As estruturas de suporte são um componente essencial para a fabricação bem-sucedida de peças impressas em 3D.
Apesar de uma das principais vantagens da impressão 3D ser a sua capacidade de criar formas geométricas complexas e de forma livre, grande parte da liberdade de design oferecida pela impressão 3D é difícil de realizar sem o uso de estruturas de suporte.
Eles são cruciais para evitar distorção e colapso de peças, entre outros usos; portanto, compreender e projetar estruturas de suporte é uma habilidade necessária para qualquer engenheiro de manufatura aditiva.
Este artigo discute os requisitos, prós e contras, remoção e como minimizar o uso de estruturas de suporte em diversas tecnologias de impressão.
A importância das estruturas de suporte na impressão 3D
Utilizadas em conjunto com praticamente todas as tecnologias de impressão 3D, as estruturas de suporte desempenham um papel crucial para garantir a capacidade de impressão das peças durante o processo de impressão 3D.
Os suportes ajudam a evitar a deformação das peças, fixam-nas à base de impressão e garantem a sua ligação ao corpo principal das peças impressas. Muito parecido com um andaime, esses suportes são utilizados durante o processo de impressão e removidos posteriormente.
Imprimir peças com recursos de design complexos, como saliências, furos e pontes, apresenta desafios significativos.
Tomemos como exemplo a impressão 3D de metal; quando a impressão inclui saliências ou estruturas de ponte, pode ocorrer deformação, até mesmo colapso, durante o processo se as estruturas de suporte não forem utilizadas.
Estas estruturas de suporte ajudam a evitar o colapso das peças formadas durante a impressão, aumentando consideravelmente a taxa de sucesso da impressão. No entanto, nem todas as estruturas pendentes necessitam de suporte adicional.
Se o ângulo vertical da saliência for inferior a 45 graus, não é necessário qualquer suporte.
Quando o ângulo vertical de tal estrutura é inferior a 45 graus, a impressora 3D possui deslocamento horizontal mínimo em camadas sucessivas, permitindo que cada camada forneça suporte para o próximo nível.
Portanto, 45 graus é um ângulo crítico, abaixo do qual nenhum suporte é necessário. Claro, isso também depende do desempenho da impressora e das propriedades dos materiais utilizados. Se o desempenho da impressora for inferior, poderá ser necessário suporte mesmo para ângulos inferiores a 45 graus.
Além disso, tecnologias como a impressão 3D de metal geralmente envolvem processos de alta temperatura, durante os quais o suporte também pode servir como dissipador de calor.
Isso ocorre porque as estruturas de suporte adicionadas durante o processo de fabricação aditiva metálica ajudam a afastar o calor da peça, evitando a formação de tensões residuais devido às altas temperaturas durante a impressão e evitando defeitos como deformações, empenamentos e trincas.
Claro, não é apenas a impressão 3D em metal que considera a adição de suportes; quase todas as tecnologias de impressão 3D precisam contemplar, até certo ponto, a inclusão de estruturas de suporte.
A tabela a seguir ilustra as diferenças no uso de suporte entre vários métodos de impressão 3D:
Princípios Técnicos | Materiais | É necessário suporte? |
Fusão seletiva a laser (SLM) Sinterização direta a laser de metal (DMLS) Deposição direta de energia (DED) Fusão por feixe de elétrons (EBM) | Materiais Metálicos | Sim |
Estereolitografia (SLA) | Fotopolímero | Sim |
Sinterização Seletiva a Laser (SLS) | Materiais em Pó | Não |
Jateamento de materiais | Materiais em Pó | Sim |
Modelagem de Deposição Fundida (FDM) | Plástico Termoplástico | Sim |
Spray adesivo | Materiais em Pó | Não |
Fusão em leito de pó (SLM, DMLS, EBM)
As estruturas de suporte são indispensáveis na impressão 3D de metal. Apesar dos componentes formados pela tecnologia de fusão em leito de pó serem rodeados por pó solto, o que proporciona algum suporte, estas tecnologias necessitam sempre de suporte para garantir a sua fixação à base e para mitigar os efeitos da tensão residual.
Sem estruturas de suporte, componentes salientes ou inclinados, bem como o estresse interno do metal, podem danificar o próprio objeto impresso, levando à falha na impressão. Geralmente, as estruturas de suporte na tecnologia de impressão baseada em leito de pó são divididas principalmente em dois tipos:
Apoio linear: Este tipo de apoio consiste em colunas verticais ligadas a toda a estrutura saliente. Porém, este tipo de suporte é mais difícil de remover.
Suporte semelhante a uma árvore: Este tipo de suporte lembra o formato de galhos de árvores. É usado para apoiar as partes salientes do componente. Está conectado apenas às posições salientes.
Sua vantagem é que é mais fácil de desmontar e não causa danos ao próprio componente.
No entanto, deve-se notar que as estruturas de suporte em forma de árvore só são adequadas para saliências não planas. Para saliências planas, elas não podem fornecer suporte suficiente.
O suporte pode ser adicionado na área de contato entre a parte inferior da peça impressa e a base de impressão, onde a tensão residual é mais concentrada.
Isso ajuda a afastar o calor da peça, minimizando assim a deformação térmica que pode causar rachaduras, empenamento, flacidez, delaminação e encolhimento.
Deposição Direta de Energia (DED)
A Deposição Direta de Energia é um processo que fabrica peças fundindo diretamente o material e construindo-o camada por camada.
Ao contrário das peças formadas pela fusão do leito de pó que são suportadas pelo leito de pó circundante, as peças impressas usando DED existem independentemente no espaço tridimensional.
Conseqüentemente, eles também exigem estruturas de suporte para garantir a estabilidade da peça, a capacidade de impressão de recursos complexos e a dissipação de calor.
1. Projeto de suporte
Ao projetar suportes para peças produzidas com tecnologia de fusão em leito de pó, é crucial garantir que eles possam ser facilmente separados do corpo principal, caso contrário, não poderão ser removidos durante o pós-processamento.
Os suportes para peças metálicas são normalmente impressos como uma estrutura de grade.
Dessa forma, atuam como dissipadores de calor, transferindo o calor da peça, permitindo seu resfriamento de forma mais controlada e evitando distorções, além de economizar custos de material e tempo de construção.
Adicionar mais suportes geralmente resulta em peças mais precisas, mas também aumenta os custos e o tempo de pós-processamento. Curiosamente, a empresa holandesa MX3D criou uma ferramenta de impressão 3D metálica que combina um braço robótico multieixos com uma máquina de soldar, permitindo a impressão de peças metálicas sem a necessidade de quaisquer suportes.
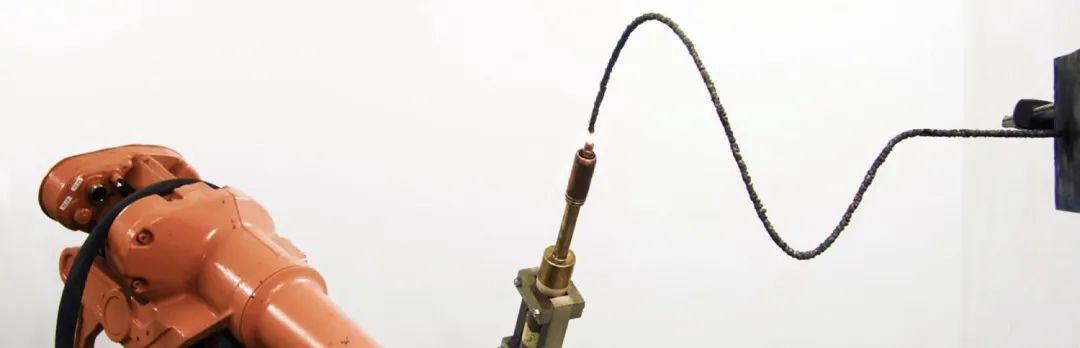
2. Remoção de suporte
A remoção de suportes de peças metálicas geralmente é mais desafiadora do que processos baseados em polímeros e normalmente requer ferramentas de corte.
Além disso, se a aparência da peça acabada for importante, o pós-processamento (como polimento) da peça metálica é necessário para obter um acabamento superficial liso.
Durante a desmontagem do modelo, a maioria dos suportes são fáceis de remover se o método estiver correto. Primeiro, você pode abrir suavemente os colchetes com os dedos, onde for possível manipulá-los manualmente.
Para posições especiais, podemos optar por utilizar ferramentas para desmontar os suportes, incluindo alicates de bico fino, raspadores e facas de trinchar.
Estereolitografia (SLA)
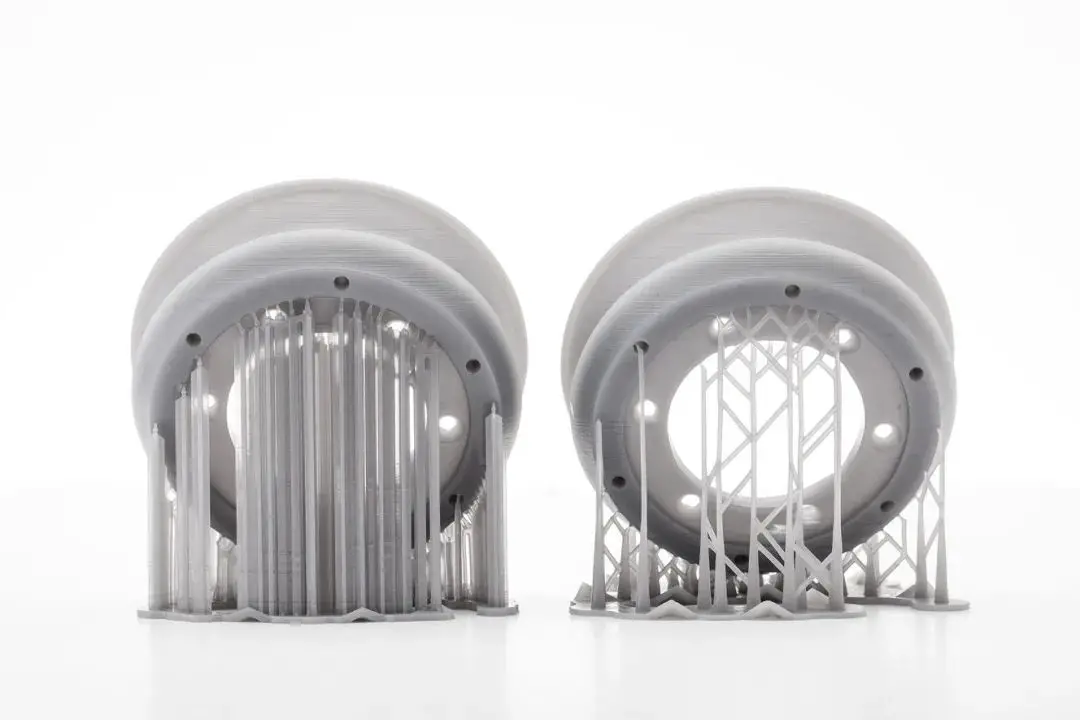
A estereolitografia funciona usando uma fonte de luz para solidificar a resina líquida. Esta tecnologia requer estruturas de suporte para fixar firmemente as peças à base de impressão e evitar empenamentos.
Os suportes utilizados no SLA são muito finos e tocam levemente as peças para economizar materiais. Isso significa que eles podem ser facilmente removidos manualmente, com a mão ou com um alicate. Porém, como a remoção dos suportes deixará marcas na peça final, é necessário lixá-la para garantir um acabamento superficial liso.
1. Projeto de suporte
O SLA é frequentemente usado para aplicações que exigem estética ou acabamentos de superfície lisos, como protótipos visuais, moldes e aparelhos auditivos.
Se for esse o caso, é fundamental projetar as peças para garantir que a área frontal da impressão não entre em contato com as estruturas de suporte. É aqui que o design de orientação das peças entra em ação.
A orientação das peças é uma consideração crucial na fase de projeto porque o reposicionamento das peças pode ajudar a reduzir a quantidade de suporte necessária. Por exemplo, peças tubulares, se colocadas horizontalmente, ocuparão mais espaço e, portanto, necessitarão de mais suporte.
Por outro lado, posicionar a mesma peça verticalmente garante que ela se conecte à placa de construção com suporte mínimo.
Modelagem de Deposição Fundida (FDM)
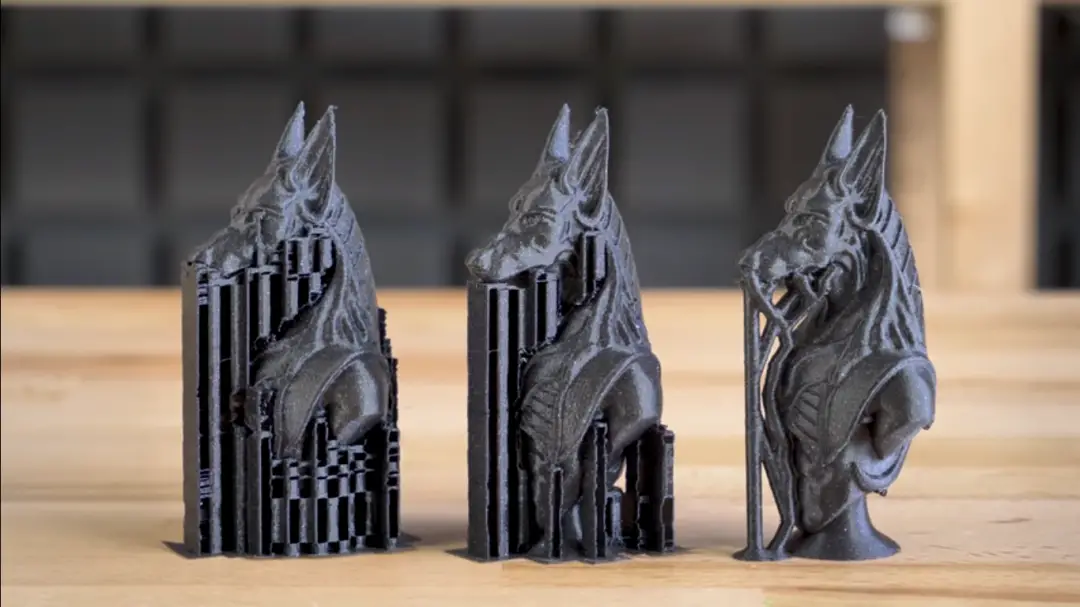
A tecnologia Fused Deposition Modeling (FDM) cria peças extrusando filamentos aquecidos camada por camada, cada uma das quais se liga à anterior após resfriamento e solidificação.
1. Projeto de suporte
No processo FDM, cada camada se projeta ligeiramente para que possa se estender além da largura da camada anterior. Isso significa que recursos podem ser criados em ângulos de até 45 graus sem suporte.
No entanto, quando o balanço de uma peça FDM excede 45 graus ou a peça inclui recursos como pontes e superfícies salientes maiores que 5 milímetros, é necessário suporte. O suporte no FDM pode assumir a forma de uma estrutura em treliça ou de uma estrutura em forma de árvore.
2. Remoção de suporte
Uma técnica para remover suportes de impressões FDM é através de uma solução de dissolução química.
Normalmente, as impressoras 3D FDM industriais (com duas cabeças de impressão) utilizam materiais de suporte solúveis, como Álcool Polivinílico (PVA) e Poliestireno de Alto Impacto (HIPS). Esses materiais podem ser depositados no modelo usando uma extrusora separada.
Embora o PVA se dissolva na água, ele pode ser afetado pelas mudanças de temperatura, causando bloqueios no cabeçote de impressão. O HIPS, por outro lado, dissolve-se em limoneno em vez de água e não é facilmente afetado pelas mudanças de temperatura.
A utilização de suportes solúveis elimina a necessidade de operações manuais e a necessidade de lixamento e polimento adicionais para remover vestígios deixados pelos suportes. Por outro lado, este processo pode ser demorado (levando várias horas) e dispendioso.
Jateamento de materiais
Ao usar uma impressora 3D Material Jetting, é sempre necessário suporte para estruturas salientes, independentemente do ângulo.
No entanto, estes suportes são normalmente feitos de diferentes materiais que são solúveis em água ou podem ser facilmente removidos posteriormente com água pressurizada ou por imersão num banho ultrassónico.
Sinterização seletiva a laser e jato de ligante
A Sinterização Seletiva a Laser e o Binder Jetting são tecnologias à base de pó que geralmente não requerem estruturas de suporte.
Isso porque nessas duas tecnologias as peças impressas são encapsuladas em pó solto que serve como estrutura de suporte.
Desvantagens dos suportes
Embora necessárias, as estruturas de suporte aumentam o tempo geral de impressão e os custos de material do processo de produção.
Despesas materiais:
A geração de suportes necessita de material adicional durante o processo de impressão, aumentando assim o tempo e os custos de material. Igualmente importante é o facto de os suportes não serem reutilizáveis e normalmente serem descartados, levando ao desperdício de material.
Liberdade geométrica limitada:
Ao remover suportes manualmente, a utilização de mãos ou ferramentas deve ser considerada durante o projeto dos suportes. No entanto, isso pode limitar sua capacidade de projetar certas formas geométricas que requerem suporte, mas são inacessíveis manualmente ou com ferramentas.
Tempo adicionado:
Projetar uma peça para acomodar estruturas de suporte e, em seguida, criar os próprios suportes exige mais tempo. Apesar da disponibilidade de softwares que geram suportes automaticamente, a criação de estruturas de suporte para aplicações industriais ainda requer modificações manuais e um certo nível de conhecimento em design.
Pós-processamento adicional:
Uma vez concluída a peça, os suportes devem ser removidos, às vezes manualmente, aumentando assim o tempo necessário para o pós-processamento.
Risco de Danos: Durante a fase de pós-processamento, os suportes devem ser removidos e a superfície da peça deve ser polida.
Qualquer manuseio incorreto durante a desmontagem dos suportes pode causar defeitos na superfície da peça, afetando sua precisão dimensional e aspecto estético.
Além disso, quando os apoios são colocados incorretamente, como em estruturas finas, podem ocorrer fraturas estruturais. Eles podem quebrar junto com as estruturas de suporte, levando à falha total da impressão.
Portanto, o emprego de estruturas de suporte apresenta certas desvantagens e só deve ser adicionado quando necessário.
Além disso, também podemos evitar o uso de suportes chanfrados. A chanfragem transforma os locais dos balanços em balanços seguros com ângulos inferiores a 45 graus, dispensando a necessidade de suportes e garantindo a utilização eficiente do material.
Quatro métodos para minimizar suportes
Reduzir o número de apoios necessários é muitas vezes uma estratégia sólida. Ajuda a economizar custos de material e tempo de produção. Aqui estão quatro dicas essenciais sobre como maximizar sua redução, economizando tempo de impressão e materiais:
1. Escolha a orientação ideal da peça
Experimentar a orientação das peças é uma das melhores maneiras de diminuir o número de suportes necessários. A orientação correta impacta significativamente o tempo de impressão, o custo e a rugosidade da superfície da peça.
Dependendo da direção da peça (vertical, horizontal ou angular), podem ser necessários menos ou mais apoios.
Considere uma peça impressa no formato da letra ‘T’. Posicionados em sua direção regular, ambos os braços da carta entrariam em colapso sem estruturas de suporte. Contudo, se a orientação da peça for invertida – disposta numa posição de “T” invertida – não é necessário qualquer suporte.
Este exemplo ilustra que uma peça pode ser construída de diversas maneiras. Cada face da peça pode ter uma superfície diferente conectada à base de impressão, implicando em diversas necessidades de suporte. Essas necessidades dependem em grande parte da orientação da peça.
Outro exemplo: ao projetar peças com características tubulares ocas, uma orientação horizontal ocupa mais espaço, enquanto uma orientação vertical ou angular economiza espaço e reduz o número de suportes necessários.
2. Otimizando estruturas de suporte
Quando os suportes são inevitáveis, devem ser otimizados para utilizar o mínimo de material possível e acelerar o processo de impressão. Por exemplo, pode-se utilizar projeto de otimização de topologia e suporte de estrutura treliçada para reduzir o volume de suportes, economizando assim material.
Para muitos processos de impressão 3D, as técnicas convencionais de geração de suporte limitam-se à produção de estruturas estritamente verticais. Eles não economizam espaço, especialmente quando há muitas áreas acima da base de impressão que precisam de suporte.
Contrariamente, a criação de estruturas de suporte semelhantes a árvores pode ser uma escolha viável. Esses suportes lembram uma árvore ramificada e podem reduzir o uso de material em aproximadamente 75% em comparação com estruturas verticais retas.
Autodesk Meshmixer é uma das ferramentas de software disponíveis para criar tais estruturas para processos FDM, SLA e DMLS.
3. Utilizando Filetes e Chanfros
Filetes e chanfros podem servir como soluções alternativas para a criação de estruturas de suporte em superfícies salientes que excedam 45 graus.
Um chanfro é um canto ou aresta angular ou chanfrado, enquanto um filete é um canto ou aresta arredondado. Essencialmente, esses recursos alteram ângulos maiores que 45 graus para ângulos de 45 graus ou menos e podem ser adicionados ao interior ou exterior de uma peça.
4. Segmentação de peças impressas
Para modelos 3D altamente complexos, muitas vezes faz sentido imprimir as peças individualmente e depois montá-las. Isto não só reduz o número de suportes, mas também acelera o processo de impressão, poupando material.
No entanto, tenha em mente que se forem montadas peças impressas em 3D, elas devem ser impressas na mesma orientação para garantir um encaixe adequado entre si.
Suportes de impressão 3D: necessários, mas frustrantes
Durante muito tempo, as estruturas de suporte foram vistas como uma “desvantagem” inevitável na impressão 3D. No entanto, os avanços recentes em hardware e software estão desafiando lentamente esta noção.
Vejamos, por exemplo, a Desktop Metal, fabricante de impressoras 3D de metal, que desenvolveu recentemente uma solução conhecida como “Suportes Separáveis” para seus sistemas de estúdio e produção, garantindo uma patente no processo.
Esses suportes para peças metálicas impressas em 3D podem ser removidos manualmente. Os Suportes Separáveis da Desktop Metal operam utilizando uma camada de pó cerâmico como interface entre a superfície da peça e a estrutura de suporte.
Após o processo de sinterização, a camada cerâmica se dissolve, permitindo a remoção sem esforço dos suportes da peça.
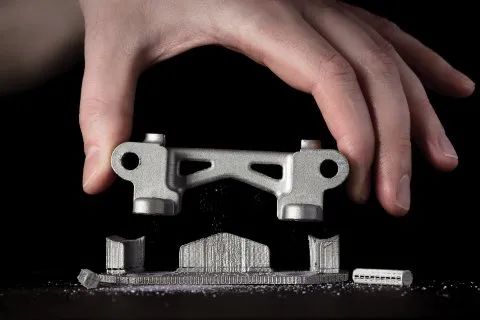

PostProcess Technologies é outra empresa que visa simplificar e acelerar a etapa de remoção de suporte para peças impressas em 3D. A empresa oferece uma gama de soluções de remoção de suporte automatizadas e sem uso das mãos para peças fabricadas aditivamente através das tecnologias FDM, SLA, PolyJet e CLIP.
No entanto, uma empresa foi ainda mais longe no domínio do suporte. Velo3D, empresa por trás do sistema Sapphire de fusão em leito de pó, oferece uma tecnologia chamada Intelligent Fusion para seu sistema, que permite a impressão de peças metálicas complexas, com foco na obtenção de impressão quase sem suporte.
Em comparação com outros sistemas de leito de pó metálico, o uso do software de simulação proprietário da Velo3D e o monitoramento de circuito fechado podem reduzir os suportes necessários para a produção de peças em até cinco vezes.
Em 2021, a SLM Solutions lançou a “Tecnologia FreeFloat Supportless”, que reduz ou elimina significativamente a necessidade de estruturas de suporte na impressão de peças por meio da integração unificada de múltiplas tecnologias.
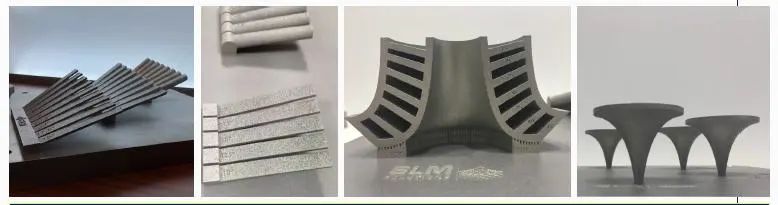
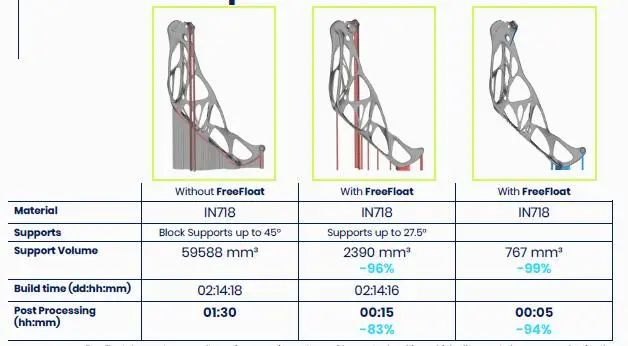
Em 2022, os especialistas da EOS desenvolveram uma variedade de técnicas de otimização de processos para a produção de peças impressas em 3D não suportadas, como anéis de estator, carcaças, bombas de turbina, tanques de óleo, trocadores de calor, válvulas e impulsores, sendo o impulsor fechado um exemplo particularmente típico.
Através da otimização do software de projeto e dos conjuntos de parâmetros, a EOS permitiu que os usuários imprimissem cantilevers e pontes em ângulos muito mais baixos, às vezes até zero grau, exigindo significativamente menos suportes, ou mesmo nenhum.
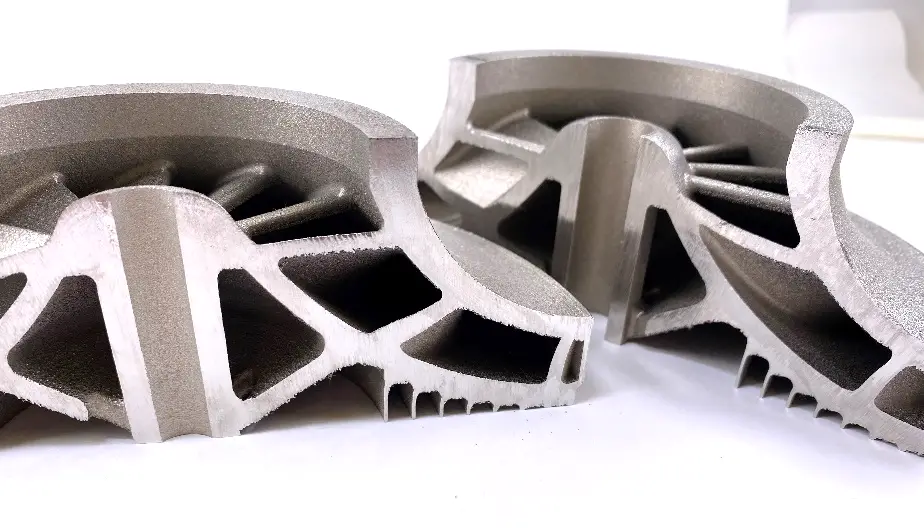
Sem dúvida, os fabricantes nacionais fizeram avanços notáveis na impressão sem suporte. Não muito tempo atrás, foi relatado que a empresa líder em impressão 3D, a Polite, havia descoberto uma solução para impressão sem suporte: estruturas com balanço inferior a 30° não necessitam de suporte.
A Polite venceu o desafio da tecnologia de impressão 3D de metal SLM sem suporte.
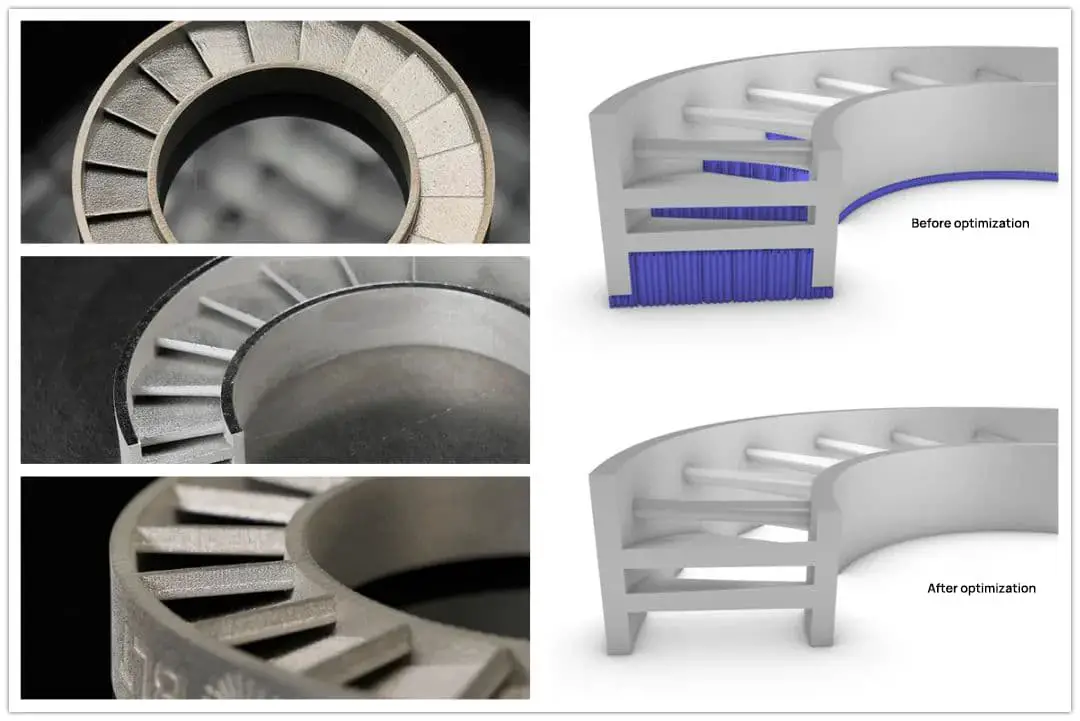
De modo geral, otimizar o design e a remoção do suporte é um desafio fundamental para tornar o fluxo de trabalho de impressão 3D mais rápido e simples.
Como pode ser visto nos exemplos acima, a indústria de fabrico aditivo está continuamente a desenvolver soluções para superar este desafio.
No entanto, para além da tecnologia, os profissionais necessitam de um nível mais elevado de competências e conhecimentos para apresentar melhores soluções.
Esperamos que este artigo tenha ampliado seu conhecimento sobre como usar estruturas de suporte de forma mais eficaz na impressão 3D, ajudando assim a transformá-los de inimigos em aliados.