Soldagem a arco de aço galvanizado
O revestimento de zinco no aço galvanizado pode apresentar desafios durante a soldagem. As principais dificuldades incluem:
- Maior sensibilidade a trincas e porosidade na soldagem
- Evaporação e geração de fuligem do zinco
- Derretimento e destruição do revestimento de zinco e escória de óxido
Destes problemas, trincas de soldagem, porosidade e escória são as principais preocupações.
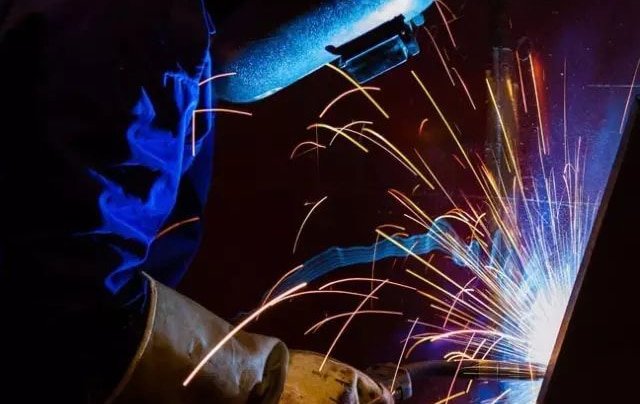
Soldabilidade
(1) A rachadura
Durante o processo de soldagem, o zinco fundido pode acumular-se na superfície da poça de fusão ou na base da solda. O ponto de fusão mais baixo do zinco em comparação com o ferro faz com que o ferro na poça fundida se solidifique primeiro, permitindo que o zinco líquido penetre nele ao longo dos limites dos grãos do aço, levando a uma diminuição na resistência da ligação intercristalina.
Além disso, a formação de compostos metálicos frágeis, como Fe3Zn10 e FeZn10, entre o zinco e o ferro reduz ainda mais a plasticidade do metal de solda. Isso o torna propenso a rachaduras ao longo dos limites do cristal devido à tensão residual de soldagem.
1) Fatores que afetam a sensibilidade ao crack
① Espessura do revestimento de zinco: A espessura do revestimento de zinco no aço galvanizado afeta sua sensibilidade a trincas. Um revestimento fino de zinco resulta em menos sensibilidade a trincas, enquanto um revestimento mais espesso em aço galvanizado a quente leva a uma maior sensibilidade a trincas.
② Espessura da peça: A espessura da peça também influencia a sensibilidade à trinca, com peças mais espessas tendo maior tensão de restrição de soldagem e maior sensibilidade à trinca.
③ Folga da ranhura: Uma folga maior da ranhura aumenta a sensibilidade à trinca.
④ Método de soldagem: Diferentes métodos de soldagem também podem afetar a sensibilidade a trincas. A soldagem a arco manual resulta em menos sensibilidade a trincas, enquanto o uso de gás CO2 para soldagem pode causar maior sensibilidade a trincas.
2) Métodos para prevenir rachaduras
① Preparação para soldagem: Antes da soldagem, é necessário criar uma ranhura em forma de V, Y ou X no local da soldagem na chapa galvanizada. O revestimento de zinco pode ser removido próximo à ranhura com oxiacetileno ou jato de areia. É importante não ter uma folga muito grande, sendo a recomendação geral de 1,5mm.
② Seleção de materiais de soldagem: Para reduzir a probabilidade de trincas, é importante escolher materiais de soldagem com baixo teor de silício. Para soldagem com proteção contra gás, deve-se utilizar um fio de soldagem com baixo teor de silício. A soldagem manual pode ser realizada usando um eletrodo tipo titânio ou um eletrodo de titânio-cálcio.
(2) Estômato
A camada de zinco próxima à ranhura pode sofrer oxidação (ZnO) e vaporização devido ao calor gerado durante a soldagem a arco, levando à emissão de fumaça branca e vapor. Isto pode facilmente resultar em porosidade na solda. Quanto maior a corrente de soldagem, mais severa será a evaporação do zinco e maior será a probabilidade de porosidade.
A soldagem com eletrodos do tipo titânio e cálcio-titânio tende a resultar em menor porosidade na faixa de média corrente. Por outro lado, tanto correntes baixas quanto altas durante a soldagem com eletrodos de soldagem do tipo celulose e com baixo teor de hidrogênio podem causar porosidade.
É importante controlar o ângulo do eletrodo para que fique na faixa de 30-70° para reduzir o risco de porosidade.
(3) A evaporação e fuligem do zinco
A camada de zinco próxima à poça fundida durante a soldagem oxida em ZnO e vaporiza devido ao calor do arco, criando uma quantidade significativa de poeira. O principal componente desta poeira é o ZnO, que pode ter efeitos nocivos no sistema respiratório dos trabalhadores.
É importante garantir uma boa ventilação durante a soldagem para reduzir o risco para os trabalhadores.
Sob as mesmas especificações de soldagem, a soldagem com um eletrodo de óxido de titânio gera menos poeira em comparação com o uso de um eletrodo de soldagem com baixo teor de hidrogênio, que tende a produzir uma maior quantidade de poeira.
(4) Escória de óxido
Ao usar uma corrente de soldagem baixa, o ZnO formado durante o processo de aquecimento pode ficar preso e formar escória de ZnO. O ZnO é estável e tem um alto ponto de fusão de 1800°C. A presença de grandes blocos de escória de ZnO pode ter um impacto negativo significativo na plasticidade da solda.
Porém, ao utilizar um eletrodo do tipo óxido de titânio, a distribuição do ZnO é pequena e uniforme, o que tem pouco efeito na plasticidade e resistência à tração da solda. Por outro lado, quando se utiliza eletrodo de celulose ou hidrogênio, o ZnO na costura de soldagem é maior e mais abundante, resultando em baixo desempenho de soldagem.
Processo de soldagem de aço galvanizado
O aço galvanizado pode ser soldado usando várias técnicas, incluindo soldagem a arco elétrico manual, soldagem com eletrodo de fusão com proteção a gás, soldagem a arco de argônio e soldagem por resistência.
(1) Soldagem a arco manual
1) Preparação da solda
Para reduzir a quantidade de pó de soldagem e evitar a formação de trincas e porosidade na soldagem, é necessário preparar o declive adequado antes da soldagem e remover a camada de zinco próxima ao sulco. Esta remoção pode ser conseguida através de chama ou jato de areia.
É importante controlar a folga da ranhura para que fique na faixa de 1,5 a 2 mm e, para peças mais espessas, a folga pode ser aumentada para 2,5 a 3 mm.
2) Seleção do eletrodo
O princípio para selecionar uma haste de soldagem é garantir que as propriedades mecânicas do metal de solda sejam tão semelhantes quanto possível às do material original. Além disso, é importante controlar a quantidade de silício no eletrodo de soldagem para que fique abaixo de 0,2%.
Leitura relacionada: Como escolher a haste de soldagem certa?
As juntas produzidas com eletrodos de soldagem do tipo ilmenita, tipo óxido de titânio, celulose, titânio-cálcio e baixo hidrogênio podem apresentar resistência satisfatória. No entanto, eletrodos com baixo teor de hidrogênio e celulose tendem a resultar em escória e porosidade nas soldas, por isso não são comumente usados.
Para chapas de aço galvanizado de aço macio, as hastes de soldagem J421/J422 ou J423 são preferidas. Para chapas de aço galvanizado com nível de resistência acima de 500MPa, devem ser utilizados varetas de solda E5001 ou E5003. Para chapas de aço galvanizado com resistência superior a 600MPa, as hastes de soldagem recomendadas são E6013, E5503 ou E5513.
Na soldagem, recomenda-se utilizar um arco curto e evitar oscilação do arco para minimizar a expansão da zona de fusão da camada galvanizada, garantir a resistência à corrosão da peça e reduzir a quantidade de fuligem gerada.
(2) Soldagem com proteção de gás com eletrodo de fusão
Soldagem com proteção de gás, como soldagem com proteção de gás CO2 ou uma mistura de Ar+CO2 ou Ar+O2, é recomendada para soldagem de aço galvanizado. O tipo de gás de proteção utilizado pode ter um impacto significativo no teor de Zn na solda. O uso de CO2 puro ou CO2+O2 resulta em um maior teor de Zn na costura de soldagem, enquanto o uso de Ar+CO2 ou Ar+O2 leva a um menor teor de Zn. A corrente de soldagem tem efeito mínimo no teor de Zn na solda, com uma ligeira diminuição à medida que a corrente aumenta.
A soldagem com proteção a gás produz mais poeira de soldagem em comparação com a soldagem a arco manual, por isso é importante prestar atenção especial à exaustão. O tamanho e a composição da fuligem são influenciados principalmente pela corrente e pelo gás de proteção, com uma corrente maior ou uma quantidade maior de CO2 ou O2 no gás levando a mais fuligem. O teor de ZnO na fuligem também aumenta, com teor máximo em torno de 70%.
A profundidade fundida do aço galvanizado é maior que a do aço não galvanizado sob as mesmas especificações de soldagem. Juntas em T, juntas sobrepostas e soldagem descendente são mais propensas à porosidade, e a velocidade de soldagem tem um impacto significativo, especialmente para ligas de aço galvanizado. Na soldagem multilinha, as linhas de soldagem subsequentes são mais sensíveis à porosidade do que as linhas anteriores.
A composição do gás protetor tem pouco efeito nas propriedades mecânicas das juntas, e o CO2 puro é comumente usado para soldagem. Os parâmetros de soldagem para juntas de topo em forma de I, juntas sobrepostas e juntas em T de placas de aço galvanizado usando soldagem CO2 estão listados nas tabelas 1-3.
Tabela 1 Parâmetros de especificação para soldagem CO2 de junta de topo de placa de aço galvanizado em forma de I
Espessura/mm | Folga/mm | Posição de soldagem | Velocidade de alimentação do fio/mm*s-1 | Tensão do arco/V | Corrente de soldagem/A | Velocidade de soldagem/mm*s-1 | Observação |
---|---|---|---|---|---|---|---|
1.6 | 0 | Soldagem plana | 59,2~80,4 | 17~20 | 70~90 | 5.1~7.2 | Fio de soldagem ER705-3
Dia. 0,9mm Extensão seca 6,4 mm |
Soldagem descendente vertical | 82,5 | 17 | 90 | 5.9 | |||
Soldagem Horizontal | 50,8 | 18 | 100 | 8,5 | |||
Soldagem aérea | 50,8~55 | 18~19 | 100~110 | - | |||
3.2 | 0,8~1,5 | Soldagem plana | 71,9 | 20 | 135 | 5.5 | |
Soldagem vertical | 71,9 | 20 | 135 | 7.6 | |||
Soldagem Horizontal | 71,9 | 20 | 135 | 6.8 | |||
Soldagem aérea | 71,9 | 20 | 135 | 5.5 |
Tabela 2 Parâmetros de especificação para soldagem CO2 de junta sobreposta de placa de aço galvanizado
Espessura/mm | Posição de soldagem | Velocidade de alimentação do fio/mm*s-1 | Tensão do arco/V | Corrente de soldagem/A | Velocidade de soldagem/mm*s-1 | Observação |
---|---|---|---|---|---|---|
1.6 | Soldagem plana | 50,8 | 19 | 110 | 5.1~6.8 | Arame de soldaER705-3
Dia. 0,9mm Extensão seca 6,4 mm |
Soldagem Horizontal | 50,8 | 19~20 | 100~110 | 5,5~6,8 | ||
Soldagem aérea | 50,8 | 19~20 | 100~110 | 4.2~5.1 | ||
Soldagem vertical | 50,8 | 18 | 100 | 5,5~6,8 | ||
3.2 | Soldagem plana | 67,2 | 19 | 135 | 3.8~4.2 | |
Soldagem Horizontal | 67,2 | 19 | 135 | 3.8~4.2 | ||
Soldagem descendente vertical | 67,7 | 19 | 135 | 5.1 | ||
Soldagem aérea | 59,2 | 19 | 135 | 3.4~3.8 |
Tabela 3 Parâmetros de especificação para soldagem CO2 de junta de topo de placa de aço galvanizado em forma de T (junta angular)
Espessura/mm | Posição de soldagem | Velocidade de alimentação do fio/mm*s-1 | Tensão do arco/V | Corrente de soldagem/A | Velocidade de soldagem/mm*s-1 | Observação |
---|---|---|---|---|---|---|
1.6 | Soldagem plana | 50,8~55 | 18 | 100~110 | - | Arame de soldaER705-3
Dia. 0,9mm Extensão seca 6,4 mm |
Soldagem vertical | 55~65,6 | 19 | 110~120 | - | ||
Soldagem aérea | 55 | 19~20 | 110 | 5.9 | ||
Soldagem Horizontal | 59,2 | 20 | 120 | 5.1 | ||
3.2 | Soldagem plana | 71,9 | 20 | 135 | 4.7 | |
Soldagem Vertical | 71,9 | 20 | 135 | 5.9 | ||
Soldagem Horizontal | 71,9 | 20 | 135 | 4.2 | ||
Soldagem aérea | 71,9 | 20 | 135 | 5.1 |