I. Princípio de funcionamento
1. A eletrólise utiliza a peça de polimento como ânodo e um metal insolúvel como cátodo. Quando ambos são imersos em um banho eletroquímico e é aplicada corrente contínua, ocorre a dissolução anódica seletiva, resultando em uma aparência altamente lisa e brilhante na superfície do aço inoxidável.
2. A ação eletrolítica garante que o aço inoxidável tenha uma cor consistente por dentro e por fora, limpo e brilhante com brilho duradouro. Forma uma película fina e viscosa na superfície, aumentando a resistência à corrosão.
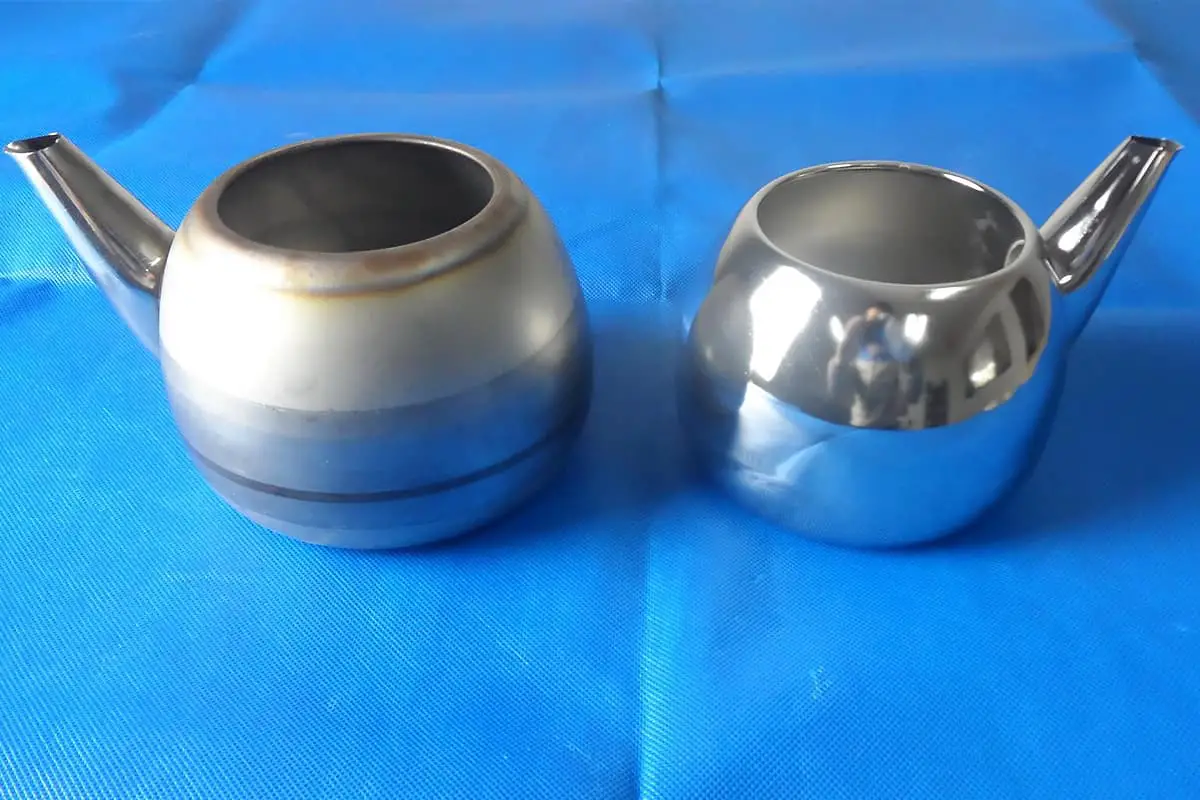
II. Composição da Solução Eletrolítica e Condições do Processo
1. Ácido Fosfórico:
Ele se dissolve e forma uma película protetora de fosfato na superfície do aço inoxidável, evitando corrosão excessiva. A concentração ideal é em torno de 750mL/L.
(1) Se a concentração for muito alta, a resistência elétrica do banho aumenta, a viscosidade aumenta, levando a uma tensão necessária mais alta e a um nivelamento mais lento.
(2) Se a concentração for muito baixa, causará corrosão irregular na superfície do aço inoxidável devido à maior ativação e menores tendências de passivação.
2. Ácido Sulfúrico:
Como ativador, melhora a condutividade da solução, reduz a resistência, diminuindo assim a tensão do banho, economizando energia e aumentando a capacidade de dispersão e a eficiência da corrente anódica. A concentração ideal é 180~210mL/L.
(1) Se a concentração for muito alta, a superfície pode ficar excessivamente corroída, resultando em corrosão uniforme e densa.
(2) Se a concentração for muito baixa, isso causará corrosão severa e irregular.
3. Anidrido Crômico:
Forte oxidante, forma uma película de passivação na superfície para evitar a corrosão, contribuindo para uma superfície mais lisa. A concentração ideal é 50~60g/L.
(1) Se a concentração de anidrido crômico for muito baixa, será um desafio conseguir uma superfície brilhante.
(2) Se a concentração for muito alta, a sedimentação poderá ocorrer sob alta corrente, reduzindo a eficiência da corrente e levando a corrosão e outras formas de corrosão excessiva na superfície de polimento.
4. Glicerol (Glicerina):
Desempenha um papel significativo na inibição da corrosão. Reage com o ácido fosfórico formando complexos e derivados metálicos, tornando a superfície polida extremamente brilhante e delicada. O glicerol também evita a corrosão química do aço inoxidável no eletrólito.
(1) Se a concentração for muito baixa, apesar de uma superfície polida brilhante, a corrosão pode torná-la áspera.
(2) Com maior concentração, pode superar a rugosidade, resultando em uma superfície polida brilhante e delicada.
(3) Se a concentração for muito alta, poderá ser produzida espuma excessiva, afetando as operações e desperdiçando material.
5. Sacarina: Aumenta o brilho.
(1) A sacarina, quando envolvida em processos catódicos, pode ser adsorvida em superfícies metálicas, contribuindo para o brilho e brilho da superfície polida.
(2) Nos processos anódicos, a sacarina forma uma película de adsorção na superfície do ânodo, que protege a superfície do aço inoxidável da erosão eletrolítica quando não há corrente. Quando a energia é aplicada, as linhas elétricas rompem primeiro a película de isolamento nas partes elevadas, iniciando a dissolução, enquanto as áreas rebaixadas são efetivamente protegidas, resultando na dissolução seletiva para uma superfície lisa e brilhante.
6. Densidade atual:
(1) Em baixas densidades de corrente, o metal está em estado ativado, com a superfície polida sendo erodida. Os produtos de dissolução anódica são mínimos e a dissolução química domina a dissolução eletroquímica, levando a uma lisura deficiente.
(2) Quando a densidade de corrente ultrapassa o valor adequado, ocorre intensa evolução de oxigênio, causando superaquecimento e corrosão excessiva na superfície do metal, levando à dissolução irregular e aumento do consumo de energia elétrica.
7. Temperatura:
Um aumento moderado na temperatura pode acelerar o processo de nivelamento e melhorar a eficiência da corrente, aumentando assim a suavidade e o brilho da superfície.
(1) Uma temperatura muito baixa aumenta a viscosidade do eletrólito, tornando mais difícil a difusão dos produtos de dissolução anódica da superfície do metal para o eletrólito e o reabastecimento do ânodo.
(2) Uma temperatura muito alta aumenta a quantidade de metal dissolvido, produzindo vapor e gás no tanque que deslocam o eletrólito da superfície do metal, retardando paradoxalmente a taxa de dissolução do metal. A diminuição da viscosidade perto do eletrólito acelera a difusão dos produtos de dissolução, levando a taxas de dissolução aceleradas e impactando a suavidade da superfície.
III. Preparação da solução eletrolítica
A solução deve ser preparada de acordo com o conteúdo em volume (% (V)) ou mL/L e conteúdo em massa (% (p)) ou g/L na fórmula, que irá diferir no cálculo da dosagem.
1. Conteúdo de volume
Supondo que o volume do líquido do tanque seja 1000L, o cálculo da dosagem e as etapas de preparação são os seguintes.
a. Dosagem de ácido fosfórico: XmL/L×1000L=XL. Meça e adicione ácido fosfórico XL ao tanque.
b. Dosagem de ácido sulfúrico: XmL/L×1000L=XL. Meça e adicione gradualmente ácido sulfúrico XL ao ácido fosfórico enquanto agita.
c. Dosagem de água: XmL/L×1000L=XL. Coloque em um recipiente separado.
d. Dosagem de anidrido crômico: XmL/L×1000L=XL. Adicione o anidrido crômico pesado à água e mexa até que se dissolva em uma solução de ácido crômico.
e. Adicione gradualmente a solução de ácido crômico à solução de ácido fosfórico-sulfúrico, mexendo até ficar uniforme. A solução aparecerá amarela.
f. (1) Dosagem de gelatina: Xg/L×1000L=Xkg. Mexa a gelatina pesada em água quente até ficar uniforme e, em seguida, adicione-a lentamente em pequenos lotes à solução de ácido fosfórico-sulfúrico. Isto iniciará uma forte reação de redução e o eletrólito ficará amarelo-esverdeado.
(2) Adicione gradualmente a quantidade calculada de glicerina ao tanque enquanto mexe. Isto também iniciará uma forte reação de redução e produzirá excesso de espuma. Para evitar que a solução transborde devido à espuma, tenha especial cuidado ao adicionar glicerina. A solução também ficará verde-amarelada. Deixe esfriar sem ser perturbado.
2. Conteúdo em massa
a. Meça a gravidade específica dos ácidos fosfórico e sulfúrico utilizados, assumindo a densidade medida do ácido fosfórico d1=1,7g/mL, densidade do ácido sulfúrico d2=1,8g/mL.
b. Então, a partir das tabelas de dados químicos da densidade relativa de cada ácido, verifica-se que: em 100g de solução ácida, o teor de ácido fosfórico P1=86,25g, o teor de ácido sulfúrico P2=88g.
c. Calcule o volume necessário de ácido fosfórico V1 e ácido sulfúrico V2.
V=xdo×1000/pd (L)
Onde x é a porcentagem em massa do ácido na fórmula; fazer é a densidade da solução, tome o valor médio=1,65g/mL
d. Volume de água=1000-V1-V2
e. Dosagem de anidrido crômico.
Como o anidrido crômico é um ácido sólido, a massa necessária é calculada pela fórmula xd0×1000/100 (Kg).
f. Adicione a quantidade calculada de anidrido crômico à água necessária e mexa até dissolver.
g. Adicione a quantidade calculada de ácido fosfórico à solução de anidrido crômico e mexa até ficar uniforme.
h. Adicione gradualmente a quantidade calculada de ácido sulfúrico à solução da etapa g enquanto agita.
3. Medindo a densidade relativa da solução:
Depois que a solução preparada esfriar até a temperatura ambiente, meça sua densidade relativa usando um hidrômetro.
1. Se a densidade relativa exceder 1,7, adicione uma quantidade adequada de água ao eletrólito, diluindo-o até que a densidade relativa esteja na faixa de 1,6 a 1,7.
2. Se a densidade relativa estiver entre 1,6 e 1,7, mas o volume do eletrólito for insuficiente, reabasteça a quantidade necessária de ácido fosfórico, ácido sulfúrico e anidrido crômico de acordo com a falta de volume.
3. Se a densidade relativa estiver abaixo de 1,6 e o volume já for suficiente ou ligeiramente excedido, aqueça o eletrólito a 80°C e evapore a umidade até que a densidade relativa atinja a faixa de 1,6 a 1,7.
4. Tratamento eletrolítico: Pendure uma placa de chumbo no cátodo e uma placa de aço inoxidável no ânodo. Na temperatura de 70 a 80°C, aplicar densidade de corrente de 60 a 80A/dm² com duração calculada em 40Ah/L.
Em seguida, inicie a produção experimental. Se a corrosão por corrosão aparecer na superfície da peça de trabalho ou o brilho da superfície não for satisfatório, a adição de anidrido crômico, gelatina e glicerina pode aumentar rapidamente o conteúdo de cromo hexavalente e cromo trivalente no eletrólito para os níveis necessários.
O tratamento eletrolítico pode tornar o eletrólito ligeiramente verde, indicando que uma certa quantidade de íons de níquel e cromo se dissolveu no eletrólito, permitindo uma produção experimental bem-sucedida.
4. Requisitos de manutenção e processo do eletrólito:
1. O aço inoxidável deve ser completamente desengraxado antes da eletrólise para evitar a contaminação do banho por óleo.
2. A densidade relativa da solução deve ser medida regularmente durante o uso e ajustada imediatamente.
3. Elementos metálicos de ferro, cromo e níquel em aço inoxidável se dissolvem no eletrólito durante o processo de eletrólise. Uma vez acumulados até certo ponto, aumentam a viscosidade e a resistência da solução, resultando em uma superfície sem brilho no aço inoxidável.
Você pode escolher entre dois métodos:
- Dilua a solução com uma quantidade adequada de água para diminuir a acidez. Impurezas como ferro, cromo e níquel podem formar fosfatos localizados e precipitar. Remova o sedimento do fundo do banho, aqueça e evapore a água para restaurar a densidade relativa original.
- Substitua parte da solução, de preferência retendo 20% da solução antiga e complementando com 80% da solução nova.
4. Limpeza das placas de chumbo do cátodo: Durante a eletrólise, a superfície da placa de chumbo do cátodo acumula uma espessa camada de impurezas, como ferro e níquel, dificultando a condutividade da superfície do cátodo e diminuindo a corrente. Isto prejudica a densidade da corrente anódica e afeta gravemente a qualidade da eletrólise. É crucial remover esses depósitos em tempo hábil para manter a fluidez do circuito.
5. Proporção da área cátodo-ânodo: A área do cátodo é mantida em 1/2 a 1/3,5 da área do ânodo para inibir o aumento do cromo trivalente. O excesso de cromo trivalente é oxidado em cromo hexavalente na superfície do ânodo. Uma superabundância de cromo trivalente pode levar ao envelhecimento eletrolítico.
6. Espaçamento entre eletrodos:
- Uma grande distância aumenta a resistência, o consumo de energia e pode causar aquecimento da solução, afetando a qualidade da eletrólise.
- Uma pequena distância pode causar curto-circuito e escurecimento do produto. A distância ideal entre o cátodo e o ânodo é de 100-300 mm.
7. Corte da fonte de alimentação durante a entrada e saída do tanque: A fonte de alimentação deve ser cortada quando as peças de trabalho são colocadas ou retiradas do tanque. Não é aconselhável transportar ou remover acessórios com eletricidade, pois isso pode resultar em faíscas elétricas, causar eletrólise e potencialmente inflamar uma mistura de gás hidrogênio e oxigênio agregado na superfície do tanque.
8. Controle a densidade de corrente anódica apropriada: A densidade de corrente anódica é proporcional à dissolução do metal. Escolher a densidade de corrente anódica correta e controlá-la dentro de uma determinada faixa de potencial anódico é essencial para uma boa qualidade de eletrólise.
- Se a densidade da corrente anódica for muito baixa, a dissolução geral do ânodo ocorre na superfície da peça sem qualquer efeito.
- B. Se a densidade da corrente anódica for muito alta, a membrana é perfurada, o oxigênio é rapidamente liberado na forma gasosa, ocorre superaquecimento da superfície, a dilatação do eletrólito se intensifica, a membrana fica arruinada, não existe mais e ocorre corrosão eletroquímica.
9. Controle a temperatura do banho:
- A temperatura deve ser mantida dentro da faixa de processo prescrita para manter a taxa de nivelamento normal, reduzir a viscosidade do eletrólito, diminuir a espessura da membrana anódica, acelerar a difusão dos produtos de dissolução anódica, acelerar a convecção da solução, facilitar o desprendimento de bolhas de gás retidas no ânodo e evitar a ocorrência de manchas ou manchas.
- Se a temperatura for muito alta, pode causar superaquecimento da solução, acelerando a conversão do cromo hexavalente em cromo trivalente (Cr 6+ +3e→Cr 3+), o que pode levar à corrosão superficial.
- Se a temperatura for muito baixa, pode aumentar a viscosidade da solução e a espessura da membrana da superfície anódica, inibir a difusão dos produtos de dissolução anódica e reduzir significativamente o efeito de nivelamento.
10. Proporção ideal de cromo hexavalente e cromo trivalente: A solução deve manter uma cor verde-amarelada durante o processo de produção.
- Se a cor for predominantemente amarela, indica que o eletrólito contém Cr 6+ em excesso. Adicione uma quantidade apropriada de gelatina ou glicerina para reduzir parcialmente o cromo hexavalente em cromo trivalente, ou use um cátodo grande e um ânodo pequeno para eletrólise para gerar cromo trivalente.
- Se a cor for verde escura, significa que o eletrólito contém Cr 3+ em excesso. Dissolva uma quantidade proporcional de anidrido crômico em água e adicione-o à solução, ou use um ânodo grande e um cátodo pequeno para eletrólise para converter parcialmente o cromo trivalente em cromo hexavalente, o que também pode melhorar a qualidade da solução.
5. Medical Device Co., Ltd. Fluxo de processo
(1) Usando o método de ativação química, o aço inoxidável é levemente gravado antes da eletrólise para remover o filme passivo e ativar a superfície metálica.
Após ataque suave, não deve ser deixado no ar por muito tempo, deve ser imediatamente limpo, seco e transferido para eletrólise.
Processo de gravação suave: Ácido sulfúrico: 3% ~ 5% Temperatura: Temperatura ambiente Duração: 0,5 ~ 1min
(2) Componentes e condições de trabalho da solução eletrolítica
- Ácido Fosfórico (H3PO4,85%) (d=1,65) (60%~70%) (Ótimo: 70%)
- Ácido Sulfúrico (H2SO4,98%) (d=1,84) (8%~15%) (Ótimo: 12%)
- Anidrido Crômico (CrO3) (5%~15%) (Ótimo: 12%)
- Glicerol ou Gelatina – 12% (8g/L)
- Água – Quantidade Restante
- Temperatura (°C) – (50~100) (Ótimo: 50~70)
- Tensão (V) – 10~20
- Densidade de corrente anódica A/d㎡ – (10~55) (ideal: 15~30)
- Densidade relativa da solução (g/cm 3) – 1,6~1,7
- Duração (min) – 30~45 (com base no tamanho da peça)
- Proporção da área de superfície do cátodo para o ânodo – (1~1,5):1
- Material Catódico – Chumbo
4. Análise de problemas comuns no polimento eletrolítico de aço inoxidável
1. Marcas na superfície da peça de trabalho
A principal causa é a distribuição desigual da densidade de corrente. Existem vários fatores que influenciam esta distribuição desigual, incluindo:
1. Densidade de corrente inconsistente causada pela estrutura do aparelho. Modificar a estrutura do acessório para garantir um contato equilibrado e uniforme com a peça de trabalho pode ajudar. Idealmente, deveríamos aumentar a área de contato entre o acessório e a peça, garantindo ao mesmo tempo a qualidade do acessório.
2. A gravidade específica do fluido de polimento eletrolítico cai ou excede o valor máximo. Se ultrapassar a faixa de gravidade específica exigida, a superfície da peça estará sujeita a marcas. A gravidade específica ideal para o fluido eletrolítico é 1,72.
3. A alta temperatura pode aumentar a condutividade do fluido eletrolítico e melhorar o brilho da superfície da peça de trabalho. No entanto, também pode levar a uma distribuição desigual da densidade de corrente, resultando em marcas.
4. Peças retrabalhadas tendem a desenvolver marcas durante a segunda rodada de polimento eletrolítico. Para evitar isso, a duração e a corrente da segunda rodada de polimento devem ser reduzidas.
5. O escape inadequado de gás deve-se principalmente ao ângulo inadequado do acessório na peça de trabalho. A direção dos furos da peça deve ser para cima e o ângulo de fixação deve ser ajustado para permitir fácil dispersão do gás durante o polimento eletrolítico.
6. O tempo prolongado de polimento eletrolítico pode causar marcas devido ao excesso de corrosão. O polimento eletrolítico é um processo de nivelamento microscópico. Quando a superfície da peça atinge um nível microscópico de brilho e suavidade, a oxidação na superfície da peça é interrompida. Se a eletrólise continuar, ocorrerá corrosão excessiva, causando marcas.
7. Alta corrente pode resultar em pontos de corrosão. Se a corrente que passa pela peça durante o polimento eletrolítico for muito alta, a taxa de dissolução da superfície da peça excede a taxa de oxidação, resultando em corrosão excessiva e manchas de corrosão.
2. Queimaduras superficiais na peça de trabalho
Vários fatores podem levar a esse defeito:
1. Se a peça não estiver posicionada corretamente na fixação antes do polimento eletrolítico, ela poderá se soltar e oscilar durante o processo. Essa frouxidão pode levar a um mau contato com o aparelho ou contato direto com o cátodo do aparelho, causando curto-circuito e subsequentes queimaduras.
2. Se o operador não realizar um teste de curto-circuito no acessório após a montagem da peça e prosseguir diretamente para o polimento eletrolítico, poderá ocorrer um curto-circuito. Sem testes, é incerto se a peça montada está em contato com o cátodo. Se ocorrer contato, a peça pode queimar.
3. Podem surgir problemas de fixação após uso prolongado, especialmente quando o acessório entra em contato direto com a peça. Se os pontos de contato no acessório ficarem irregulares, a densidade de corrente suportada pela superfície de contato da peça durante a eletrificação pode variar, causando queimaduras em áreas com maior densidade de corrente.
3. Branqueamento, escurecimento e amarelecimento da superfície das peças
1. Branqueamento de superfície: A principal causa do branqueamento da superfície da peça são as operações subsequentes, principalmente durante o processo de cozimento no forno. Se a temperatura dentro do forno for muito alta e a umidade do ar e da superfície da peça não puder ser expelida com eficácia, o problema surge. Para atenuar esta situação, a temperatura do forno deve ser controlada em torno de 80±2°C, sendo preferível utilizar um forno com bom sistema de circulação de gás.
2. Escurecimento de superfície: Este fenômeno indesejável ocorre principalmente onde a peça entra em contato com o acessório e é predominantemente devido ao próprio acessório. Uma vez finalizado o polimento eletrolítico da peça anterior, a peça deverá ser retirada da fixação em ácido nítrico diluído a 10%. Após a remoção da peça, o acessório deve ser completamente limpo com água antes de passar para a próxima peça.
3. Amarelecimento da superfície: Este problema aparece principalmente onde a peça entra em contato com o acessório. Quando a área de contato entre a peça e o ânodo do acessório é relativamente pequena, o ponto de contato pode gerar altas temperaturas e calor durante o polimento eletrolítico. Como a área de contato não está em contato com o eletrólito para resfriamento, podem ocorrer queimaduras leves, resultando em amarelecimento. A solução para este problema envolve principalmente melhorias razoáveis nos pontos de contato do acessório ou ajuste dos parâmetros de polimento eletrolítico.
4. Marcas pretas e queimadas na peça de trabalho
A formação dessas marcas se deve à alta corrente necessária para a peça eletrolítica, que ultrapassa a corrente máxima que o suspensor pode suportar. As soluções incluem:
1. Escolha de um material com melhor condutividade para o cabide:
Geralmente, a condutividade do cobre é mais de 20 vezes maior que a do titânio, portanto, os suportes de cobre têm uma condutividade mais forte do que os suportes de titânio e são menos propensos a formar marcas. Pode-se utilizar bronze fosforoso, pois apresenta boa elasticidade e dureza. Porém, a vida útil do suspensor e sua resistência à corrosão, onde o titânio se destaca, também devem ser consideradas.
2. Aumentando o número de pontos de suspensão:
Primeiro, determine a condição dos pontos de suspensão após a eletrólise. Se apenas pequenas marcas se formarem nas condições atuais, aumentar o número de pontos de suspensão poderá resolver o problema.
3. Reduzindo a tensão adequadamente:
Tensões mais altas aceleram o processo de emissão de luz, o que pode reduzir o tempo de eletrólise e aumentar a eficiência da produção. Por esta razão, as fábricas geralmente operam com tensões ligeiramente superiores às normais. No entanto, se a tensão ajustada for muito alta, poderá exceder a carga máxima do fio suspenso e criar marcas.
4. Diminuir ou controlar a temperatura do eletrólito:
Quando a temperatura do eletrólito é alta, a condutividade do suspensor diminui significativamente e a corrente exigida pela peça aumenta dramaticamente. Isso pode sobrecarregar o cabide e criar marcas. Neste caso, diminuir a temperatura do eletrólito pode resolver o problema. Se a temperatura exceder 80 graus e se formarem marcas, uma calha de resfriamento pode ser construída ao redor do tanque eletrolítico, com água circulante resfriando continuamente o eletrólito.
5. Análise de outras causas de defeitos de polimento
Defeitos de polimento | Razões: | Solução: |
Presença de manchas ou pequenas manchas na superfície | Presença de marcas de óleo ou ferrugem na superfície | Limpe completamente para remover óleo e ferrugem. |
Corrosão excessiva nas bordas e pontas da peça de trabalho | Corrente excessiva, alta temperatura ou duração prolongada | Ajuste os parâmetros correspondentes. |
Listras brancas na superfície da peça de trabalho | Solução eletrolítica densa | Diluir com água até uma densidade de 1,72. |
Qualidade variável de peças de trabalho da mesma ranhura | Muitas peças de trabalho ou interferência mútua | Reduza o número de peças de trabalho ou modifique os acessórios. |
Espuma excessiva na superfície do eletrólito | Peça suja | Certifique-se de que a peça de trabalho esteja completamente limpa. |
Superfície opaca com manchas brancas | Alto teor de anidrido crômico | Considere usar a solução eletrolítica ecologicamente correta |
Custos exorbitantes de eletricidade | Alta densidade de corrente | Considere usar a solução eletrolítica ecologicamente correta |
Faíscas observadas durante a eletrólise | Mau contato entre o acessório e a peça de trabalho | Altere os acessórios e aumente os pontos de contato. |