O que é soldagem por spray?
A soldagem por spray envolve o aquecimento de um revestimento em pó de liga autossolúvel pré-aquecido a uma faixa de temperatura de 1000-1300 ℃, derretendo as partículas, flutuando a escória na superfície do revestimento e dispersando o boreto e o siliceto no revestimento. Este processo permite uma boa combinação entre as partículas e a superfície do substrato.
O depósito final forma uma estrutura cristalina metálica densa e cria uma camada de ligação metalúrgica de aproximadamente 0,05-0,1 mm com a matriz. Esta camada de ligação tem uma resistência de cerca de 400MPa, excelente resistência ao impacto, resistência ao desgaste e resistência à corrosão, ao mesmo tempo que exibe uma aparência espelhada.
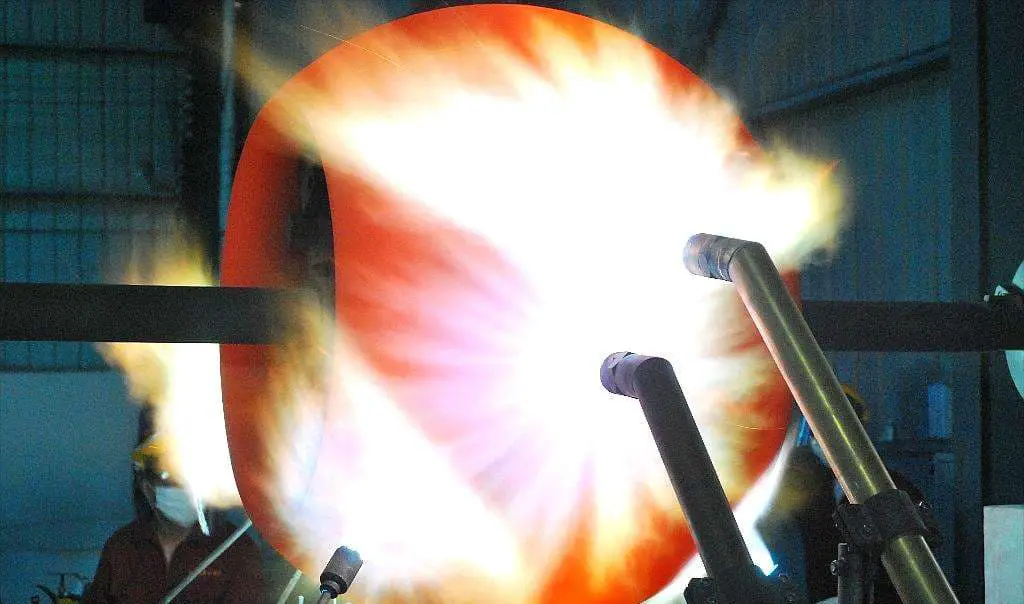
Vantagems de soldagem por spray
Comparado ao revestimento por spray, o revestimento por soldagem por spray oferece vantagens significativas. Porém, devido à alta temperatura que a matriz atinge durante o processo de refusão, até 900°C, pode ocorrer maior deformação térmica, levando a certas limitações no escopo de aplicação da soldagem por spray.
As peças e materiais adequados para soldagem por pulverização são geralmente:
① Peças vulneráveis que requerem alta dureza superficial e boa resistência ao desgaste sob carga de impacto, como lâminas de lixadeira, placas dentárias de britadores, dentes de caçamba de escavadeira, etc.
② Grandes peças vulneráveis com geometrias simples, como eixos, êmbolos, controles deslizantes, cilindros hidráulicos e placas de calha.
③ Materiais incluindo aço de baixo carbono, aço de médio carbono (menos de 0,4% de carbono), aço estrutural contendo menos de 3% de manganês, molibdênio e vanádio, aço inoxidável níquel-cromo, ferro fundido e outros materiais semelhantes.
Pó de liga autofluxante para soldagem por spray
O pó de liga autofundente é composto de níquel, cobalto e ferro como materiais de base. Quantidades apropriadas de elementos de boro e silício são adicionadas para servir como agentes desoxidantes, formadores de escória, fluxo de soldagem e para reduzir o ponto de fusão da liga. Este tipo de liga é adequada para fundir novamente o revestimento com chama de acetileno-oxigênio.
Existem muitos tipos de pós de liga autofundentes domésticos disponíveis. Os pós de liga à base de níquel têm forte resistência à corrosão, resistência à oxidação de até 650°C e apresentam forte resistência ao desgaste.
O pó de liga à base de cobalto é caracterizado por excelente dureza vermelha, permitindo manter boa resistência ao desgaste e à corrosão até 700°C.
O pó de liga à base de ferro possui resistência superior ao desgaste abrasivo em comparação com os outros dois tipos.
Processo de soldagem por pulverização
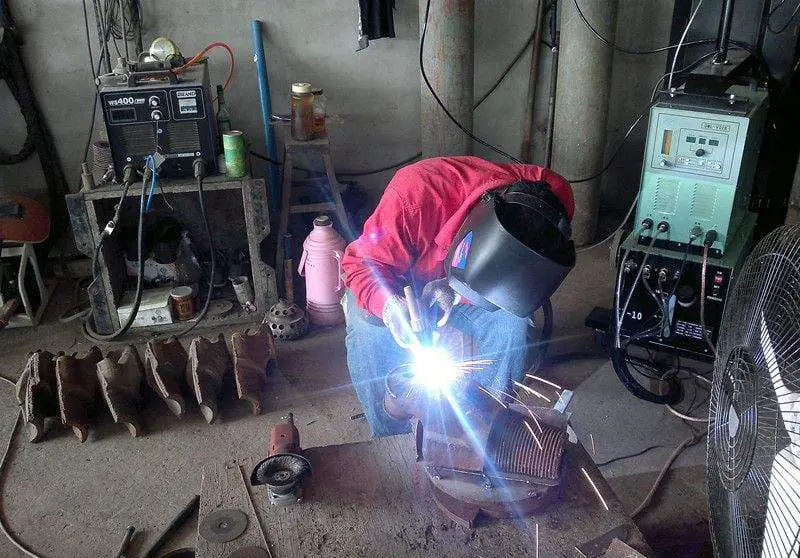
O processo de soldagem por pulverização é essencialmente semelhante ao da pulverização. No entanto, na soldagem por pulverização, um processo adicional de refusão é realizado durante o procedimento de pulverização do pó.
A soldagem por spray compreende dois tipos: soldagem por spray em uma etapa e soldagem por spray em duas etapas.
Antes de iniciar o processo, os seguintes pontos precisam ser levados em consideração:
① A camada de cementação ou nitretação presente na superfície da peça deve ser removida durante o pré-tratamento.
② A temperatura de pré-aquecimento da peça de trabalho deve ser de 200-300°C para aço carbono comum e 350-400°C para aço austenítico resistente ao calor. Uma chama neutra ou de carbono fraco deve ser usada para pré-aquecimento.
É importante notar que a espessura da camada pulverizada reduz aproximadamente 25% após a refusão. Portanto, este fator deve ser levado em consideração ao medir a espessura da camada a quente após a pulverização.
Soldagem por spray em uma etapa.
O método de uma etapa envolve alternar entre pulverização e fusão de uma seção de cada vez usando a mesma pistola de pulverização.
Pistolas de soldagem por pulverização médias e pequenas estão disponíveis para seleção.
Antes de começar, pré-aqueça a peça e aplique uma camada protetora de 0,2mm, selando bem a superfície para evitar oxidação.
Comece a pulverizar e derreter por uma das extremidades, mantendo uma distância de 10-30 mm.
Aqueça a camada protetora parcialmente em sequência até que o fundido comece a molhar sem fluir. Repita o processo, pulverizando e derretendo o pó até atingir a espessura predeterminada e a superfície apresentar um reflexo “espelho”. Em seguida, continue expandindo para frente até que toda a superfície esteja coberta com a camada de pulverização e soldagem.
Se a espessura for insuficiente, repita o processo.
O método de uma etapa é adequado para peças pequenas ou pequenas áreas que requerem soldagem por spray.
Método de soldagem por spray em duas etapas.
O método de duas etapas envolve primeiro aplicar a camada de pulverização e depois fundi-la novamente.
Pistolas de pulverização de alta potência, como pistolas de pulverização e soldagem SpH-E, são usadas para derreter completamente o pó da liga na chama e criar uma camada de depósito de deformação plástica na superfície da peça de trabalho.
Pó à base de ferro deve ser pulverizado usando uma chama de carbono fraco, enquanto chamas neutras ou de carbono fraco devem ser usadas para pó à base de níquel e cobalto.
Cada camada de pulverização de pó deve ter menos de 0,2 mm de espessura e a pulverização repetida deve atingir a espessura de refusão desejada de geralmente 0,5-0,6 mm.
Se uma camada espessa de soldagem por spray for necessária e uma refusão não for suficiente, ela poderá ser pulverizada e refundida várias vezes.
A refusão é o processo chave no método de duas etapas e deve ser realizada imediatamente após a pulverização.
Deve ser usada uma chama suave de alta potência de chama neutra ou chama fraca de carbonização.
A distância de pulverização deve ser de cerca de 20-30 mm e o ângulo entre a chama e a superfície deve ser de 60°-75°.
Começando a cerca de 30 mm de distância do revestimento, a velocidade de refusão deve ser controlada adequadamente e o revestimento deve ser aquecido até que apareça um reflexo “espelhado” do revestimento antes de refundir a próxima peça.
Durante a refusão, é necessário evitar o derretimento excessivo (ou seja, rachaduras na superfície do espelho), o escoamento do metal do revestimento ou a oxidação da superfície devido ao tempo excessivo de aquecimento local.
Durante a refusão multicamadas, a camada anterior deve ser resfriada a cerca de 700°C e a escória da superfície deve ser removida antes da pulverização secundária.
A refusão não deve ser feita mais de três vezes.
Resfriamento da peça de trabalho.
Peças de aço de médio e baixo carbono, peças de aço de baixa liga e peças fundidas de ferro com camada fina de soldagem com formatos simples podem ser resfriadas naturalmente ao ar.
No entanto, para peças fundidas de ferro com camada de soldagem espessa e formato complexo, peças fundidas de aço-liga com alto teor de manganês, cobre e vanádio e peças com alta dureza, devem ser enterradas em poços de cal para resfriamento lento.
Diferença de processo entre pulverização e soldagem por pulverização
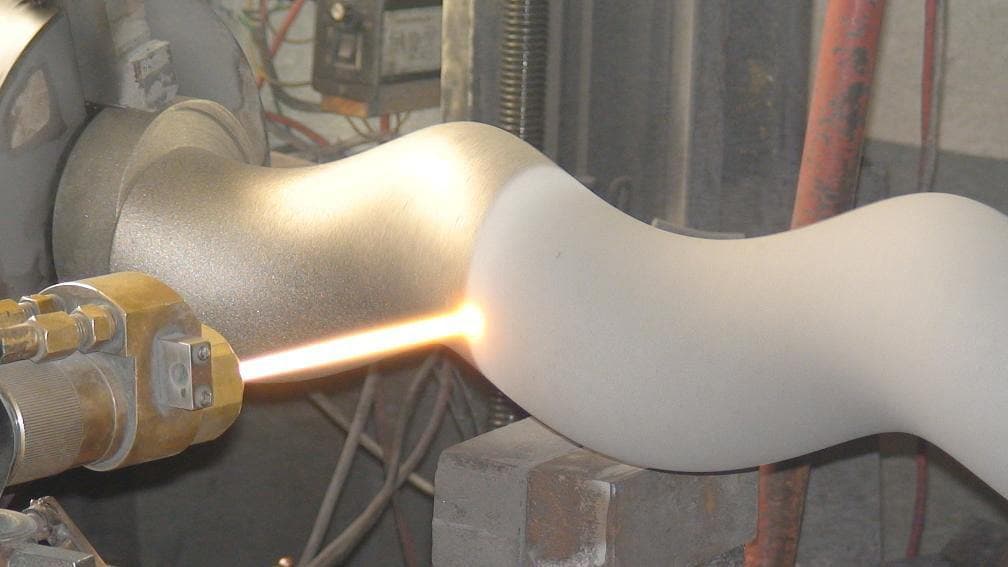
A combinação da camada de pulverização e da camada de soldagem por pulverização com o metal base é diferente.
Ao aquecer o alumínio revestido de níquel com um feixe de chama pulverizado, ocorre uma reação química exotérmica e a remoção da ferrugem por jato de areia atinge Sa3, RZ>50 μm. A superfície do aço carbono forma um revestimento de ligação mecânica com uma camada inferior de ligação micrometalúrgica e uma camada de trabalho, que também produz um efeito de “gancho de ancoragem”. Em contraste, a ligação entre a camada de soldagem por pulverização e o substrato é puramente um revestimento de ligação metalúrgica.
Diferentes materiais de pulverização requerem o uso de pó de liga autofusível para soldagem por spray, enquanto a pulverização requer pó de baixa autofusibilidade, que não é necessariamente pó de liga autofusível.
Vários pós de liga autofusíveis podem ser usados tanto para soldagem por pulverização quanto para pulverização, mas o pó de pulverização não possui autofusibilidade. Portanto, ele só pode ser usado para pulverização e não para o processo de soldagem por pulverização.
A peça de trabalho é aquecida de maneira diferente durante a pulverização e a soldagem por pulverização, e a temperatura de pré-aquecimento antes da pulverização também é diferente. Como resultado, a microestrutura e as propriedades da peça após a pulverização também são diferentes.
A densidade do revestimento também difere, pois a camada de soldagem por pulverização é densa, enquanto o revestimento por pulverização possui alguns poros.
Além disso, a capacidade de suportar carga é diferente. Geralmente, o revestimento em spray pode suportar contato em grandes áreas e é usado principalmente em superfícies de trabalho lubrificadas, superfícies de contato e outras condições de trabalho com menos estresse. No entanto, o revestimento para soldagem por spray pode suportar grandes forças de impacto, tensões de extrusão ou tensões de contato.
Aplicação de soldagem por spray
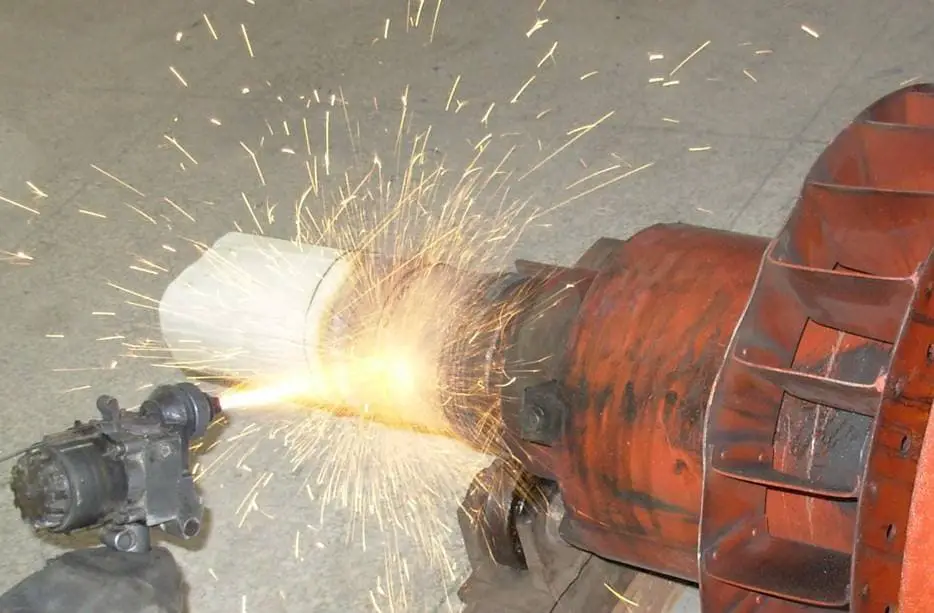
(1) A carga superficial em peças feitas de vários aços carbono e aços de baixa liga é significativa, especialmente sob cargas de impacto.
Para peças com resistência de ligação entre revestimento e substrato de 350-450N/mm2dureza da soldagem por spray HRC150 ≤ 65, espessura do revestimento variando de 0,3 a vários milímetros e rugosidade da superfície da camada de soldagem por spray após a retificação atingindo Ra0,4-0,1 μm acima.
(2) Quando utilizado em meio corrosivo, o revestimento deve ser compacto e livre de poros.
(3) O design original da superfície da peça adota têmpera, cementação, nitretação, cromagem dura e outros processos, exigindo que a superfície tenha alta dureza.
(4) O ambiente de trabalho da peça de trabalho é ruim, como forte desgaste abrasivo, desgaste por erosão, cavitação, etc.
(5) O processo de soldagem por spray de pó de liga de chama de oxiacetileno é adequado para reforço de superfície ou reparo de várias peças de aço carbono e aço de baixa liga, mas algumas características dos materiais da peça devem ser observadas.
Quando o coeficiente de expansão linear do material de base é muito diferente daquele da camada de soldagem por pulverização de liga, ou seja, menos de 12 × 10-6/℃ ou superior a 12 × 10-6/℃, este processo deve ser usado com cautela para evitar rachaduras.
Se o conteúdo de elementos com alta afinidade ao oxigênio no metal base for superior a 3%, como tungstênio e molibdênio, o conteúdo total de alumínio, magnésio, cobalto, titânio, molibdênio e outros elementos for superior a 0,5%, ou o teor de enxofre no aço for maior, também trará dificuldades para a soldagem por pulverização.
Isso ocorre porque esses materiais geram um filme de óxido denso e estável sob a ação do oxigênio, bloqueando o efeito umectante da liga fundida sobre a base.
Durante a refusão, a liga líquida rolará como contas, como “gotas de suor”.
Portanto, ao utilizar o processo de soldagem por pulverização, deve-se prestar atenção à adaptabilidade deste processo ao material de base pulverizado.
(6) Materiais metálicos que podem ser soldados por pulverização sem tratamento especial:
① Aço estrutural de carbono com teor de carbono ≤ 0,25%.
② Liga de aço estrutural com teor total de Mh, Mo, V, Cr e Ni <3%.
③ Aço inoxidável 18-8, aço inoxidável níquel, aço fundido cinza, ferro maleável, ferro dúctil, ferro puro com baixo teor de carbono, cobre vermelho.
(7) Materiais metálicos que requerem resfriamento lento após soldagem por pulverização a 250-375 ℃ devem ser pré-aquecidos:
① Aço estrutural de carbono com teor de carbono >0,4%;
② Aço estrutural de liga de manganês, molibdênio e vanádio com teor total de níquel> 3%;
③ Liga de aço estrutural com teor de cromo ≤ 2%;
(8) Materiais metálicos que requerem recozimento isotérmico após soldagem por pulverização:
① Aço inoxidável martensítico com teor de cromo ≥ 13%;
② Aço estrutural de liga de níquel-molibdênio com teor de carbono ≥ 0,4%.
Depois de determinar o processo de soldagem por pulverização, a seleção do processo de soldagem por pulverização de uma ou duas etapas deve ser baseada nas seguintes condições:
(1) Se a peça de trabalho exigir reparo local e a posição de soldagem por spray não puder tolerar uma grande entrada de calor, use o processo de soldagem por spray de uma etapa. Por exemplo, o reparo de cicatrizes locais em várias guias de máquinas-ferramenta pode ser feito através deste processo.
(2) Se a superfície da peça for complexa ou irregular, como rodas dentadas, superfícies de dentes de engrenagens, alimentadores de parafuso, etc., use o processo de soldagem por spray de uma etapa.
(3) Para peças grandes que são difíceis de aquecer como um todo, como rodas de locomotivas e bondes, o processo de soldagem por spray de uma etapa deve ser usado.
(4) Para peças de eixo em geral que podem girar na máquina-ferramenta, use o processo de soldagem por spray em duas etapas.
(5) A dureza do revestimento deve ser o mais próxima possível da dureza superficial do projeto original. Por exemplo, se a dureza superficial do projeto original for HRC≥55, o que foi alcançado através de processos de têmpera ou tratamento químico, o pó de “revestimento duro”, como Ni15Ni60Fé65ou pó composto Wc, deve ser usado.
(6) Superfícies não conjugadas altamente desgastadas, como impulsores, carcaças de bombas de lama, dentes de pás de carregadeiras de rocha, superfícies de alimentadores em espiral, etc., devem ser feitas de pós compostos de alta dureza, como Ni15Ni60Fé65ou Wc.
(7) Peças de trabalho que não podem ser processadas em tornos e retificadoras, mas precisam ser processadas, só podem ser feitas manualmente com limas e outras ferramentas. Por exemplo, reparar cicatrizes locais na superfície do trilho-guia da máquina-ferramenta requer o uso apenas de pós de soldagem por pulverização de baixa dureza, como SH, F103Ni15etc.
(8) Diferenças entre processos de soldagem por pulverização e revestimento por arco:
Durante o processo de soldagem por spray, a ligação entre a camada de soldagem por spray e a matriz é uma ligação metalúrgica por difusão de solução, enquanto a superfície usa uma ligação metalúrgica por fusão.
A matriz não derrete durante o processo de soldagem por spray, mas há um efeito de dissolução entre a camada de soldagem por spray e a matriz, resultando em uma zona de difusão de solução mútua entre as duas.
Como a matriz é insolúvel, a camada de soldagem por pulverização não será diluída pelo material de base. Assim, a taxa de diluição é extremamente baixa, garantindo um bom desempenho da camada de soldagem por pulverização.
Em contraste, a matriz de soldagem de sobreposição é derretida e a taxa de diluição da camada de soldagem de sobreposição é alta. O desempenho da camada de soldagem só pode ser garantido se a soldagem overlay for muito espessa, dificultando a garantia das arestas e cantos do contorno da peça. Isso pode levar a defeitos comuns, como cortes inferiores e colapsos de cantos. No entanto, a soldagem por spray não apresenta tais defeitos.
Características de soldagem por pulverização de peças de ferro fundido
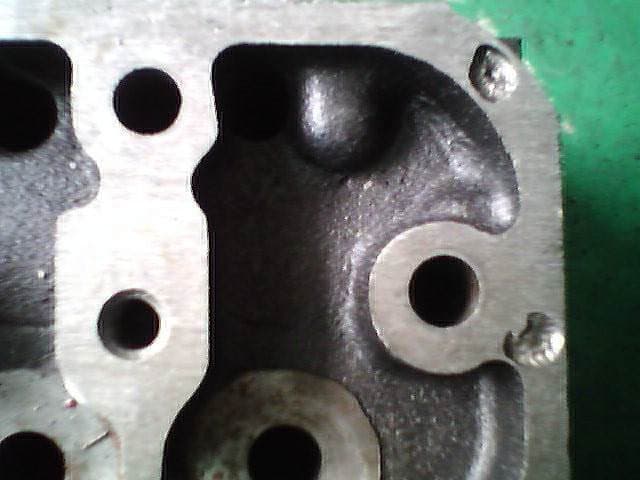
(1) O ferro fundido é uma liga de ferro-carbono com um teor de carbono superior a 2%. É amplamente utilizado em diversas indústrias, normalmente contendo 2,5% a 4% de carbono, 1% a 3% de silício e pequenas quantidades de manganês, enxofre, fósforo, etc.
O ferro fundido tem alto teor de carbono, baixa resistência e é sensível às mudanças de temperatura. Durante o reparo de soldagem, ele experimenta aquecimento local, grandes diferenças de temperatura e taxas de resfriamento rápidas. Como resultado, soldar ferro fundido é um desafio.
A fraca soldabilidade do ferro fundido leva a vários problemas durante o reparo da soldagem:
(2) A peça de reparo por soldagem pode facilmente desenvolver uma microestrutura branca que é dura, quebradiça e difícil de usinar. Tal estrutura também tende a rachar facilmente.
(3) As rápidas taxas de aquecimento e resfriamento durante o reparo da soldagem podem causar rachaduras por tensão térmica. Além disso, a presença de impurezas como enxofre e fósforo no ferro fundido aumenta a probabilidade de trincas no reparo da solda.
(4) A porosidade e a inclusão de escória também são problemas comuns. Devido ao alto teor de carbono, mais impurezas e rápidas taxas de resfriamento no processo de reparo de soldagem, gases e óxidos não podem precipitar e flutuar com o tempo, levando à formação de porosidade ou inclusão de escória na zona de solda.
Felizmente, a soldagem por pulverização em uma etapa com pó de liga de chama de oxigênio-acetileno pode resolver esses problemas de forma satisfatória.
(5) O ponto de fusão do pó da liga usado na soldagem por spray é inferior ao da matriz. Durante a refusão, a matriz de ferro fundido não derrete, evitando assim o problema de diluição da camada de soldagem por pulverização e a criação de uma zona semi-fundida. Consequentemente, a soldagem por spray correta não produz uma microestrutura branca na área de reparo da solda, facilitando o processamento.
Além disso, como a matriz não derrete, ela evita naturalmente que impurezas como enxofre e fósforo derretam na camada de soldagem por spray, o que ajuda a prevenir rachaduras.
(6) O processo de soldagem por spray de uma etapa envolve menos entrada de calor para o substrato e tem um efeito térmico menor no substrato, tornando-o mais eficaz no controle de trincas por tensão térmica. A baixa entrada de calor é particularmente vantajosa no reparo de peças com alta precisão dimensional.
Além disso, o uso de aquecimento por chama de oxigênio-acetileno, que é mais lento que o resfriamento por soldagem elétrica, também é útil na prevenção de rachaduras e deformações.
(7) O pó de liga usado na soldagem por spray contém fortes elementos desoxidantes, como boro e silício. Esses elementos protegem os demais elementos do pó da queima oxidativa e reduzem os óxidos na superfície da matriz, evitando assim a formação de poros e inclusão de escória.
(8) A camada de soldagem por spray tem uma estrutura compacta e plana, é bem formada, sem cortes inferiores e requer apenas uma pequena quantidade de processamento. Isso resulta em economia de material e alta eficiência. Peças de ferro fundido soldadas por spray geralmente usam SH · F103, pó de liga à base de níquel Ni15, etc. No entanto, o pó de liga à base de ferro tem um alto ponto de fusão, alta fragilidade, impacto significativo na matriz e baixo desempenho.
(9) Durante a soldagem por pulverização, o objetivo principal do pré-aquecimento da peça é remover a umidade da superfície da peça e gerar alguma expansão térmica. Isto reduz a diferença de temperatura, minimizando assim o estresse térmico e promovendo melhor resistência de ligação da camada de soldagem por pulverização.
As temperaturas de pré-aquecimento geralmente variam de 250-300°C para aço, 450-500°C para aço inoxidável austenítico, 350-400°C para aço inoxidável níquel-cromo e 250-300°C para aço de baixa liga e ferro fundido. Para peças pequenas e aço facilmente oxidável, a temperatura de pré-aquecimento é mais baixa.
A espessura da camada de soldagem por pulverização depende das características de expansão térmica e contração a frio da peça de trabalho após a pulverização. O encolhimento após a refusão é normalmente em torno de 25-30%. Portanto, ao determinar a espessura do revestimento, a tolerância de usinagem e o diâmetro da peça antes da pulverização devem ser levados em consideração, juntamente com a contração.
A espessura do revestimento por pulverização é calculada da seguinte forma: Espessura do revestimento antes da refusão = (espessura da camada de soldagem por pulverização + tolerância de usinagem) ÷ (1-0,3).
Leitura relacionada: Como soldar ferro fundido?
Circunstâncias em que o processo de soldagem por pulverização não pode ser usado.
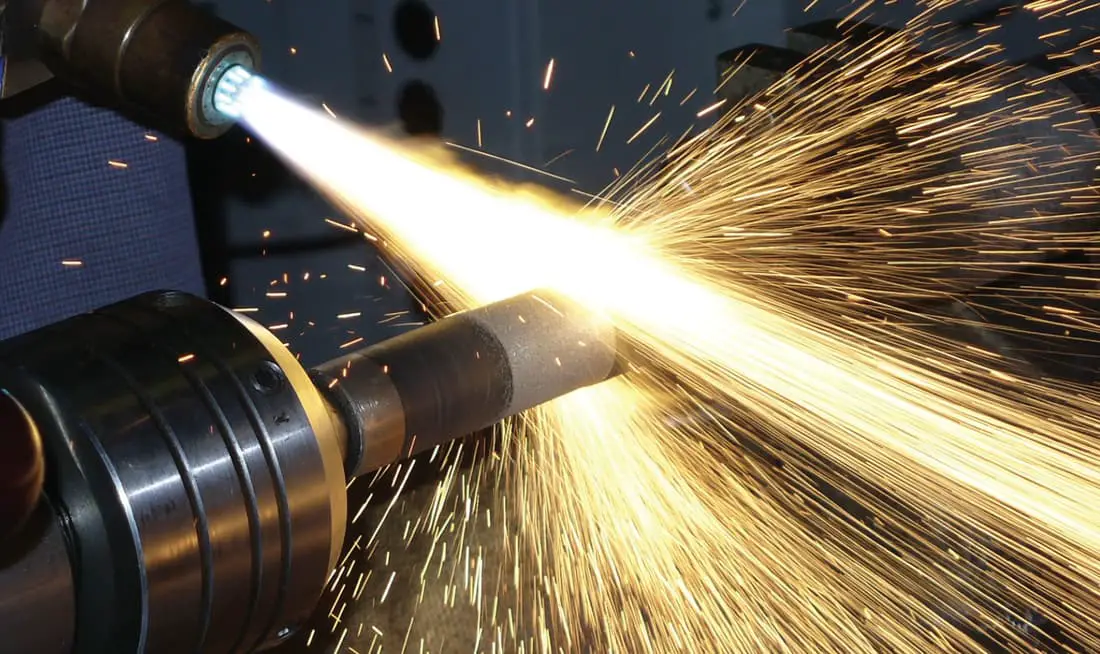
(1) Materiais com ponto de fusão inferior ao das ligas, como alumínio e suas ligas, magnésio e suas ligas, latão e bronze.
(2) A peça de trabalho é um eixo delgado ou uma placa muito fina que não deve deformar.
(3) Os requisitos de projeto original da peça são muito rígidos e a estrutura metalográfica não pode mudar.
(4) Aço de liga de níquel-cromo-molibdênio com alta temperabilidade.
(5) Aço martensítico com alto teor de cromo e teor de cromo superior a 18%.
(Nota: A soldagem por spray de alta precisão pode ser realizada em eixos longos com diâmetro externo superior a 28 mm e comprimento inferior a 8 m.)
Pontos-chave do processo de soldagem por spray para peças fundidas de ferro
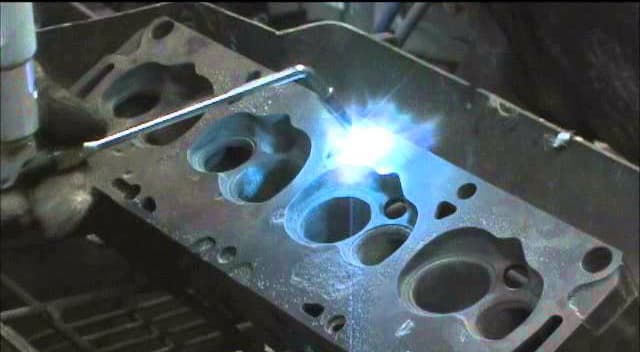
① Existem muitas peças em veículos e equipamentos mecânicos feitos de ferro fundido, e vários problemas são inevitáveis durante a fabricação ou uso. O processo de soldagem por spray de chama de oxigênio e acetileno não é apenas uma forma eficaz de fortalecer o ferro fundido, mas também um meio ideal para reparar vários defeitos e danos, como buracos de areia, buracos de ar, desgaste e outros danos em peças fundidas.
② A soldagem por spray é usada principalmente para reparar defeitos locais de peças fundidas de ferro, que variam em tamanho e profundidade. É adequado para soldagem por spray em uma etapa. Pistolas de pulverização de pequena potência devem ser usadas tanto quanto possível para reduzir a entrada de calor no substrato, dependendo das peças da peça e do reparo de soldagem necessário. Geralmente, QH-1/h, QH-2/h, QH-4/h, etc., são selecionados.
③ Durante a soldagem por pulverização, o pó de liga à base de níquel (série Ni-B-Si) deve ser preferido devido à baixa soldabilidade das peças de ferro fundido. O ponto de fusão do pó de liga à base de níquel é geralmente de 950 ~ 1050 ℃ e a matriz não derrete durante a refusão. Ao mesmo tempo, a camada de soldagem por pulverização em pó à base de níquel com baixo teor de carbono tem baixa dureza e boa plasticidade. O relaxamento da tensão da soldagem por pulverização é útil para evitar rachaduras, o que é extremamente importante para operadores não qualificados.
④ Ao selecionar as especificações de soldagem por pulverização, fatores como material de ferro fundido, tamanho das peças defeituosas e requisitos de condições de trabalho devem ser considerados. É importante garantir a energia necessária da chama e, ao mesmo tempo, minimizar a entrada de calor no substrato. Os limites apropriados de pressão de oxigênio e gás acetileno devem ser seguidos, e a distância de pulverização e fusão deve ser ajustada adequadamente durante a pulverização e refusão do pó para controlar a entrada de calor.
⑤ Pequenos defeitos locais, como furos de ar e furos de areia, podem ser reparados por soldagem sem pré-aquecimento antes da soldagem por pulverização. A área de aquecimento ao redor da camada de soldagem por pulverização deve ser minimizada para tornar a área de alta temperatura a menor possível.
⑥ Para o reparo de defeitos locais pequenos e profundos, a soldagem por pulverização contínua é adequada. Este método tem uma alta taxa de deposição de pó, rápido crescimento de espessura e alta eficiência, mas requer tecnologia de operação qualificada para coordenar a quantidade de alimentação de pó com a velocidade de pulverização e fusão para obter pulverização e penetração uniformes.
⑦ Para defeitos grandes e profundos, a soldagem por pulverização intermitente pode ser usada para evitar um aumento no estresse térmico devido ao aquecimento excessivo do substrato. Soldagem elétrica e soldagem por spray também podem ser usadas, e hastes de soldagem podem ser usadas para preencher as partes inferior e superior para soldagem por spray. Se a espessura da parede da peça fundida for grande, o plantio de arame pré-pulverizado pode ser usado para aumentar a resistência da ligação, evitar que a camada de soldagem por spray se solte do metal base e eliminar parte do estresse térmico da soldagem por spray.
⑧ Fundições grandes e complexas para soldagem por spray geralmente sofrem alto estresse térmico, portanto, medidas devem ser tomadas para reduzir o acúmulo de tensão durante a soldagem por spray, como o uso de métodos de redução de tensão de aquecimento e o método de simetria de subseção. O pré-aquecimento antes da soldagem e o resfriamento lento após a soldagem também podem alcançar bons resultados.
⑨ É importante controlar a temperatura de refusão durante a soldagem por pulverização. Se a temperatura for muito alta, os elementos da liga podem queimar, a matriz pode superaquecer e até derreter, resultando na entrada do carbono do ferro fundido na camada de soldagem por spray. Isso aumenta o teor de carbono, a dureza e reduz a plasticidade, podendo causar maior estresse térmico levando à formação de fissuras. No entanto, se a temperatura de refusão for muito baixa, pode levar à inclusão de cinzas ou à impenetrabilidade e afetar a resistência da ligação. Os operadores devem prestar atenção ao estado da superfície do revestimento durante a refusão e remover a pistola de refusão imediatamente assim que o “reflexo do espelho” for exibido, indicando que o pó derreteu e a escória flutuou. As peças fundidas novamente não devem ser reaquecidas.