Dividir uma vara de bambu ao meio faz com que ambas as metades se dobrem – a metade maior menos e a metade menor mais significativamente. Este fenômeno ocorre porque o material possui inerentemente tensão, e sua divisão perturba o equilíbrio original dessa tensão, levando à deformação como forma de restabelecer o equilíbrio.
Da mesma forma, a deformação da peça por EDM (usinagem por descarga elétrica) com fio segue este princípio, onde o processo de corte perturba o equilíbrio de tensão original dentro da peça.
Causas da deformação da peça em eletroerosão a fio
A extensão da deformação na eletroerosão a fio está relacionada à estrutura da peça. Cavidades e saliências estreitas e longas são propensas à deformação, com o grau de deformação dependendo da complexidade da forma, proporção de aspecto e outros fatores; peças de trabalho com paredes mais finas têm maior probabilidade de se deformar.
Se a deformação for mínima e estiver dentro dos requisitos de precisão do processo de usinagem, pode ser quase insignificante.
Porém, se a deformação exceder a precisão de usinagem exigida, causará desvios perceptíveis nas dimensões, afetando o formato da peça usinada.
A deformação pode resultar de vários fatores, incluindo propriedades do material, tratamento térmico, projeto estrutural, planejamento do processo e a escolha da fixação da peça e do caminho de corte durante a EDM com fio.
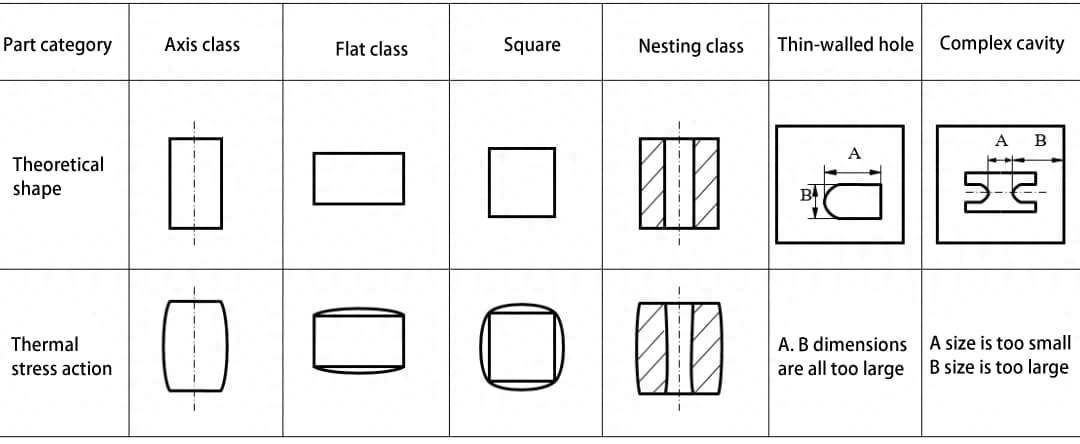
Medidas preventivas para deformação da peça
Certas medidas podem controlar e prevenir a deformação na eletroerosão a fio.
1) Usinagem de desbaste ou corte com alívio de tensão antes do corte final.
O corte de grandes áreas em um material pode perturbar o equilíbrio de tensões internas, causando deformação significativa. Ao remover a maior parte do excesso de material através de usinagem de desbaste ou executando caminhos de corte com alívio de tensão, a maior parte da tensão interna pode ser eliminada.
Para moldes com cavidades grandes em EDM, realizar dois cortes principais pode ser benéfico. Aumente o deslocamento em 0,1~0,2 mm para o primeiro corte principal para permitir o alívio de tensão e, em seguida, prossiga com o deslocamento padrão para o segundo corte principal, conforme mostrado nas ilustrações.
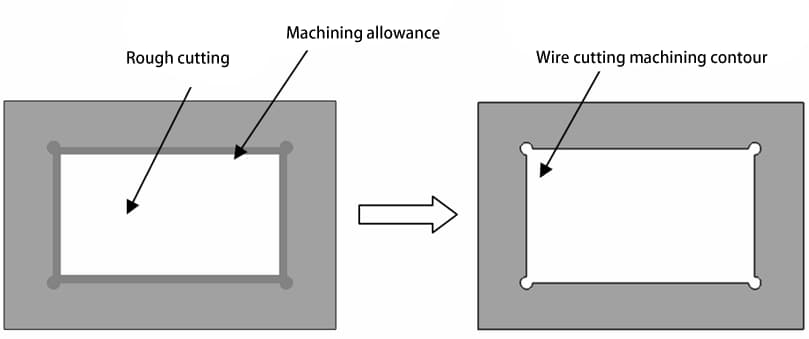
Para formatos longos e estreitos, realizar cortes com alívio de tensão dentro do formato antes de usinar o perfil externo pode reduzir significativamente a deformação.
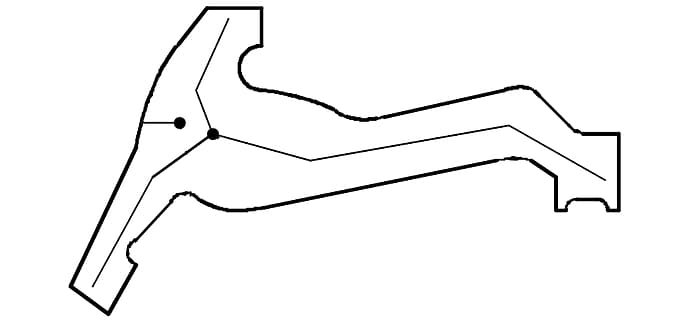
2) Perfuração de furos para rosqueamento de fio
Ao cortar saliências, iniciar o corte diretamente do exterior do material, conforme mostrado na figura (a), pode levar à deformação devido ao estresse desequilibrado do material, resultando em deformações de abertura ou fechamento.
Fazer furos para rosqueamento de fio para usinagem de contorno fechado, conforme mostrado na figura (b), pode reduzir significativamente a deformação causada pela eletroerosão a fio.

Reduzindo a deformação perfurando furos para passar fio
3) Otimizando o caminho de corte
Geralmente, é melhor iniciar o corte próximo à extremidade de fixação e organizar o segmento que separa a peça de trabalho de sua peça de fixação no final do caminho de usinagem, colocando pontos de pausa próximos à extremidade fixada da peça de trabalho.
Arranjos de caminhos de usinagem irracionais também podem levar à deformação na eletroerosão a fio.
Um caminho de usinagem mais racional é: A→B→C→D……→A. Se o caminho estiver disposto no sentido horário: A→L→K→J……→A, cortar a peça de trabalho da peça de fixação no início pode afetar diretamente a precisão da saliência devido à fixação não confiável.
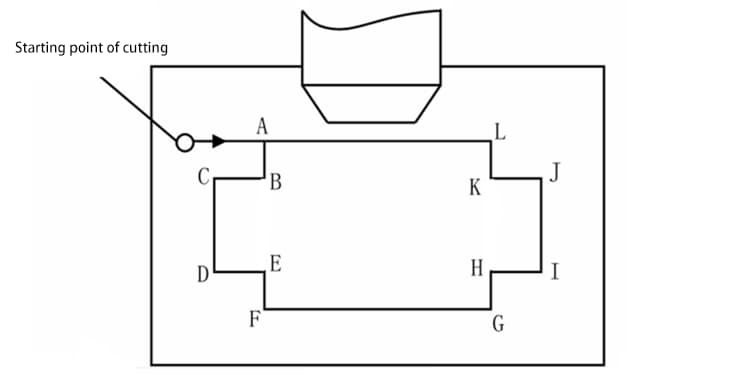
4) Vários cortes
Para peças de trabalho ainda propensas a deformações após a tomada de certas medidas, mudar o hábito tradicional de cortar no tamanho certo de uma só vez e usar cortes múltiplos pode atender aos requisitos de precisão.
Cortes múltiplos na eletroerosão a fio, que visam principalmente obter melhor rugosidade superficial, também reduzem significativamente a deformação resultante de tensões internas nas peças do molde.
5) Otimizando o processo de usinagem para placas de molde com múltiplas cavidades
Durante a eletroerosão a fio, a interação das tensões internas originais e das tensões térmicas geradas pelo processo de corte pode causar deformações imprevisíveis e irregulares, levando à remoção irregular de material em cortes subsequentes e afetando a qualidade e a precisão da usinagem.
Para resolver isso, para moldes de alta precisão, todas as cavidades podem ser cortadas em vários estágios. O primeiro corte remove todos os resíduos das cavidades.
Após a remoção dos resíduos, o recurso de reposicionamento automático da máquina é utilizado para finalizar sequencialmente as cavidades: corte principal para cavidade a, remover resíduos→corte principal para cavidade b, remover resíduos→corte principal para cavidade c, remover resíduos→……→corte principal para a cavidade n, remova os resíduos→corte de acabamento para a cavidade a→corte de acabamento para a cavidade b→……→corte de acabamento para a cavidade n, completando o processo.
Este método de corte permite que cada cavidade tenha tempo suficiente para liberar tensões internas, minimizando a influência mútua e pequenas deformações causadas por diferentes ordens de usinagem e garantindo a precisão das dimensões do molde.
No entanto, este método envolve múltiplas operações de rosqueamento e é trabalhoso, tornando-o mais adequado para máquinas EDM de fio lento equipadas com mecanismos de rosqueamento automáticos. Após o corte, as medições confirmam que as dimensões atendem aos requisitos de alta precisão.
6) Definir vários segmentos de subsídio
Para peças grandes e de formato complexo, é aconselhável definir dois ou mais segmentos de tolerância com vários pontos de partida, conforme mostrado nas ilustrações.
Durante a programação, a forma é dividida em múltiplos segmentos e conectada sequencialmente para usinagem. O contorno é usinado primeiro, seguido pelos segmentos de tolerância.
