As chapas de metal são dobradas e formadas usando uma dobradeira de placas. A peça de trabalho é colocada na máquina e a alavanca de elevação é usada para levantar o bloco do freio, o que permite o posicionamento da peça de trabalho. O bloco do freio é então abaixado sobre a peça de trabalho e a alavanca de dobramento é pressionada para dobrar a chapa metálica.
O raio de curvatura mínimo é determinado pela ductilidade e espessura do metal que está sendo formado. Para chapas de alumínio, o raio de curvatura deve ser maior que a espessura da placa.
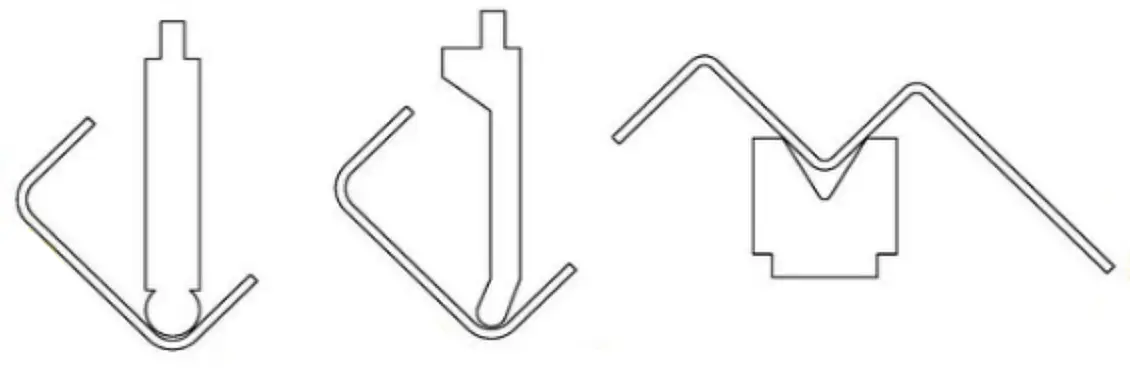
Devido à elasticidade, o ângulo de flexão do metal é ligeiramente maior que o ângulo necessário.
A dobra de chapas metálicas é normalmente realizada em uma oficina de processamento de metal. O processamento de chapas metálicas envolve uma série de técnicas, como dobra, rebitagem e soldagem de materiais metálicos.
Os problemas comuns que ocorrem durante este processo e suas soluções correspondentes são discutidos abaixo.
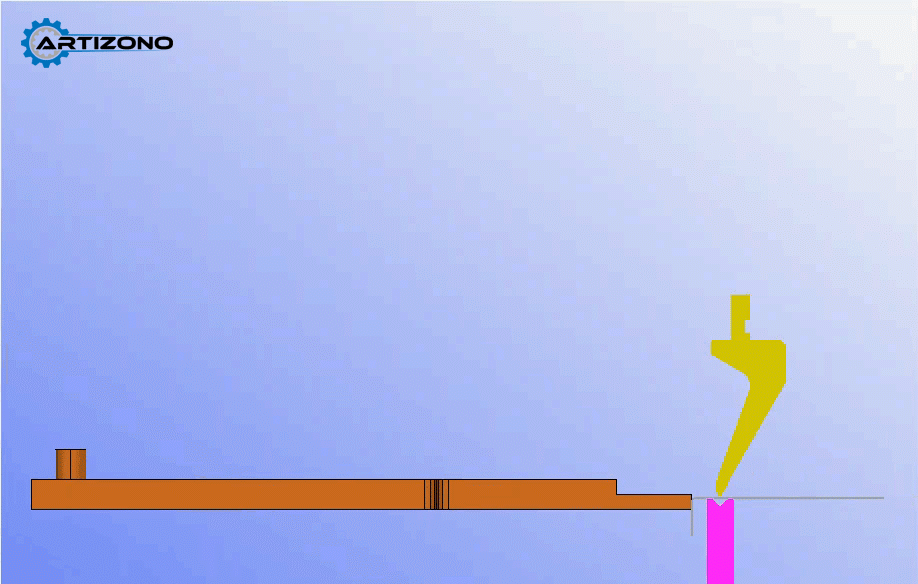
1. Desafios na flexão de peças do tipo ranhura e multidobra
Durante o processo de dobra dessas peças, a largura da ranhura é maior que a altura da perna, causando interferência entre uma extremidade da peça e a matriz superior ou o controle deslizante da prensa dobradeira. Isto impossibilita garantir as dimensões da peça, conforme mostra a Figura 2.
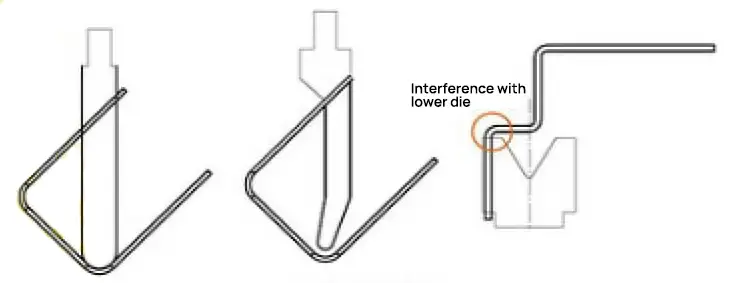
Previsão de interferência na dobra de chapa metálica
Ao lidar com peças de chapa metálica de precisão de perna alta, determinar se a dobra pode ser concluída requer vários cálculos, com as dimensões correspondentes indicadas na Figura 3.
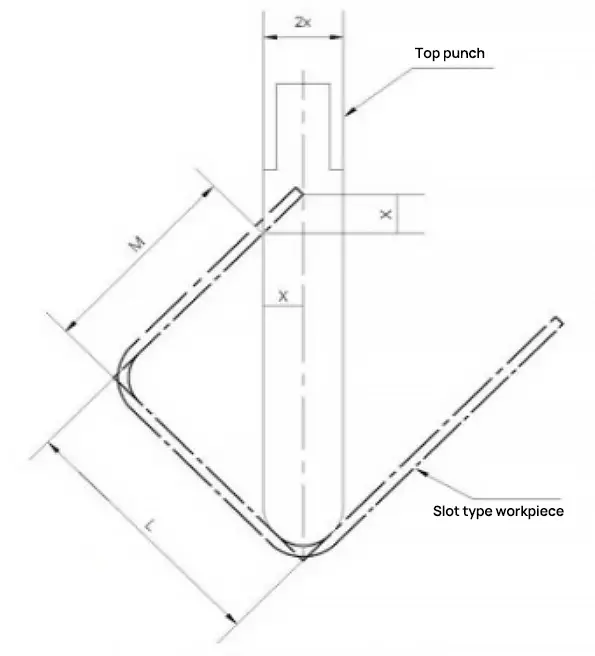
Se LM<1,5x, a peça pode ser dobrada sem interferência. Se LM>1,5x, a peça de trabalho não pode ser dobrada, pois isso causaria interferência.
Soluções para problemas de interferência
(1) Se uma peça de trabalho do tipo ranhura sofrer interferência de flexão, uma matriz superior com pescoço de ganso pode ser selecionada para flexão. Isso evita interferência entre a borda de dobra da peça e a prensa dobradeira ou matriz superior, garantindo as dimensões de dobra da peça, conforme mostrado na Figura 4.
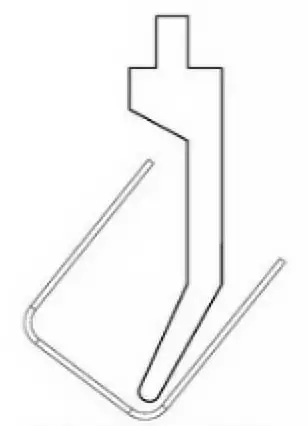
(2) Se uma peça de trabalho do tipo ranhura sofrer interferência de flexão e não houver matrizes superiores de pescoço de ganso adequadas disponíveis, uma pré-dobragem reversa pode ser realizada no meio da dobra sem afetar os requisitos de uso, conforme mostrado na Figura 5. Por aumentando artificialmente o ângulo de curvatura, a peça pode ser dobrada normalmente. Em seguida, uma matriz de pneu furado pode ser usada para pressionar a área de pré-dobra para garantir que os requisitos de qualidade do produto sejam atendidos.
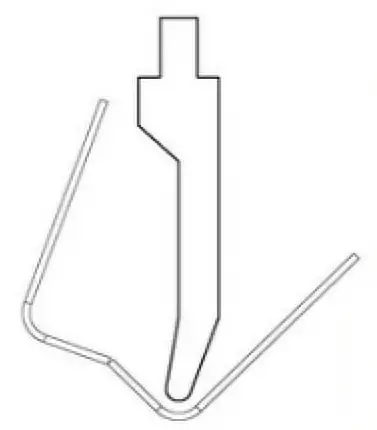
(3) Ao dobrar peças de trabalho com múltiplas dobras, se H1>H ou B
① Selecione uma matriz inferior de alta dimensão com H> H1 para garantir a flexão normal da peça de trabalho;
② Selecione uma abertura inferior da matriz com B>V/2 para garantir a flexão normal da peça de trabalho;
③ Se não houver matriz inferior de alta dimensão, altere a sequência de dobra. Pré-deforme a dobra intermediária em um determinado ângulo, depois dobre no lado curto, forme a terceira dobra e, finalmente, reprima a dobra intermediária no tamanho e ângulo necessários, garantindo o tamanho do processo da peça, conforme mostrado na Figura 6.
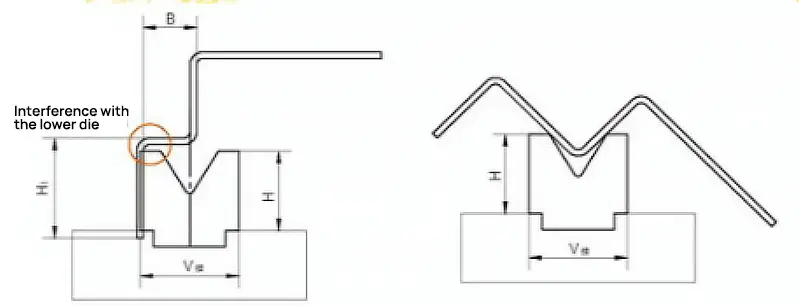
2. Fissuração por Dobra
(1) Análise das Causas
Freqüentemente, rachaduras por flexão ocorrem na superfície de tração das peças de chapa metálica durante a dobra, danificando as propriedades mecânicas da peça e não atendendo aos requisitos de uso, levando ao desmantelamento da peça e à perda econômica. Os principais motivos são:
① A chapa metálica tem uma estrutura cristalina especial e direção de grão rolante, e dobrar paralelamente à direção de grão pode facilmente causar fratura;
② O raio de curvatura R escolhido é muito pequeno;
③ O ângulo R da ranhura em forma de V da matriz inferior é pequeno;
④ O desempenho do material é ruim.
(2) Medidas Preventivas
① Ao cortar, gire a chapa para cortar na direção perpendicular à dobra (ou seja, a direção de dobra do material é perpendicular à fibra);
② Aumente o ângulo R da matriz superior;
③ Use uma matriz inferior com um grande ângulo R para processamento;
④ Escolha materiais de alto desempenho.
3. A borda dobrada não é reta e o tamanho é instável.
Análise de causa:
- nenhuma linha pressionando ou pré-dobrando.
- pressão inadequada do material
- filete de matriz convexo-côncavo dissimétrico e pressão de flexão irregular
- altura baixa
Soluções
- técnicas de prensagem de linha de design ou pré-dobra
- aumentar a força de levantamento
- folga uniforme na matriz convexa-côncava e no filete polido
- tornar a altura maior ou igual ao tamanho mínimo
4. A peça de trabalho é raspada após dobrar.
Análise de causa:
- superfície de material irregular
- raio de curvatura da matriz convexa muito pequeno
- folga de flexão muito pequena
Soluções
- melhorar a suavidade da matriz côncava
- aumentar o raio de curvatura da matriz convexa
- ajustar a folga de flexão
5. Existem rachaduras nos ângulos de curvatura
Análise de causa:
- raio de curvatura muito pequeno
- grão do material paralelo à linha de dobra
- rebarba da folha de trabalho estendendo-se para fora
- fraca remodelabilidade do metal
Soluções
- aumentar o raio de curvatura da matriz convexa
- alterar o layout de supressão
- fazendo rebarbas no filete interno da peça de trabalho
- recozimento ou uso de material macio
6. A flexão causa deformação do furo
Análise de causa:
Quando a flexão elástica é utilizada para posicionar o furo, a parte externa do braço de flexão é puxada por fricção na superfície do molde côncavo e na superfície externa da peça de trabalho, deformando o furo de posicionamento.
Soluções
- empregando flexão de forma
- aumentar a pressão da cobertura
- adicione uma manta de corrosão à placa de cobertura para aumentar o atrito e evitar que a peça de trabalho deslize ao dobrar
7. A superfície de dobra é mais fina
Análise de causa:
- filete de molde convexo-côncavo muito pequeno
- folga da matriz convexo-côncava muito pequena
Soluções
- aumentar o raio do filete da matriz convexo-côncavo
- ajuste a folga da matriz convexo-côncava
8. A superfície da peça de trabalho está saliente ou irregular
Análise de causa:
Sob a tensão na direção circunferencial, a superfície externa do material encolhe enquanto a superfície interna se estende durante a flexão, formando protuberâncias na direção da flexão.
Soluções
- fornecer pressão adequada à matriz convexa-côncava na fase final de estampagem
- tornar o raio do ângulo redondo côncavo igual ao do círculo externo da peça de trabalho
- otimizar técnicas
9. A parte côncava é irregular na parte inferior
Análise de causa:
- material irregular
- pequena área de contato entre a cobertura e o material ou força de levantamento inadequada
- nenhum dispositivo de suporte de material na matriz côncava
Soluções
- materiais de nivelamento
- ajuste o dispositivo de suporte de material e aumente a força de levantamento
- aumentar ou corrigir dispositivo de suporte de material
- aumentar os processos de modelagem
10. Os eixos dos furos nos dois lados ficam desalinhados após a flexão
Análise de causa:
O rebote do material altera o ângulo de curvatura, desalinhando a linha central.
Soluções
- aumentar o processo de correção
- melhorar a estrutura do modelo de flexão para reduzir o rebote do material
11. A posição precisa do furo não pode ser garantida após a dobra
Análise de causa:
- tamanhos de desdobramento incorretos
- retorno elástico do material
- posicionamento instável
Soluções
- calcule o tamanho do espaço em branco com precisão
- aumentar o processo de correção ou melhorar a estrutura da matriz de flexão
- alterar métodos de processamento ou melhorar o posicionamento
12. A linha de dobra não é paralela ao centro de dois furos
Análise de causa:
Quando a altura de dobra é menor que a altura mínima de dobra, a peça dobrada ocorre expansão.
Soluções
- aumentar a altura da peça a ser dobrada
- melhorar técnicas de flexão
13. A deformação ocorre em termos de largura após a flexão (a parte dobrada ocorre deflexão do arco em largura)
Análise de causa:
A profundidade inconsistente e o encolhimento na largura da peça causam torção e deflexão.
Soluções
- aumentar a pressão de flexão
- aumentar o processo de correção
- garantir um certo ângulo entre materiais e direção de dobra
14. Peça de trabalho com incisão ocorre deflexão para baixo
Análise de causa:
A incisão faz com que as duas bordas retas se abram para o lado esquerdo e direito, formando uma deflexão na parte inferior.
Soluções
- melhorar a estrutura da peça
- aumentar a margem de processamento nas incisões para conectar as incisões e, em seguida, cortar o processo após dobrar
15. Material deslizante durante o processamento
Análise de causa:
Ao selecionar a matriz de dobra, normalmente é escolhida uma largura de ranhura em V de 4 a 6 vezes a espessura do material (T). No entanto, se o tamanho da dobra for menor que metade da largura da ranhura em V selecionada, poderá ocorrer deslizamento.
Problema: A ranhura em V selecionada é muito grande.
Soluções:
- Método de desvio de linha central (usinagem excêntrica). Quando o tamanho do material a ser dobrado for menor que a metade de 4 a 6 vezes T, aumente o máximo possível.
- Processamento de preenchimento
- Dobre com uma ranhura em V pequena e pressione com uma ranhura em V grande.
- Selecione uma ranhura em V menor.
16. A largura de dobra interna é mais estreita que a do molde padrão
Análise de causa:
A largura padrão da matriz inferior da dobradeira deve ser de pelo menos 10 mm. Portanto, o material a ser dobrado deve ter menos de 10 mm de espessura. Se a curva tiver um ângulo de 90 graus, seu comprimento não deve ser inferior a √2 (L + V / 2) + T.
Para evitar o deslocamento do molde e qualquer sucata resultante ou acidentes de segurança, o molde deve ser fixado com segurança na base do molde, com exceção de qualquer grau de liberdade ascendente.
Soluções:
- Aumente o tamanho da dobra negociando com o cliente e alargando a dobra interna.
- Processamento especial do molde.
- Use ferramentas de retificação, embora isso aumente os custos de processamento.
17. O furo está muito próximo da linha de dobra. Dobrar fará com que o furo puxe e gire o material
Análise de causa:
Suponha que a distância do furo à linha de dobra seja L. Se L for menor que (4 a 6) vezes a espessura da placa T dividida por 2, o material sofrerá tração. Isso ocorre porque durante o processo de flexão, a força de tração deforma o material, causando tração e distorção.
O valor mínimo de L para diferentes espessuras de chapa, baseado na largura padrão da ranhura do molde, é o seguinte:
Soluções:
- Aumente o tamanho da dobra e apare a bainha após a formação.
- Expanda o furo até a linha de dobra, mas somente se isso não afetar a aparência ou função e o cliente concordar.
- Use processamento secante ou de crimpagem.
- Processe excentricamente o molde.
- Modifique o tamanho do furo.
18. A distância L entre a aresta desenhada e a linha de dobra é pequena, e o local da aresta desenhada é deformado após a dobra
Análise de causa:
Quando L é menor que (4 a 6) vezes a espessura da placa T dividida por 2, o material sofrerá deformação durante o processo de dobra devido ao contato entre o material e o molde inferior.
Soluções:
- Use processamento secante ou de crimpagem.
- Modifique o tamanho do material.
- Empregue processamento de molde especial.
- Processe excentricamente o molde.
19. O lado longo e achatado sobe após o achatamento
Análise de causa:
A longa borda de achatamento pode não aderir firmemente durante o processo de achatamento, fazendo com que suba nas extremidades. Esta questão depende em grande parte da posição de achatamento, por isso é importante prestar muita atenção à posição de achatamento.
Soluções:
- Primeiro dobre o ângulo para cima (conforme mostrado no diagrama) antes de dobrar a borda morta e, em seguida, alise-o.
- Achate em várias etapas.
- Pressione a extremidade primeiro para dobrar o lado morto para baixo.
- Achate a parte raiz.
Precauções:
A qualidade do processo de achatamento depende das habilidades do operador, por isso é importante prestar muita atenção à situação real durante o achatamento.
20. Ponte levadiça de grande altura é fácil de quebrar
Análise de causa:
O material está severamente esticado e fraturado devido à alta altura da ponte levadiça. Outras causas podem incluir:
- Afiação insuficiente ou cantos de moldes especiais opacos.
- Baixa tenacidade do material ou ponte levadiça estreita.
Soluções:
- Aumente o orifício do processo em um lado da fratura.
- Aumente a largura da ponte levadiça.
- Repare o ângulo R do molde especial e aumente a transição do arco.
- Adicione lubrificante à ponte levadiça. Observe que este método sujará a superfície da peça de trabalho e não pode ser usado para peças AL, etc.
21. Durante o processamento especial do molde, o tamanho do processamento mudará
Análise de causa:
A peça é deslocada para frente durante o processamento devido a uma força de pressão para frente, causando um aumento no pequeno ângulo L da porção frontal.
Soluções:
- Remova todas as sombras da imagem e tente compensar o máximo possível.
- Substitua as peças desgastadas de autoposicionamento do molde por estruturas de retorno para melhor posicionamento.
22. O tamanho total do blanking (referindo-se à expansão) é muito pequeno ou muito grande, o que não é consistente com a superfície redonda
Análise de causa:
- Erro de implantação do projeto.
- Tamanho de alimentação incorreto.
Soluções:
- Calcule o desvio atribuído a cada curva com base no desvio total e no número de curvas na direção do desvio.
- Se a tolerância de distribuição calculada estiver dentro da faixa de tolerância, a peça será considerada aceitável.
- Se o tamanho for muito grande, use uma pequena ranhura em V.
- Se o tamanho for muito pequeno, use uma ranhura em V grande.
23. Lascar ou soltar o furo após a rebitagem e causar deformação
Análise de causa:
- A fragmentação ocorre devido a um pequeno ângulo R do furo de extração ou rebarbas excessivas no flange.
- A rebitagem está solta porque os furos de extração não estão devidamente alinhados.
- A deformação é causada por furos desalinhados ou método de rebitagem incorreto.
Soluções:
- Use um punção central com um ângulo R maior e preste atenção às rebarbas ao redor do furo de extração ao flangear.
- Aumente a pressão, aprofunde o brochamento e use um punção central com ângulo R maior.
- Aborde a causa raiz dos furos desalinhados e do método de rebitagem incorreto.
24. A rebitagem do pino está torta ou a peça de trabalho está deformada após a rebitagem
Análise de causa:
- A peça de trabalho não fica achatada durante o processamento.
- Força irregular ou pressão excessiva é aplicada à superfície inferior da peça de trabalho.
Soluções:
- Achate a peça de trabalho ao pressionar o pino.
- Use uma estrutura de suporte.
- Reajuste a pressão.
- Aumente a faixa de tensão na superfície inferior e reduza a faixa de força na superfície superior.
25. Os dois lados não são paralelos após a flexão deslocada
Análise de causa:
- O molde não está calibrado corretamente.
- As juntas superior e inferior da matriz não estão ajustadas corretamente.
- As faces superior e inferior da matriz não são idênticas.
Soluções:
- Recalibre o molde.
- Ajuste as juntas aumentando ou diminuindo-as.
- Use processamento excêntrico para o molde.
- Certifique-se de que o molde superior e inferior tenham a mesma superfície.
26. O vinco da superfície do produto é muito profundo
Análise de causa:
- Pequena ranhura em V na matriz inferior.
- Pequeno ângulo R da ranhura em V na matriz inferior.
- O material é muito macio.
Soluções:
- Use uma ranhura em V grande para processamento.
- Use um molde com um ângulo R grande.
- Use dobramento de preenchimento (com metal ou poliuretano fundido).
27. A área próxima à dobra foi deformada após a dobra
Análise de causa:
A máquina funciona muito rápido durante o processo de dobra, fazendo com que a velocidade de dobra ascendente durante a deformação da peça seja maior do que a velocidade com que o operador segura a peça com a mão.
Soluções:
- Reduza a velocidade de funcionamento da máquina.
- Aumente a velocidade de retenção manual do operador.
28. As peças AL são propensas a rachar quando dobradas
O material AL tem tendência a quebrar ao longo de linhas paralelas durante a flexão devido à sua estrutura cristalina especial.
Soluções:
- Ao moldar, gire o material AL de modo que a direção da dobra fique perpendicular à textura e depois corte.
- Aumente o ângulo R da matriz superior.
Leitura relacionada: 12 soluções para problemas de dobra de chapas metálicas
1 commento
Como dobra Chapa com espessura de 8 mm se a tira estiver empenada