Conceitos Básicos
Elementos de liga são elementos químicos adicionados especificamente ao aço para garantir as propriedades estruturais, físicas, químicas e mecânicas desejadas.
As impurezas referem-se a elementos químicos que são introduzidos durante o processo de fundição através de matérias-primas ou métodos de fundição.
O aço carbono é uma liga ferro-carbono com teor de carbono variando de 0,0218% a 2,11%.
O aço-liga é o aço ao qual foi adicionado uma certa quantidade de elementos de liga à base de aço carbono.
Aço de baixa liga geralmente se refere ao aço com um teor total de elementos de liga menor ou igual a 5%.
Aço de liga média geralmente se refere ao aço com um teor total de elementos de liga entre 5% e 10%.
Aço de alta liga geralmente se refere ao aço com um teor total de elementos de liga superior a 10%.
Aço microligado é o aço que possui elementos de liga (como V, Nb, Ti, Zr, B) com conteúdo menor ou igual a 0,1%, o que pode afetar significativamente a estrutura e as propriedades.
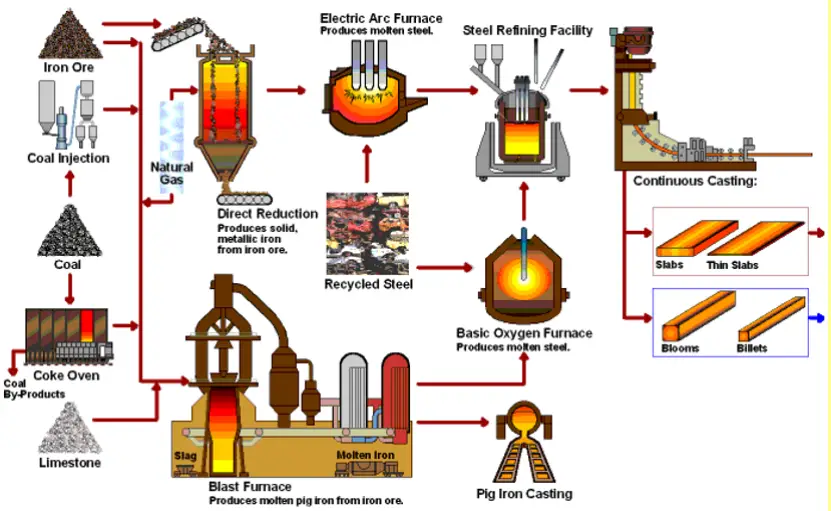
Linha siderúrgica
Impurezas Comuns em Aço Carbono
1. Manganês (MN) e silício (SI)
O manganês (Mn) entra no aço durante a fabricação do aço por meio de desoxidantes ou ferro-gusa residual. No aço carbono, o teor de Mn é normalmente inferior a 0,8%. Pode dissolver-se no aço e também formar inclusões MNS de alto ponto de fusão (1600°C).
As inclusões de MnS têm certa plasticidade em altas temperaturas e não causam fragilização do aço a quente. Após o processamento, o sulfeto de manganês é distribuído em forma de tira ao longo da direção de laminação.
O teor de silício (Si) no aço é geralmente inferior a 0,5%. Também pode dissolver-se no aço e formar inclusões de SiO.
Embora Mn e Si sejam impurezas benéficas, a presença de inclusões de MnS e SiO pode reduzir a resistência à fadiga, a plasticidade e a tenacidade do aço.
2. Enxofre (S) e fósforo (P)
S: A solubilidade do S no ferro sólido é muito pequena. Quando S e Fe se combinam, eles podem formar FeS, o que facilita a formação de um eutético de baixo ponto de fusão. Isto pode levar à fragilização térmica e rachaduras.
P: Embora seja solúvel em α-Ferro, a presença de fósforo reduz significativamente a tenacidade do aço, especialmente em baixas temperaturas, o que é conhecido como fragilização a frio. No entanto, o fósforo pode melhorar a resistência à corrosão do aço na atmosfera.
S e P são considerados impurezas prejudiciais no aço. No entanto, eles podem melhorar a usinabilidade do aço.
3. Nitrogênio (N), hidrogênio (H), oxigênio (O)
N: O aço contendo n supersaturado precipita nitretos após deformação a frio, através de um processo conhecido como envelhecimento mecânico ou envelhecimento por deformação.
Além disso, o N pode formar nitretos estáveis com elementos como vanádio, titânio e cromo, o que pode levar ao refinamento do grão e ao fortalecimento da precipitação.
H: O efeito combinado da tensão residual e do hidrogênio pode causar fragilização no aço, o que pode levar à falha do material.
Ó: O aço pode formar compostos de silicato como 2MnO · SiO2, MnO · SiO, ou óxidos compostos como MgO · Al2O3, MnO · Al2O3.
N, H e O são considerados impurezas prejudiciais no aço.
Classificação do Aço Carbono
1. De acordo com o teor de carbono no aço
1) Classificação de acordo com Fe Fe3Diagrama de fase C
- Aço hipoeutetóide: 0,0218% ≤ WC ≤ 0,77%
- Aço eutetóide: Wc=0,77%
- Aço hipereutetóide: 0,77% < WC ≤ 2,11%

2) Classificação por teor de carbono no aço
- Aço de baixo carbono: WC ≤ 0,25%
- Aço carbono médio: 0,25% < WC ≤ 0,6%
- Aço de alto carbono: WC > 0,6%
2. De acordo com a qualidade do aço (qualidade)
(1) Aço carbono comum:
CS ≤ 0,05%, WP ≤ 0,045%.
(2) Aço carbono de alta qualidade:
cS≤0,035%,wP≤0,035%
(3) Aço carbono de alta qualidade:
cS≤0,02%,wP≤0,03%
(4) Aço carbono de super qualidade:
cS≤0,015%,wP≤0,025%
3. Classificação de acordo com a utilização do aço
(1) Aço Estrutural Carbono:
O aço estrutural de carbono é utilizado principalmente em vários componentes de engenharia, incluindo pontes, navios, componentes de construção, etc. Além disso, também pode ser utilizado em peças menos críticas.
(2) Aço Estrutural de Carbono de Alta Qualidade:
O aço estrutural de carbono de alta qualidade é usado principalmente na fabricação de diversas peças de máquinas, como eixos, engrenagens, molas, bielas, etc.
(3) Aço para ferramentas de carbono:
O aço carbono para ferramentas é utilizado principalmente na fabricação de diversas ferramentas, como ferramentas de corte, moldes, ferramentas de medição, etc.
(4) Aço Carbono Fundido para Engenharia Geral:
O aço carbono fundido para engenharia geral é usado principalmente na fabricação de peças com formato complexo que requer certa resistência, plasticidade e tenacidade.
4. Classificação de acordo com o grau de desoxidação durante a fundição do aço
(1) Aço com aro refere-se ao aço com desoxidação incompleta, com código F.
(2) Aço morto refere-se ao aço com desoxidação completa, com código denominado Z.
(3) Aço semi-acabado refere-se ao aço com grau de desoxidação entre o aço de borda e o aço morto, com código B.
(4) Aço morto especial refere-se ao aço com desoxidação especial, com código denominado TZ.
Uso de Aço Carbono
1. Aço estrutural de carbono comum
a. É usado principalmente para estruturas de engenharia em geral e peças comuns.
Geralmente é laminado em placas de aço, tiras de aço, tubos de aço, fio-máquina, perfis de aço, barras de aço ou perfis diversos (aço redondo, aço quadrado, viga I, reforço, etc.), que podem ser usados para soldagem, rebitagem , parafusos e outras peças estruturais.
É amplamente utilizado (mais de 70% da produção total de aço).
b. O resfriamento a ar após a laminação a quente é o estado usual de fornecimento desse tipo de aço.
Os usuários geralmente não precisam realizar tratamento térmico, mas sim utilizá-lo diretamente.
cC =0,06%~0,38%.
Quando o grau de qualidade é “A” e “B”, a composição química pode ser ajustada adequadamente de acordo com a necessidade do demandante com garantia de propriedades mecânicas.
c. Designação de aço estrutural de carbono comum
É composto por letras (Q) representando o limite de escoamento, valor do limite de escoamento, símbolos de grau de qualidade (A, B, C, D) e símbolos do método de desoxidação (F, b, Z, TZ) em sequência.
O valor do limite de escoamento é dividido em cinco graus de resistência: 195, 215, 235, 255 e 275;
O símbolo de grau refere-se ao símbolo de grau de qualidade utilizado exclusivamente para este tipo de aço, que também é dividido de acordo com o número de impurezas S e P. Quatro símbolos A, B, C e D representam quatro graus, entre os quais:
- Classe A wS ≤ 0,05%, WP ≤ 0,045%,
- Classe B wS ≤ 0,045%, WP ≤ 0,045%,
- Classe C wS ≤ 0,04%, WP ≤ 0,04%,
- Nível D wS ≤ 0,035%, WP ≤ 0,035%
Dentre eles, o grau de qualidade mais alto é o grau D, que atinge o grau de alta qualidade do aço estrutural de carbono. As classes A, B e C pertencem todas à gama de classes normais.
O símbolo do método de desoxidação pode ser omitido nas classes de aço morto e aço morto especial.
d. Marca típica, desempenho e aplicação
Q195, Q215:
O teor de carbono é muito baixo e a resistência não é alta, mas possui boa plasticidade, tenacidade e desempenho de soldagem.
É frequentemente usado como peças de trabalho com baixos requisitos de resistência, como pregos, fios de ferro, janelas de aço e diversas placas finas.
Q235A, Q255A:
É utilizado para tirantes, pequenos eixos, correntes, etc. em máquinas e ferramentas agrícolas.
Também é utilizado para reforço de edifícios, chapas de aço, perfis de aço, etc;
Q235B, Q255B:
É utilizado como peças estruturais soldadas com altos requisitos de qualidade em projetos de construção, e eixos giratórios em geral, ganchos, quadros de bicicletas, etc.
Q235C, Q235D:
A qualidade é boa e pode ser usada como algumas peças estruturais de soldagem importantes e peças de máquinas.
Q255, Q275:
A resistência é alta, entre as quais Q275 é o aço de médio carbono, que pode ser usado para fabricar embreagem de fricção, correia de aço para freio, etc.
2. Aço estrutural de carbono de alta qualidade
(1) Para peças mecânicas importantes, as propriedades mecânicas das peças podem ser ajustadas através de vários tratamentos térmicos.
(2) O estado de fornecimento pode ser resfriamento a ar após laminação a quente, recozimento, normalização e outros estados, o que geralmente depende das necessidades dos usuários.
(3) A marca é geralmente representada por dois dígitos.
Esses dois números representam dez mil vezes a fração mássica média de carbono no aço, como o aço 20 e o aço 45.
a. Três tipos de aço estrutural de carbono de alta qualidade são aços com aros, que são 08F, 10F e 15F.
O aço semi-morto é marcado com “b” e o aço morto geralmente não é marcado com símbolos.
b. O aço estrutural de carbono de alta qualidade é marcado com “A” após a marca, e o aço estrutural de carbono de alta qualidade é marcado com “E”.
c. Para aços estruturais carbono especiais de alta qualidade, também deve ser adicionado um símbolo representando a finalidade do produto no início (ou fim) da marca, como aço para caldeira com teor médio de carbono de 0,2%, cuja marca é “20g ”, etc.
d. O aço estrutural de carbono de alta qualidade é dividido em dois grupos: teor de manganês comum e maior teor de manganês de acordo com os diferentes teores de manganês.
Para o grupo com alto teor de manganês, adicionar “Mn” no final do seu número, como 15Mn, 45Mn, etc.
e. Existem 31 tipos de aço estrutural de carbono de alta qualidade
Aço 08F: baixa fração mássica de carbono, boa plasticidade e baixa resistência.
Pode ser usado para todos os tipos de peças formadoras de deformação a frio.
Aço 10 ~ 25: possui boas propriedades de soldagem e estampagem a frio e pode ser usado para fabricar peças padrão, luvas de eixo, recipientes, etc.
Também pode ser usado para fabricar peças resistentes ao desgaste e ao impacto com alta dureza superficial e alta resistência e tenacidade no coração.
Como engrenagens, cames, pinos, placas de fricção, pregos de cimento, etc.
45 aço de médio carbono: boas propriedades mecânicas abrangentes podem ser obtidas por tratamento térmico adequado.
Ele pode ser usado para peças mecânicas, como eixo de transmissão, biela do motor, engrenagem de máquinas-ferramenta, etc.
Aço estrutural de alto carbono: após tratamento térmico adequado, pode obter alto limite elástico, índice de rendimento, tenacidade suficiente e resistência ao desgaste.
Pode fabricar molas, trilhos pesados, rolos, pás, cabos de aço, etc. com pequenos diâmetros de fio.
Classes de aço estrutural de carbono de alta qualidade, características de desempenho e aplicações
Nota | Características de desempenho | Exemplos de uso |
08F, 08, 10 | Boa plasticidade, tenacidade e baixa resistência | Chapas laminadas a frio, tiras de aço, fios de aço, chapas de aço, produtos de estampagem, como conchas, recipientes, tampas, cartuchos de bala, painéis de instrumentos, juntas, arruelas, etc. |
15, 20, 25, 15 minutos, 20 minutos | Boa plasticidade e tenacidade, com um certo grau de resistência | Peças de suporte de carga que não requerem tratamento térmico, como parafusos, porcas, tirantes, flanges, peças carburadas que podem ser transformadas em engrenagens, eixos, cames, etc. |
30, 35, 40, 45, 50, 55, 30Mn, 40Mn, 50Mn | Boa resistência, plasticidade e tenacidade | Produz principalmente peças como engrenagens, bielas e eixos, entre as quais 40 aço e 45 aço são amplamente utilizados. |
60, 65, 70, 60Mn, 65Mn | Alta elasticidade e resistência ao escoamento | Muitas vezes produzem peças elásticas e facilmente desgastadas, como molas, arruelas de pressão, rolos, arados, etc. |
3. Aço carbono para ferramentas
(1) É usado principalmente para fazer várias ferramentas pequenas.
Pode ser temperado e revenido em baixa temperatura para obter alta dureza e alta resistência ao desgaste.
Ele pode ser dividido em aço para ferramentas de carbono de alta qualidade e aço para ferramentas de carbono de alta qualidade.
(2) A marca registrada é geralmente expressa pelo símbolo simbólico “T” (o prefixo fonético chinês do carbono) mais mil vezes a fração de massa do carbono. Como T10, T12, etc.
Geralmente, o aço para ferramentas de carbono de alta qualidade não adiciona o símbolo de grau de qualidade, enquanto o aço para ferramentas de carbono de alta qualidade adiciona a palavra “a” após seu número, como T8A, T12, etc.
(3) A fração mássica de manganês em aço para ferramentas contendo manganês pode ser expandida para 0,6%.
Neste momento, Mn está marcado no final da marca, como T8Mn, T8MnA.
(4) Aço para ferramentas de carbono típico
T7, T8: adequado para a fabricação de ferramentas de corte que suportam certo impacto e exigem alta tenacidade, como machados de marcenaria, cinzéis de bancada, etc. a dureza após têmpera e revenido em baixa temperatura é de 48 ~ 54HRC (parte de trabalho);
Aço T9, T10, T11: é usado para fabricar ferramentas de corte que exigem alta dureza e resistência ao desgaste devido a pequenos impactos, como pequenas brocas, machos, lâminas de serra manual, etc. 62HRC.
O aço T10A também pode ser usado para fabricar alguns moldes para trabalho a frio e ferramentas de medição com formato simples e pequena carga de trabalho;
Aço T12 e T13: a dureza e a resistência ao desgaste são as mais altas, mas a tenacidade é a pior.
É utilizado na fabricação de ferramentas de corte que não sofrem impacto, como limas, pás e raspadores. A dureza após têmpera e revenido a baixa temperatura é de 62 ~ 65 HRC.
O T12A também pode ser usado para fabricar ferramentas de medição.
T7~t12 e T7A~T12A também podem ser usados para moldes plásticos com formatos simples.
Classe, características de desempenho e aplicação de aço carbono para ferramentas
Nota | Características de desempenho | Exemplos de uso |
T7, T7A, T8, T8A, T8Mn | Boa tenacidade com uma certa dureza | Ferramentas para marcenaria, ferramentas de montagem, como martelos, cinzéis, moldes, tesouras, etc. T8Mn pode ser usado para fabricar ferramentas com seções transversais maiores |
T9, T9A, T10, T10A, T11, T11A | Maior dureza e certa tenacidade | Ferramentas de baixa velocidade, como plainas, machos, matrizes, lâminas de serra, calibradores, matrizes e matrizes de trefilação |
T12, T12A, T13, T13A | Alta dureza e baixa tenacidade | Ferramentas de baixa velocidade que não estão sujeitas a vibração, como limas, raspadores, ferramentas cirúrgicas e brocas |
4. Aço carbono fundido para engenharia geral
(1) É utilizado principalmente para peças ásperas de ferro fundido que não podem garantir sua plasticidade e seu formato é complexo, o que não é conveniente para forjamento.
Seu teor de carbono é geralmente inferior a 0,65%.
(2) A marca é representada pelo símbolo “ZG” (o prefixo fonético chinês do aço fundido) mais o valor mínimo do limite de escoamento – o valor mínimo de resistência à tração.
Por exemplo, ZG340-640 refere-se a aço fundido com resistência ao escoamento não inferior a 340MPa e resistência à tração não inferior a 640MPa.
(3) Aço fundido carbono típico
(4) Outros tipos de peças fundidas de aço incluem:
Fundições de aço carbono para estruturas soldadas
(GB/T7659-1987), como ZG230-450H;
Fundições de aço de baixa liga
(GB/T14408-1993), como ZGD535-720;
Fundições de aço resistentes ao calor
(GB/T8492-1987), como ZG40Cr30Ni20;
Fundições de aço inoxidável e resistentes a ácidos
(GB2100-1980), como ZG1Cr18Ni9Ti;
Fundições de aço inoxidável de média e alta resistência (GB6967-1986), como ZG10Cr13Ni1Mo, etc.
Propriedades do Aço Carbono
Os materiais são a base material das máquinas. As propriedades dos materiais metálicos são a principal base para a seleção do material.
As propriedades dos materiais metálicos são geralmente divididas em desempenho de processo e desempenho de serviço.
O desempenho do processo refere-se às propriedades dos materiais metálicos exibidas sob diversas condições de processamento, desde a fundição até os produtos acabados; o desempenho em serviço refere-se às propriedades dos materiais metálicos exibidas pelas peças metálicas sob condições de uso.
O desempenho de serviço dos materiais metálicos determina o seu âmbito de utilização. O desempenho do serviço inclui propriedades físicas, químicas e mecânicas.
1. Propriedades físicas.
(1) Densidade
A densidade de um metal é a massa de uma unidade de volume do metal, expressa em kg/m3.
Com base na sua densidade, os materiais metálicos podem ser classificados em metais leves e metais pesados. Metais com densidade inferior a 4,5 g/cm3 são chamados de metais leves, como alumínio, titânio, etc.
(2) Ponto de fusão
A temperatura na qual um metal passa do estado sólido para o estado líquido é chamada de ponto de fusão, geralmente expressa em graus Celsius (℃). Cada metal tem um ponto de fusão fixo. Por exemplo, o ponto de fusão do chumbo é 323 ℃ e o ponto de fusão do aço é 1538 ℃. O ponto de fusão é importante para refino, fundição, soldagem e preparação de ligas.
Metais com ponto de fusão abaixo de 1.000 ℃ são chamados de metais de baixo ponto de fusão, aqueles com ponto de fusão entre 1.000 e 2.000 ℃ são chamados de metais de ponto de fusão médio e aqueles com ponto de fusão superior a 2.000 ℃ são chamados de metais de alto ponto de fusão. metais com ponto de fusão.
(3) Condutividade térmica
A capacidade de um material metálico de conduzir calor é chamada de condutividade térmica. A qualidade da condutividade térmica dos materiais metálicos é geralmente expressa em termos de condutividade térmica (coeficiente de condutividade térmica) λ.
Metais com alta condutividade térmica apresentam boa condutividade térmica. Em geral, os materiais metálicos têm melhor condutividade térmica do que os materiais não metálicos. A prata tem a melhor condutividade térmica entre todos os metais, seguida pelo cobre e pelo alumínio.
Metais com boa condutividade térmica também apresentam boa dissipação de calor e podem ser usados na fabricação de peças dissipadoras de calor, como aletas de radiadores de refrigeradores e condicionadores de ar.
(4) Expansão térmica
Quando um material metálico é aquecido, seu volume aumentará e encolherá quando resfriado. Este fenômeno é chamado de expansão térmica. Diferentes metais têm diferentes propriedades de expansão térmica.
No trabalho prático, o efeito da expansão térmica deve, por vezes, ser considerado. Por exemplo, algumas ferramentas de medição de precisão devem ser feitas de metais com pequenos coeficientes de expansão; colocar trilhos, erguer pontes, medir dimensões em processos de usinagem, etc., todos precisam considerar o fator de expansão térmica.
(5) Condutividade elétrica
A capacidade de um material metálico de conduzir eletricidade é chamada de condutividade elétrica. No entanto, a condutividade elétrica de cada metal é diferente. A prata tem a melhor condutividade elétrica entre todos os metais, seguida pelo cobre e pelo alumínio.
Na indústria, o cobre e o alumínio são utilizados como materiais condutores. Materiais metálicos de alta resistência e baixa condutividade elétrica, como ligas de ferro-cromo, ligas de níquel-cromo-alumínio, Constantan, manganês-cobre, etc., são usados para fabricar peças de instrumentos ou elementos de aquecimento elétrico, como fios de fornos.
(6) Magnetismo
A capacidade de um metal de conduzir fluxo magnético é chamada de magnetismo. Materiais metálicos com condutividade magnética podem ser atraídos por ímãs.
Ferro, cobalto, etc., são materiais ferromagnéticos, e manganês, cromo, cobre e zinco são materiais diamagnéticos ou paramagnéticos.
No entanto, para alguns metais, o magnetismo não é fixo e imutável, como o ferro que não apresenta magnetismo ou paramagnetismo acima de 768 ℃.
Materiais ferromagnéticos podem ser usados para fazer núcleos de transformadores, núcleos de motores, peças de instrumentos de medição, etc.; materiais diamagnéticos ou paramagnéticos podem ser usados para peças que não requerem interferência de campo magnético.
2. Propriedades químicas.
As propriedades químicas dos materiais metálicos referem-se às propriedades exibidas pelos metais sob reações químicas.
(1) Resistência à corrosão
A capacidade de um material metálico resistir à corrosão do oxigênio, vapor de água e outros meios químicos em temperatura normal é chamada de resistência à corrosão. A ferrugem do aço é um exemplo comum de corrosão.
(2) Resistência à oxidação
A capacidade de um material metálico de resistir à oxidação é chamada de resistência à oxidação. Quando um material metálico é aquecido, a reação de oxidação acelera.
Por exemplo, durante operações de aquecimento, como forjamento, tratamento térmico e soldagem de aço, podem ocorrer oxidação e descarbonetação, causando perda de material e vários defeitos.
Portanto, ao aquecer tarugos ou materiais, um gás redutor ou gás protetor é frequentemente formado em torno deles para evitar a oxidação de materiais metálicos.
(3) Estabilidade química
A estabilidade química refere-se à soma da resistência à corrosão e à oxidação dos materiais metálicos. A estabilidade química dos materiais metálicos em altas temperaturas é chamada de estabilidade térmica.
Os materiais metálicos utilizados na fabricação de peças que operam em altas temperaturas devem apresentar boa estabilidade térmica.
3. Propriedades mecânicas.
As propriedades mecânicas, também conhecidas como propriedades de resistência, referem-se às propriedades exibidas pelos materiais sob a ação de forças.
As principais propriedades mecânicas incluem resistência, plasticidade, dureza, tenacidade e resistência à fadiga.
(1) Força
Resistência refere-se à capacidade de um metal de resistir à deformação permanente (deformação plástica) e à fratura. Os critérios de resistência comumente usados são o ponto de escoamento (anteriormente conhecido como limite de escoamento ou limite de escoamento) e a resistência à tração.
O método para determinação dos critérios de resistência é através de um ensaio de tração.

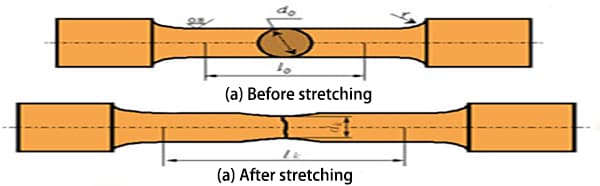
Curva de tração: a relação entre a força de tração (F) e o alongamento (l-lo).
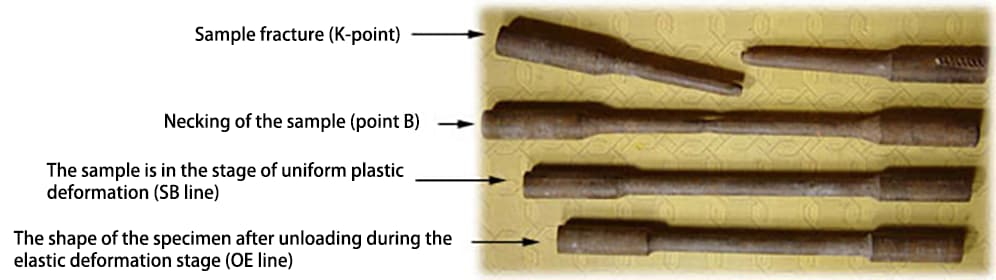
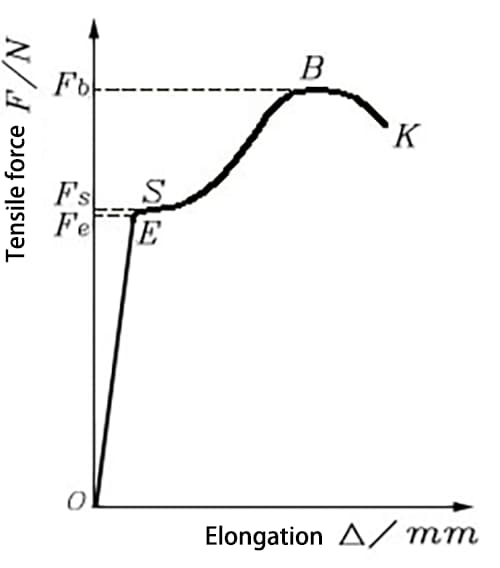
Quando um material é submetido a forças externas, a força de interação interna entre os elementos do material é chamada de força interna, que é igual em magnitude e oposta em direção à força externa. A força interna por unidade de área é chamada de tensão e é denotada pelo símbolo σ.
Limite elástico
A tensão máxima que uma amostra pode suportar quando sofre deformação elástica completa.
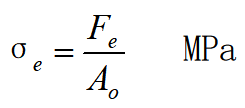
onde σe é o limite elástico em unidades de tensão (como MPa ou psi), Fe é a força de tração máxima que a amostra pode suportar quando sofre deformação elástica completa, medida em unidades de força (como N ou lbf), e Aó é a área da seção transversal original da amostra, medida em unidades de área (como mm2 ou em2).
Ponto de rendimento
Definição: A tensão na qual uma amostra deixa de se comportar elasticamente e se torna permanentemente deformada durante o processo de teste, enquanto a força permanece constante ou diminui.
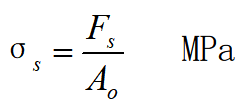
Onde:
Fé – Força de tração quando o corpo de prova sofre escoamento, em N.
Aó – Área da seção transversal original da amostra, em mm2.
Força de rendimento condicional:
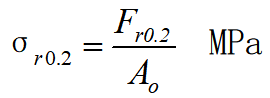
Resistência à tracção
Definição: A tensão máxima que uma amostra pode suportar antes de quebrar durante o processo de teste de tração.
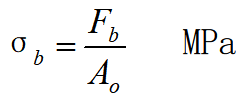
Onde:
Fb – A força de tração máxima que a amostra pode suportar antes de quebrar, em N.
Aó – Área da seção transversal original da amostra, em mm2.
Razão entre resistência ao escoamento e resistência à tração (σé/σb)
Os materiais de engenharia requerem não apenas alta resistência à tração, mas também uma certa relação entre limite de escoamento e resistência à tração (σé/σb). Quanto menor a relação entre a resistência ao escoamento e a resistência à tração, maior será a confiabilidade do componente e ele não quebrará imediatamente sob sobrecarga durante o uso. No entanto, se a relação entre a resistência ao escoamento e a resistência à tração for muito pequena, a taxa de utilização efetiva da resistência do material diminuirá.
(2) Plasticidade
Refere-se à capacidade de um material sofrer deformações irreversíveis e permanentes antes de quebrar. O critério de ductilidade é determinado pelo alongamento após a fratura e pela redução da área da seção transversal.
(1) Alongamento após fratura
O alongamento após a fratura refere-se ao aumento percentual no comprimento da amostra após sua ruptura durante o processo de teste de tração em comparação com seu comprimento de referência original.
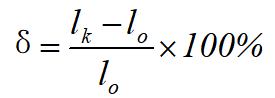
Refere-se à capacidade de um material sofrer deformações irreversíveis e permanentes antes de quebrar. O critério de ductilidade é determinado pelo alongamento após a fratura e pela redução da área da seção transversal.
(2) Redução da área transversal após fratura
A redução na área da seção transversal após a fratura refere-se à diminuição percentual na redução máxima na área da seção transversal no ponto de estrangulamento da amostra após ela ter quebrado durante o processo de teste de tração em comparação com sua área da seção transversal original.
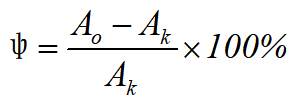
(3) Dureza
A dureza é a medida da capacidade de um material resistir à deformação local, particularmente deformação plástica, indentação ou arranhões. Ele determina se um material é macio ou duro.
Atualmente, os métodos de teste de dureza mais comumente usados são o teste de dureza Brinell, o teste de dureza Rockwell e o teste de dureza Vickers.
(1) Dureza Brinell
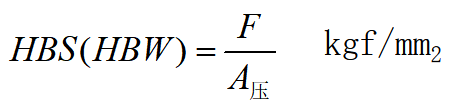
Onde:
- Ap – Superfície esférica do recuo, em mm2.
- D – Diâmetro do penetrador, em mm.
- d – Diâmetro médio do recuo, em mm.
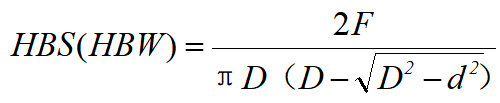
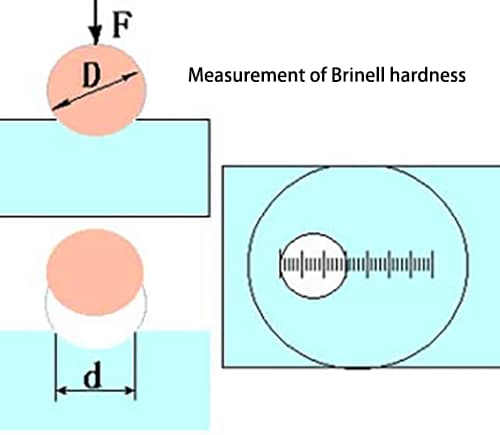
(A força de teste F é medida em kgf)
O método de representação da dureza Brinell é o seguinte:
- 140HBS10/10000/30
- 500HBW5/7500
Normalmente, ao especificar o valor de dureza Brinell para um requisito de material em um desenho de peça ou documento de processo, as condições de teste não são especificadas. Apenas a faixa de dureza necessária e o símbolo de dureza são marcados, como 200 ~ 230HBS.
HBS é usado para testar materiais com valor de dureza inferior a 450; O HBW é usado para medir materiais com valor de dureza na faixa de 450-650.
A dureza Brinell é usada principalmente para determinar a dureza de ferro fundido, metais não ferrosos e materiais de aço recozidos, normalizados e temperados e revenidos, como produtos semiacabados e matérias-primas.
(2) Dureza Rockwell
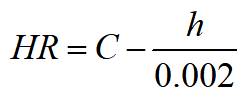
Na fórmula, C é uma constante. Quando o penetrador for um cone de diamante, C = 100; quando o penetrador é uma esfera de aço endurecido, C = 130.
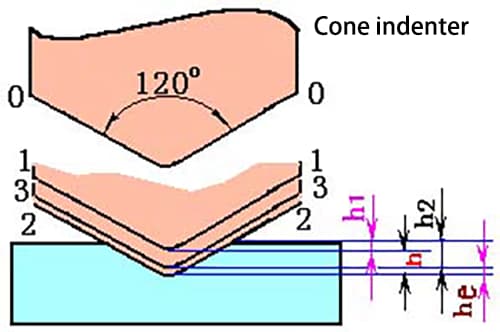
1- A posição do êmbolo após adicionar a carga inicial.
2- A posição do êmbolo após adicionar a carga inicial e a carga principal.
3- A posição do êmbolo após a retirada da carga principal.
ele: Recuperação elástica após remoção da carga principal.
Especificação comum da escala Rockwell | ||||
Símbolo de dureza | Tipo de cabeça | Força total de teste (kgf) | Faixa efetiva de valor de dureza | Exemplos de aplicação |
RH | Cone de diamante de 120° | 60 | 60~88 | Liga dura, têmpera de superfície, aço de cementação, etc. |
HRB | φ esfera de aço de 1,588 mm | 100 | 20~100 | Metais não ferrosos, aço recozido, normalizado, etc. |
CDH | Cone de diamante de 120° | 150 | 20~70 | Aço temperado, aço temperado e temperado, etc. |
Nota: Força total de teste=força de teste inicial+força de teste principal; A força de teste inicial é 10kgf (98,07N)
Tomando como exemplo o aço GCr15 temperado e revenido a baixa temperatura, meça o valor HRC.
A dureza Rockwell não possui unidade de medida, portanto o símbolo da escala de dureza deve ser indicado. O valor da dureza é escrito antes do símbolo, como 60HRC, 80HRA e 90HRB. Não há correspondência entre as diferentes escalas de dureza Rockwell, portanto os valores de dureza não podem ser comparados diretamente.
O teste de dureza Rockwell é simples, rápido e deixa uma pequena marca. É usado principalmente para testar peças acabadas com alta dureza após tratamento térmico e peças finas. Para materiais com estrutura e dureza irregulares, o valor da dureza flutua muito e sua precisão não é tão boa quanto a dos valores de dureza Brinell.
(3) Dureza Vickers

Na fórmula,
- F é a força de teste em Newtons (N),
- Ao é a área superficial do recuo em milímetros quadrados (mm²),
- d é a média aritmética dos comprimentos diagonais do recuo em milímetros (mm).
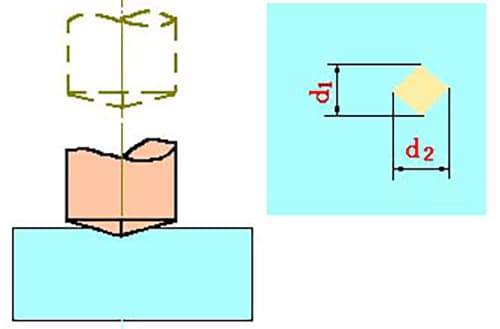
Tomando como exemplo o aço T8A temperado e revenido a baixa temperatura, meça o valor HV.
Os valores de dureza Vickers geralmente não são marcados com unidades e o valor de dureza é escrito antes do símbolo HV.
O teste de dureza Vickers tem uma pequena força de teste (comumente usada 49,03N), indentação rasa, perfil claro, resultados precisos e uma ampla faixa de seleção de força de teste (49,03 ~ 980,7N). Portanto, ele pode medir a dureza dos materiais de macios a duros, e os valores de dureza Vickers podem ser comparados diretamente.
A dureza Vickers é comumente usada para testar a dureza de materiais de chapa fina, revestimentos metálicos e camadas de peças com superfície endurecida. No entanto, o teste é complicado e não é adequado para inspeções de rotina na produção em massa.
Nota especial: Os valores de dureza obtidos por vários métodos de teste de dureza não podem ser comparados diretamente. Eles devem ser convertidos em um determinado valor de dureza por meio de uma tabela de conversão de dureza antes de comparar a dureza relativa.
(4) Tenacidade e resistência à fadiga
(1) Resiliência
Tenacidade refere-se à capacidade de um metal de absorver energia de deformação antes da fratura, que pode ser usada para medir a resistência de um material metálico a cargas de impacto.
O critério de tenacidade é determinado através de testes de impacto.
Teste de medição de energia de absorção de impacto de aço 40Cr:
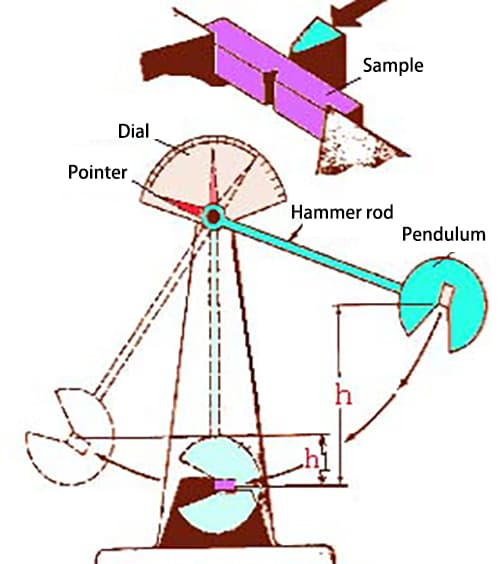
(5) Resistência à fadiga
Tensão cíclica: A magnitude e a direção da tensão sofrem mudanças periódicas ao longo do tempo.
O fenômeno de fratura de um componente sob tensão cíclica, muitas vezes em um nível de tensão muito inferior ao σ do materialb ou até menor que seu σé resistência, é chamada de fadiga do metal. O critério para fadiga do metal é a resistência à fadiga.
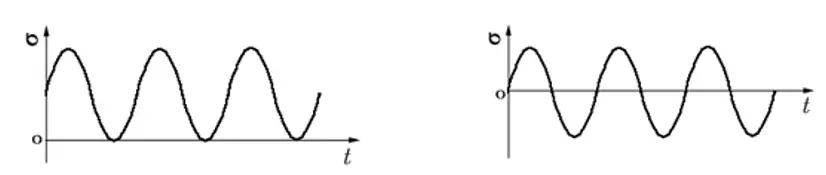
Foi comprovado que quando o nível de tensão σ está abaixo de um determinado valor, o material pode sofrer um número infinito de tensões cíclicas sem fraturar, e esse nível de tensão é chamado de resistência à fadiga.
Na engenharia, a resistência à fadiga refere-se à tensão máxima que não causa fratura sob um certo número de ciclos.
Geralmente, o número do ciclo de tensão é definido como 108 para materiais de aço e 107 para metais não ferrosos.
O projeto razoável da estrutura do componente, evitar a concentração de tensão, reduzir os valores de rugosidade da superfície, laminação da superfície, tratamento de shot peening, tratamento térmico da superfície, etc.
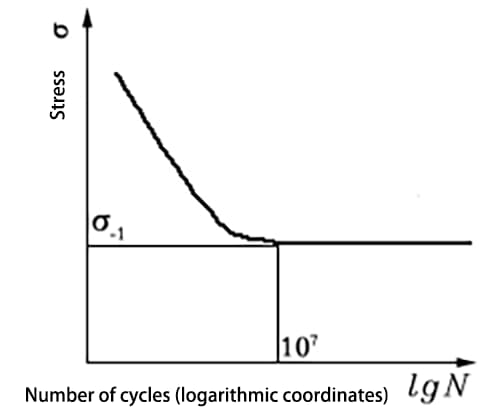