Ambiente de serviço de materiais aeroespaciais
Os materiais aeroespaciais não devem apenas ser capazes de suportar altas tensões e forças inerciais, mas também suportar impactos e cargas alternadas causadas por fatores como decolagem e pouso, vibração do motor, rotação rápida de peças, vento repentino e manobras de voo.
A exposição das aeronaves aos gases do motor e à radiação solar cria um ambiente de alta temperatura, com o aumento da velocidade de voo levando a um aquecimento aerodinâmico significativo.
Esses materiais também estão sujeitos a temperaturas variadas, incluindo quedas para cerca de -50°C quando voam em velocidade subsônica na estratosfera, e temperaturas ainda mais baixas nas regiões polares durante o inverno.
Componentes metálicos e pneus de borracha são suscetíveis à fragilização, enquanto combustíveis e lubrificantes podem ter efeitos corrosivos em materiais metálicos e efeitos de dilatação em materiais não metálicos.
Além disso, a exposição à radiação solar, a erosão eólica e pluvial e o armazenamento a longo prazo em ambientes úmidos podem acelerar o processo de envelhecimento dos materiais poliméricos.
Seleção e aplicação de materiais aeroespaciais
Os veículos aeroespaciais têm funcionado na atmosfera ou no espaço sideral há um longo período. Para garantir sua alta confiabilidade, segurança e ótimo desempenho de voo, eles devem ser projetados para operar de forma eficaz em ambientes desafiadores.
Para atingir esses objetivos, é essencial otimizar a estrutura para atender aos requisitos aerodinâmicos, tecnológicos e de manutenção. No entanto, também requer a utilização de materiais que possuam excelentes características e funções.
1. Princípio de seleção de materiais
Em serviço, os componentes estruturais devem ser capazes de suportar vários tipos de forças externas sem exceder o nível aceitável de deformação ou ruptura dentro de um período de tempo especificado.
Um dos objetivos do projeto em estruturas aeroespaciais é minimizar seu tamanho e peso. No passado, o foco principal estava na resistência estática dos componentes, muitas vezes negligenciando ou dando atenção limitada à sua resistência plástica. Isso resultou em acidentes catastróficos.
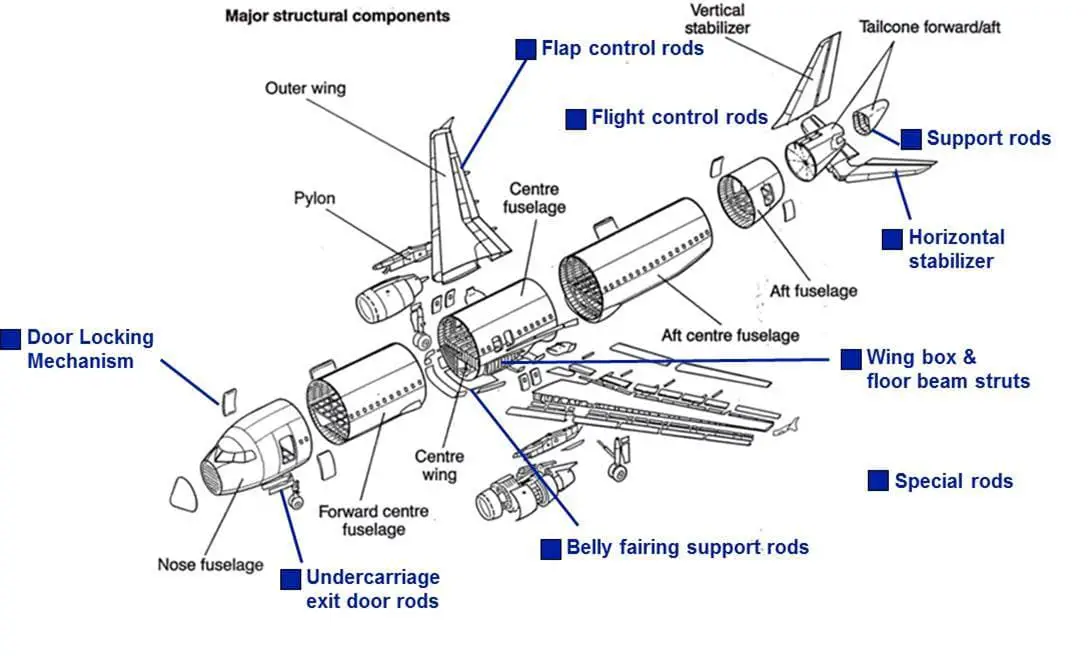
Principais componentes estruturais das aeronaves da linha principal
Para garantir a segurança dos componentes estruturais e aproveitar ao máximo o desempenho do material, o projeto de peças estruturais aeroespaciais mudou de um “princípio de projeto de resistência” para um “princípio de projeto de tolerância a danos” e evoluiu para um “princípio de projeto de ciclo de vida completo”. .
Na fase de design, todos os aspectos do ciclo de vida de um produto são levados em consideração e todos os fatores relevantes são considerados e otimizados de forma abrangente na fase de design do produto.
Os materiais não devem apenas ter alta resistência e rigidez específicas, mas também apresentar certa resistência à fratura e ao impacto, resistência à fadiga, resistência a altas e baixas temperaturas, resistência à corrosão, resistência ao envelhecimento e resistência ao molde, bem como indicadores de desempenho aprimorados.
Diferentes critérios de seleção de materiais são aplicados em diferentes áreas de carga, sendo os materiais escolhidos com base nos requisitos específicos de cada componente. Para áreas de alta carga, são utilizados critérios de resistência e selecionados materiais de alta resistência. Para áreas de carga média, são utilizados critérios de rigidez e escolhidos materiais com módulos elásticos elevados. Em áreas de baixa carga, a estabilidade dimensional é a principal consideração para garantir que os componentes sejam maiores que o tamanho crítico mínimo.
Ao selecionar e avaliar materiais estruturais, métodos de teste apropriados para propriedades mecânicas (tração, compressão, impacto, fadiga, impacto de baixa temperatura) devem ser selecionados com base nas condições de serviço e nos estados de tensão. Uma consideração abrangente da resistência, plasticidade e tenacidade do material deve ser feita para diferentes modos de fratura, incluindo fratura dúctil, fratura frágil, fadiga por tensão, fadiga por deformação, corrosão sob tensão, fragilização por hidrogênio, fragilização por irradiação de nêutrons, etc.
Para membros sob tração, a distribuição de tensões deve ser uniforme tanto na superfície quanto no núcleo, e o material selecionado deve ter estrutura e desempenho uniformes, com boa temperabilidade para membros grandes.
Para membros sujeitos a cargas de flexão e torção, existe uma grande diferença de tensões entre a superfície e o núcleo, podendo ser utilizados materiais com baixa temperabilidade.
O limite de fadiga e a sensibilidade do entalhe são critérios de avaliação importantes para a seleção de materiais para componentes sob cargas alternadas.
Para componentes expostos a ambientes corrosivos, fatores como resistência à corrosão, sensibilidade à fragilização por hidrogênio, tendência à corrosão sob tensão e resistência à fadiga por corrosão são indicadores de avaliação importantes para a seleção do material.
A estabilidade da estrutura deve ser considerada para materiais utilizados em serviços de alta temperatura, e o desempenho em baixa temperatura deve ser levado em consideração para serviços de baixa temperatura.
A redução do peso tem significado prático para melhorar a segurança das aeronaves, aumentar a carga útil e a resistência, melhorar a manobrabilidade e o alcance e reduzir o consumo de combustível ou propulsor e os custos de voo. Quanto mais rápida a velocidade da aeronave, mais significativa se torna a redução de peso. Por exemplo, reduzir o peso de um caça em 15% pode resultar numa redução de 15% na distância de táxi, num aumento de 20% no alcance e num aumento de 30% na carga útil.
Para aeronaves descartáveis de curto prazo, como mísseis ou veículos lançadores, é necessário alcançar funções equivalentes com volume e massa mínimos, buscando maximizar o desempenho do material e selecionando a menor margem de segurança possível para garantir confiabilidade absoluta ao longo de sua vida útil.
2. Principais materiais aeroespaciais
A redução da massa estrutural pode ser alcançada reduzindo a densidade em 30%, o que é mais do que a resistência em 50%.
Ligas de alumínio, ligas de titânio e materiais compósitos são os principais materiais utilizados em estruturas aeroespaciais devido à sua alta resistência e rigidez específicas, o que pode melhorar a carga útil, a manobrabilidade e a resistência das aeronaves, ao mesmo tempo que reduz os custos de voo.
O uso de aço de ultra-alta resistência (com limite de escoamento superior a 1380 MPa) na engenharia aeroespacial é limitado a menos de 10%.
Para aeronaves modernas, como caças supersônicos, a quantidade de aço de ultra-alta resistência é estável em 5% ~ 10%, a resistência à tração é de 600 ~ 1850MPa, às vezes tão alta quanto 1950mpa, e a resistência à fratura KEUc = 78 ~ 91MPa·m1/2.
O aço resistente à corrosão de alta resistência é normalmente usado para a estrutura de suporte de carga da fuselagem em ambientes com corrosão ativa, enquanto o aço resistente à corrosão sem carbono é usado para componentes em aeronaves equipadas com motores a combustível de hidrogênio usando hidrogênio líquido e meio hidrogênio.
Os principais materiais estruturais utilizados nas fuselagens de aeronaves no século 21 são ligas de alumínio, incluindo as séries 2XXX, série 7XXXX e ligas de alumínio-lítio. A adição de lítio às ligas de alumínio pode melhorar a sua resistência e reduzir a sua densidade, aumentando assim a sua resistência e rigidez específicas.
Ligas de alumínio-lítio têm sido usadas em grandes aeronaves de transporte, aviões de combate, mísseis estratégicos, ônibus espaciais e veículos de lançamento, e são usadas em componentes como projéteis, componentes de suporte de carga, tanques de armazenamento de hidrogênio líquido e oxigênio líquido, tubulações e adaptadores de carga útil. São considerados um material promissor para o desenvolvimento aeroespacial.
As ligas de alumínio-lítio de terceira e quarta geração não priorizam mais a baixa densidade e apresentam melhores propriedades gerais. Em comparação com as ligas de alumínio-lítio de terceira geração, as ligas de quarta geração têm maior resistência estática (especialmente resistência ao escoamento) e tenacidade à fratura, enquanto mantêm taxa de crescimento de trincas, desempenho de fadiga, desempenho de corrosão e módulo de elasticidade equivalentes.
As ligas de titânio têm uma resistência específica mais alta do que as ligas de alumínio e são usadas em componentes de aeronaves, como estrutura, trilho-guia e suporte do flap, base do motor, peças da estrutura de pouso e peças de aquecimento, como capô de exaustão e escudo contra incêndio. Para aeronaves supersônicas com números Mach maiores que 2,5, a temperatura da superfície pode atingir 200 a 350°C, e ligas de titânio podem ser usadas como revestimento.
As ligas de titânio de alta pureza e alta densidade preparadas por métodos de solidificação rápida/metalurgia do pó têm boa estabilidade térmica e mantêm sua resistência a 700°C, semelhante à sua resistência à temperatura ambiente. As ligas de titânio do tipo β de alta resistência e alta tenacidade desenvolvidas foram selecionadas pela NASA como material de matriz para materiais compósitos SiC/Ti usados na fuselagem de aeronaves e painéis de asas.
A proporção de ligas de titânio utilizadas em aeronaves está aumentando gradativamente, sendo 20% utilizadas em fuselagens de aviação civil e 50% em fuselagens de aeronaves militares.
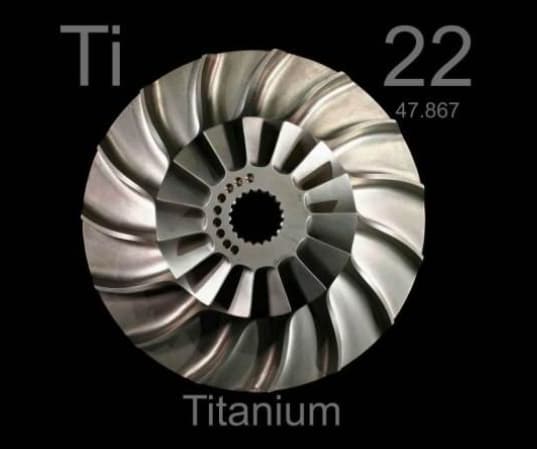
Compósitos de matriz metálica, compósitos de matriz de resina de alta temperatura, compósitos de matriz cerâmica e compósitos de carbono/carbono estão desempenhando um papel cada vez mais importante na indústria aeroespacial.
Os materiais compostos de carbono/carbono combinam as propriedades refratárias do carbono com a alta resistência e rigidez das fibras de carbono. Eles têm excelente estabilidade térmica e condutividade, bem como alta resistência e tenacidade a 2500°C com uma densidade que é apenas um quarto das ligas de alta temperatura.
Os compósitos híbridos ganharam atenção significativa, como a adição de fibra de vidro a compósitos de fibra de carbono para melhorar o desempenho de impacto ou a adição de fibra de carbono a plásticos reforçados com fibra de vidro para aumentar a rigidez.
Os materiais compósitos em camadas também estão se tornando mais amplamente utilizados na engenharia aeroespacial, como o uso de 3% de GLARE, um novo laminado, no A380. O laminado é um material compósito feito pelo empilhamento de dois materiais diferentes sob pressão.
Um laminado normalmente consiste em um painel superior, uma camada de ligação superior, um material de núcleo, uma camada de ligação inferior e um painel inferior. Sua resistência e rigidez são superiores às do painel individual ou do material do núcleo. Tem sido usado em aeronaves de transporte e caça.
O laminado GLARE é formado pela prensagem a quente de múltiplas placas finas de alumínio e fibra de vidro unidirecional pré-impregnada com adesivo epóxi sob pressão ou em tanque de prensagem a quente, conforme Figura 1. As placas de alumínio devem ser devidamente pré-tratadas para facilitar a adesão ao a camada pré-impregnada de fibra.
A Tabela 1 mostra os tipos de laminados GLARE produzidos comercialmente, que podem ser transformados em placas de diferentes espessuras conforme necessário. As fibras podem ter 2, 3, 4 camadas ou mais, e seu conteúdo e direção podem atender aos requisitos da tabela. Cada tipo de laminado GLARE pode ter diferentes formatos e ser ajustado para atender necessidades específicas.
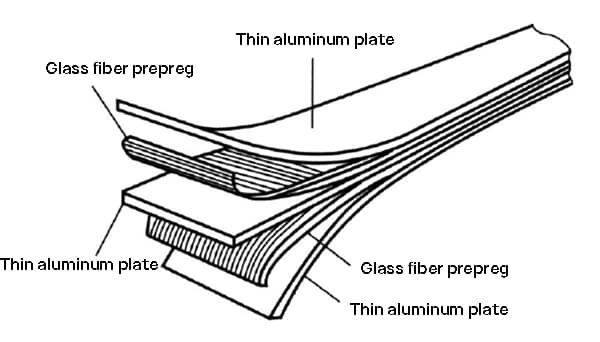
Fig. 1 Diagrama esquemático do laminado brilhante
Tabela 1 tipos de laminados ofuscantes disponíveis comercialmente
Laminado |
Camada de alumínio |
Camada fibrosa |
Densidade típica / (g / cm 3) |
||
produto de alumínio |
Espessura de camada única/mm |
orientação |
Espessura de camada única/mm |
||
BRILHO1 GLARE2 BRILHO3 GLARE4 BRILHO5 BRILHANTE6 |
7475-T76 2024-T3 2024-T3 2024-T3 2024-T3 2024-T3 |
0,3~0,4 0,2~0,5 0,2~0,5 0,2~0,5 0,2~0,5 0,2~0,5 |
Unidirecional Unidirecional 0°/ 90° ortogonal 0°/ 90°/0° ortogonal 0°/ 90°/90°/0° ortogonal +45° / – 45° ortogonal |
0,25 0,25 0,25 0,375 0,5 0,25 |
2,52 2,52 2,52 2,45 2,38 2,52 |
A tecnologia de emenda dos laminados GLARE resolve o problema da largura limitada da placa. Conforme mostrado na Figura 2, existe uma costura estreita entre a mesma camada de placas de alumínio, com juntas entre diferentes camadas localizadas em posições diferentes. Essas juntas podem ser conectadas a outras camadas de placas de alumínio através de camadas de fibra, permitindo a fabricação de placas de parede ou de todo o revestimento da fuselagem com excelente resistência à fadiga, à corrosão e ao fogo, eliminando a necessidade de furos para rebites e as concentrações de tensões resultantes. .
Para garantir a transferência segura da carga, uma camada de reforço pode ser adicionada na emenda, como uma camada de placa metálica ou uma camada de fibra de vidro pré-impregnada com resina.
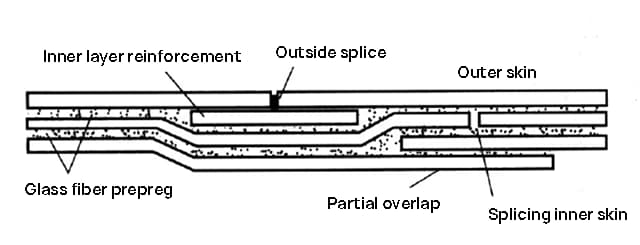
Fig. 2 Diagrama de emenda do laminado brilhante
Os materiais compósitos sanduíche em favo de mel são compostos por um núcleo sanduíche e uma pele (painel). A pele pode ser feita de alumínio ou materiais compósitos de carbono/epóxi, enquanto o núcleo sanduíche se assemelha a um favo de mel e é composto de uma série de células hexagonais, quadrilaterais ou de outros formatos feitas de metal, fibra de vidro ou materiais compósitos. As superfícies superior e inferior do sanduíche são coladas ou soldadas aos painéis mais finos.
O material do núcleo dos compósitos sanduíche de favo de mel de alumínio é feito colando folhas de alumínio de diferentes maneiras e formando favos de mel de várias especificações por meio de alongamento. O desempenho do material do núcleo é determinado principalmente pela espessura da folha de alumínio e pelo tamanho das células.
Esses materiais têm alta resistência e rigidez específicas, boa resistência ao impacto, redução de vibração, transmissão de microondas e forte designabilidade. Em comparação com estruturas rebitadas, a eficiência estrutural pode ser aumentada em 15% a 30%.
Estruturas sanduíche em favo de mel podem ser usadas para vários painéis de parede, como superfícies de asas, superfícies de cabine, coberturas de cabine, pisos, tampas de motor, placas de silenciador, placas de isolamento térmico, conchas de estrelas de satélite, antenas parabolóides, fundos de tanques de armazenamento de propelente de foguete e muito mais. No entanto, as estruturas sanduíche em favo de mel são suscetíveis à corrosão em certos ambientes.
Quando submetido ao impacto, o sanduíche de favo de mel sofrerá deformação permanente e se separará da pele.
3. Análise de materiais aeroespaciais
A Tabela 2 mostra a porcentagem de materiais estruturais utilizados em aeronaves militares nos Estados Unidos. A tendência é que o uso de materiais compósitos e ligas de titânio aumente gradativamente, enquanto o uso de ligas de alumínio diminua.
Tabela 2 porcentagem de materiais estruturais para aeronaves militares dos EUA
Tipo | Aço | Liga | Liga de titânio | Material combinado |
F-16 | 5 | 8 | 2 | 3 |
F-18A/B | 15 | 50 | 12 | 9,5 |
F-18C/D | 16 | 50 | 13 | 10 |
F-18E/F | 14 | 31 | 21 | 23 |
F-22 | 5 | 16 | 41 | 24 |
F-35 | – | – | 27 | 36 |
F117 | 5 | 20 | 25 | 10 |
B-1 | 9 | 41 | 21 | 29 |
B2 | 6 | 19 | 26 | 38 |
Capítulo 17 | 12.3 | 69,3 | 10.3 | 8.1 |
A Tabela 3 mostra a discriminação dos materiais utilizados em aeronaves típicas da linha principal. O B787 possui 50% de materiais compósitos e o A350 possui 52% de materiais compósitos. O uso de materiais compósitos está se tornando uma tendência na indústria aeroespacial devido à sua capacidade de reduzir peso, aumentar a resistência a danos, fornecer proteção contra corrosão e aumentar a durabilidade.
No entanto, os materiais compósitos também apresentam desvantagens, como alto custo, resistência limitada ao impacto, falta de plasticidade, maior dificuldade técnica, baixa manutenção e dificuldade de reciclagem. Como resultado, o uso de materiais compósitos não aumentou no A320neo e no B737MAX em comparação com o A320 e o B737.
Tabela 3 proporção de materiais típicos de aeronaves de linha principal (%)
Tipo | Liga de alumínio | Aço | Liga de titânio | Material combinado | Outro |
B373 | 79 | 12 | 5 | 3 | 1 |
B747 | 79 | 13 | 4 | 3 | 1 |
B757 | 78 | 12 | 6 | 3 | 1 |
B767 | 80 | 14 | 2 | 3 | 1 |
B777 | 70 | 11 | 7 | 11 | 1 |
B787 | 20 | 10 | 15 | 50 | 5 |
A300 | 76 | 13 | 4 | 5 | 2 |
A310 | 74 | 8 | 5 | 6 | 7 |
A320 | 66 | 6 | 5 | 15 | 8 |
A330/A340 | 66 | 5 | 5 | 16 | 8 |
A380 | 61 | 5 | 5 | 22 | 7 |
A350 | 20 | 7 | 14 | 52 | 7 |
MD-82 | 74,5 | 12 | 6 | 7,5 | – |
MS-21 | 33 | 5 | 19 | 38 | 5 |
Capítulo 919 | 63 | 8 | 8 | 21 | – |
A maioria das seções da cabine das espaçonaves tripuladas são feitas de ligas de alumínio, ligas de titânio e materiais compósitos. Por exemplo, os orbitadores do ônibus espacial são construídos principalmente de ligas de alumínio, enquanto a estrutura de impulso que suporta o motor principal é feita de liga Qin. A estrutura principal da fuselagem intermediária é composta por um material compósito de matriz de metal reforçado com liga de alumínio reforçada com fibra de boro, e a porta do compartimento de carga é feita de uma estrutura especial em sanduíche de favo de mel de papel com material compósito de resina epóxi reforçada com fibra de grafite como painel .
Materiais ablativos são usados na superfície externa da cabeça do míssil, na cápsula de reentrada da espaçonave e na superfície interna do motor do foguete. Sob fluxo de calor, esses materiais podem sofrer alterações físicas e químicas, incluindo decomposição, derretimento, evaporação, sublimação e erosão. Isso resulta no consumo de massa da superfície do material, o que retira grande quantidade de calor, evitando que o fluxo de calor durante a reentrada na atmosfera entre na aeronave e resfrie a câmara de combustão e o bocal do motor do foguete.
Para manter a temperatura adequada na cabine, são tomadas medidas de proteção contra radiação térmica para a seção de reentrada. O revestimento externo é feito de liga à base de níquel resistente a altas temperaturas ou placa de berílio, e a estrutura interna é composta de liga resistente ao calor. A camada externa e a estrutura interna são preenchidas com materiais com boas propriedades de isolamento térmico, como fibra de quartzo e cerâmica composta de fibra de vidro.
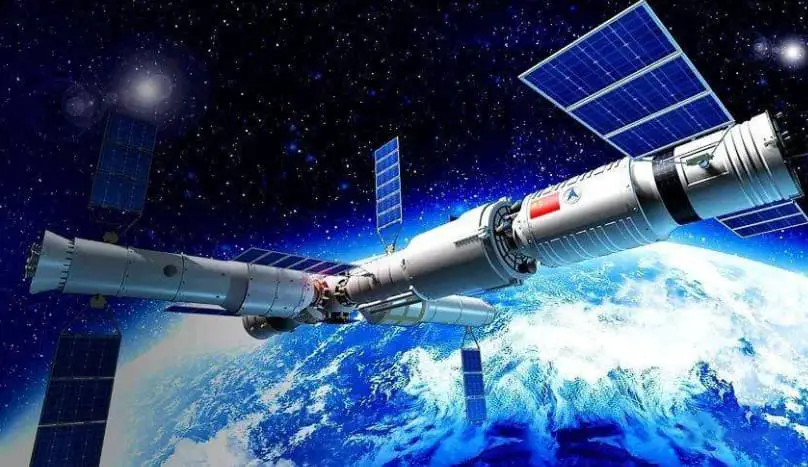
Conclusão
Com a implementação e o avanço contínuo de projetos espaciais, como voos espaciais tripulados, exploração lunar, exploração do espaço profundo, satélites de alta resolução, veículos de alta velocidade, veículos reutilizáveis e veículos espaciais móveis, novos e mais exigentes requisitos estão sendo impostos aos materiais, oferecendo novas oportunidades e impulsionando o desenvolvimento de novos materiais aeroespaciais.
Avanços significativos foram alcançados na garantia independente das principais matérias-primas e aplicações de engenharia na área de materiais.