Na indústria de usinagem, “precisão de usinagem” é um termo comum usado com frequência. Isso é mencionado várias vezes ao dia e, ao conversar com pessoas do setor, a precisão da usinagem é sempre discutida.
Surge então a questão: como a máquina CNC pode garantir a precisão da usinagem?
A precisão das máquinas-ferramenta CNC depende, em última análise, da precisão da própria máquina-ferramenta. Essa precisão inclui vários fatores, como precisão geométrica, precisão de posicionamento, precisão de posicionamento repetido e precisão de corte.
Precisão geométrica:
Também é conhecida como precisão estática, que reflete de forma abrangente os erros geométricos dos principais componentes das máquinas-ferramentas CNC após a montagem.
Precisão de posicionamento:
Isto demonstra a precisão do movimento da máquina-ferramenta que está sendo medida sob o controle do dispositivo de controle numérico. Com base no valor medido da precisão de posicionamento, pode-se determinar a precisão ideal para usinar a peça no processo de usinagem automatizado da máquina-ferramenta.
A precisão do posicionamento refere-se à diferença entre a posição real da peça ou ferramenta e a posição padrão (posição teórica ou ideal). Quanto menor a diferença, maior será a precisão.
Garantir a precisão do processamento de peças depende da obtenção de alta precisão de posicionamento, que é um pré-requisito crucial.
Repita a precisão do posicionamento
Isto se refere à consistência na precisão da posição obtida pela execução repetida do mesmo código de programa em uma máquina-ferramenta CNC. Inclui também a consistência dos resultados obtidos ao processar um lote de peças nas mesmas condições, como utilizar a mesma máquina-ferramenta CNC e métodos de operação, e com o mesmo programa de peça.
Precisão de corte:
Esta é uma inspeção abrangente da precisão geométrica e de posicionamento da máquina-ferramenta durante as operações de corte.
Conforme exposto acima, a precisão das máquinas-ferramenta CNC é dividida em aspectos mecânicos e elétricos. Os aspectos mecânicos cobrem a precisão do fuso, incluindo desvio e barramento, a precisão do parafuso de avanço, a precisão do acessório durante o processamento e a rigidez da máquina-ferramenta.
Os aspectos elétricos dizem respeito principalmente a métodos de controle, como malha semifechada e malha totalmente fechada, métodos de feedback e compensação e precisão de interpolação durante o processamento.
Assim, a precisão da máquina-ferramenta não depende apenas de ela ser totalmente fechada ou não.
I. Introdução ao princípio
A cadeia de movimento das máquinas-ferramentas CNC inclui os seguintes componentes: dispositivo CNC → servo codificador → servo acionamento → motor → parafuso → peças móveis.
Dependendo da posição de instalação do dispositivo de detecção de posição, o controle pode ser classificado em três tipos: controle de malha totalmente fechada, controle de malha semifechada e controle de malha aberta.
Sistema servo de alimentação de controle de circuito totalmente fechado
A máquina-ferramenta é equipada com dispositivos de detecção de posição, como réguas de grade e sincronizadores de indução linear, que são instalados em suas partes móveis, como bancadas de trabalho. Esses dispositivos fornecem feedback em tempo real sobre a posição das peças móveis.
Após o sistema CNC processar as informações, o estado da máquina-ferramenta é retransmitido ao servo motor. O servo motor compensa automaticamente qualquer erro de movimento através do comando do sistema.
No entanto, como envolve o controle de malha fechada dos grandes elos de inércia do parafuso de avanço, do par de porcas e da mesa da máquina-ferramenta, pode ser mais desafiador depurar o sistema em um estado estável.
Além disso, a instalação de dispositivos de medição, como réguas de grade e sincronizadores de indução linear, pode ser cara e complicada, o que pode levar a oscilações.
Portanto, a maioria das máquinas-ferramentas em geral não utiliza controle total em malha fechada.
Sistema servo de alimentação de controle de circuito semifechado
Um dispositivo de detecção de posição é instalado na extremidade do motor de acionamento ou na extremidade da haste do parafuso para detectar o ângulo de rotação do parafuso ou servo motor. Isso ajuda a medir indiretamente a posição real das peças móveis da máquina-ferramenta, que é então enviada de volta ao sistema de controle por meio de feedback.
Com os avanços na fabricação mecânica e melhorias na precisão dos elementos de detecção de velocidade e passos dos parafusos, as máquinas-ferramentas CNC de circuito semifechado alcançaram um nível bastante alto de precisão de alimentação.
Como resultado, a maioria dos fabricantes de máquinas-ferramenta adotou amplamente sistemas CNC de circuito semifechado.
II. Aplicação prática
Sistema de controle de circuito totalmente fechado
Dispositivos de detecção de posição, como réguas de grade e sincronizadores de indução linear, têm níveis variados de precisão, variando de ±0,01 mm a ±0,003 mm. O nível de precisão afeta a precisão do posicionamento e, mesmo com controle total em malha fechada, podem ocorrer erros.
A detecção de posição também é afetada pelas propriedades térmicas, especificamente pela deformação térmica. Os dispositivos de medição são normalmente feitos de materiais não metálicos e o coeficiente de expansão térmica varia entre os vários componentes da máquina-ferramenta.
Este é um aspecto crítico da precisão da máquina-ferramenta e deve ser abordado reduzindo a geração de calor durante a usinagem para superar a deformação térmica causada pela temperatura. Máquinas-ferramentas de última geração utilizam vários métodos, como resfriamento de parafuso oco, lubrificação de trilho guia e resfriamento de temperatura constante de fluido de corte para reduzir a deformação térmica.
A instalação do dispositivo de detecção de posição também é crucial. Em teoria, quanto mais próximo estiver do eixo de acionamento (par de parafusos), mais precisa será a medição. No entanto, devido a limitações estruturais de espaço, existem apenas duas maneiras de instalar a régua de grade: próximo à lateral do parafuso de avanço ou na parte externa do trilho-guia.
Embora seja recomendado optar pelo primeiro método de instalação, pode ser inconveniente para fins de inspeção e manutenção. Por outro lado, embora tenha sido selecionada uma régua de grade de alta precisão, ela não conseguiu atingir a precisão necessária para máquinas-ferramentas CNC.
No primeiro caso, a posição de instalação da régua da grade é relativamente próxima ao eixo de acionamento, mas ainda mantém uma certa distância dele. Esta distância, juntamente com a oscilação do objeto durante a condução, causa problemas na detecção e controle da régua de grade.
Quando o objeto acionado balança em direção ao lado de montagem da régua de grade, ele confunde a velocidade de movimento como insuficiente durante a detecção, resultando no sistema emitindo um sinal de aceleração. Quando o objeto em movimento oscila para o outro lado, a régua da grade confunde a velocidade do movimento como muito rápida durante a detecção e o sistema emite um sinal de desaceleração.
Essas operações repetidas não melhoram o controle dos eixos de coordenadas lineares da máquina-ferramenta CNC, mas intensificam a vibração do objeto acionador. Isto leva a um fenômeno peculiar onde o circuito totalmente fechado não é tão bom quanto o circuito semifechado.
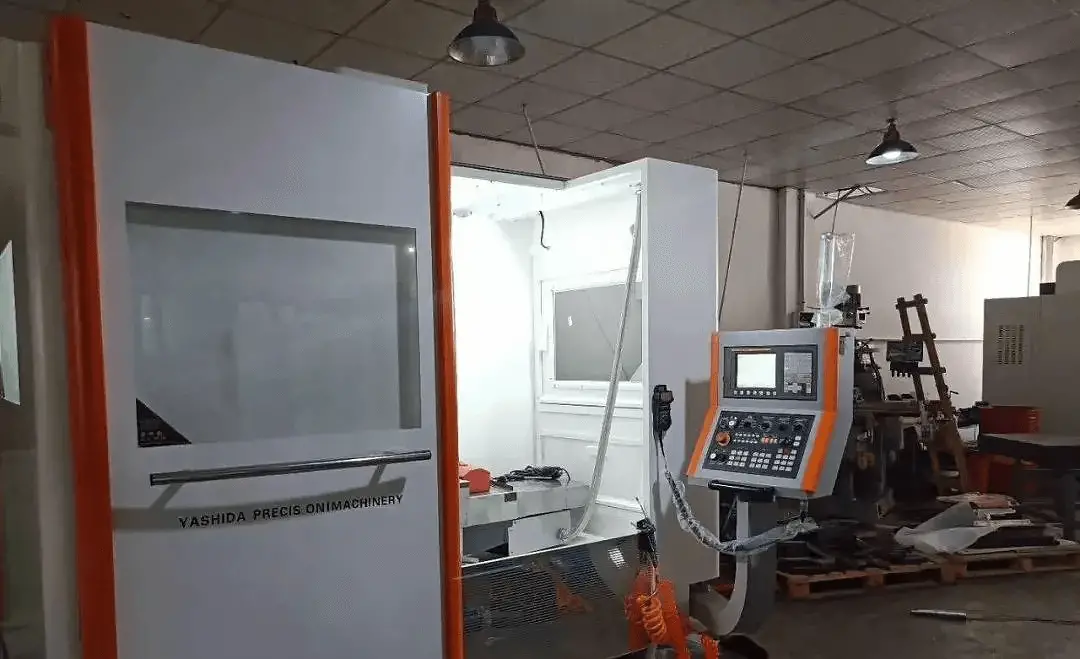
Impacto ambiental da produção:
Geralmente, as fábricas de usinagem possuem ambientes agressivos, onde poeira e vibração são fenômenos comuns. No entanto, escalas de grade e sincronizadores de indução linear são componentes de precisão que medem a posição relativa do movimento através da reflexão da luz.
Poeira e vibração são os dois maiores fatores que afetam a precisão da medição. Além disso, a névoa de óleo de corte e a névoa de água são mais graves durante a usinagem de máquinas-ferramenta, afetando muito a régua de grade e o sincronizador de indução linear.
Portanto, se for utilizado um sistema de controle de circuito totalmente fechado, é essencial garantir a instalação e vedação adequadas e melhorar o ambiente de produção. Caso contrário, a precisão da nova máquina-ferramenta, que era originalmente boa, diminuirá dentro de um ano, e a máquina frequentemente soará um alarme.
Sistema de controle de malha semifechada
Como o dispositivo de medição é normalmente instalado na parte superior do motor ou do parafuso de avanço, é mais fácil de vedar, tornando desnecessárias as exigências ambientais.
O erro de precisão do sistema de controle de malha semifechada depende principalmente da folga direta e reversa do parafuso.
Graças aos avanços na tecnologia de processamento mecânico, o atual nível de fabricação de parafusos de avanço importados é relativamente alto. Pares de fusos de avanço de alta precisão praticamente eliminam a folga para frente e para trás.
Além disso, durante o processo de montagem, o par de parafusos adota um par de fusos de esfera reverso de duas carreiras, que pode eliminar totalmente a folga direta e reversa.
Muitas fábricas de máquinas-ferramenta usam o método de pré-alongamento durante a montagem da máquina-ferramenta para eliminar o impacto da deformação térmica na precisão da rosca.
Portanto, o atual sistema de controle de circuito semifechado pode garantir alta precisão da máquina-ferramenta.
Conclusão
Em resumo, pode-se observar que, em teoria, o controle de malha totalmente fechada pode melhorar a precisão básica do posicionamento em comparação com o controle de malha semifechada se fatores externos não forem considerados. No entanto, a falha em abordar fatores como calor da máquina, poluição ambiental, aumento de temperatura, vibração e instalação pode levar a um cenário em que o controle de malha totalmente fechada tenha um desempenho pior do que o de malha semifechada.
Embora possa funcionar bem no curto prazo, as mudanças de poeira e temperatura podem impactar significativamente os dados de feedback de medição da régua de grade no longo prazo, reduzindo assim sua eficácia.
Além disso, se houver algum problema com a régua da grade, ela gera um alarme, que pode causar mau funcionamento da máquina-ferramenta.
Devido a considerações de custo e concorrência, o controle de circuito fechado completo para máquinas-ferramentas de médio e baixo custo foi simplificado. Como resultado, alguns aspectos como a vedação e o controle do aumento de temperatura podem não ser bem garantidos.
Nesses casos, a simples configuração da régua de grade não pode melhorar a precisão da máquina-ferramenta e pode incorrer em custos significativos.