1. Introdução
Na fabricação de tubos de escape automotivos e peças tubulares semelhantes, problemas de qualidade, como rugas ou rasgos, ocorrem frequentemente devido a fatores como raio de curvatura e propriedades do material. É particularmente crucial reduzir ou eliminar estes problemas, a fim de melhorar a qualidade do produto e reduzir as taxas de desperdício.
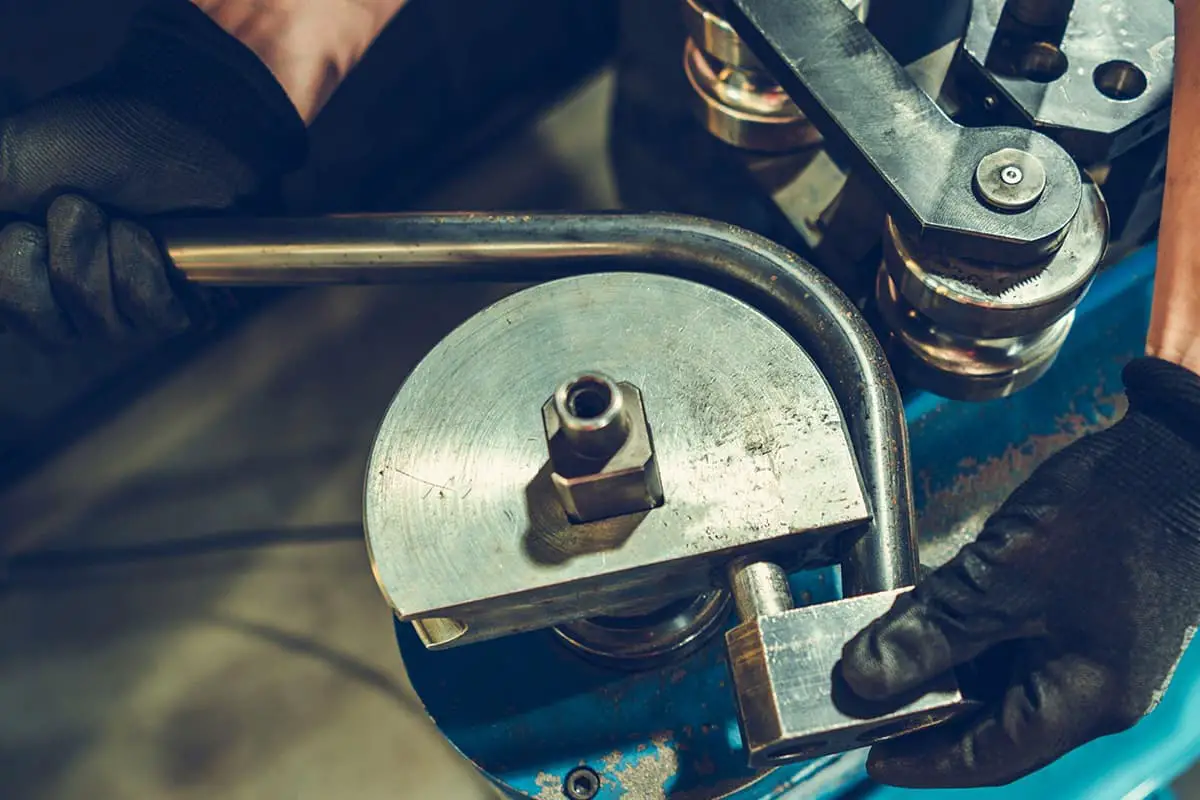
O processo de flexão dos tubos é comparável ao da chapa metálica: a parede externa da camada neutra é submetida a tensões de tração, afinando a parede, enquanto a parede interna da camada neutra sofre tensões de compressão, engrossando a parede. A deformação excessiva pode causar rachaduras na parede externa e enrugamento na parede interna. A Tabela 1 apresenta os raios de curvatura mínimos para tubos de aço.
Tabela 1: Raio de curvatura mínimo (R) para tubos de aço
![]() |
Espessura da parede | Raio de curvatura mínimo R |
0,02D | 4D | |
0,05D | 3.6D | |
0,10D | 3D | |
0,15D | 2D |
Os métodos de dobra de tubos geralmente incluem: dobra com ferramentas manuais de dobra de tubos; dobra com máquinas de dobra de tubos dedicadas; método de flexão anti-deformação; flexão por extrusão a frio; prensagem de molde para formar cotovelos; flexão por extrusão a quente da haste central. Este artigo se concentra principalmente no uso de máquinas curvadoras de tubos dedicadas como exemplos para analisar problemas de enrugamento e rasgo.
2. O processo de dobrar tubos usando uma máquina curvadora de tubos dedicada.
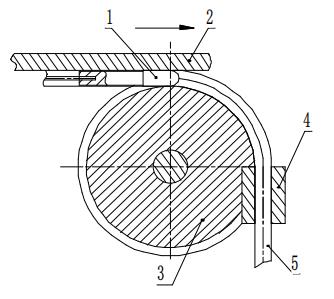
1. Mandril
2. Placa guia
3. Morra
4. Bloco de pressão
5. Componente do tubo
O dobrador de tubos dedicado normalmente usa um mandril para dobrar. O processo envolve a montagem da matriz, item 3, em um fuso giratório da máquina. Antes de o tubo ser dobrado, ele é fixado na matriz pelo bloco de pressão, item 4. Um mandril, item 1, é inserido dentro do tubo. Quando a máquina é iniciada, o material do tubo curva-se gradualmente em torno da matriz para tomar forma.
3. Análise de Elementos de Controle e Métodos de Controle Correspondentes
3.1 Raio de Curvatura
Durante o processo de dobra, um raio de curvatura menor pode causar enrugamento no lado interno ou até mesmo rachaduras na parede externa. O projeto deve levar em consideração a espessura da parede do tubo, o diâmetro externo e as propriedades do material. A Tabela 1 deve ser consultada ao escolher o raio de curvatura.
Empiricamente, ao utilizar um mandril cilíndrico regular para dobra, o raio mínimo de curvatura pode ser um pouco menor do que o indicado na Tabela 1, desde que não cause enrugamento ou trincas. Quando um raio de curvatura menor é necessário, a espessura da parede do tubo pode ser aumentada, o diâmetro externo reduzido e um material com boa ductilidade e exterior liso deve ser selecionado.
3.2 Formato do Mandril e Posição de Fixação
3.2.1 Posição de Trabalho do Mandril
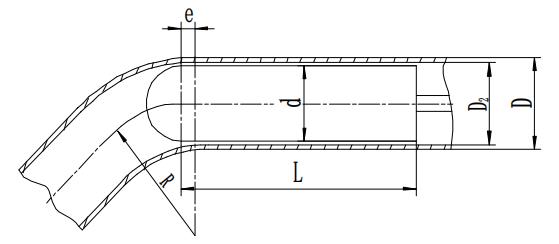
Na dobra do núcleo de tubos, o formato e a posição operacional do mandril têm um impacto significativo na qualidade da dobra do tubo. Normalmente, o diâmetro d do mandril deve ser 0,5-1,5 mm menor que o diâmetro interno do tubo, facilitando a inserção no tubo.
A distância e do ponto onde o mandril entra no tubo até o início do processo de dobra (ver Figura 2) pode ser calculada usando a seguinte fórmula empírica.
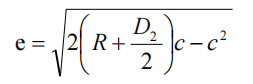
Na equação,
- e – a distância onde o mandril começa a dobrar dentro do tubo
- R – o raio de curvatura da camada central da seção transversal
- D2 – o diâmetro interno do tubo
- c – a folga entre o diâmetro interno do tubo e o mandril. Normalmente, c é escolhido entre 0,5 e 1,5 mm.
3.2.2 Seleção do formato do mandril
Existem vários formatos de mandris, divididos aproximadamente em: mandris cilíndricos padrão, mandris em forma de colher, mandris de arame e mandris de eixo flexível. O mandril cilíndrico padrão é frequentemente utilizado devido à sua estrutura simples, facilidade de fabricação e fácil remoção após dobramento.
Contudo, uma vez que a área de contacto entre o mandril e a parede do tubo é pequena, é menos eficaz na prevenção da criação de uma forma elíptica.
O comprimento do mandril, indicado como L, deve ser (ver Fig. 2)
L = (3 a 5) d mm
Quando o diâmetro d do mandril é grande, o coeficiente assume um valor menor e vice-versa.
3.2.3 Controle da folga entre o mandril e a parede interna das conexões para tubos
Se a folga entre o mandril e a parede interna dos acessórios para tubos for muito grande, no início do processo de dobra, o mandril e a parede do tubo não se tocam totalmente, causando enrugamento severo no lado interno dos acessórios para tubos, e a ocorrência de curvas mortas. Se a folga for muito pequena, ao fixar um tubo soldado normal, a altura irregular da solda na parede interna da conexão do tubo pode dificultar a inserção do mandril na conexão do tubo.
Através de um longo período resumindo o trabalho de flexão de tubos, o autor determinou uma folga mais apropriada entre a parede interna do tubo e o mandril:
c = D2 – d = 0,5 a 1,5 mm.
3.3 Ajuste de velocidade da placa guia
Nas operações padrão de dobra de tubos em dobradeiras, as placas guia (Figura 1) prendem a peça de trabalho e se movem em sincronia com ela. A velocidade desta placa guia é ajustável e sua velocidade de movimento influencia diretamente na qualidade do tubo dobrado.
A peça de trabalho, fixada pelo bloco de prensa na matriz, contém um mandril dentro dela. À medida que a máquina opera, o material do tubo curva-se gradualmente em torno da matriz, com a placa guia avançando em sincronia com a velocidade da matriz. Durante este processo, o atrito estático entre a placa guia e a peça atua na peça.
Se a velocidade da placa guia for maior que a da matriz, ela transmite um impulso para frente na peça de trabalho; inversamente, aplica uma força de resistência se sua velocidade for menor. Os testes de flexão mostram que, em condições iguais, se a velocidade da placa guia exceder substancialmente a velocidade linear da matriz, tendem a formar-se rugas na parede interna do tubo.
Por outro lado, se a velocidade da placa guia for significativamente atrasada, a parede externa do tubo ficará visivelmente mais fina, até o ponto de rasgar. Portanto, ajustar efetivamente a velocidade de impulso da placa guia para corresponder à velocidade da matriz é crucial para garantir a qualidade da dobra.
A partir desta análise, fica claro que a velocidade de impulso da placa guia deve estar sincronizada com a velocidade de dobra durante o processo de dobra. Portanto, antes de dobrar ou depois de mudar para uma matriz com raio de curvatura diferente, é necessário ajustar a velocidade da placa guia de acordo.
Conforme mostrado na Figura 1, a velocidade de curvatura α e o raio de curvatura R são predefinidos. É calculado o comprimento do arco que a matriz de dobra deve girar, ou seja, a distância que a placa guia deve avançar de forma síncrona ao mesmo tempo. A dobradeira fica em marcha lenta enquanto o operador gira lentamente a alavanca da válvula de controle de velocidade, observando o movimento da placa guia.
Após dobrar até o ângulo definido e parar, o deslocamento real da placa guia é medido com uma régua, comparando-o com o cálculo teórico. Se forem diferentes, o ajuste da marcha lenta pode ser repetido até que o valor medido corresponda ao valor calculado.
Na realidade, devido aos fatores de carga, a velocidade de movimento da placa guia durante a flexão real é muitas vezes mais lenta do que durante a marcha lenta. Portanto, ao ajustar a velocidade de impulso da placa guia, o valor real pode ser ligeiramente superior ao valor teórico.
4. Conclusão
Concluindo, a presença de rugas, rasgos ou deformidades elípticas no tubo é uma medida importante da qualidade da dobra.
Esses defeitos de qualidade podem ser minimizados selecionando um raio de curvatura adequado, um formato de mandril apropriado, controlando a folga entre o mandril e a parede interna do tubo, ajustando a posição de inserção do mandril e a velocidade de movimento da placa guia.