O design leve é o futuro da produção: reduz as emissões de carbono e melhora o desempenho dos componentes.
Os benefícios ambientais e económicos substanciais da prossecução de inovações em design de peso leve garantem a sua importância contínua como uma área chave de investimento e investigação em muitas indústrias, tanto agora como nos próximos anos.
Este artigo apresenta uma visão geral dos materiais, técnicas e soluções futuras de design leve.
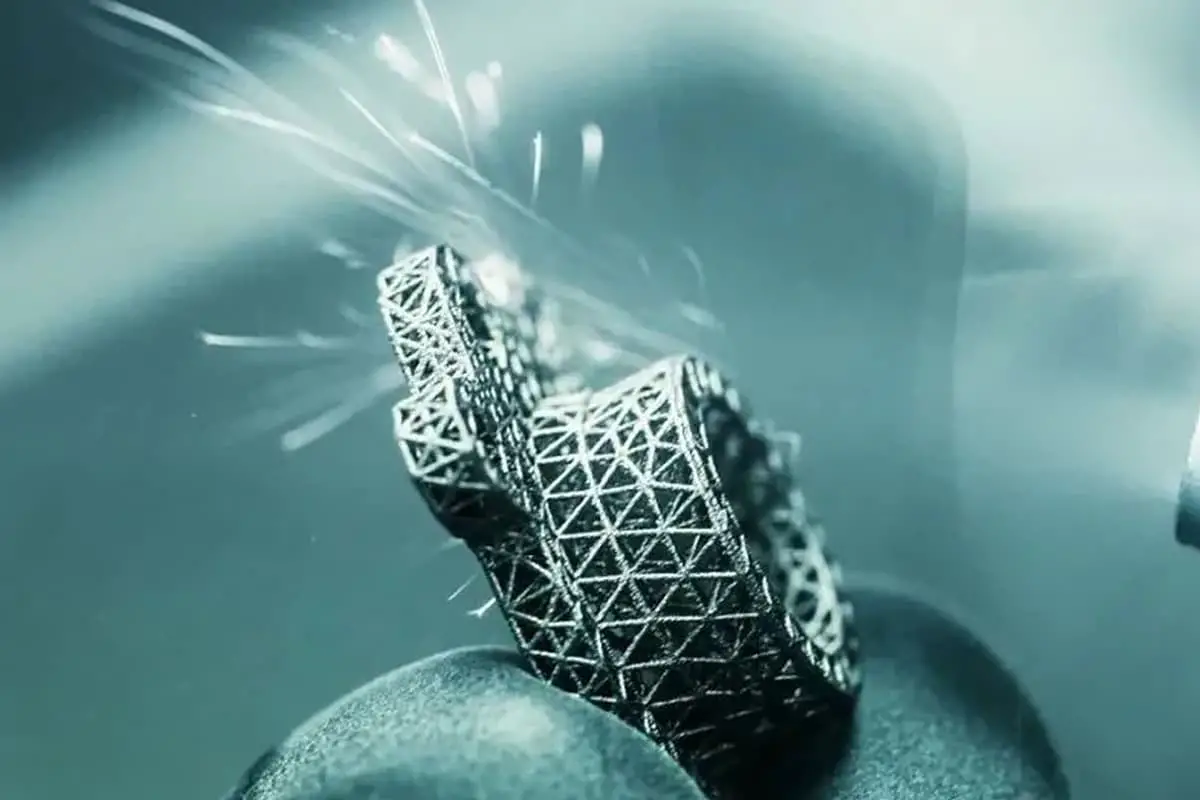
I. Valor Econômico do Design Leve
Essencialmente, o design leve é a prática de reduzir a quantidade de material num componente, sem comprometer a fiabilidade ou funcionalidade, para diminuir o seu peso total.
Atualmente, as nações de todo o mundo estão a impor exigências a todas as indústrias para reduzir o consumo de energia e as emissões de gases com efeito de estufa.
O design leve visa fornecer aos fabricantes a solução necessária para enfrentar os desafios das alterações climáticas, ao mesmo tempo que alcança um desempenho superior dos componentes e prolonga a vida útil do produto.
Mais comumente observado nas indústrias automotiva e aeroespacial, o design leve melhora a eficiência do combustível e aumenta o desempenho de aviões e veículos elétricos.
No entanto, vale a pena notar que o design leve também está a impulsionar a inovação nos setores da construção, das energias renováveis e da produção de produtos eletrónicos e elétricos. Componentes mais leves reduzem os custos de transporte e energia, e métodos de produção mais eficientes em termos de recursos são adotados em todos estes setores.
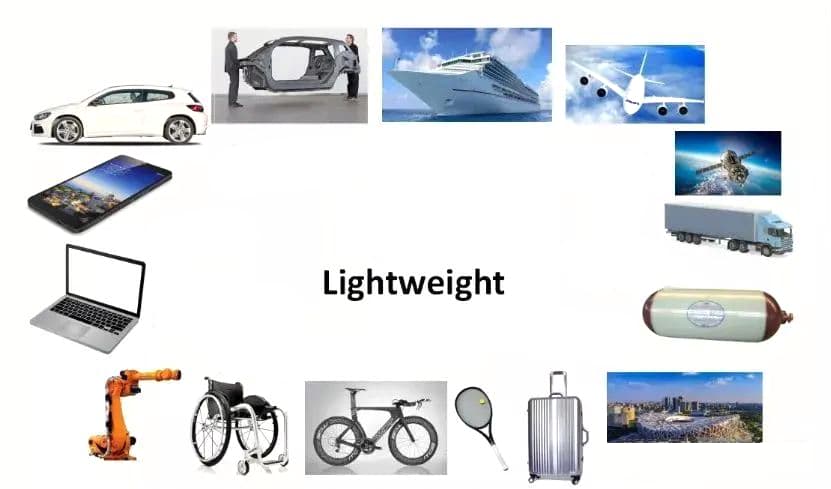
II. Materiais-chave em design leve
Materiais leves são aqueles que podem ser usados para diminuir o peso do produto e melhorar o desempenho geral do produto. A redução do peso do material envolve a redução do peso usando metais leves e não metais que atendam aos requisitos de desempenho mecânico.
No atual setor de fabricação automotiva, os materiais leves incluem principalmente ligas de alumínio, magnésio e titânio.
(1) Ligas de alumínio
O alumínio é amplamente utilizado na indústria automotiva devido às suas propriedades de leveza. Analistas da indústria automotiva sugerem que o uso de peças de liga de alumínio pode reduzir o peso do veículo em até 50% sem sacrificar a segurança ou o desempenho.
A maleabilidade, durabilidade e leveza do alumínio também o tornam um material popular para a fabricação de bens de consumo, eletrônicos e aviões.
À medida que as tendências dos veículos híbridos e eléctricos continuam, os fabricantes de automóveis continuarão a considerar o alumínio como o material de eleição devido ao seu baixo custo, elevado desempenho e características excepcionais de redução de peso.
(2) Ligas de Magnésio
As ligas de magnésio têm a densidade mais baixa de todos os metais estruturais, sendo 33% mais leves que o alumínio, 50% mais leves que o titânio e 75% mais leves que o aço, reduzindo potencialmente o peso dos componentes em até 70%.
O magnésio provou ser um material valioso para engenheiros de projetos leves. É fácil de processar, tem boa resistência estrutural e é amplamente utilizado nas indústrias automotiva e aeroespacial, bem como na fabricação de bens de consumo. No setor automotivo, o magnésio é atualmente usado em caixas de trem de força ou subcomponentes.
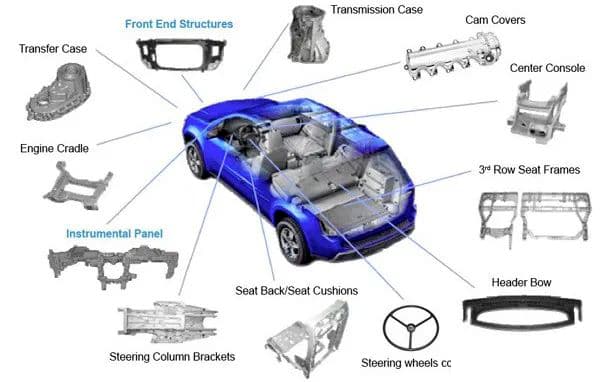
Sua baixa densidade e alta resistência específica significam que o magnésio é usado como componente leve em tudo, desde aviões e mísseis até laptops e TVs. Além de componentes e elementos estruturais, atualmente estão sendo desenvolvidas baterias à base de magnésio para a indústria automotiva.
Uma análise da US Automotive Materials Partnership indicou que 113 kg de magnésio poderiam substituir 226 kg de aço. 40 kg de magnésio poderiam substituir 68 kg de alumínio. Isto leva a uma redução no peso do veículo em 15%.
A China planeja aumentar a quantidade de componentes de magnésio utilizados na produção de veículos para 45 kg por veículo até 2030.
O mercado global de magnésio foi avaliado em US$ 4,115 bilhões em 2019 e deverá atingir US$ 5,9281 bilhões até 2027. A China produz cerca de 85% do magnésio mundial.
(3) Ligas de Titânio
O titânio tem excelente resistência à corrosão, propriedades antimagnéticas, boa blindagem contra campos elétricos e campos eletromagnéticos, resistência a temperaturas extremas e maior resistência à tração do que o aço, pesando apenas metade.
Nos últimos anos, a produção de ligas de titânio fez progressos significativos. Eles são usados para fabricar pás de turbinas, estruturas de aeronaves, resistores, placas de circuito, instrumentos cirúrgicos e muito mais. A indústria automotiva fabrica sistemas de escapamento, motores, transmissões e estruturas leves em liga de titânio.
Espera-se que a demanda global por titânio aumente de US$ 24,7 bilhões em 2021 para US$ 33,5 bilhões em 2026.
III. Inovação em Design Leve e Técnicas de Fabricação
À medida que diversas indústrias se esforçam para criar componentes mais leves para cumprir os seus objectivos ambientais, técnicas de fabrico inovadoras estão a impulsionar isto. As empresas estão buscando novos métodos para fabricar componentes de baixo custo e alto desempenho, e a reofundição está agora substituindo amplamente a tixocasting.
Uma das principais vantagens da reofundição é a sua capacidade de fundir metais com uma vasta gama de frações sólidas, produzindo de forma eficaz e econômica peças leves, com alta resistência e boa ductilidade.
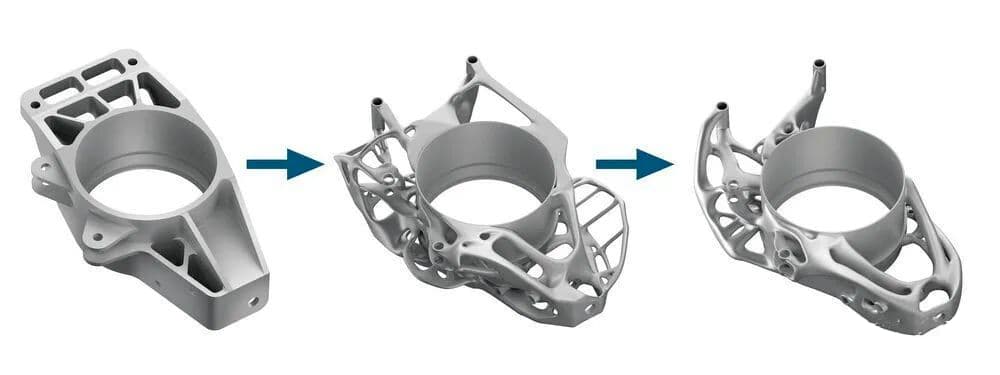
Os avanços nas tecnologias de fabricação aditiva (impressão 3D) concederam aos engenheiros uma liberdade de design sem precedentes. A manufatura aditiva permite que os fabricantes fabriquem geometrias complexas com custos significativamente reduzidos em comparação com as técnicas tradicionais de fundição sob pressão.
Também é utilizado para diminuir o peso da peça, transformando geometrias sólidas em estruturas ocas ou substituindo estruturas sólidas por designs de treliça interna. Na verdade, existe agora uma gama de peças leves que só podem ser produzidas utilizando técnicas de fabrico aditivo.
V. Soluções futuras para redução de peso
O futuro do design leve continuará a centrar-se na utilização de ligas de alumínio, magnésio e titânio, mas também incorporará materiais compósitos como carbono ou polímeros reforçados com fibra de vidro.
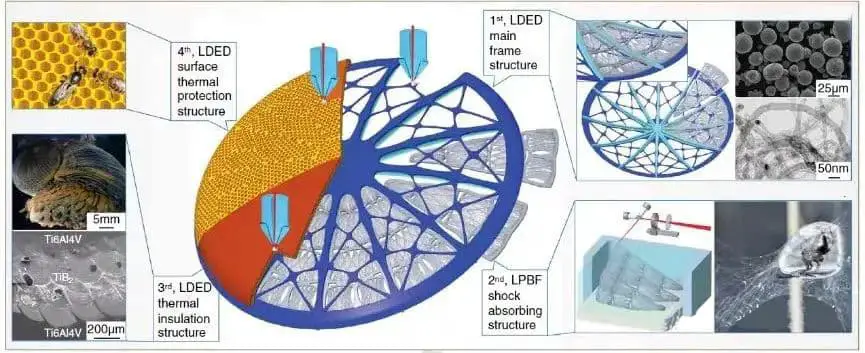
Muitas empresas estão atualmente concentrando-se no desenvolvimento de peças híbridas leves à base de plástico para as indústrias aeroespacial e automotiva.
As inovações em software de computador e tecnologias de fabricação aditiva permitirão o desenvolvimento de produtos, peças e estruturas mais leves.
Os engenheiros podem identificar áreas onde o peso pode ser reduzido de forma mais eficaz usando software especializado, alcançando a otimização máxima da topologia para uma variedade de componentes. Os modelos digitais 3D podem então testar o desempenho das peças leves para determinar as melhores opções de design.
O design biomimético e a biônica podem representar o futuro do design leve. Engenheiros e cientistas estão produzindo componentes baseados em estruturas leves e multifuncionais encontradas na natureza.
Exemplos disso incluem o avião-conceito Airbus 2050, que adotou uma fuselagem baseada em esqueleto. Pesquisas recentes concentram-se nos exoesqueletos do plâncton unicelular, estruturas em favo de mel, estruturas de caule de grama e células epidérmicas e asas de borboletas.
Ao combinar a inovação tecnológica e científica contínua com uma compreensão mais profunda da natureza, os fabricantes e as indústrias continuarão a desenvolver componentes mais leves e mais fortes para ajudar a humanidade a alcançar objectivos comuns de redução das emissões de CO2 e de resposta às alterações climáticas.