Com o advento de equipamentos de grande escala e a utilização crescente de aço em vez de materiais fundidos, as chapas ultraespessas tornaram-se cada vez mais predominantes na fabricação de equipamentos.
O corte por chama é a etapa inicial na fabricação e processamento de componentes estruturais.
Dada a natureza irreversível do corte por chama, o processo de corte por chama CNC para chapas ultragrossas tornou-se uma tecnologia crucial para grandes fabricantes de equipamentos.
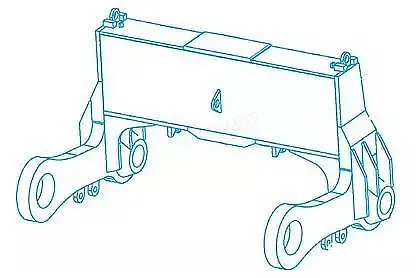
figura 1
1. Características do corte por chama de chapa ultragrossa
Oxigênio e acetileno para corte de chapas ultraespessas
O corte de peças de chapas ultra grossas requer uma grande quantidade de oxigênio e acetileno, pois essas peças geralmente são maiores. Para garantir um processo de corte suave e eficiente, é crucial ter um fornecimento contínuo e estável destes gases.
Grande tamanho e peso de placas ultragrossas
Por exemplo, uma chapa de 220 mm x 2.200 mm x 8.000 mm de espessura pesa aproximadamente 30 toneladas. Além disso, o peso das peças individuais pode ser bastante substancial, com a placa de aço número 9 da biela superior, por exemplo, pesando mais de 4 toneladas (consulte a Figura 1).
Risco de defeitos de corte
Chapas ultragrossas são mais propensas a defeitos de corte, como corte impermeável, em comparação com chapas normais.
Grande perda de sucata de material
A significativa perda de material durante o processo de orla de chapas ultragrossas dificulta o reaproveitamento das arestas cortadas.
Cortando Distorção
O calor gerado durante o processo de corte pode causar deformação na chapa de aço e resultar em desvio das dimensões desejadas. Além disso, o ressalto repentino da placa sob alta tensão pode levar a riscos de segurança. Para evitar estes problemas de qualidade e segurança, é essencial considerar a distorção de corte ao formular o processo de corte.
2. A seção de corte de chapa ultraespessa está sujeita a defeitos de qualidade
(1) Defeitos de corte na borda superior
A borda superior do corte desmorona ou cai na forma de fios derretidos, resultando no colapso dos cantos arredondados devido ao derretimento muito rápido da borda superior da fenda.
Causas Possíveis:
- Escala refratária espessa na superfície do aço;
- Velocidade de corte lenta e chama de pré-aquecimento excessiva;
- Altura incorreta entre o bico de corte e a peça, tamanho grande do bico de corte e excesso de oxigênio na chama.
Conforme ilustrado na Figura 2.
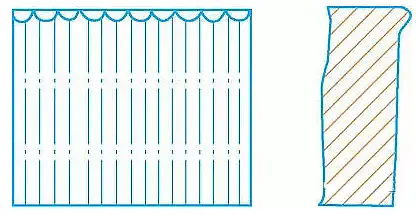
Figura 2
(2) Má planicidade da superfície de corte
① Há um defeito côncavo sob a borda da seção cortada (consulte a Figura 3). Além disso, a borda superior apresenta vários graus de colapso por fusão.
Isso pode ser atribuído à alta pressão de oxigênio de corte ou à altura excessiva entre o bico de corte e a peça de trabalho, bem como a um bico de corte entupido que causa interferência do vento.
② A seção de corte apresenta rugosidade excessiva.
Isto pode ser devido à velocidade de corte excessiva ou impurezas na chapa de aço que impactam na sua formação.
Conforme mostrado na Figura 3.
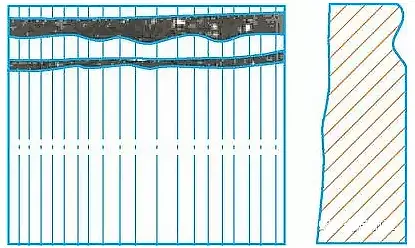
Figura 3
(3) Fraca Verticalidade
① A largura da costura de corte varia, sendo estreita na parte superior e larga na parte inferior ou vice-versa, devido a uma velocidade de corte rápida ou lenta, um bico de corte entupido que interfere na linha do vento e oxigênio de corte inadequado ou excessivo que leva à queima insuficiente ou excessiva do metal.
② A tocha de corte cria um ângulo oblíquo que não é perpendicular à superfície da peça de trabalho ou a linha do vento está incorreta.
(4) Defeitos de Corte na Borda Inferior
① Há uma depressão perto da borda inferior e a borda inferior derrete em cantos arredondados devido a uma velocidade de corte rápida, um bico de corte entupido ou danificado e uma linha de ar bloqueada ou deteriorada.
② A remoção de escória na superfície de corte ou borda inferior é difícil devido a fatores como velocidade de corte rápida ou lenta, bico de corte pequeno, baixa pressão de oxigênio de corte, excesso de gás na chama de pré-aquecimento, superfície da placa de aço corroída ou suja , altura excessiva entre o bico de corte e a peça de trabalho e uma forte chama de pré-aquecimento. Além disso, um alto teor de liga pode resultar na formação de escória na seção transversal e na borda inferior (consulte a Figura 4).
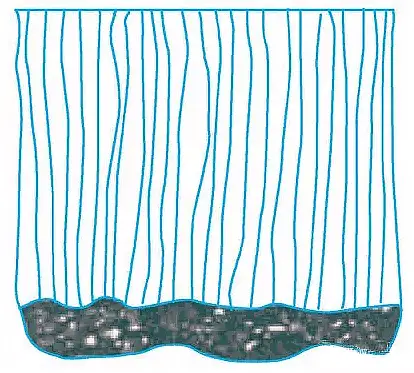
Figura 4
(5) Rachaduras
Microfissuras aparecem na seção de corte ou zona afetada pelo calor devido ao alto equivalente de carbono na placa de aço que resulta em alta sensibilidade a trincas, juntamente com a falta de medidas adequadas de pré-aquecimento e resfriamento lento.
(6) Deformação
O aquecimento local da chapa de aço durante o corte causa deformação por deslocamento do material, levando ao desvio dimensional das peças cortadas e afetando sua qualidade.
Conforme ilustrado na Figura 5.
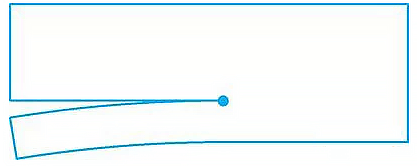
Figura 5
3. Processo de corte
(1) Corte do sistema de abastecimento de gás
Para manter um fornecimento consistente e confiável de oxigênio e gás acetileno, diversas garrafas de gás podem ser utilizadas em paralelo. Isso garantirá um fluxo estável e ininterrupto de gás acetileno.
Um pacote de fornecimento de gás paralelo pode ser criado conforme mostrado na Figura 6. Um tubo de aço de φ100 mm é utilizado como airbag e ambas as extremidades são soldadas de forma segura com placas de aço.
Seis tubos de entrada e um tubo de saída de ar são perfurados no tubo de aço, tomando cuidado para garantir a qualidade adequada da soldagem e evitando vazamentos no air bag.
Uma válvula de esfera estanque a gases e um dispositivo de conexão devem ser adicionados a cada entrada e saída de ar.
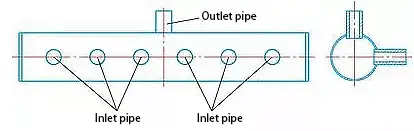
Figura 6
(2) Estrutura de suporte de corte
Devido ao grande tamanho e peso da chapa grossa, que tem peso máximo de 30 toneladas, e ao tamanho e peso substanciais das peças individuais, com peso máximo de 4 toneladas, a estrutura de suporte da máquina de corte CNC original não pode atender ao corte requisitos, pois fornece suporte insuficiente para as ripas (como mostrado na Figura 7a).
Para garantir um suporte estável da estrutura, são necessárias modificações na estrutura de suporte. Após cuidadosa análise, pesquisa e discussão, decidiu-se utilizar resíduos de aço em forma de H como estrutura de suporte de placa espessa.
(A) Estrutura de suporte antes da transformação
(B) Estrutura de suporte após transformação
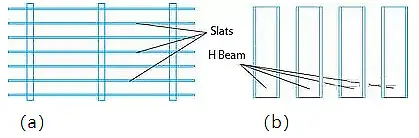
Figura 7
(3) Otimização do Programa de Corte
Inicialmente, o processamento do ponto de saída é introduzido.
O maior desafio no corte de placas ultra grossas (até 220mm) é garantir um corte de qualidade, principalmente no posicionamento dos pontos de entrada e saída das peças, o que muitas vezes leva a defeitos de corte.
Conforme ilustrado nas Figuras 8a e 8b, os pontos de corte de chapas grossas muitas vezes não são verticais.
Quando o ponto de corte coincide com o ponto de entrada, se a linha de corte girar neste momento, a raiz não será cortada, causando defeitos por fraturas pelo peso das peças.
Para evitar a ocorrência de tais defeitos, otimizar a entrada e a saída no processo de corte pode ser uma solução eficaz.
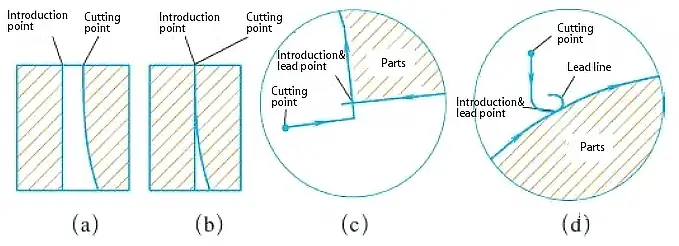
Figura 8
Em segundo lugar, se não forem tomados os devidos cuidados com a direção durante o processo de corte, pode causar deformação das peças. Isso ocorre porque a força de expansão afastará a peça, levando a inconsistências no tamanho da peça e no tamanho do programa.
Para resolver este problema, a nossa análise sugere que, ao cortar chapas de aço, o peso leve resulta em baixa pressão e atrito mínimo com a estrutura de suporte, fazendo com que a peça seja empurrada pela força de expansão. Por outro lado, o peso pesado produz alta pressão e atrito significativo com a estrutura de suporte, evitando que ela seja empurrada pela força de expansão.
É importante levar isso em consideração ao escrever o programa. Durante o processo de corte, a peça deve estar o mais conectada possível a uma peça pesada.
Com base neste princípio, a descarga, a sequência de corte e a direção de corte da biela superior são representadas na Figura 9.
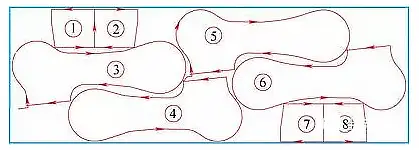
Figura 9
Finalmente, otimizar o layout pode economizar custos maiores ao otimizar o tamanho.
Ao projetar o programa, mais tempo pode ser alocado para otimizar o layout. É melhor utilizar qualquer material restante, e várias pessoas podem colaborar para verificar o tamanho da peça e gerar o programa após confirmar sua precisão.
Para cortar peças mais espessas, o modelo da tocha, o número do bico de corte e a pressão do oxigênio devem ser aumentados.
A pressão do oxigênio e a espessura da peça de corte, o modelo da tocha de corte e os parâmetros de corte de chapa ultragrossa devem ser selecionados com base no equipamento de campo, na experiência de corte e na tabela anexa.
Parâmetros para corte por chama de oxiacetileno de placa ultra grossa
Grossura | Diâmetro do bico de corte | Pressão de oxigênio | Pressão de acetileno | Tempo de pré-aquecimento | Velocidade de corte | Fluxo de gás |
---|---|---|---|---|---|---|
milímetros | milímetros | MPa | MPa | é | mm/min | L/min |
180 | 5 | 1,0-1,4 | 0,09-0,11 | 30-35 | 145-165 | 17-20 |
200 | 5 | 1,0-1,4 | 0,09-0,11 | 30-35 | 140-165 | 20-23 |
220 | 5 | 1,0-1,4 | 0,09-0,11 | 30-35 | 135-155 | 22-25 |
(4) Desempenho de corte
O corte da chapa de aço deve ser feito corretamente na primeira tentativa.
Comece cortando os cantos descartados da chapa de aço, ajustando a linha de ar de corte e garantindo que a seção cortada não apresente nenhum dos defeitos mencionados.
É importante monitorar de perto o processo de corte e resolver rapidamente quaisquer problemas que surjam.
4. Conclusões
Com uma preparação adequada e um processo de corte bem definido, o corte de placas ultra-espessas tem alcançado sucesso consistentemente em uma única tentativa. A qualidade e aparência dos produtos cortados atendem aos requisitos do processo, resultando na produção de peças qualificadas (conforme Figura 10).
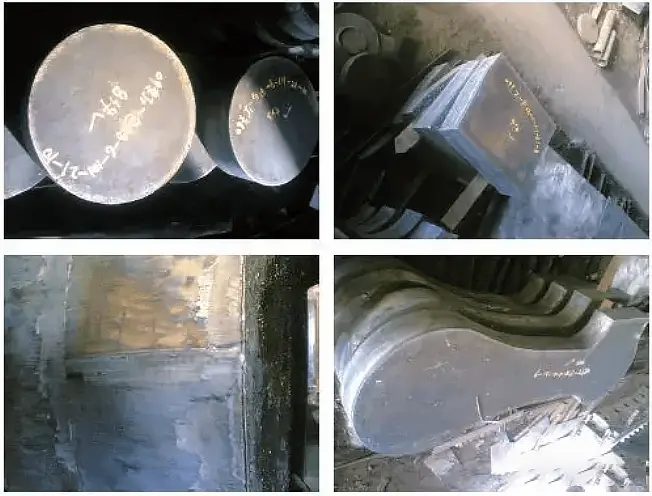
Figura 10
O processo de produção de chapas de aço ultragrossas por chama utilizando os equipamentos atuais foi estabelecido, fornecendo uma base técnica para a fabricação de produtos similares.