorrer diferenças significativas de cor entre o metal de solda e o metal base. Isto exige uma seleção cuidadosa da composição do metal de adição, especialmente quando contém silício, o que pode afetar a correspondência de cores.
Se necessário, a solda pode ser polida mecanicamente. Os métodos comuns de polimento mecânico incluem polimento, retificação, jateamento abrasivo e jateamento. O polimento mecânico melhora a superfície das peças de alumínio por meio de métodos físicos, como retificação, rebarbação, polimento, polimento ou jato de areia. O objetivo é atingir a qualidade superficial desejada com o menor número de etapas possível.
No entanto, o alumínio e suas ligas são metais macios com elevados coeficientes de atrito. O superaquecimento durante o processo de retificação pode potencialmente causar a deformação das peças soldadas ou até mesmo levar a fraturas nos limites dos grãos do metal base. Portanto, é necessária lubrificação suficiente durante o processo de polimento e a pressão na superfície do metal deve ser minimizada.
III. Tratamento térmico pós-soldagem
O objetivo do tratamento térmico pós-soldagem é melhorar a estrutura e o desempenho da junta soldada ou eliminar tensões residuais. As ligas de alumínio tratáveis termicamente podem passar por tratamento térmico pós-soldagem, restaurando a resistência da zona afetada pelo calor do metal base próximo à sua resistência original.
Geralmente, o ponto de falha na junta ocorre dentro da zona de fusão da solda. Após o tratamento térmico pós-soldagem, a resistência adquirida pelo metal de solda depende principalmente do metal de adição disperso.
1. Características da soldagem de alumínio e ligas de alumínio
(1) O alumínio oxida facilmente ao ar e durante a soldagem, formando óxido de alumínio (Al2O3) que possui alto ponto de fusão e é extremamente estável, dificultando sua remoção. Isto impede a fusão e fusão do material original. A grande gravidade específica do filme de óxido impede que ele flutue na superfície, resultando em defeitos como inclusões de escória, falta de fusão e penetração incompleta.
A película de óxido superficial do alumínio e sua umidade absorvida podem causar porosidade na costura de solda. Antes da soldagem, deve-se realizar uma limpeza rigorosa da superfície utilizando métodos químicos ou mecânicos para remover a película de óxido. A proteção deve ser reforçada durante a soldagem para evitar oxidação.
Durante a soldagem com gás inerte de tungstênio (TIG), uma fonte de energia de corrente alternada deve ser usada para remover o filme de óxido através de “limpeza catódica”. Na soldagem a gás, deve-se usar um fluxo que remova a película de óxido. Durante a soldagem de chapas grossas, o calor de soldagem pode ser aumentado. Por exemplo, o arco de hélio tem alto calor, então use proteção de gás misto de hélio ou argônio-hélio, ou soldagem por arco de gás metálico de grande diâmetro (GMAW) com corrente contínua positiva, o que elimina a necessidade de “limpeza catódica”.
(2) A condutividade térmica e o calor específico do alumínio e suas ligas são mais que o dobro dos do aço carbono e do aço de baixa liga. A condutividade térmica do alumínio é dezenas de vezes maior que a do aço inoxidável austenítico.
Durante o processo de soldagem, uma grande quantidade de calor pode ser rapidamente transferida para o metal base, portanto, ao soldar o alumínio e suas ligas, além da energia consumida na fusão da poça metálica, mais calor é desperdiçado em outras partes do metal. Este desperdício de energia é mais significativo do que na soldagem de aço. Para obter juntas soldadas de alta qualidade, fontes de energia concentradas e de alta potência devem ser utilizadas tanto quanto possível. O pré-aquecimento e outras medidas de processo também podem ser utilizados.
(3) O coeficiente de expansão linear do alumínio e suas ligas é aproximadamente duas vezes maior que o do aço carbono e do aço de baixa liga. O alumínio exibe retração volumétrica significativa durante a solidificação, causando deformação e tensão substanciais na soldagem. Assim, medidas para evitar a deformação da soldagem devem ser empregadas. A solidificação de uma poça de soldagem de alumínio tende a resultar em cavidades de contração, porosidade, trincas a quente e alta tensão interna.
Para evitar a ocorrência de trincas a quente, a produção pode ajustar a composição do fio de soldagem e o processo de soldagem. Em situações resistentes à corrosão, o fio de soldagem de liga de alumínio-silício pode ser usado para soldar ligas de alumínio, excluindo ligas de alumínio-magnésio.
Nas ligas de alumínio-silício, a tendência à trinca a quente é considerável quando o teor de silício é de 0,5%. À medida que o teor de silício aumenta, a faixa de temperatura de cristalização da liga diminui, sua fluidez melhora significativamente e sua taxa de encolhimento diminui, reduzindo consequentemente a tendência à trinca a quente.
De acordo com a experiência de produção, quando o teor de silício é de 5% a 6%, não ocorre trinca a quente, portanto, o uso de fio SAlSi (com teor de silício de 4,5% a 6%) proporciona melhor resistência à trinca.
(4) O alumínio tem forte refletividade para luz e calor. Durante a transição do estado sólido para o líquido, não há mudança perceptível de cor, tornando difícil avaliar durante o processo de soldagem. O alumínio de alta temperatura tem resistência muito baixa, dificultando o suporte da poça de fusão e sujeito a queimaduras.
(5) O alumínio e suas ligas podem dissolver uma quantidade significativa de hidrogênio no estado líquido, mas dificilmente algum no estado sólido. Durante a solidificação e resfriamento rápido da poça de soldagem, o hidrogênio não tem tempo de escapar, levando à formação de porosidade de hidrogênio.
A umidade na atmosfera do arco, nos materiais de soldagem e na umidade adsorvida na película de óxido da superfície do material original são fontes significativas de hidrogênio na costura de solda. Portanto, é necessário um controle rigoroso sobre as fontes de hidrogênio para evitar a formação de porosidade.
(6) Os elementos de liga tendem a evaporar e queimar, reduzindo o desempenho da costura de solda.
(7) Se o metal base do material original for endurecido por deformação ou tratado termicamente por solução, o calor da soldagem pode reduzir a resistência da zona afetada pelo calor.
(8) O alumínio, tendo uma rede cúbica de face centrada e sem formas alotrópicas, não sofre transição de fase durante o aquecimento e o resfriamento. Isto leva a grãos grossos na solda, que não podem ser refinados através de transições de fase.
2. Métodos de soldagem
Quase todos os métodos de soldagem podem ser usados para soldar alumínio e suas ligas. Contudo, a adaptabilidade do alumínio e suas ligas a diferentes métodos de soldagem varia, e cada método tem suas próprias aplicações.
A soldagem a gás e a soldagem a arco de metal blindado são simples e convenientes. A soldagem a gás pode ser usada para reparos de costuras em chapas de alumínio e peças fundidas onde os requisitos de qualidade não são altos. A soldagem a arco de metal blindado pode ser usada para reparo de peças fundidas de liga de alumínio.
A soldagem com proteção de gás inerte (TIG ou MIG) é o método mais amplamente utilizado para soldagem de alumínio e suas ligas. Folhas de alumínio e ligas de alumínio podem ser soldadas usando soldagem com gás inerte de tungstênio de corrente alternada ou soldagem com gás inerte de tungstênio pulsado.
Placas de alumínio e liga de alumínio podem ser soldadas usando soldagem a arco de hélio e tungstênio, soldagem com gás inerte de tungstênio com mistura de argônio-hélio, soldagem com gás inerte de metal e soldagem com gás inerte de metal pulsado. A aplicação de soldagem com gás inerte de metal e soldagem com gás inerte de metal pulsado está se tornando cada vez mais difundida (argônio ou mistura de argônio/hélio).
3. Materiais de soldagem
(1) Fio de soldagem
Além de considerar o bom desempenho do processo de soldagem, a seleção de fios de soldagem de alumínio e ligas de alumínio deve garantir que a resistência à tração e a plasticidade (por meio de testes de flexão) das juntas de topo atendam aos requisitos especificados de acordo com os requisitos da embarcação.
Os requisitos de resistência ao impacto devem ser atendidos para ligas de alumínio-magnésio com teor de magnésio superior a 3%. Para vasos com requisitos de resistência à corrosão, a resistência à corrosão da junta soldada deve atingir ou estar próxima do nível do material de base. Portanto, a seleção do fio de soldagem é baseada principalmente nas propriedades do alumínio.
1) A pureza do fio de soldagem de alumínio puro geralmente não é inferior à do material original;
2) A composição química do fio de soldagem de liga de alumínio é geralmente semelhante ou próxima à do material original;
3) O conteúdo de elementos resistentes à corrosão (magnésio, manganês, silício, etc.) no fio de soldagem de liga de alumínio geralmente não é inferior ao do material original;
4) Ao soldar diferentes tipos de materiais de alumínio, escolha o fio de soldagem com base no material original mais resistente à corrosão e mais forte;
5) Ligas de alumínio de alta resistência (ligas de alumínio reforçadas com tratamento térmico) que não requerem resistência à corrosão podem usar fios de soldagem de diferentes composições, como fios de soldagem de liga de alumínio-silício resistentes a trincas como SAlSi-1 (observe que a resistência pode ser inferior ao material original).
(2) Gás de Proteção
O gás de proteção é argônio, hélio ou uma mistura destes. Para soldagem TIG de alta frequência em corrente alternada, use mais de 99,9% de argônio puro. A soldagem com polaridade positiva em corrente contínua é adequada para hélio.
Na soldagem MIG, recomenda-se o uso de argônio com adição de 50% a 75% de hélio quando a espessura da placa for de 75 mm. O argônio deve atender aos requisitos de GB/T 4842-1995 “Pure Argon”. A pressão do cilindro de argônio é insuficiente e não pode ser usada quando estiver abaixo de 0,5 MPa.
(3) Eletrodos de tungstênio
Quatro tipos de eletrodos de tungstênio são usados na soldagem a arco de argônio: tungstênio puro, tungstênio toriado, tungstênio de cério e tungstênio de zircônio. Os eletrodos de tungstênio puro têm altos pontos de fusão e ebulição, tornando-os menos propensos a fusão, evaporação, queima do eletrodo e contaminação da ponta.
No entanto, eles têm uma menor capacidade de emissão de elétrons. Os eletrodos de tungstênio toriado, feitos pela adição de 1% a 2% de óxido de tório ao tungstênio puro, possuem maior capacidade de emissão de elétrons, permitem maior densidade de corrente e mantêm um arco mais estável. No entanto, o tório é ligeiramente radioativo, portanto devem ser tomadas medidas de proteção adequadas durante o uso.
Os eletrodos de cério e tungstênio são feitos adicionando 1,8% a 2,2% de óxido de cério (com impurezas ≤0,1%) ao tungstênio puro. Esses eletrodos possuem baixa função de trabalho eletrônico, alta estabilidade química, permitem alta densidade de corrente e não possuem radioatividade. Eles são os eletrodos mais usados atualmente.
Eletrodos de zircônio e tungstênio podem evitar a contaminação do eletrodo do metal base. Suas pontas são fáceis de manter em formato hemisférico, tornando-as adequadas para soldagem AC.
(4) Fluxo
O fluxo utilizado na soldagem a gás consiste em cloretos e fluoretos de elementos como potássio, sódio, lítio e cálcio, que podem remover a película de óxido.
4. Preparação antes da soldagem
(1) Limpeza pré-soldagem
Antes de soldar o alumínio e suas ligas, é fundamental remover rigorosamente a película de óxido e a graxa da linha de soldagem da peça e da superfície do fio de soldagem.
A qualidade dessa limpeza afeta diretamente o processo de soldagem e a qualidade da junta, como a tendência de gerar porosidade na solda e diversas propriedades mecânicas. Essa limpeza normalmente é obtida usando métodos de limpeza química ou mecânica.
1) Limpeza Química
A limpeza química é altamente eficiente e de qualidade consistente, tornando-a adequada para a limpeza de fios de soldagem e peças de pequeno porte produzidas em massa. Submersão e esfregação são dois métodos comuns.
Solventes orgânicos como acetona, gasolina e querosene são usados para desengorduramento de superfície, seguido de lavagem alcalina usando uma solução de NaOH de 5% a 10% a 40°C a 70°C por 3 a 7 minutos (mais tempo para alumínio puro, mas não excedendo 20 minutos), depois enxaguar com água corrente.
Posteriormente, é realizada uma lavagem ácida com solução de HNO3 a 30%, em temperatura ambiente até 60°C, por 1 a 3 minutos, seguida de outro enxágue com água corrente e secagem com ar ou fogo baixo.
2) Limpeza Mecânica
A limpeza mecânica é frequentemente usada quando a peça de trabalho é grande, o ciclo de produção é longo, a soldagem multicamadas está envolvida ou quando a peça de trabalho é recontaminada após a limpeza química.
Primeiro, solventes orgânicos como acetona ou gasolina são usados para desengordurar a superfície, seguido de escovação com uma escova de cobre ou aço inoxidável de 0,15 mm a 0,2 mm de diâmetro até que um brilho metálico seja revelado.
O uso de rebolos ou lixa comum geralmente é desencorajado para evitar que grãos de areia permaneçam na superfície do metal, o que poderia entrar na poça de fusão durante a soldagem e causar inclusões de escória ou outros defeitos. Alternativamente, raspadores ou limas podem ser usados para limpar a superfície a ser soldada.
Após a limpeza da peça e do fio de soldagem, um filme de óxido reaparecerá durante o armazenamento, principalmente em ambientes úmidos ou contaminados por vapores ácidos ou básicos, onde o filme de óxido cresce ainda mais rápido.
Portanto, o tempo de armazenamento desde o final da limpeza até o início da soldagem deve ser minimizado. Em condições úmidas, a soldagem geralmente deve ser realizada dentro de 4 horas após a limpeza. Se o tempo de armazenamento após a limpeza for muito longo (por exemplo, exceder 24 horas), o processo de limpeza deverá ser repetido.
(2) Placa de apoio
O alumínio e suas ligas apresentam baixa resistência sob altas temperaturas, e o alumínio fundido flui facilmente, levando ao colapso potencial do metal de solda durante a soldagem. Para garantir a penetração completa sem colapso, placas de apoio são frequentemente usadas para apoiar a poça de fusão e o metal adjacente.
As placas de apoio podem ser feitas de grafite, aço inoxidável, aço carbono, placas de cobre ou barras de cobre. Uma ranhura curva é feita na superfície da placa de apoio para garantir a formação da solda no verso.
Alternativamente, a soldagem unilateral com formação bilateral pode ser realizada sem placa de apoio, mas isso requer operações de soldagem qualificadas ou a aplicação de medidas de processo avançadas, como controle de feedback automático rigoroso da energia de soldagem.
(3) Pré-aquecimento antes da soldagem
Peças finas e pequenas de alumínio geralmente não requerem pré-aquecimento. O pré-aquecimento pode ser realizado para espessuras entre 10 mm a 15 mm, com temperaturas variando de 100°C a 200°C dependendo do tipo de liga de alumínio.
Técnicas como chamas de oxiacetileno, fornos elétricos ou maçaricos podem ser usadas para aquecimento. O pré-aquecimento ajuda a minimizar a deformação da soldagem e a reduzir defeitos como porosidade.
5. Tratamento Pós-Soldagem
(1) Limpeza Pós-Soldagem
O fluxo de soldagem residual e a escória deixada sobre e perto da solda podem danificar o filme de passivação na superfície do alumínio e podem até mesmo corroer as peças de alumínio, exigindo assim uma limpeza completa. Para peças de formato simples com requisitos gerais, podem ser usados métodos de limpeza simples, como enxágue com água quente ou escovação a vapor.
Para peças de alumínio de formato complexo e de alta demanda, após escovar em água quente com uma escova dura, elas devem ser embebidas em uma solução aquosa de ácido crômico ou solução de dicromato de potássio com concentração de 2-3% a aproximadamente 60°C-80°C por 5 -10 minutos, seguido de esfrega com uma escova dura.
Em seguida, devem ser enxaguados em água quente e secos em estufa ou com ar quente. A secagem natural também é aceitável.
(2) Tratamento térmico pós-soldagem
Geralmente, o tratamento térmico não é necessário após a soldagem de recipientes de alumínio. No entanto, se o material de alumínio em uso apresentar sensibilidade significativa à corrosão sob tensão sob as condições do meio em contato com o recipiente, é necessário passar por tratamento térmico pós-soldagem para eliminar altas tensões de soldagem, reduzindo assim a tensão no recipiente para abaixo do limite para fissuração por corrosão sob tensão.
Este requisito deve ser especialmente indicado nos documentos de projeto do recipiente antes que o tratamento térmico de alívio de tensões seja realizado após a soldagem. Se for necessário tratamento térmico de recozimento pós-soldagem, a temperatura recomendada para alumínio puro, 5052, 5086, 5154, 5454, 5A02, 5A03, 5A06, etc., é 345°C; para 2014, 2024, 3003, 3004, 5056, 5083, 5456, 6061, 6063, 2A12, 2A24, 3A21, etc., é 415 ℃; para 2017, 2A11, 6A02, etc., é 360 ℃.
Dependendo do tamanho e dos requisitos da peça de trabalho, a temperatura de recozimento pode ser ajustada para cima ou para baixo em 20°C-30°C, enquanto o tempo de manutenção pode variar de 0,5 a 2 horas.