A eletrólise é usada para formar uma fina película de óxido na superfície de peças de metal ou liga, usando as peças como ânodos.
O filme de óxido metálico altera o estado e as propriedades da superfície, como coloração da superfície, melhor resistência à corrosão, maior resistência ao desgaste e dureza e proteção da superfície metálica.
Por exemplo, na anodização de alumínio, o alumínio e suas ligas são colocados em eletrólitos correspondentes (como ácido sulfúrico, ácido crômico, ácido oxálico, etc.) como ânodos, e a eletrólise é realizada sob condições específicas e com corrente externa aplicada.
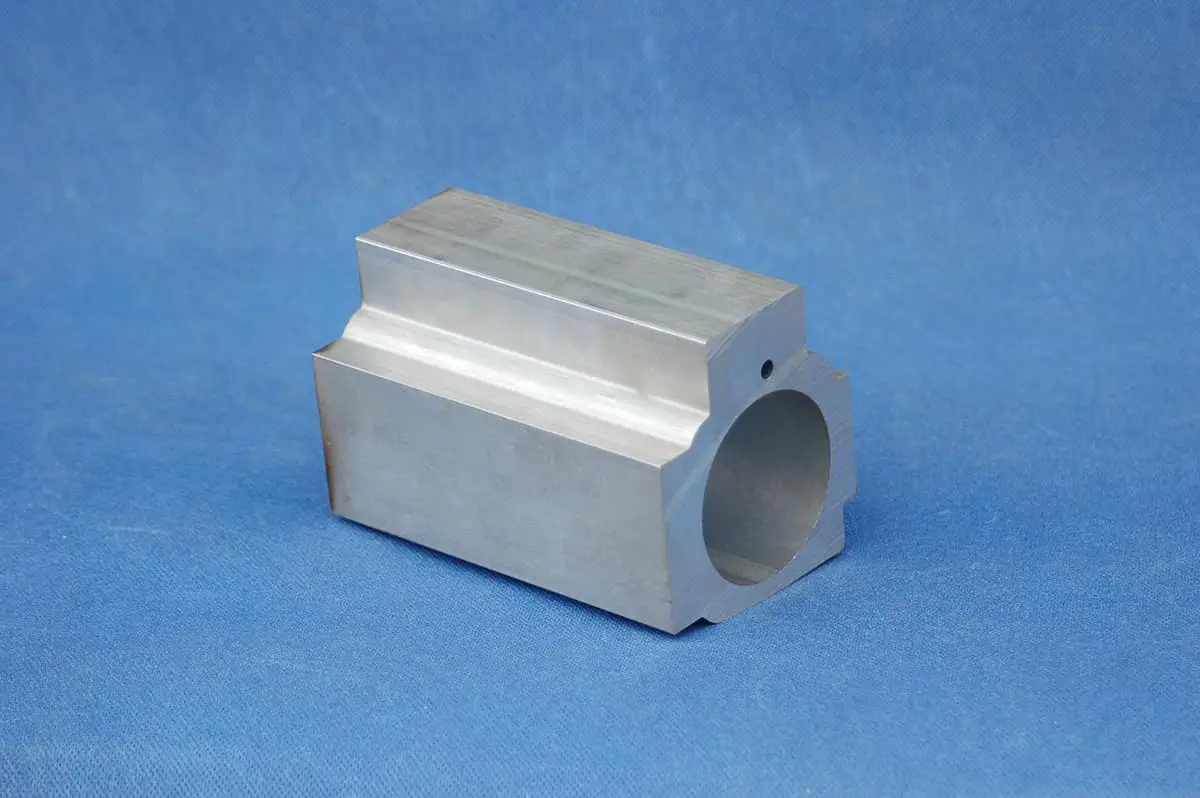
O alumínio ou sua liga no ânodo oxida, formando uma fina camada de óxido de alumínio na superfície, com espessura de 5 a 20 mícrons. Os filmes de anodização dura podem atingir 60-200 mícrons de espessura.
Após a anodização, a dureza e a resistência ao desgaste do alumínio ou de sua liga são melhoradas, atingindo 250-500 kg/milímetro quadrado. O filme de anodização dura também possui boa resistência ao calor, com ponto de fusão tão alto quanto 2
Em aplicações práticas, a anodização de ligas de alumínio é bastante comum e pode ser utilizada no dia a dia, pois esse processo cria uma dura camada protetora na superfície das peças de alumínio, tornando-a adequada para a produção de utensílios de cozinha e outros utensílios domésticos.
Porém, a anodização do alumínio fundido apresenta resultados ruins, com superfícies irregulares e apenas coloração preta. A anodização de perfis de liga de alumínio é relativamente melhor.
Nos últimos anos, a tecnologia de coloração por oxidação de alumínio da China desenvolveu-se rapidamente e muitas fábricas adotaram novas tecnologias de processo e acumularam uma rica experiência na produção real.
Existem muitos métodos maduros e em desenvolvimento para anodização de alumínio e suas ligas, dos quais processos adequados podem ser selecionados com base nas necessidades de produção.
Antes de selecionar um processo de oxidação, é importante compreender o material de alumínio ou liga de alumínio, pois a qualidade do material e sua composição afetam diretamente a qualidade do produto de alumínio anodizado.
Por exemplo, se houver defeitos como bolhas, arranhões, descascamento, rugosidade, etc. na superfície do alumínio, eles ainda serão visíveis após a anodização. A composição da liga também afeta diretamente a aparência da superfície anodizada.
Por exemplo, ligas de alumínio contendo 1-2% de manganês tornam-se azuis acastanhadas após a oxidação, e o aumento do teor de manganês leva a uma transformação da cor azul acastanhada para marrom escuro.
As ligas de alumínio contendo 0,6-1,5% de silício tornam-se cinza após a oxidação, enquanto aquelas contendo 3-6% de silício tornam-se branco-acinzentadas. As ligas contendo zinco parecem leitosas, enquanto as ligas contendo cromo exibem cores irregulares que variam do amarelo dourado ao cinza, e as ligas contendo níquel aparecem amarelo claro.
De modo geral, apenas ligas de alumínio contendo mais de 5% de magnésio e titânio podem atingir uma aparência transparente e brilhante após a oxidação.
Depois de selecionar materiais adequados de alumínio e liga de alumínio, é necessário considerar a escolha do processo de anodização apropriado.
Atualmente, a oxidação do ácido sulfúrico, a oxidação do ácido oxálico e a oxidação do ácido crômico são amplamente utilizadas na China e foram minuciosamente documentadas em manuais e livros. Este artigo apresenta brevemente alguns novos processos atualmente em desenvolvimento na China e métodos estrangeiros.
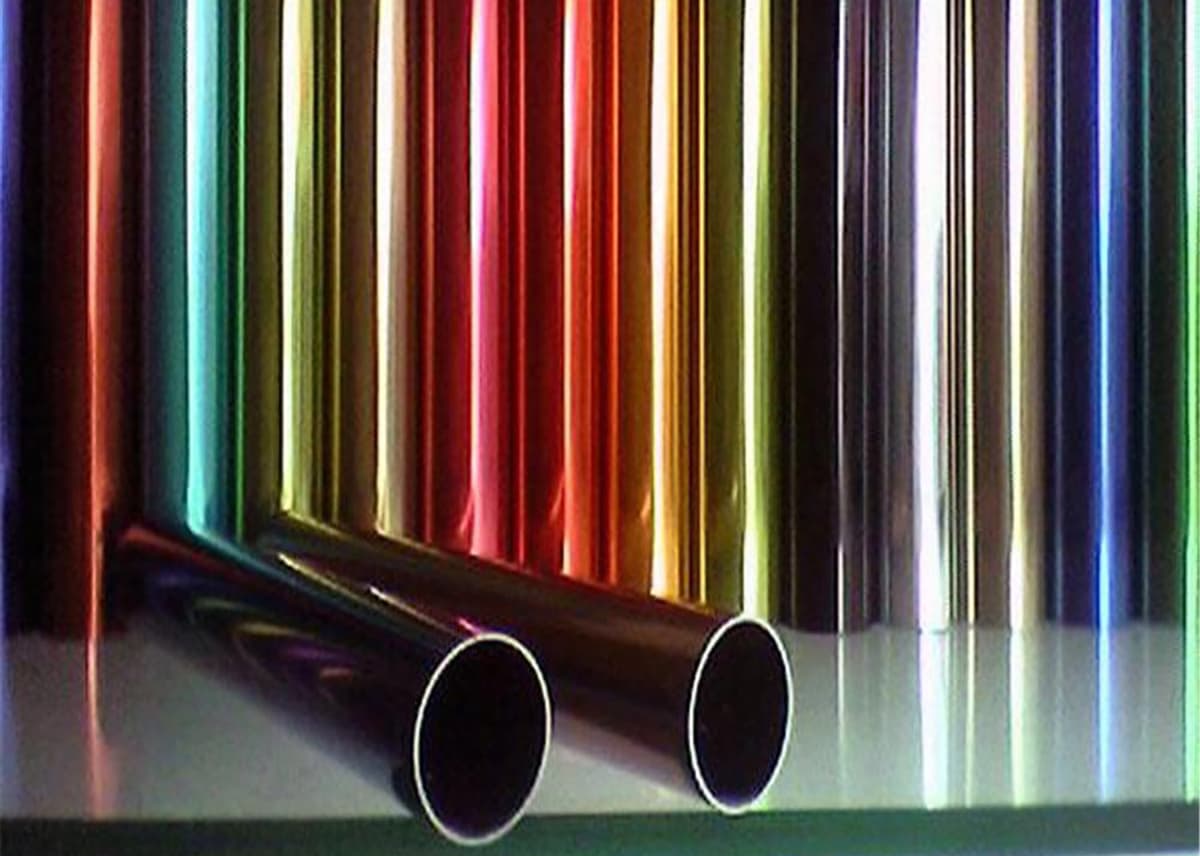
1. Novos processos desenvolvidos na China:
(1) Oxidação rápida de AC em mistura de ácido oxálico-metanóico.
O uso de uma mistura de ácido oxálico-metanóico baseia-se na ideia de que o ácido metanóico é um forte agente oxidante e pode acelerar a dissolução da camada interna (camada de barreira e camada de bloqueio) do filme de óxido, resultando na formação de uma camada externa porosa. .
Este tipo de solução pode aumentar a condutividade (ou seja, aumentar a densidade da corrente), permitindo a formação rápida do filme de óxido. Em comparação com a oxidação do ácido oxálico puro, esta solução pode aumentar a produtividade em 37,5% e reduzir o consumo de energia (3,32 kWh por metro quadrado para oxidação do ácido oxálico em comparação com 2 kWh por metro quadrado para este processo), economizando 40% de eletricidade.
A formulação do processo é a seguinte: ácido oxálico 4-5%, ácido metanóico 0,55%, CA trifásico 44 V, densidade de corrente 2-2,5 A/d㎡, temperatura 30±2℃.
(2) Oxidação ácida mista.
Este método foi oficialmente incluído no padrão nacional japonês em 1976 e adotado pela Kita-sei Nissho Co., Ltd. Suas características são rápida formação de filme, maior dureza, resistência ao desgaste e resistência à corrosão do filme em comparação com a oxidação convencional de ácido sulfúrico.
O filme é branco prateado e adequado para impressão e coloração de produtos. Depois que a indústria chinesa de produtos de alumínio visitou o Japão, este método foi recomendado para uso em 1979.
A formulação do processo recomendada é: H2SO4 10-20%, COOHCOOH·2H2O 1-2%, tensão 10-20 V, densidade de corrente 1-3 A/d㎡, temperatura 15-30℃, tempo 30 minutos.
(3) Oxidação cerâmica.
A oxidação cerâmica utiliza principalmente ácido crômico, ácido bórico e oxalato de titânio e potássio como eletrólitos e é submetida a tratamento eletrolítico em alta tensão e temperatura.
O filme assemelha-se ao esmalte da cerâmica, com alta resistência à corrosão, boa resistência ao desgaste, podendo ser colorido com corantes orgânicos ou inorgânicos, conferindo-lhe brilho e cor especiais. É usado principalmente em panelas de alumínio, isqueiros e canetas douradas e é muito popular entre os consumidores.
(4) Oxidação de cor militar.
A oxidação da cor militar é usada principalmente para decoração em produtos militares de alumínio, por isso requer efeitos de proteção especiais. O filme de óxido é verde militar, não brilhante, resistente ao desgaste, durável e possui boas propriedades de proteção.
O processo envolve primeiro realizar a oxidação do ácido oxálico para gerar uma camada de filme amarelo dourado e, em seguida, submetê-la ao tratamento de oxidação anódica usando uma solução de 20g/l de permanganato de potássio e 1g/l de H2SO4. A Shenyang Aluminum Products Factory usou esse processo para produzir garrafas de água e utensílios de cozinha militares.
(5) Oxidação multicolorida.
A camada de óxido anódico já tingida, mas não fechada, é umedecida com ácido crômico ou ácido oxálico para que o CrO3 se espalhe.
A superfície do produto tingido desbota quando é umedecido com CrO3, e o ácido oxálico ou crômico é lavado com água em qualquer parte conforme necessário, geralmente interrompendo a reação com a imagem.
Em seguida, o segundo corante é aplicado ou o processo de limpeza, enxágue e tingimento com CrO3 é repetido para produzir padrões como flores e nuvens, conforme necessário.
Atualmente, esse método é amplamente utilizado em produtos como xícaras de ouro, xícaras de água, caixas de chá e isqueiros.
(6) Processo de tingimento de padrão de mármore.
Após o produto ser oxidado e tingido com a primeira cor, ele é seco e depois imerso em água com graxa na superfície.
Quando levantada ou imersa, a graxa e a água fluem naturalmente, causando manchas irregulares em formato de listras no filme. Quando o segundo corante é aplicado, o filme oxidado não pode ser manchado onde está manchado com graxa, enquanto a parte sem graxa é tingida com o segundo tom, formando um padrão irregular semelhante ao mármore.
Este método pode ser encontrado no artigo do camarada Zhou Shouyu da Yangjiang Knife Factory, de propriedade do Estado de Guangdong (Electroplating and Coating, 1982, Edição 2).
(7) Oxidação por ataque químico.
Após polimento mecânico e desengorduramento, os produtos de alumínio são revestidos com agentes de mascaramento ou materiais fotossensíveis e secos, depois submetidos a ataque químico (atacantes com flúor ou sal de ferro) para formar padrões côncavo-convexos.
Após polimento eletroquímico e oxidação anódica, apresenta-se o padrão de superfície com forte sentido do corpo principal, que pode ser comparável à aparência do aço inoxidável. Atualmente é usado em produtos como canetas douradas, caixas de chá e telas.
(8) Oxidação anódica rápida à temperatura ambiente.
Normalmente, a oxidação do H2SO4 requer um dispositivo de resfriamento, resultando em alto consumo de energia. A adição de ácido alfa-hidroxipropiônico e glicerol pode suprimir a dissolução do filme de óxido, possibilitando a oxidação à temperatura ambiente.
Em comparação com a oxidação comum do ácido sulfúrico, a espessura do filme pode ser aumentada duas vezes. A formulação do processo recomendada é:
H2ENTÃO4 | 150~160g/l |
CH3CH(OH)COOH | 18ml/l |
CH2OHCHOHCH2OH | 12ml/l |
Densidade atual | 0,8-12 A/d㎡ |
Tensão | 12-18V |
Temperatura | 18-22℃ |
(9) Método de oxidação química (também conhecido como filme de óxido condutor).
A resistência à corrosão da camada de filme é semelhante à do filme de óxido anódico de ácido sulfúrico. O filme de óxido condutor tem menor resistência de contato e pode conduzir eletricidade, enquanto o H2ENTÃO4 o filme de óxido anódico não pode conduzir eletricidade devido à sua alta resistência de contato.
A resistência à corrosão do filme de óxido condutor é muito mais forte do que a do alumínio banhado a cobre, prateado ou estanhado.
A desvantagem é que a soldagem de estanho não pode ser realizada na camada de filme, apenas a soldagem por pontos pode ser usada. A formulação de processo recomendada é: CrO3 4g/l, K4Fe(CN)6·3H2O 0,5g/l, NaF 1g/l, temperatura 20-40°C, tempo 20-60 segundos.
Ao selecionar o alumínio para oxidação anódica, também deve ser observado o seguinte:
(1) A superfície do alumínio selecionado não deve apresentar arranhões graves, defeitos estruturais ou inclusões. Eles afetarão a aparência e a resistência à corrosão da camada de filme de óxido.
(2) Algumas ligas de alumínio devem ser tratadas termicamente de acordo com especificações razoáveis. O tamanho dos grãos tem certo impacto na estrutura e nas propriedades do filme de óxido. Os grãos grossos reagem de forma desigual durante a oxidação, muitas vezes resultando em uma aparência semelhante a uma casca de laranja. Portanto, é geralmente desejado que o alumínio tenha uma estrutura de grão fino.
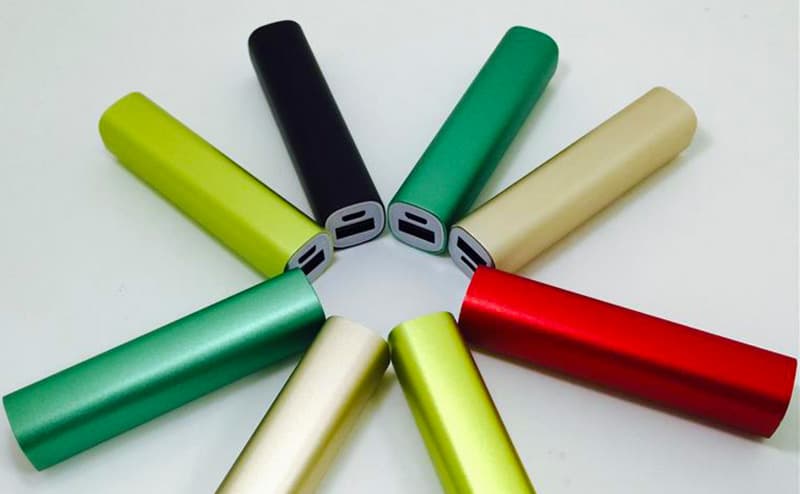
2. Introdução a novos processos de tratamento de superfície no exterior
Nos últimos anos, os países estrangeiros desenvolveram-se rapidamente no tratamento de superfície de alumínio. Antigos processos que outrora exigiam muita mão-de-obra, muita energia e muitos recursos foram reformados, e novos processos e tecnologias foram amplamente aplicados na produção industrial.
(1) Método de oxidação anódica de alta velocidade.
O processo de oxidação anódica de alta velocidade altera principalmente a composição da solução eletrolítica e reduz a impedância da solução eletrolítica, permitindo assim densidades de corrente mais altas para oxidação anódica de alta velocidade.
A velocidade de formação de filme do processo antigo usando uma densidade de corrente de 1A/d㎡ era de 0,2~0,25μ/min, enquanto a velocidade de formação de filme deste novo processo usando a solução modificada pode ser aumentada para 0,4~0,5μ/min mesmo com um 1A/dm2 densidade atual, reduzindo significativamente o tempo de processamento e melhorando a eficiência da produção.
(2) Método do estilo Tomita (oxidação em alta velocidade).
O método estilo Tomita tem um tempo de processamento muito mais curto do que o processo antigo e sua eficiência de produção pode ser aumentada em mais de 33%. Este método é adequado não apenas para filmes de óxido anódico comuns, mas também para filmes de óxido duro.
Se for necessário produzir um filme duro, é utilizado um método para reduzir a temperatura da solução. A velocidade de formação do filme é geralmente a mesma listada na tabela acima. A relação entre a dureza do filme e a temperatura da solução é a seguinte:
- 10℃ – dureza 500H
- 20℃ – dureza 400H
- 30℃ – dureza 300H
(3) Filme Ruby.
O processo de produção de um filme de rubi na superfície do alumínio é um processo novo. A cor do filme pode ser comparável à dos rubis artificiais, tornando-o ideal para fins decorativos. Também possui boa resistência à corrosão e resistência ao desgaste.
Diferentes tipos de óxidos metálicos na solução podem ser usados para produzir uma variedade de aparências. O processo envolve primeiro a anodização com ácido sulfúrico a 15% usando uma densidade de corrente de 1A/dm2 por 80 minutos.
Então, a peça é imersa em um (NH4)2CrO4 solução em diferentes concentrações por 30 minutos a 40°C, dependendo da intensidade de cor desejada, para permitir que os íons metálicos entrem nos poros do filme de óxido anódico.
Depois disso, a peça de trabalho é imersa em uma solução de bissulfato de sódio (1 grama de peso molecular) e bissulfato de amônio (1,5 gramas de peso molecular) a 170°C com uma densidade de corrente de 1A/dm2. O filme resultante é de cor vermelho púrpura com brilho fluorescente, enquanto o Fe2(CrO4)3 ou Na2CrO4 soluções produzirão filmes azuis com fluorescência roxa profunda.
(4) Eletrocoloração Asada.
A eletrocoloração Asada é um processo onde, após a anodização, cátions metálicos (sais de níquel, sais de cobre, sais de cobalto, etc.) são eletrolisados no fundo dos orifícios do filme de óxido para produzir cor. Esse processo se desenvolveu rapidamente nos últimos anos, principalmente porque pode obter as cores bronze e preto, populares na indústria da construção.
As cores produzidas são estáveis e resistentes às intempéries. Este processo pode economizar energia em comparação com métodos de coloração natural.
Quase todos os perfis arquitetônicos de alumínio do Japão são coloridos usando este método.
(5) Método de coloração natural.
O método de coloração natural completa a coloração em uma eletrólise.
Existem vários tipos de soluções utilizadas, incluindo ácido salicílico e ácido sulfúrico, ácido sulfônico e ácido de titânio, e ácido sulfônico e ácido maleico.
Como os ácidos orgânicos são usados principalmente no método de coloração natural, o filme de óxido é relativamente denso e possui excelente resistência à luz, resistência ao desgaste e resistência à corrosão.
Porém, a desvantagem deste método é que para obter cores excelentes, a composição do material da liga de alumínio deve ser rigorosamente controlada.
1. Anodização com ácido sulfúrico.
A anodização com ácido sulfúrico possui as seguintes características:
(1) Baixo custo da solução, composição simples, fácil operação e manutenção.
Geralmente, é necessária apenas a diluição do ácido sulfúrico até uma determinada concentração, sem adição de outros agentes químicos. Recomenda-se o uso de ácido sulfúrico quimicamente puro ou ácido sulfúrico industrial com menos impurezas, portanto o custo é particularmente baixo.
(2) Alta transparência do filme de óxido.
O filme anodizado com ácido sulfúrico de alumínio puro é incolor e transparente. Para ligas de alumínio, à medida que os elementos de liga Si, Fe, Cu e Mn aumentam, a transparência diminui. Comparado com outros eletrólitos, a cor do filme anodizado de ácido sulfúrico é a mais clara.
(3) Alto desempenho de coloração.
O filme de óxido de ácido sulfúrico é transparente e a camada porosa tem forte adsorção e é fácil de tingir e colorir. A cor é brilhante e não desbota facilmente, com forte efeito decorativo.
(4) As condições operacionais para anodização com ácido sulfúrico são:
H2ENTÃO4(volume) | 10%~30% |
Temperatura ℃ | 18~22 |
Al/gL-1 | ≤20 |
Densidade de corrente/A.dm-2 | 0,6~3 |
Tempo/minuto | 10~60 |
2. Anodização com ácido oxálico e ácido crômico.
A anodização com ácido oxálico é amplamente utilizada no Japão e as características do filme de óxido são semelhantes às da anodização com ácido sulfúrico, com menor porosidade que a anodização com ácido sulfúrico, alta resistência à corrosão e dureza. O custo da solução de ácido oxálico e a tensão operacional são superiores aos do ácido sulfúrico, e a cor do filme de óxido de algumas ligas pode ser mais escura. Tanto a anodização com ácido oxálico quanto com ácido sulfúrico requerem um bom sistema de resfriamento.
As condições operacionais para anodização com ácido oxálico são:
Ácido oxálico (fração volumétrica) | 2%~10% |
Temperatura / ℃ | 15~35 |
Densidade de corrente / A.dm-2 | 0,5~3 |
Tensão/V | 40~60 |
Os filmes anodizados com ácido crômico são particularmente resistentes à corrosão e são usados principalmente na indústria aeroespacial. A adesão de filmes de óxido crômico e tintas é forte, tornando-os adequados como base para tintas. O filme anodizado de ácido crômico cinza opaco geralmente não é usado para fins decorativos.
As condições operacionais para anodização com ácido crômico são:
CrO3/gL-1 | 30~100 |
Temperatura/℃ | 40~70 |
Densidade de corrente/A.dm-2 | 0,1~3 |
Tensão/V | 0~100 |
Tempo/minuto | 35~60 |
3. Anodização dura.
No final da Segunda Guerra Mundial, a fim de aumentar a dureza e a espessura do filme anodizado, a temperatura do tanque de anodização de ácido sulfúrico foi reduzida para 0 ℃ e a densidade de corrente foi aumentada para 2,7 ~ 4,0 A/dm2, obtendo um “filme de óxido duro” de 25~50μm. Um filme anodizado duro pode ser obtido a 5~15°C usando ácido oxálico com uma pequena quantidade de ácido sulfúrico. Algumas patentes utilizam concentração otimizada de ácido sulfúrico, ácidos orgânicos ou outros aditivos, como ácido benzeno hexacarboxílico para anodização dura.
Na Escócia, Campbell inventou o uso de fonte de alimentação sobreposta AC-DC, fluxo de eletrólito de alta velocidade, 0 ℃ e densidade de corrente de 25 ~ 35A / dm2 para obter um filme anodizado duro de 100 μm.
Hoje em dia, a corrente pulsada é usada para anodização dura, especialmente para ligas de alumínio com alto teor de cobre, que geralmente são difíceis de anodizar duramente. O uso de corrente pulsada pode evitar “queima”. Existem também muitas fontes de alimentação usadas para anodização rígida, como AC-DC, várias frequências de correntes de pulso monofásicas ou trifásicas, correntes reversas, etc.
Na anodização rígida DC tradicional, a densidade de corrente geralmente não pode exceder 4,0A/dm2. Para fonte de alimentação de pulso retificador monofásico, o valor de pico do pulso de corrente pode ser muito grande, mas manter a uniformidade da espessura do filme de óxido é uma questão importante.