Causas de falha por fadiga de estruturas soldadas
As causas da falha por fadiga de estruturas soldadas incluem principalmente os seguintes aspectos:
① Objetivamente, a capacidade de carga estática das juntas soldadas normalmente não é mais fraca do que a do metal base. Porém, quando submetidos a cargas dinâmicas alternadas, sua capacidade é significativamente menor e está intimamente relacionada ao tipo de junta soldada e estrutura. Isto é um dos principais contribuintes para a falha prematura de algumas estruturas devido à fadiga nas juntas soldadas.
② O projeto inicial da estrutura de soldagem concentrava-se principalmente na resistência à carga estática, ignorando o projeto de fadiga. Alguns projetos de juntas soldadas são agora considerados irracionais devido à falta de especificações perfeitas de projeto de fadiga.
③ Os projetistas e técnicos de engenharia carecem de conhecimento adequado das características de resistência à fadiga das estruturas soldadas, levando a projetos que muitas vezes copiam os critérios de projeto de fadiga e as formas estruturais de outras estruturas metálicas.
④ Estruturas soldadas estão se tornando cada vez mais comuns e, no processo de projeto e fabricação, há uma tendência para estruturas leves e de baixo custo, resultando em aumento das cargas de projeto para essas estruturas.
⑤ À medida que as estruturas soldadas avançam em direção a altas velocidades e cargas pesadas, a demanda por sua capacidade de suporte de carga dinâmica continua a aumentar. No entanto, o nível de investigação sobre a resistência à fadiga de estruturas soldadas permanece inadequado.
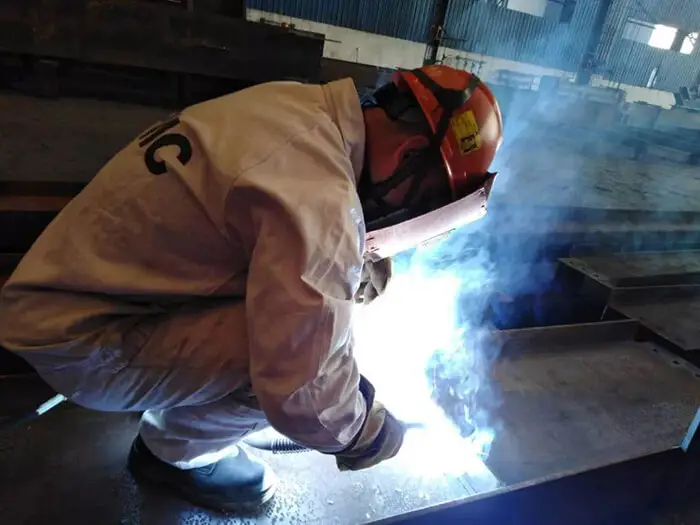
2. Causas de falha por fadiga da estrutura soldada
2.1 Efeito da resistência à carga estática na resistência à fadiga da estrutura soldada
No estudo de materiais de ferro e aço, os pesquisadores buscam alta resistência específica, ou seja, a capacidade de suportar cargas pesadas e ao mesmo tempo ser leve. Isto permite que as estruturas tenham maior capacidade de carga mantendo o mesmo peso, ou tenham a mesma capacidade sendo mais leves. Como resultado, o aço de alta resistência foi desenvolvido e apresenta alta resistência à fadiga.
A resistência à fadiga dos metais básicos aumenta com o aumento da resistência à carga estática. No entanto, isto não se aplica a estruturas soldadas. A resistência à fadiga das juntas soldadas tem correlação limitada com a resistência estática do metal base, do metal de solda, da microestrutura e das propriedades da zona afetada pelo calor e da resistência do metal de solda.
Em outras palavras, dados os mesmos detalhes da junta soldada, a resistência à fadiga do aço de alta resistência e do aço de baixo carbono é a mesma, e eles apresentam a mesma curva SN. Isto se aplica a vários tipos de juntas, como juntas de topo, juntas de canto e vigas soldadas.
Maddox conduziu um estudo sobre o crescimento de trincas por fadiga em aço carbono-manganês com limite de escoamento variando de 386 a 636 MPa, e metal de solda e zonas afetadas pelo calor soldados usando seis eletrodos diferentes.
Os resultados indicam que as propriedades mecânicas do material têm algum impacto na taxa de crescimento de fissuras, mas o efeito não é significativo.
No projeto de estruturas soldadas sujeitas a cargas alternadas, a seleção de aço de alta resistência não é significativa para atender aos requisitos de engenharia. O aço de alta resistência só é necessário para o metal base da junta soldada quando a taxa de tensão é superior a +0,5 e a condição de resistência estática desempenha um papel dominante.
A razão para estes resultados é a presença de defeitos de cunha de escória semelhantes a rebaixos ao longo da linha de fusão na ponta da solda da junta, com espessura de 0,075 mm a 0,5 mm e raio de ponta inferior a 0,015 mm. Os defeitos agudos são a origem das trincas de fadiga, equivalentes à etapa de formação de trincas de fadiga.
Portanto, a vida à fadiga da junta sob uma certa amplitude de tensão é determinada principalmente pelo estágio de propagação da trinca por fadiga. Esses defeitos resultam no mesmo tipo de juntas soldadas para todos os aços com a mesma resistência à fadiga, independentemente da resistência estática do metal base e dos materiais de soldagem.
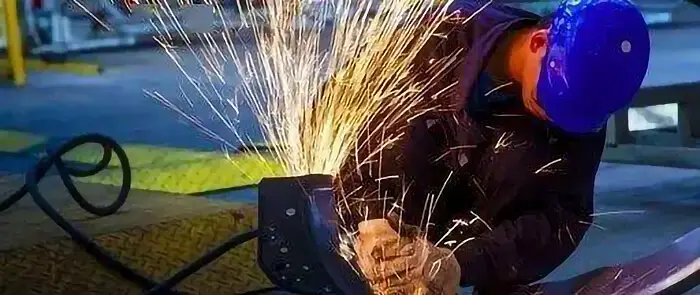
2.2 Efeito da concentração de tensões na resistência à fadiga
2.2.1 Influência do tipo de junta
As juntas soldadas incluem juntas de topo, juntas cruzadas, juntas em T e juntas sobrepostas. Estas juntas são suscetíveis à concentração de tensões devido à interferência da linha de transmissão de força.
A interferência da linha de tensão das juntas de topo é mínima, resultando em baixa concentração de tensão e maior resistência à fadiga em comparação com outras juntas. No entanto, experimentos mostraram que a resistência à fadiga das juntas de topo pode variar muito, devido a vários fatores, como tamanho da amostra, formato da ranhura, método de soldagem, tipo de eletrodo, posição de soldagem, formato da solda, processamento de solda pós-soldagem e pós-soldagem. tratamento térmico.
O uso de uma placa de apoio permanente em uma junta de topo pode causar concentração significativa de tensão na placa de apoio e reduzir a resistência à fadiga da junta. As fissuras por fadiga neste tipo de junta ocorrem na junta entre a solda e a placa de apoio, e não na ponta da solda, e sua resistência à fadiga é geralmente igual à de uma junta de topo com o pior formato sem placa de apoio.
Juntas transversais e juntas em T são amplamente utilizadas em estruturas soldadas.
Nessas juntas estruturais, a mudança óbvia na seção na transição da solda para o metal base resulta em um fator de concentração de tensão mais alto em comparação com a junta de topo, levando a uma menor resistência à fadiga para juntas transversais e em T em comparação com juntas de topo. articulações.
Para juntas não chanfradas conectadas por soldas de ângulo e juntas ranhuradas com soldas de penetração local, fraturas por fadiga podem ocorrer em dois elos fracos, ou seja, na junção entre o metal base e a ponta da solda ou solda, quando a solda transmite tensão de trabalho. Para juntas transversais com penetração em canal, as fraturas geralmente ocorrem apenas na ponta da solda, e não na solda.
A resistência à fadiga das juntas em forma de T e cruzadas, onde a solda não suporta tensões de trabalho, depende principalmente da concentração de tensões na junção da solda e da placa principal tensionada. As juntas em T têm maior resistência à fadiga, enquanto as juntas cruzadas têm menor resistência à fadiga.
Melhorar a resistência à fadiga de juntas em forma de T ou cruzadas pode ser alcançado usando soldagem de canal e usinagem da transição da solda para criar uma transição suave. Esta medida pode melhorar muito a resistência à fadiga.
A resistência à fadiga das juntas sobrepostas é muito baixa devido à grave distorção da linha de força. Usar uma junta de topo de placa de cobertura chamada “reforçada” é extremamente irracional.
O uso de uma placa de cobertura em uma junta de topo enfraquece significativamente sua alta resistência à fadiga devido ao aumento da concentração de tensões.
Em juntas de placas de cobertura resistentes, podem ocorrer fissuras por fadiga no metal base ou na solda. Além disso, alterar a largura da placa de cobertura ou o comprimento da solda alterará a distribuição de tensões no metal base, afetando a resistência à fadiga da junta. A resistência à fadiga da junta aumenta à medida que aumenta a relação entre o comprimento da solda e a largura da placa de cobertura, pois isso tende a resultar em uma distribuição de tensões mais uniforme no metal base.
2.2.2 EUinfluência do formato da solda
Independentemente da forma da junta, elas são conectadas por dois tipos de solda: solda de topo e solda de ângulo.
A forma das soldas afeta o fator de concentração de tensões, levando a variações significativas na resistência à fadiga.
A forma da solda de topo tem o maior impacto na resistência à fadiga da junta.
(1) Influência do ângulo de transição
Yamaguchi et al. estabeleceram a relação entre a resistência à fadiga e o ângulo de transição (ângulo obtuso externo) entre o metal base e o metal de solda.
Nos testes, a largura (W) e a altura (H) da solda mudaram, mas a relação H/W permaneceu constante, ou seja, o ângulo incluído permaneceu inalterado. Os resultados mostraram que a resistência à fadiga também permaneceu inalterada.
Porém, quando a largura da solda permaneceu constante e a altura mudou, verificou-se que um aumento na altura resultou em uma diminuição na resistência à fadiga da junta. Isto é claramente devido a uma diminuição no ângulo externo incluído.
(2) Influência do raio de transição da solda
Os resultados da pesquisa de Sander et al. indicam que o raio de transição da solda também impacta significativamente a resistência à fadiga da junta. À medida que o raio de transição aumenta (enquanto o ângulo de transição permanece inalterado), a resistência à fadiga aumenta.
A forma da solda de ângulo também tem um impacto significativo na resistência à fadiga da junta. Quando a relação entre a espessura calculada (a) de uma única solda e a espessura da placa (b) é inferior a 0,6 a 0,7, geralmente ela quebra na solda. Quando a/b > 0,7, geralmente rompe o metal base.
Aumentar o tamanho da solda não pode alterar a resistência de outra seção fraca, ou seja, o metal base na extremidade da ponta da solda e, portanto, a resistência à fadiga não pode ser excedida, na melhor das hipóteses.
Soete e Van Crombrugge conduziram testes em placas de 15 mm de espessura soldadas com diferentes soldas de ângulo sob carga de fadiga axial.
Os resultados mostraram que quando a perna da solda era de 13mm, ocorriam fraturas no metal base ou na ponta da solda. Se a perna da solda fosse menor que esse valor, ocorreriam fraturas por fadiga na solda. Quando o tamanho da perna era de 18 mm, ocorreram fraturas no metal base.
Com base nessas descobertas, eles propuseram um limite para o tamanho da perna de solda: S = 0,85B, onde S é o tamanho da perna de solda e B é a espessura da placa.
Mesmo que o tamanho da perna da solda tenha atingido a espessura da placa (15mm), ainda ocorreram fraturas na solda, o que confirma os resultados teóricos.
2.2.3 influência dos defeitos de soldagem
Existem numerosos tipos diferentes de defeitos na ponta da solda que levam à trinca precoce de trincas por fadiga e a uma diminuição significativa na resistência à fadiga do metal base (até 80%).
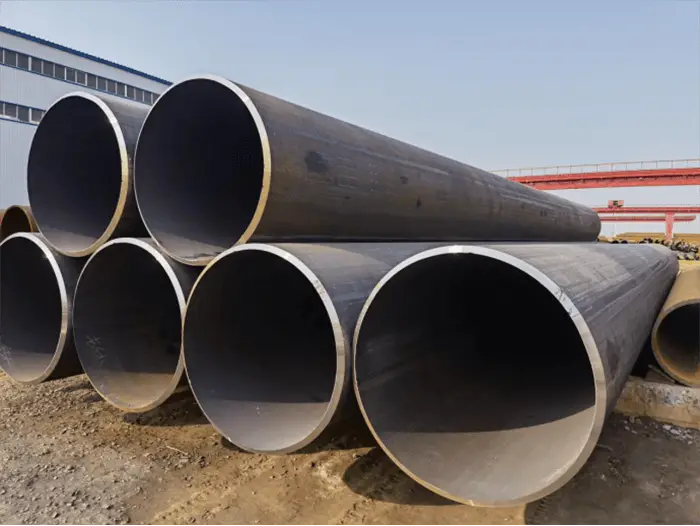
Os defeitos de soldagem podem ser geralmente divididos em duas categorias:
Defeitos planares (como trincas e falta de fusão) e defeitos volumétricos (como poros e inclusão de escória) têm vários graus de influência.
Além disso, o impacto dos defeitos de soldagem na resistência à fadiga das juntas depende do tipo, direção e localização dos defeitos.
1) Rachadura
Trincas na soldagem, como trincas a frio e a quente, são fontes significativas de concentração de tensão, além de uma microestrutura frágil e podem reduzir significativamente a resistência à fadiga de estruturas ou juntas.
Estudos anteriores mostraram que em uma amostra de junta de topo de aço de baixo carbono com largura de 60mm e espessura de 12,7mm, quando há trincas com comprimento de 25mm e profundidade de 5,2mm na solda (que ocupam cerca de 10% da área da seção transversal da amostra), sua resistência à fadiga sob carga alternada é reduzida em 55% a 65% após 2 milhões de ciclos.
2) Penetração incompleta
É importante ressaltar que a penetração incompleta nem sempre é considerada um defeito, pois pode ser projetada intencionalmente para determinadas juntas, como bicos de vasos de pressão.
Defeitos de penetração incompleta podem ser defeitos superficiais (solda unilateral) ou defeitos internos (solda dupla face) e podem ser locais ou globais. Eles enfraquecem principalmente a área da seção transversal e causam concentração de tensões.
Os testes mostraram que, em comparação com resultados sem tais defeitos, a resistência à fadiga é reduzida em 25%, o que significa que o impacto não é tão severo quanto o das fissuras.
3) Fusão incompleta
Apesar de ser um problema significativo, há pesquisas limitadas sobre esse tema devido às dificuldades no preparo da amostra.
Contudo, está claro que a falta de fusão é um tipo de defeito planar e não pode ser ignorada. Muitas vezes é tratado como uma forma de penetração incompleta.
4) Corte inferior
Os principais parâmetros que descrevem o corte inferior são o comprimento do corte inferior (L), a profundidade do corte inferior (h) e a largura do corte inferior (W).
Atualmente, o principal parâmetro que afeta a resistência à fadiga é a profundidade do rebaixo (h), e pode ser avaliado tanto pela profundidade (h) quanto pela razão entre a profundidade e a espessura da placa (h/B).
5) Estômatos
Harrison analisou e resumiu os resultados de testes anteriores relacionados a defeitos volumétricos.
A diminuição da resistência à fadiga deve-se principalmente à redução da área da seção transversal causada pelos poros. Existe uma relação linear entre eles.
No entanto, alguns estudos mostram que quando a superfície da amostra é usinada, resultando na localização dos poros na superfície ou logo abaixo dela, o impacto negativo dos poros aumentará. Eles atuarão como uma fonte de concentração de tensões e se tornarão o ponto de partida para trincas por fadiga.
Isto sugere que a localização dos poros tem um impacto maior na resistência à fadiga da junta do que o seu tamanho, e os poros localizados na superfície ou abaixo dela têm o efeito negativo mais significativo.
6) Inclusão de escória
A pesquisa realizada pelo IIW mostrou que dentre os defeitos volumétricos, a inclusão de escória tem maior impacto na resistência à fadiga das juntas em comparação à porosidade.
O impacto dos defeitos de soldagem na resistência à fadiga das juntas não depende apenas do tamanho do defeito, mas também é influenciado por vários outros fatores, como os defeitos superficiais que têm um impacto maior que os defeitos internos e os defeitos planares perpendiculares à direção da força. tendo um impacto maior do que em outras direções.
A influência de defeitos localizados em áreas de tensão residual de tração é maior do que aqueles em áreas de tensão residual de compressão, e defeitos localizados em áreas de concentração de tensão, como trincas de solda, têm um impacto maior do que os mesmos defeitos em campos de tensão uniformes.
2.3 Efeito da tensão residual de soldagem na resistência à fadiga
A tensão residual de soldagem é uma característica de estruturas soldadas que é amplamente estudada por seu impacto na resistência à fadiga dessas estruturas. Numerosos estudos experimentais foram conduzidos para examinar esta questão.
Os testes de fadiga são frequentemente realizados comparando amostras com tensão residual de soldagem com aquelas que foram submetidas a tratamento térmico para remoção da tensão residual. Isto ocorre porque a geração de tensão residual de soldagem é frequentemente acompanhada por alterações nas propriedades do material resultantes do ciclo térmico de soldagem, e o tratamento térmico não apenas elimina a tensão residual, mas também restaura parcial ou totalmente as propriedades do material.
No entanto, devido à variabilidade dos resultados dos testes, existem diferentes interpretações dos resultados e avaliações do impacto da tensão residual da soldagem. Isso pode ser visto observando as pesquisas iniciais e recentes conduzidas por vários indivíduos.
Por exemplo, diferentes pesquisadores chegaram a conclusões diferentes a partir de testes de ciclo 2×106 em juntas de topo com reforço.
Verificou-se que a resistência à fadiga de uma amostra após tratamento térmico para alívio de tensões foi 12,5% maior do que a mesma amostra em seu estado soldado. No entanto, alguns estudos descobriram que a resistência à fadiga das amostras soldadas e tratadas termicamente era a mesma, com pouca diferença. Em outras descobertas, a resistência à fadiga aumentou após o tratamento térmico para remover a tensão residual, mas o aumento foi muito inferior a 12,5%.
Resultados semelhantes foram encontrados nos testes de amostras de juntas de topo com retificação superficial. Alguns testes mostraram que a resistência à fadiga poderia ser aumentada em 17% após o tratamento térmico, enquanto outros não mostraram melhora.
Esta questão tem sido fonte de confusão há algum tempo. Contudo, uma série de testes sob carga alternada conduzidos por estudiosos da antiga União Soviética ajudaram a esclarecer o problema. A pesquisa de Trufyakov sobre o efeito da tensão residual da soldagem na resistência à fadiga da junta sob diferentes características do ciclo de tensão é especialmente digna de nota.
Os testes foram realizados utilizando aço estrutural comum de baixa liga 14Mn2 e envolveram uma solda de topo transversal na amostra, com um cordão de solda longitudinal sobreposto em ambos os lados.
Um grupo de amostras foi submetido a tratamento térmico para eliminar tensões residuais após a soldagem, enquanto o outro grupo não foi tratado. O teste de comparação da resistência à fadiga foi realizado utilizando três coeficientes característicos do ciclo de tensão, r = -1, 0 e +0,3.
Sob carga alternada (r = -1), a resistência à fadiga da amostra com tensão residual aliviada foi próxima de 130 MPa, enquanto a amostra sem eliminação apresentou resistência à fadiga de apenas 75 MPa.
Sob carga pulsante (r = 0), a resistência à fadiga de ambos os grupos de amostras foi a mesma, a 185 MPa.
Quando r = 0,3, a resistência à fadiga da amostra com tensão residual eliminada por tratamento térmico foi de 260 MPa, ligeiramente inferior à da amostra sem tratamento térmico, que apresentou resistência à fadiga de 270 MPa.
As principais razões para este fenômeno são:
Quando o valor de r é alto, como sob carga pulsante (r = 0), a resistência à fadiga é alta e a tensão residual é rapidamente liberada sob a influência da alta tensão de tração, reduzindo o impacto da tensão residual na resistência à fadiga. Quando r aumenta para 0,3, a tensão residual diminui ainda mais sob carga, não tendo efeito na resistência à fadiga.
O tratamento térmico não só elimina a tensão residual, mas também amolece o material, levando a uma diminuição da resistência à fadiga após o tratamento.
Este teste demonstra a influência da tensão residual e das alterações de material causadas pelo ciclo térmico da soldagem na resistência à fadiga. Também indica que o impacto da tensão residual de soldagem na resistência à fadiga de uma junta está relacionado com as características do ciclo de tensão da carga de fadiga. Quando o valor característico do ciclo é baixo, o impacto é relativamente alto.
Foi observado anteriormente que, devido à tensão residual atingir o ponto de escoamento do material em uma solda estrutural, em uma junta com um ciclo de tensão de amplitude constante, o ciclo de tensão real próximo à solda cairá abaixo do ponto de escoamento do material, independentemente do ciclo original. características.
Por exemplo, o ciclo de tensão nominal deve ser de +S1 a -S2, com uma faixa de tensão de S1 + S2. No entanto, a faixa real do ciclo de tensão na junta será de sy (amplitude de tensão no ponto de escoamento) a SY-(S1 + S2).
Este é um fator crucial a considerar quando se estuda a resistência à fadiga de juntas soldadas, levando alguns códigos de projeto a substituir a característica cíclica r pela faixa de tensões.
Além disso, o tamanho da amostra, o modo de carregamento, a relação do ciclo de tensão e o espectro de carga também têm um impacto significativo na resistência à fadiga.
3. Método de processo para melhorar a resistência à fadiga da estrutura soldada
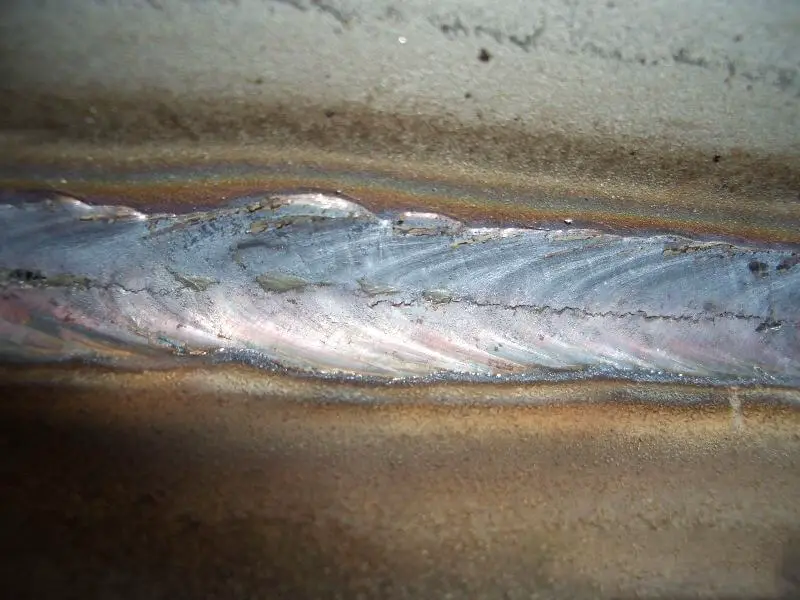
O início da trinca por fadiga em juntas soldadas normalmente ocorre na raiz e na ponta da solda. Se o risco de início de trincas por fadiga na raiz da solda for controlado, os pontos mais vulneráveis nas juntas soldadas ficam concentrados na ponta da solda.
Existem várias maneiras de melhorar a resistência à fadiga das juntas soldadas:
① Reduzir ou eliminar defeitos de soldagem, principalmente aberturas;
② Melhorar a geometria da ponta da solda e diminuir o fator de concentração de tensão;
③ Ajuste o campo de tensão residual de soldagem para produzir um campo de tensão residual de compressão. Esses métodos de melhoria podem ser divididos em duas categorias, conforme mostrado na Tabela 1.
A otimização do processo de soldagem não só melhora a resistência à fadiga da estrutura soldada, mas também aumenta a resistência à carga estática e as propriedades metalúrgicas das juntas soldadas. Existe uma vasta quantidade de dados sobre este tema, que não serão repetidos aqui.
Tabela 1 métodos de melhoria da resistência à fadiga da estrutura soldada
Método de melhoria da resistência à fadiga de estrutura soldada | Otimização do processo de soldagem | Geometria local | Controle de qualidade | Controle de defeitos de soldagem | 1 | |
Melhoria da geometria | 2 | |||||
Processo tecnológico | Sequência de soldagem | 3 | ||||
Tensão residual(<0) | Tratamento metalúrgico do dedo do pé da solda | 4 | ||||
Modelagem de cordão de solda | Geometria do dedo do pé da solda | 5 | ||||
Estado de ouro e metal | 6 | |||||
Melhoria de soldagem | Geometria local | Usinagem | Retificação de ponta de solda | 7 | ||
Impacto da água | 8 | |||||
Refusão local | Reparação de TG | 9 | ||||
Reparo de plasma | 10 | |||||
Estresse residual | Método de liberação de estresse | Tratamento térmico | 11 | |||
Tratamento mecânico | 12 | |||||
Aquecimento local | 13 | |||||
Método mecânico | Contato mecânico | Tiro peening | 14 | |||
Martelar | 15 | |||||
Impacto ultrassônico | 16 | |||||
Soldagem | Estampagem | 17 | ||||
Compressão local | 18 |
Os principais métodos para aumentar a resistência à fadiga de juntas soldadas são discutidos detalhadamente em três partes, com foco nos métodos de processo.
3.1 Mmétodos para melhorar a geometria da ponta da solda e reduzir a concentração de tensão
1) Curativo TIG
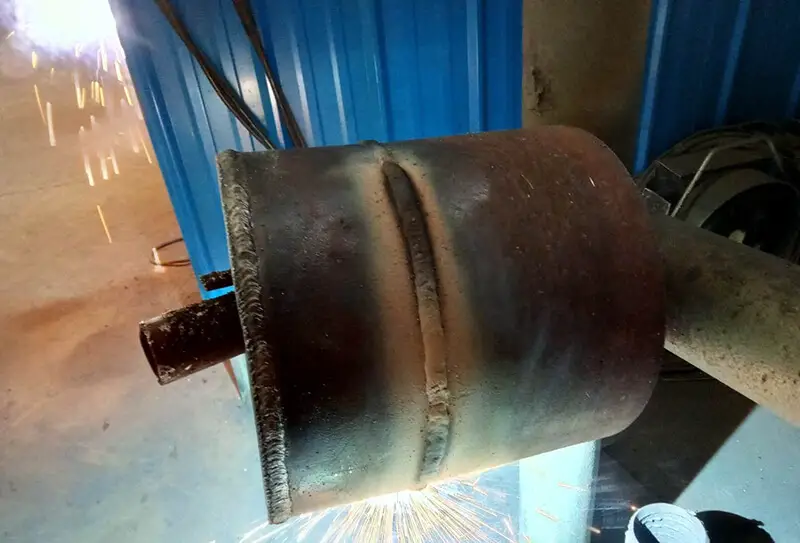
Estudos demonstraram que o reparo TIG pode aumentar significativamente a resistência à fadiga de juntas soldadas, tanto nacional quanto internacionalmente. O processo envolve o uso de soldagem TIG para fundir novamente a seção de transição da junta soldada, criando uma transição suave entre a solda e o metal base. Isto reduz a concentração de tensões e elimina pequenas inclusões de escória não metálica, resultando numa melhoria da resistência à fadiga da junta.
A pistola de soldagem é normalmente posicionada de 0,5 a 1,5 mm de distância da ponta da soldagem durante o processo de reparo, e a área fundida novamente deve ser mantida limpa. A adição de uma leve moagem prévia melhorará os resultados.
É crucial lidar adequadamente com o processo de retroarco se a extinção do arco ocorrer durante a refusão, pois isso afetará a qualidade do cordão de solda refundido. A melhor posição para o retroarco é geralmente 6 mm à frente da cratera do cordão de solda.
Recentemente, a Sociedade Internacional de Soldagem colaborou com institutos de pesquisa em soldagem em vários países europeus e no Japão para conduzir um estudo unificado sobre a eficácia de métodos para aumentar a resistência à fadiga das juntas. As amostras foram preparadas pelo British Welding Research Institute.
O estudo confirmou que a resistência nominal à fadiga da junta após 2×106 ciclos aumentou 58% após o tratamento com este método. Este valor nominal de resistência à fadiga de 211MPa corresponde a um valor característico (índice K) de 144MPa. Supera o maior valor de FAT na resistência à fadiga de detalhes de juntas estabelecido pela International Welding Society.
2) Usinagem
Usinar a superfície da solda pode reduzir bastante a concentração de tensão e melhorar a resistência à fadiga da junta de topo. Se a solda estiver livre de defeitos, sua resistência à fadiga pode até ultrapassar a do metal base. Porém, a usinagem é um processo caro e só deve ser realizado quando os benefícios justificarem o custo.
No caso de soldas com defeitos significativos e sem soldagem de fundo, a concentração de tensões no defeito ou na raiz da solda é muito mais severa do que na superfície, tornando a usinagem sem sentido. Se houver falta de defeito de penetração, as trincas por fadiga não iniciarão no reforço e na ponta da solda, mas serão transferidas para a raiz da solda. Nesses casos, a usinagem pode realmente reduzir a resistência à fadiga da junta.
A retificação apenas da ponta da solda, em vez de todo o metal de solda, também pode melhorar a resistência à fadiga da junta. A pesquisa mostrou que o ponto de início da trinca neste cenário é transferido da ponta da solda para o defeito da solda.
Testes de resistência à fadiga conduzidos por Makorov da antiga União Soviética em aço de alta resistência (resistência à tração σb = 1080MPa) mostraram que a resistência à fadiga de soldas transversais de topo sob carga alternada foi de ± 150MPa após 2×106 ciclos como soldados. A usinagem da solda e a remoção do reforço aumentaram a resistência à fadiga para ± 275MPa, equivalente à resistência à fadiga do metal base. A retificação local na ponta da solda de topo resultou em uma resistência à fadiga de ± 245MPa, equivalente a 83% do efeito de usinagem e uma melhoria de 65% em relação ao estado soldado.
É importante notar que uma técnica adequada deve ser utilizada tanto na usinagem quanto na retificação para garantir a melhoria desejada na resistência à fadiga.
3) Retificação de rebolo

A retificação com um rebolo pode não ser tão eficaz quanto a usinagem, mas ainda é um método útil para aumentar a resistência à fadiga de juntas soldadas. A International Welding Society recomenda o uso de um rebolo elétrico ou hidráulico de alta velocidade com velocidade de 15.000 a 40.000 RPM, feito de material de carbono e tungstênio. O diâmetro do rebolo deve garantir que a profundidade e o raio de retificação sejam iguais ou superiores a 1/4 da espessura da placa.
Uma pesquisa recente da International Welding Society descobriu que a resistência nominal à fadiga da amostra após 2 ciclos aumentou 45% após a retificação. O valor nominal de resistência à fadiga de 199 MPa corresponde a um valor característico (135 MPa), que é superior ao maior valor de FAT na resistência à fadiga do detalhe da junta estabelecido pela International Welding Society.
É importante observar que a direção de retificação deve estar alinhada com a direção da linha de tensão. A retificação em uma direção diferente pode deixar um entalhe perpendicular à linha de tensão, atuando efetivamente como uma fonte de concentração de tensão e reduzindo a resistência à fadiga da junta.
4) Método de eletrodo especial
Este método envolve o desenvolvimento de um novo tipo de eletrodo. Seu metal líquido e escória líquida possuem alta molhabilidade, o que aumenta o raio de transição da solda, reduz o ângulo na ponta da solda, reduz a concentração de tensão na ponta da solda e melhora a resistência à fadiga da junta soldada.
Tal como a reparação por soldadura TIG, tem uma forte preferência por determinadas posições de soldadura, particularmente soldadura plana e de filete, enquanto os seus benefícios são significativamente reduzidos para soldadura vertical, horizontal e suspensa.
3.2 Mmétodo de ajustar o campo de tensão residual para produzir tensão de compressão
1) Método de pré-sobrecarga
Quando uma carga de tração é aplicada a uma amostra contendo concentração de tensão até que o escoamento ocorra no entalhe, resultando em alguma deformação plástica de tração, a tensão de compressão será gerada no local da deformação plástica de tração próximo ao entalhe carregado após o descarregamento. A tensão de tração abaixo do limite de escoamento será equilibrada em outras seções da amostra.
Nos testes de fadiga subsequentes, a faixa de tensão da amostra submetida a este tratamento será diferente daquela da amostra original sem pré-carga e será significativamente reduzida. Isto pode melhorar a resistência à fadiga das juntas soldadas.
Pesquisas mostram que é necessário um teste de pré-carga antes de grandes estruturas soldadas, como pontes e vasos de pressão, serem colocadas em operação. Isso melhorará seu desempenho em fadiga.
2) Aquecimento local
O aquecimento local pode ajustar o campo de tensões residuais na soldagem, gerando tensões residuais compressivas em pontos de concentração de tensões, o que pode melhorar a resistência à fadiga da junta. Atualmente, este método só é aplicável a soldas longitudinais descontínuas ou juntas com placas longitudinais reforçadas.
Para placas de filete de face única, a posição de aquecimento é normalmente cerca de 1/3 da largura da placa a partir da solda. Para placas de filé de dupla face, a posição de aquecimento é o centro da placa. Isto gera tensões de compressão na solda, aumentando a resistência à fadiga da junta.
Diferentes pesquisadores obtiveram resultados variados usando este método. Para placas de reforço unilaterais, a resistência à fadiga aumentou em 145-150%, enquanto para placas de reforço de dupla face, a resistência à fadiga aumentou em 70-187%.
A posição do aquecimento local tem um impacto significativo na resistência à fadiga da junta. O aquecimento pontual no final da solda causa tensão residual compressiva no entalhe e aumenta a resistência à fadiga em 53%. No entanto, o aquecimento pontual no centro da amostra na extremidade da solda, com a mesma distância da extremidade da solda, tem o mesmo efeito metalográfico, mas produz tensão residual de tração, resultando na mesma resistência à fadiga que a amostra não tratada.
3) Método de extrusão
O mecanismo de extrusão local é semelhante ao método de aquecimento pontual, na medida em que melhora a resistência à fadiga da junta, gerando tensão residual de compressão. Porém, seu ponto de ação difere e a posição de extrusão deve ser onde a tensão residual compressiva é desejada.
O método de extrusão tem um efeito mais significativo em amostras de aço de alta resistência do que em aço de baixo carbono.
4) Método de Gurnnert
Gunnert propôs um método para obtenção de resultados satisfatórios devido à dificuldade em determinar com precisão a posição e a temperatura do aquecimento no método de aquecimento local. A chave para este método é aquecer o entalhe diretamente, e não a área circundante, a uma temperatura que pode causar deformação plástica, mas é inferior à temperatura de transformação de fase de 55°C ou 550°C, e então resfriá-lo rapidamente.
O resfriamento tardio do metal sob a superfície e do metal circundante que não é resfriado causará encolhimento e gerará tensão de compressão na superfície resfriada. Esta tensão compressiva pode aumentar a resistência à fadiga do membro.
É importante observar que o processo de aquecimento deve ser lento para aquecer a camada inferior. Gunnert recomenda um tempo de aquecimento de 3 minutos, enquanto Harrison recomenda 5 minutos.
Ohta evitou com sucesso rachaduras por fadiga em tubos de topo usando este método. A parte externa da tubulação foi aquecida por indução e a parte interna foi resfriada pela circulação de água, gerando tensão de compressão na tubulação e evitando efetivamente a formação de trincas por fadiga. Após o tratamento, a taxa de crescimento de trincas por fadiga do tubo de solda de topo foi bastante reduzida e atingiu a mesma taxa de crescimento de trincas que o metal base.
3.3 Mmétodos de redução da concentração de tensão e geração de tensão compressiva
1) Método de martelar
O martelamento é um método de trabalho a frio que cria tensão de compressão na superfície da ponta da solda em uma junta. A eficácia deste método depende da deformação plástica na superfície da ponta da solda.
Além disso, o martelamento pode reduzir a nitidez do entalhe e, portanto, a concentração de tensão, levando a uma melhoria significativa na resistência à fadiga da junta. A Sociedade Internacional de Soldagem recomenda uma pressão de martelo pneumático de 5-6 Pa.
O topo da cabeça do martelo deve ser sólido com um diâmetro de 8-12mm, e é recomendado o uso de quatro impactos para garantir uma profundidade de martelamento de 0,6mm.
Uma pesquisa da Sociedade Internacional de Soldagem mostra que para juntas em T não estruturais, o martelamento aumenta a resistência à fadiga em 54% sob 2×106 ciclos.
2) Shot peening
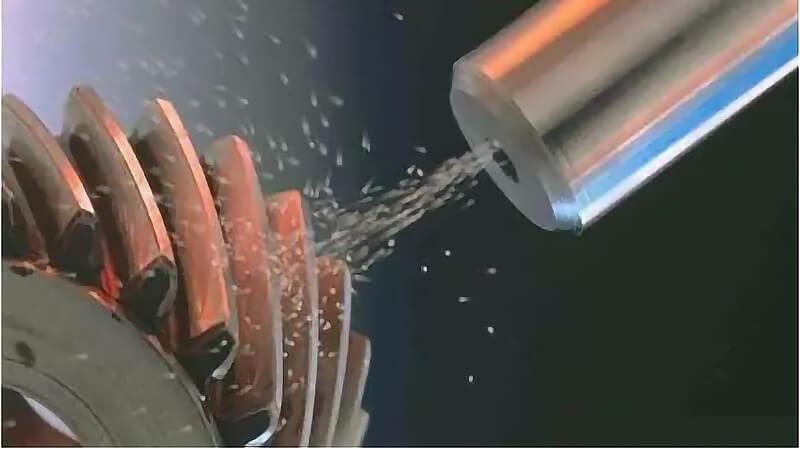
Shot peening é outra forma de martelamento e é um tipo de usinagem de impacto. A eficácia do shot peening depende do diâmetro do shot peening. O diâmetro não deve ser muito grande para resolver pequenos defeitos, mas não muito pequeno para atingir um certo nível de endurecimento por trabalho a frio. O shot peening normalmente pode impactar a superfície a uma profundidade de alguns milésimos de milímetro.
A pesquisa mostra que o shot peening pode melhorar muito a resistência à fadiga de juntas de aço de alta resistência e tem um efeito particularmente forte na soldagem a arco de argônio de materiais de aço de alta resistência, superando até mesmo o reparo TIG. O uso de shot peening também pode aumentar o impacto do reparo por fusão TIG.
4. A mais recente tecnologia para melhorar a resistência à fadiga de juntas soldadas
4.1 vocêMétodo de tratamento de impacto ultrassônico
Nos últimos anos, o impacto ultrassônico foi desenvolvido como um meio de melhorar a resistência à fadiga de juntas e estruturas soldadas. Seu mecanismo é semelhante ao do martelamento e do shot peening.
No entanto, o impacto ultrassônico tem vantagens como peso leve, bom controle, uso flexível e conveniente, ruído mínimo, alta eficiência, menos restrições de aplicação, baixo custo e eficiência energética. É adequado para todos os tipos de juntas e é um método eficaz para melhorar o desempenho à fadiga de juntas soldadas após a soldagem.
Foram realizados estudos utilizando tratamento de impacto ultrassônico em juntas de topo e juntas de canto longitudinais sem suporte de vários aços estruturais soldados típicos. Testes comparativos de fadiga foram então conduzidos em juntas soldadas e tratadas por impacto. Os resultados, apresentados na Tabela 2, indicam que a resistência à fadiga das juntas soldadas aumentou de 50 a 170% após o tratamento por impacto ultrassônico.
Tabela 2 Comparação da resistência à fadiga antes e após tratamento com impacto ultrassônico
Material e forma conjunta | Resistência à fadiga Ds/MPa | Grau de aumento (%) | |
---|---|---|---|
Como soldado | Estado tratado por choque | ||
Q235B (R= 0,1) – junta de topo | 152 | 230 | 51 |
SS800 (R= 0,05) – junta de topo | 306 | 101 | |
16Mn (R= 0,1) – junta de topo | 285 | 88 | |
Q235B (R=0,1) – junta de canto longitudinal | 104 | 200 | 92 |
SS800 (R=0,05) – junta de canto longitudinal | 279 | 168 | |
16Mn (R=0,1) – junta de canto longitudinal | 212 | 104 |
4.2 eumétodo de tira de soldagem a ponto com mudança de fase
4.2.1 PPrincípio e desenvolvimento de melhoria da resistência à fadiga de juntas soldadas
A tensão compressiva pode aumentar a resistência à fadiga das juntas soldadas, o que tem sido amplamente discutido na literatura. No entanto, o desafio reside em como introduzir facilmente tensões de compressão nas juntas soldadas.
É bem conhecido que a composição química, o teor de liga e a taxa de resfriamento podem resultar em diferentes alterações microestruturais durante o processo de resfriamento de materiais de ferro e aço. Estas transformações estruturais são acompanhadas por expansão de volume, que pode criar tensões de transformação de fase quando restringidas, levando a tensões de compressão.
Para o metal de solda, isso reduz a tensão residual de tração e até resulta em tensão residual de compressão, melhorando assim as propriedades mecânicas das juntas soldadas.
O eletrodo de soldagem de baixa temperatura de transformação (LTTE) é um novo material de soldagem que utiliza tensão de transformação de fase para produzir tensão de compressão em juntas soldadas e aumentar sua resistência à fadiga.
Já na década de 1960, especialistas em soldagem na antiga União Soviética propuseram o método de tira de soldagem a ponto com transformação de baixa fase para melhorar a resistência à fadiga de estruturas soldadas, embora o termo “tira de soldagem a ponto com transformação de baixa fase” não fosse usado na época e foi simplesmente referido como um eletrodo especial.
A composição metálica de superfície consiste principalmente em 3-4% Mn para reduzir a temperatura de transformação de fase e alcançar a transformação de fase metalúrgica. A literatura sugere que a resistência à fadiga de pequenas amostras após o revestimento com esses eletrodos especiais é 75% maior do que sem revestimento.
Recentemente, o desenvolvimento de aço de carbono ultrabaixo e o uso de Cr e Ni para reduzir a temperatura de transformação martensítica do metal depositado em materiais de soldagem levou a um rápido progresso na tira de soldagem por pontos de baixa transformação.
Tanto o Japão como a China conduziram extensas pesquisas nesta área, embora ainda estejam em fase de laboratório.
4.2.2 Eefeito do eletrodo LTTE na melhoria da resistência à fadiga
A Escola de Materiais da Universidade de Tianjin projetou e otimizou o eletrodo de soldagem de baixa temperatura de transformação (LTTE) e conduziu extensos testes de fadiga e testes de desempenho de processo em várias juntas soldadas.
(1) Método LTTE
O eletrodo de soldagem de baixa temperatura de transformação (LTTE) e o eletrodo comum E5015 foram usados para soldar a junta de topo transversal, junta cruzada sem carga, junta de filete circunferencial longitudinal, junta de solda de filete paralela longitudinal e junta de topo longitudinal, respectivamente. Um teste comparativo de fadiga foi realizado.
Os resultados indicam que a resistência à fadiga da junta LTTE da haste de soldagem a ponto de mudança de fase foi 11%, 23%, 42%, 46% e 59% maior do que a do eletrodo comum E5015. A vida à fadiga aumentou de várias vezes para centenas de vezes.
Tabela 3 Efeito de melhoria da resistência à fadiga de diferentes tipos de juntas soldadas
Tipo de eletrodo | Junta de topo transversal | Junta cruzada sem carga | Junta de solda de filete circunferencial longitudinal | Junta de solda de filete paralela longitudinal | Junta de topo longitudinal |
---|---|---|---|---|---|
Haste de solda E5015 | 176,9 | 202.1 | 167,0 | 182,7 | 179,4 |
Eletrodo LTTE | 157,8 | 164,8 | 118,3 | 124,9 | 113,0 |
Grau de melhoria | 11% | 23% | 41% | 47% | 58% |
Concentração de estresse | Leve K1 | Médio K2 | Forte K3 | N4 particularmente forte | K4 particularmente forte |
Grau de restrição | Pequeno grande |
Como o eletrodo de soldagem com baixa temperatura de transformação (LTTE) cria tensão de compressão residual a partir da expansão volumétrica da transformação martensítica a uma temperatura mais baixa, a magnitude da tensão de compressão residual está intimamente ligada à restrição da junta soldada.
Quanto mais restrita for a junta soldada, maior será a tensão de compressão residual e mais significativa será a melhoria na resistência à fadiga.
(2) Método de curativo LTTE para soldagem a ponto com transformação de baixa fase
No entanto, adicionar mais elementos de liga aos materiais de soldagem para obter a transformação martensítica a uma taxa de resfriamento normal e baixa temperatura aumenta significativamente o custo do eletrodo de soldagem com baixa temperatura de transformação (LTTE). Se todas as soldas em uma estrutura soldada forem feitas com materiais de soldagem de baixa mudança de fase, o custo global da estrutura também será significativamente maior, tornando-a economicamente inviável.
É bem conhecido que a fratura por fadiga em juntas soldadas geralmente ocorre na ponta da solda. Se a tensão de compressão residual for gerada na ponta da solda, a resistência à fadiga da junta soldada pode ser melhorada sem o uso de todas as tiras de soldagem a ponto de baixa mudança de fase, reduzindo o custo dos materiais.
Com essa ideia em mente, a Universidade de Tianjin propôs o método de curativo com eletrodo de soldagem de baixa temperatura de transformação (LTTE) para melhorar a resistência à fadiga de juntas soldadas, com base em resultados experimentais. A resistência à fadiga do curativo LTTE e das juntas soldadas com eletrodo comum foi comparada usando dois tipos de junta cruzada sem carga e junta de solda de filete circunferencial longitudinal. A resistência à fadiga do primeiro foi 19,9% e 41,7% superior à do segundo, respectivamente, comprovando a viabilidade e praticidade da ideia.
Esta pesquisa preliminar fornece uma aplicação mais razoável do eletrodo de soldagem de baixa temperatura de transformação (LTTE) na prática de engenharia.
Ao mesmo tempo, a junta de revestimento da ponta do eletrodo de soldagem de baixa temperatura de transformação (LTTE) também pode refletir sua aplicação em soldas de cobertura e cordões de solda próximos à ponta da ponta.
4.2.3 AVantagens e desvantagens da tira de soldagem a ponto com baixa mudança de fase
Vantagem:
(1) O método do eletrodo de soldagem de baixa temperatura de transformação (LTTE) é realizado durante o processo de soldagem, eliminando a necessidade de processamento pós-soldagem.
(2) O método LTTE não requer habilidades operacionais especiais, tornando-o simples e conveniente de usar.
(3) Ao usar eletrodo de soldagem de baixa temperatura de transformação (LTTE), a resistência à fadiga das juntas soldadas pode ser melhorada. Como não é afetado pelos efeitos térmicos dos cordões de solda subsequentes, é adequado para melhorar a resistência à fadiga de soldas ocultas, soldas cobertas, soldas traseiras de soldagem unilateral e outras soldas que não podem ser processadas após a soldagem.
(4) O eletrodo LTTE também pode ser usado para reparar trincas por fadiga em estruturas soldadas.
Desvantagens:
A adição de mais elementos de liga aos materiais de soldagem aumenta o custo dos materiais de eletrodo de soldagem de baixa temperatura de transformação (LTTE), mas isso pode ser compensado pelo uso de curativo LTTE e outros métodos.
5. Conclusão
Concluindo, os requisitos de capacidade de suporte dinâmico para estruturas soldadas têm aumentado à medida que são utilizadas para cargas pesadas e de alta velocidade. Como resultado, o desenvolvimento e a utilização de novas tecnologias para melhorar o desempenho à fadiga das juntas soldadas é crucial para uma aplicação mais ampla de estruturas soldadas.
Tanto a tecnologia de impacto ultrassônico quanto o uso de eletrodo de soldagem de baixa temperatura de transformação (LTTE) para melhorar a resistência à fadiga de juntas soldadas são importantes direções de pesquisa no campo da melhoria do desempenho à fadiga e do processo de estruturas soldadas.