A principal ferramenta para usinar peças planas é uma fresa de facear, que possui arestas de corte ao longo de sua circunferência e face final. A aresta de corte da face final é considerada uma aresta de corte secundária.
A fresa de facear normalmente tem um diâmetro grande, portanto, ao selecionar a fresa, é comum separar os dentes e o corpo da fresa para garantir o uso a longo prazo.
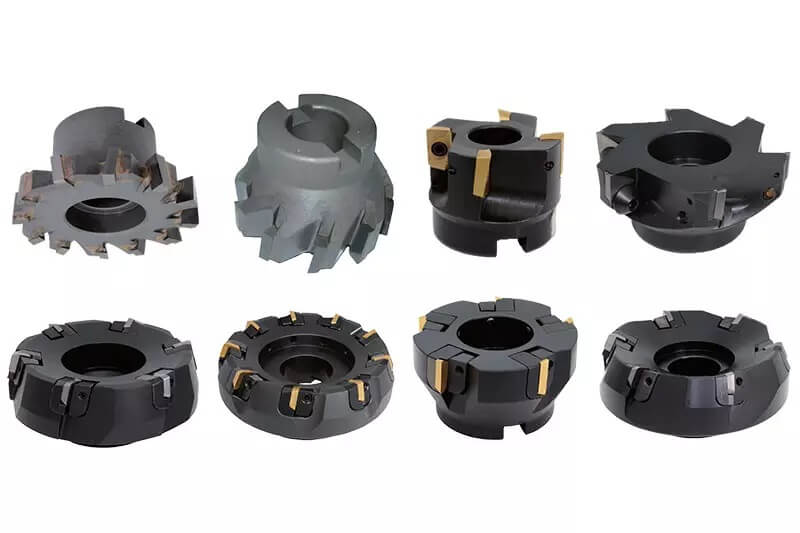
1. Seleção do diâmetro da fresa de facear
A seleção do diâmetro da fresa de facear é dividida principalmente em três casos:
(1) Ao usinar uma área plana pequena, é importante escolher uma ferramenta ou fresa com diâmetro maior que a largura do plano para obter fresamento de plano único. Os melhores resultados são alcançados quando o diâmetro da fresa plana é 1,3 a 1,6 vezes a largura da superfície de usinagem.
(2) Para uma grande área do plano de usinagem, são necessários múltiplos passes com uma fresa de diâmetro apropriado. O diâmetro da fresa será limitado pelas limitações da máquina-ferramenta, profundidade e largura de corte e tamanho da lâmina e da ferramenta.
(3) Quando o plano de usinagem é pequeno e as peças estão espalhadas, uma fresa de topo de diâmetro menor deve ser selecionada para fresamento. Para maximizar a eficiência, a fresa deve ter 2/3 do seu diâmetro em contato com a peça, o que significa que o diâmetro da fresa é igual a 1,5 vezes a largura fresada.
Ao fresar para frente, a proporção apropriada entre o diâmetro da ferramenta e a largura de corte garantirá um ângulo de corte adequado para a fresa ao entrar na peça de trabalho.
Se houver incerteza sobre a capacidade da máquina-ferramenta de manter esta relação de corte, a espessura do corte axial pode ser concluída em múltiplas passagens para manter a relação entre o diâmetro da fresa e a largura de corte, tanto quanto possível.
2. Seleção do número de dentes da fresa
Ao escolher uma fresa para usinagem, é importante considerar o número de dentes da fresa. Por exemplo, uma fresa de dentes esparsos de 100 mm de diâmetro tem apenas 6 dentes, enquanto uma fresa de dentes densos de 100 mm de diâmetro pode ter 8 dentes. A densidade dos dentes do cortador afeta a eficiência da produção e a qualidade do produto.
Dentes densos levam a maior eficiência de produção e melhor qualidade do produto, mas também dificultam a descarga de cavacos. Os cortadores podem ser divididos em dentes esparsos, dentes finos e dentes densos com base no diâmetro dos dentes. Dentes esparsos são usados para usinagem de desbaste de peças e possuem de 1 a 1,5 lâminas para cada 25,4 mm de diâmetro, proporcionando amplo espaço para retenção de cavacos.
Este tipo de ferramenta é utilizada para cortar materiais macios que produzem cavacos contínuos e é mais adequada para cortes com lâminas longas e de grande largura.
Dentes densos são ideais para condições de usinagem estáveis e são comumente usados para usinagem em desbaste de ferro fundido. Eles também são adequados para cortes rasos e estreitos em superligas e para cortes sem espaço para cavacos. Dentes densos são usados no fresamento de acabamento com uma quantidade de corte axial posterior de 0,25 a 0,64 mm, resultando em uma baixa carga de corte por dente e requisitos de energia reduzidos. Este tipo de cortador é ideal para processar materiais de paredes finas.
O passo do dente determina o número de dentes da fresa envolvidos no corte ao mesmo tempo durante o fresamento. É importante ter pelo menos uma lâmina cortando sempre para evitar impactos de fresamento que podem causar danos à ferramenta e sobrecarga da máquina-ferramenta. Além disso, o número de dentes da lâmina deve ser selecionado para permitir que os cavacos enrolem e saiam facilmente da área de corte. Um espaço insuficiente para segurar os cavacos pode fazer com que os cavacos fiquem presos, danificando a aresta de corte e potencialmente a peça de trabalho. A lâmina também deve ter densidade suficiente para garantir que pelo menos uma lâmina esteja cortando o tempo todo durante o corte, ou poderá causar impacto severo, levando à fratura da aresta de corte, danos à ferramenta e sobrecarga da máquina-ferramenta.
3. Seleção do ângulo da ferramenta
O ângulo de corte da ferramenta pode ser posicionado como um ângulo de inclinação positivo, ângulo de inclinação negativo ou ângulo de inclinação zero em relação ao plano radial e ao plano axial. O ângulo de inclinação zero, onde toda a aresta de corte impacta a peça ao mesmo tempo, geralmente não é usado.
A escolha do ângulo da fresa de facear afeta o modo de contato da fresa plana. Para minimizar o impacto na fresa, reduzir danos à fresa e evitar o modo de contato com a face stuv, é importante considerar tanto o ângulo de corte da fresa quanto o ângulo geométrico da fresa de facear.
O ângulo de corte é determinado pela combinação do ângulo de inclinação radial e axial.
Os métodos básicos comuns de combinação incluem:
- Ângulo de inclinação radial negativo e ângulo de inclinação axial negativo.
- Ângulo de inclinação radial positivo e ângulo de inclinação axial positivo.
- Ângulo de inclinação radial negativo e ângulo de inclinação axial positivo.
- Ângulo de inclinação radial positivo e ângulo de inclinação axial negativo.
Ferramentas com ângulos de avanço axial e radial negativos (referidas como “duplo negativo”) são usadas principalmente para usinagem de desbaste de ferro fundido e aço fundido, mas a máquina-ferramenta deve ter alta potência e rigidez suficiente. A lâmina “duplo negativo” tem uma aresta de corte forte e pode suportar grandes cargas de corte, mas a máquina-ferramenta, a peça e o acessório também devem ter alta rigidez.
Ferramentas com ângulos de avanço axial e radial positivos (chamadas de “duplo positivo”) aumentam o ângulo de corte, tornando o corte mais leve e a remoção de cavacos mais suave, mas a resistência da aresta de corte é fraca.
Esta combinação é ideal para processar materiais macios e materiais como aço inoxidável, aço resistente ao calor, aço comum e ferro fundido. Deve ser usado quando a máquina-ferramenta tem baixa potência, o sistema de processo tem rigidez insuficiente e ocorrem tumores de acúmulo de cavacos.
A combinação do ângulo de inclinação radial negativo e do ângulo de inclinação axial positivo aumenta a resistência da aresta de corte com o ângulo de inclinação radial negativo e produz uma força de cisalhamento com o ângulo de inclinação axial positivo. Esta combinação possui forte resistência ao impacto e uma aresta de corte afiada, tornando-a adequada para fresamento pesado de aço, aço fundido e ferro fundido.
O ângulo de inclinação radial positivo e o ângulo de inclinação axial negativo fazem com que os cavacos quebrados se movam abaixo do centro, fazendo com que os cavacos arranhem a superfície usinada e levando a uma remoção deficiente dos cavacos.
4. Seleção da pastilha de fresagem
A escolha da preparação da pastilha de fresamento também é um fator importante no fresamento plano. Em alguns casos, uma lâmina prensada é mais apropriada e em outros, uma lâmina retificada é necessária.
Uma lâmina prensada é mais econômica para usinagem de desbaste e tem melhor resistência da aresta, tornando-a resistente ao impacto e capaz de lidar com grandes retroalimentos e avanços. Ele também possui uma ranhura de curvatura de cavacos na face de saída que reduz a força de corte, o atrito com a peça de trabalho e os cavacos e a demanda de energia.
No entanto, a superfície da lâmina prensada não é tão lisa quanto uma lâmina retificada e tem baixa precisão dimensional, com uma grande diferença na altura de cada ponta da ferramenta no corpo da fresa. Apesar dessas desvantagens, a lâmina prensada é amplamente utilizada na produção devido ao seu baixo custo.
Para fresamento de acabamento, uma lâmina retificada é preferida devido à sua boa precisão dimensional, resultando em alta precisão de posicionamento da aresta de corte, maior precisão de usinagem e menor valor de rugosidade superficial. A tendência na retificação de pastilhas de fresamento usadas na usinagem de acabamento é retificar uma ranhura curvada de cavacos para formar uma grande aresta de corte positiva, permitindo que a lâmina corte com pequeno avanço e retroprojeção.
No entanto, sem um ângulo de inclinação acentuado, uma lâmina de metal duro processada com pequeno avanço e retroprojeção resultará em atrito da ponta da ferramenta na peça de trabalho e reduzirá a vida útil da ferramenta.