1. Prefácio
A nitretação a gás tem diversas vantagens sobre a nitretação iônica, incluindo facilidade de operação, alta repetibilidade do processo, estrutura de equipamento simples e capacidade de obter controle automático do processo.
Um dos benefícios mais significativos da nitretação a gás é a melhoria da temperatura e da uniformidade da atmosfera durante o processo.
Em particular, a profundidade da camada de nitretação na raiz do dente e no círculo primitivo de engrenagens de módulos pequenos é mais uniforme durante a nitretação a gás em comparação com a nitretação iônica.
Nos últimos anos, o processo de nitretação a gás tem visto avanços significativos, como o desenvolvimento de processos de pré-oxidação e nitretação a gás e várias outras técnicas de nitretação a gás.
Esses avanços reduziram o tempo do ciclo de produção entre a nitretação iônica e a nitretação gasosa em vários graus.
No entanto, é essencial prestar atenção a possíveis problemas durante o processo de controle da atmosfera durante a nitretação das engrenagens.
2. Limpeza antes da nitretação a gás
Antes de passar pela nitretação e carga a gás, a engrenagem deve ser cuidadosamente limpa para garantir que não haja água ou impurezas presentes.
Se esta etapa não for concluída corretamente, a superfície nitretada resultante poderá ter uma aparência irregular e poderão aparecer manchas escuras.
Embora não haja diferença significativa na profundidade da camada nitretada, na dureza ou na estrutura metalográfica entre as áreas manchadas e as áreas normais, essas manchas podem impactar significativamente a qualidade geral da aparência da engrenagem.
A macromorfologia dessas áreas pontilhadas irregulares foi analisada usando um estereomicroscópio de ultraprofundidade de campo (como visto na Figura 1).
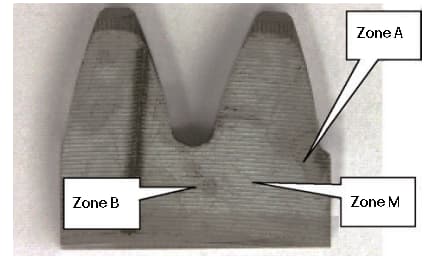
Fig. 1 macro morfologia da área de manchas da face da extremidade da engrenagem
A morfologia microscópica da área manchada foi analisada utilizando um microscópio eletrônico de varredura (como visto na Figura 2). As áreas que pareciam brancas a olho nu foram observadas ao microscópio eletrônico de varredura.
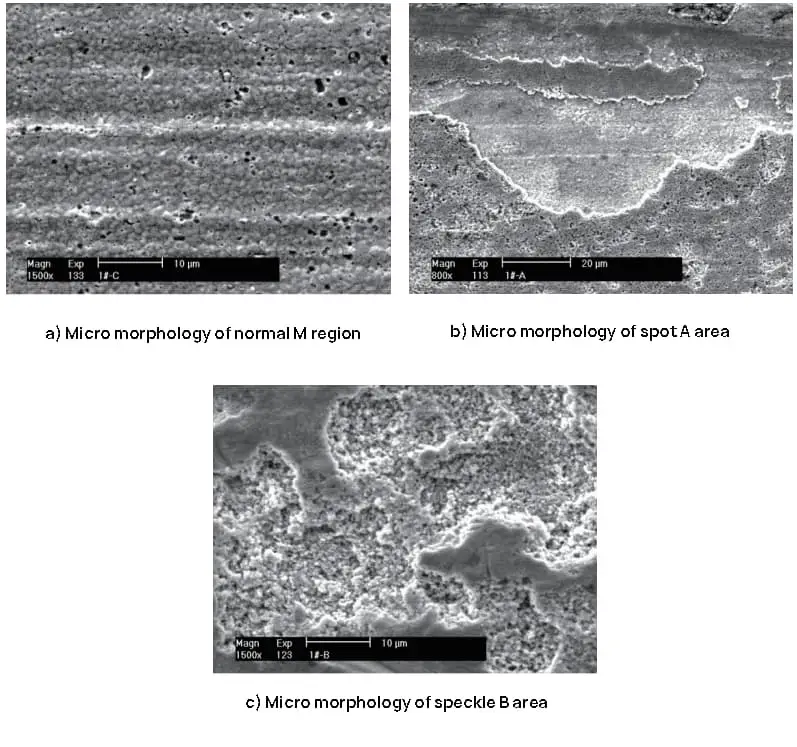
Fig. 2 micromorfologia da área de manchas da face da extremidade da engrenagem
A composição química da área manchada com aparência anormal na face final da engrenagem foi comparada e analisada com a área normal na face final da engrenagem. Os resultados dessa comparação são apresentados na Tabela 1.
Tabela 1 resultados de comparação (fração mássica) (%) da determinação da composição química na microárea da face final da engrenagem
Local de detecção: | C | N | Ó | N / D | Al | Si | P | S | C | K | Ca | Cr | Mn | Fé | |
Zona M | Superfície normal | 0,22 | 0,98 | – | – | – | 0,26 | – | – | – | – | – | 0,19 | 0,63 | 97,72 |
0,21 | 0,99 | – | – | – | 0,24 | – | – | – | – | – | 0,25 | 0,57 | 97,73 | ||
Zona A | Superfície mancha branca | 0,43 | 1.03 | 2,91 | – | – | 0,22 | – | – | – | 0,09 | 0,21 | 0,19 | 0,35 | 94,59 |
0,38 | 0,89 | 2,58 | – | 0,07 | 0,18 | 0,05 | 0,11 | 0,08 | 0,10 | 0,25 | 0,12 | 0,31 | 94,86 | ||
Descascando fundo plano | 0,28 | 0,73 | 8,59 | – | 0,09 | 0,56 | 0,04 | 0,08 | 0,10 | 0,12 | 0,06 | 0,33 | 1,40 | 89,61 | |
0,39 | 0,84 | 11h59 | 0,15 | 0,10 | 0,67 | 0,13 | 0,11 | 0,09 | 0,12 | 0,06 | 0,34 | 1,71 | 83,71 | ||
Zona B | Manchas escuras | 1.03 | 0,58 | 29,53 | 0,50 | 0,10 | 0,51 | 0,05 | 0,90 | 0,39 | 1.21 | 0,18 | 0,26 | 0,51 | 64,25 |
0,80 | 0,55 | 28.27 | 0,38 | 0,04 | 0,53 | 0,07 | 1.04 | 0,36 | 1,33 | 0,11 | 0,20 | 0,50 | 65,84 | ||
Mancha redonda branca | 0,62 | 0,83 | 3.29 | 0,25 | 0,16 | 0,39 | 0,10 | 0,15 | 0,20 | 0,22 | 0,60 | 0,29 | 0,58 | 92,33 | |
0,96 | 0,66 | 5.05 | 030 | 0,16 | 0,60 | 0,06 | 0,14 | 0,23 | 0h30 | 0,96 | 0,32 | 1.09 | 89,16 |
Conforme visto na Tabela 1, o conteúdo do elemento O na área manchada anormal é maior do que na área normal. Além de maior teor de O, também contém vestígios de Na, S, Cl, K, Ca, Mg, Al e outros elementos provenientes de resíduos de água, agentes de limpeza e óleo de barbear.
Esta análise mostra que o aparecimento da nitretação a gás é causado pela má limpeza antes do processo de nitretação. Portanto, os seguintes pontos devem receber atenção especial durante a limpeza de engrenagens de nitretação a gás:
- Ao usar um agente de limpeza à base de água, a temperatura da água para o enxágue final não deve ser muito alta. Se a temperatura da água estiver muito alta, ela evaporará rapidamente e deixará resíduos na superfície da peça de trabalho. É melhor reduzir a temperatura de enxágue e usar uma pistola de ar de alta pressão para secar a peça de trabalho.
- A limpeza com substâncias como acetona ou gasolina é possível, mas essas substâncias têm baixo ponto de inflamação. É importante garantir ventilação adequada e segurança contra incêndio no ambiente de limpeza.
- A peça de trabalho deve ser completamente seca antes de ser limpa com um limpador de hidrocarboneto.
- A qualidade da água utilizada no processo de limpeza deve ser considerada, e água pura deve ser utilizada tanto quanto possível.
3. Controle da distorção da nitretação de engrenagens
A distorção que ocorre durante a nitretação de engrenagens é influenciada por vários fatores, incluindo formato da engrenagem, tensão residual de usinagem, material da engrenagem, ferramentas de nitretação, processo de nitretação e velocidade de resfriamento da engrenagem após a nitretação.
Na produção típica, as pessoas tendem a se concentrar nos primeiros fatores, mas muitas vezes ignoram a velocidade de resfriamento da engrenagem após a nitretação. Isto é especialmente relevante para o furo interno de engrenagens de paredes finas, que são particularmente sensíveis à velocidade de resfriamento após a nitretação.
Por exemplo, considere a engrenagem mostrada na Figura 3.
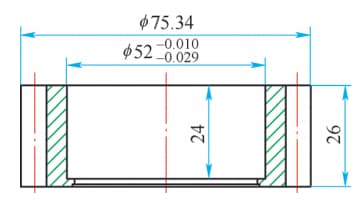
Fig. 3 tamanho da engrenagem
O tamanho do furo interno antes da nitretação era de φ 52-0,02-0,035 mm. A Tabela 2 apresenta a relação entre o tempo de resfriamento da engrenagem e a expansão do furo interno.
Tabela 2 Relação entre tempo de resfriamento da engrenagem e expansão do furo interno
Tempo de resfriamento após nitretação /h |
Expansão do furo interno / milímetros |
Taxa de aprovação (%) |
Observações |
≥6 | 0,012~0,021 | 75 | O tamanho do furo interno excede a tolerância superior |
4~5 | 0,008~0,012 | 99 | O furo interno está basicamente dentro da faixa de tamanho |
≤4 | 0,005~0,01 | 78 | Tamanho do furo interno fora da tolerância |
Os resultados dos testes mostram que a tendência de distorção dos furos internos da engrenagem em diferentes velocidades de resfriamento é consistente e geralmente aumenta, mas a extensão da distorção varia. Quando a taxa de resfriamento após a nitretação é lenta, a distorção do furo interno é maior, e quando a taxa de resfriamento após a nitretação é rápida, a distorção do furo interno é menor.
Para garantir uma distorção estável do furo interno da engrenagem e melhorar a taxa de qualificação do furo interno da engrenagem após a nitretação, a velocidade de resfriamento da engrenagem durante a nitretação a gás deve ser cuidadosamente controlada.
4. Remédio para oxidação causada por vazamento de gás do forno de nitretação a gás
Se ocorrer um vazamento de gás no forno de nitretação a gás devido à vedação ou outros problemas, a superfície da peça ficará oxidada. Esta oxidação não afeta a qualidade interna da peça, mas não atende aos padrões de qualidade de aparência. Em tal situação, o processo de redução descrito na Tabela 3 pode ser utilizado para reparo.
Tabela 3 Processo de reparo de peças oxidadas
Temperatura de reparo /℃ |
Tempo de reparo /min |
Taxa de decomposição de amônia (%) |
480~500 | 30~40 | 30~40 |
A aparência da engrenagem após nitretação a gás, oxidação e redução de vazamento de gás é mostrada na Figura 4.
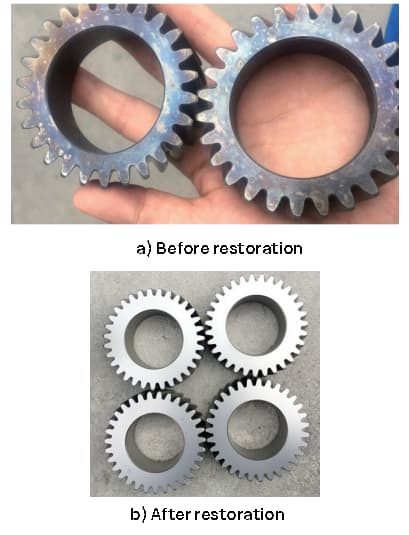
Fig. 4 aparência das engrenagens antes e depois da redução do vazamento de gás amônia
É importante ressaltar que durante o processo de redução da aparência, a temperatura de nitretação não deve ultrapassar a primeira temperatura de nitretação. Tipicamente, a temperatura de nitretação durante a redução deve ser cerca de 20°C inferior à última temperatura de nitretação. A duração do processo de redução pode ser ajustada com base na extensão da oxidação.
5. Conclusão
Os três problemas e soluções acima destacam a importância de prestar atenção a cada detalhe no processo de tratamento térmico. Com uma consideração cuidadosa de cada etapa, é possível resolver com eficácia quaisquer problemas que possam surgir.