Nos estágios iniciais, a produção em linha manual utilizava matrizes de estampagem, o que resultava em um alto índice de retrabalho e refugo devido à queda de cavacos de ferro das bordas das matrizes. Isso impactou seriamente nossa qualidade, custo e eficiência.
Para resolver esse problema, estabelecemos um grupo de pesquisa técnica focado no corte e na queda de cavacos de ferro, e conduzimos uma extensa pesquisa sobre o problema da queda de cavacos de ferro. Os resultados desta pesquisa foram bem-sucedidos.
O objetivo da principal fábrica de motores da indústria automobilística é alcançar alta qualidade mantendo baixo custo.
O ritmo de produção da linha de produção de estampagem manual na antiga fábrica era de 3 a 5 golpes por minuto (spm). No entanto, após a atualização para uma linha de produção automática, o ritmo de produção aumentou para 6 a 10 spm, resultando no dobro da eficiência da produção e na redução significativa de custos na produção e nas operações.
Um desafio que enfrentámos foi que os moldes utilizados na linha manual não eram suficientes para suportar as exigências da linha automática. Para superar isso, os moldes utilizados na linha manual tiveram que ser transformados e atualizados para atender aos requisitos da produção em linha fechada automática.
O problema das lascas de ferro caindo da matriz de estampagem
O principal objetivo da conversão do molde da linha de estampagem manual em um molde automático é resolver o problema da queda de limalha de ferro durante o corte.
As escritas de ferro na produção de estampagem tendem a aderir à superfície do molde e das peças (conforme mostrado na Figura 1), causando recortes na superfície das peças (conforme mostrado na Figura 2).
Quando defeitos de indentação são detectados pelo inspetor de qualidade de final de linha, pelo menos 7 peças devem ser retrabalhadas ou descartadas.
Isto não só impacta severamente a qualidade da aparência dos produtos de estampagem, mas também aumenta o custo das operações subsequentes.
Eliminar as escritas de ferro produzidas pelas matrizes de corte é um grande desafio na produção de estamparia.
Ao otimizar e transformar a estrutura da matriz da linha de produção manual, podemos efetivamente reduzir a quantidade de escritas de ferro produzidas durante a produção, e não haverá esmagamento significativo de escritas de ferro residual na superfície das peças estampadas.
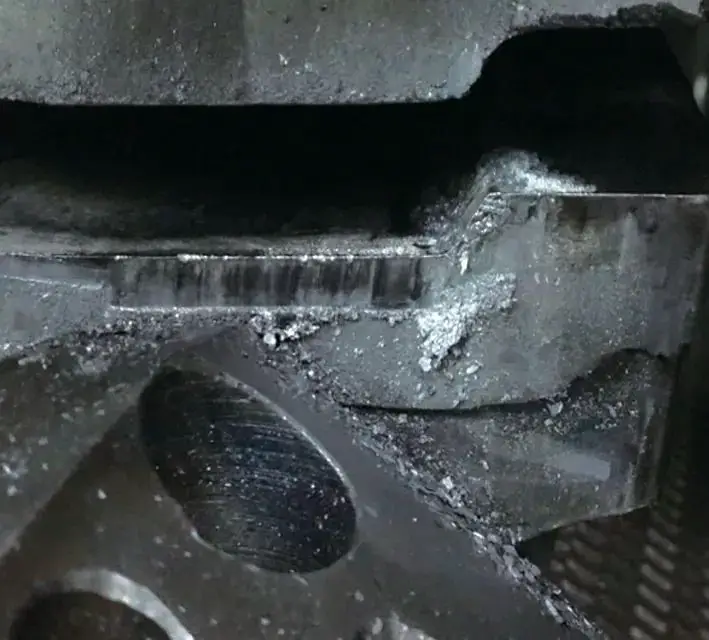
Fig. 1 acúmulo de limalha de ferro no bloco inferior da matriz
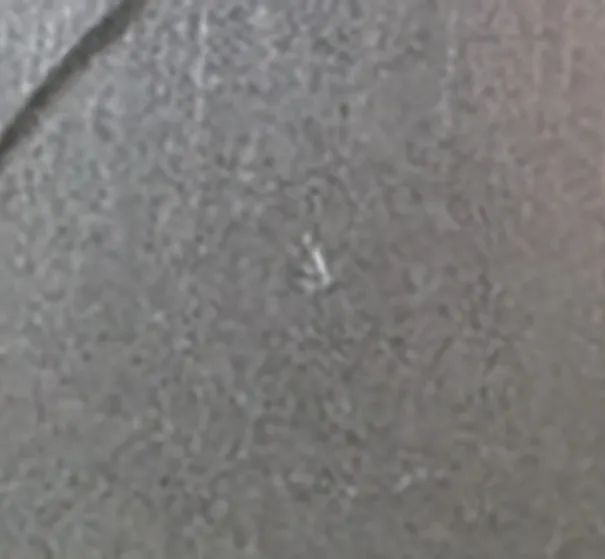
Fig. 2 esmagamento na superfície externa das peças estampadas
Otimização e retificação da estrutura da lâmina
A otimização e correção do bloco de faca de corte e punção podem atender aos padrões, manter a produção estável, minimizar a geração de limalha de ferro e resolver efetivamente o problema de escritas de ferro.
⑴ A otimização e melhoria do bloco de ferramentas de endireitamento inclui as seguintes etapas (conforme mostrado nas Figuras 3 e 4):
① Suavização da porção “ondulada” da superfície de referência;
② Transformar o cone positivo da superfície de corte em um plano vertical de 90°;
③ Afiação da aresta através de reparos;
④ Manter a superfície de referência a uma distância de 10mm.
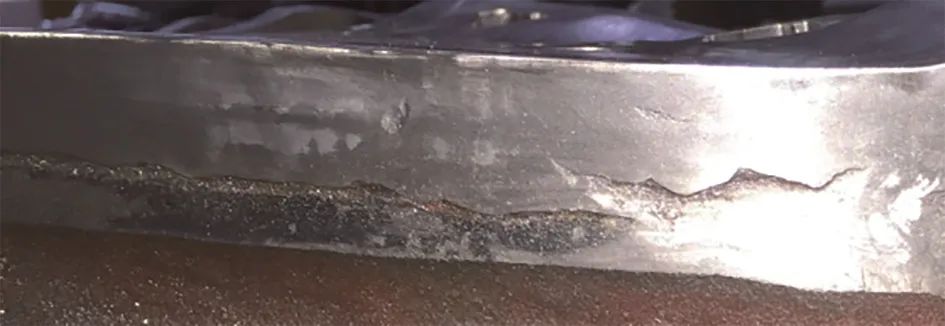
Fig. 3 antes da retificação do bloco de ferramentas de reparo direto
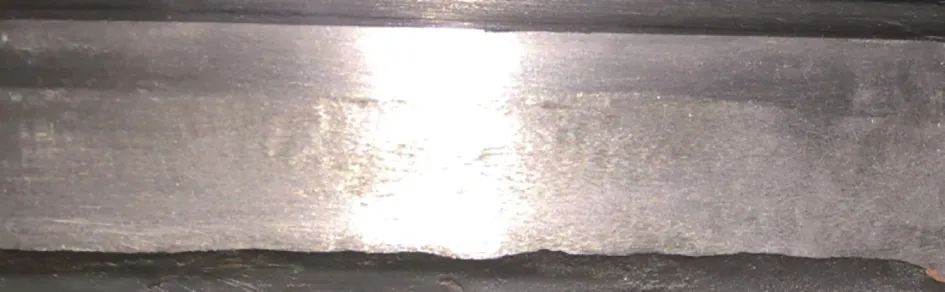
Fig. 4 após a retificação do bloco de ferramentas de reparo direto
⑵ A otimização e melhoria do punção incluem as seguintes etapas (conforme mostrado nas Figuras 5 e 6):
① Diminuir a ingestão original de 10 mm para 5 mm;
② Abaixando a borda periférica da parte superior do punção e achatando a protuberância intermediária;
③ Moldar e polir a borda e a circunferência do punção.
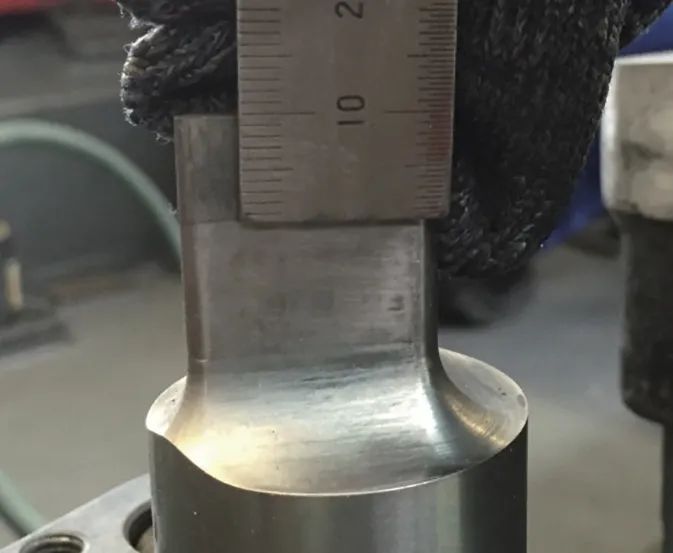
Fig. 5 ingestão excessiva de punção
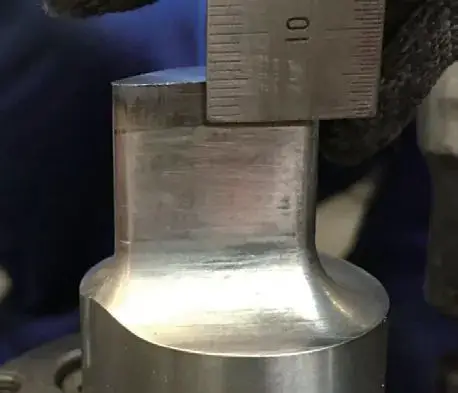
Fig. 6 ingestão razoável de punção
⑶ A otimização e melhoria da folga da lâmina e sua distância da placa de prensagem incluem:
① Esmerilhar e alinhar a folga da lâmina com ponta vermelha para garantir um espaçamento uniforme e adequado (conforme mostrado nas Figuras 7 e 8);
② Aumentar a folga entre a aresta de corte e a placa de pressão de 0 ~ 0,1 mm para 0,5 mm ~ 0,7 mm (conforme mostrado nas Figuras 9 e 10).
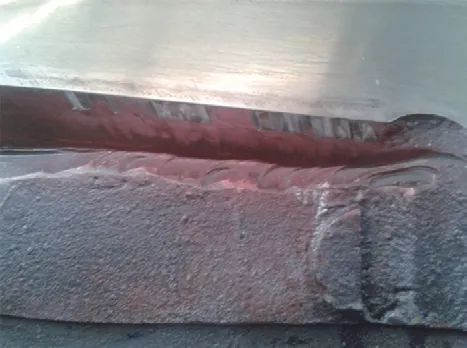
Fig. 7 a folga da lâmina é muito pequena
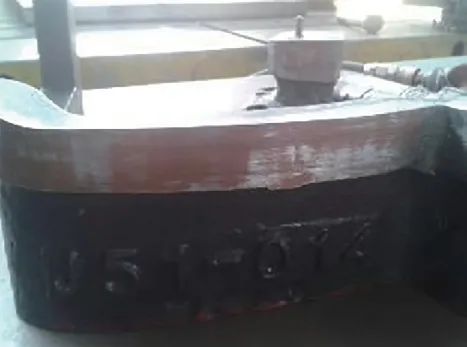
Fig. 8 folga uniforme da lâmina
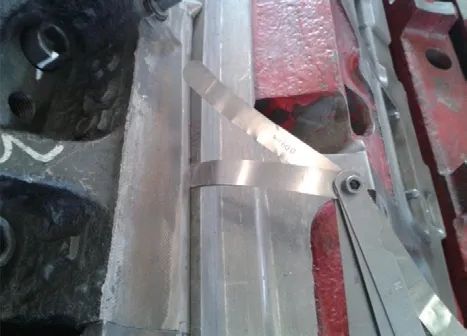
Fig. 9 a folga entre a aresta de corte e o contorno da placa de prensagem é pequena
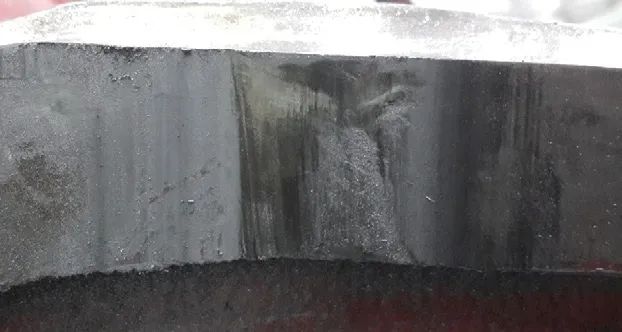
Fig. 10 a folga entre a aresta de corte e o contorno da placa de prensagem é uniforme
(4) A otimização e melhoria das facas residuais incluem as seguintes etapas (conforme mostrado nas Figuras 11 e 12):
① Reduzindo a folga entre a faca residual e o bloco da faca de 7mm para 1mm;
② Diminuindo a ingestão de 12mm para 4mm;
③ Mudar de uma faca não vazia para uma faca vazia.
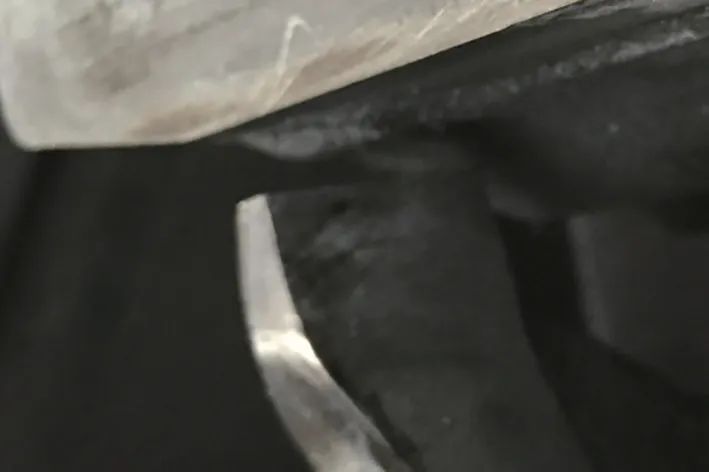
Fig. 11 resíduos de faca antes da retificação
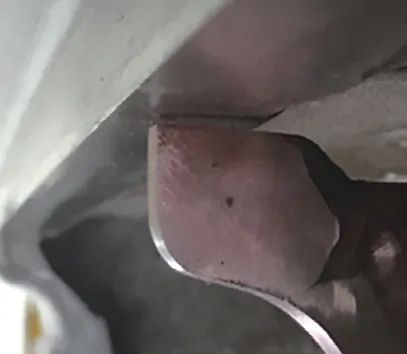
Fig. 12 após retificação de resíduos de faca
Retificação da estrutura central de prensagem
A otimização e melhoria da superfície de prensagem do núcleo de prensagem incluem as seguintes etapas (conforme mostrado nas Figuras 13 e 14):
① Diminuir a superfície de controle de prensagem do núcleo de prensagem de um máximo de 40cm para menos de 20cm.
A redução da área de prensagem ajuda a minimizar os recuos, pois mesmo pequenas quantidades de limalha de ferro não serão introduzidas no molde;
② Aumentar a taxa de lapidação do núcleo de prensagem de 75% para mais de 95%;
③ Alisar e polir todas as superfícies de prensagem.
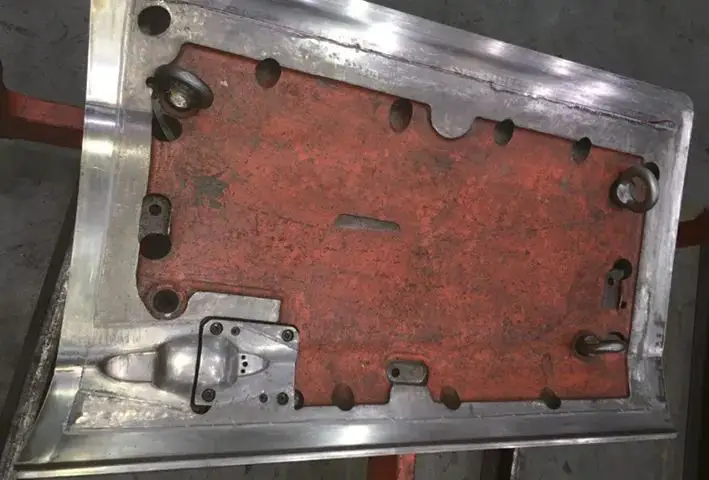
Fig. 13 antes da retificação do perfil do núcleo de prensagem
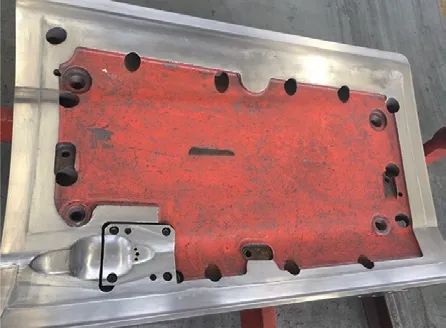
Fig. 14 após retificação do perfil do núcleo de prensagem
Um orifício de ventilação com diâmetro de 30 mm foi adicionado à área fechada local dentro do núcleo de prensagem para manter a consistência com a pressão do ar externo, evitando assim o problema de absorção de restos de ferro devido à pressão negativa dentro do molde durante a produção (como mostrado nas Figuras 15 e 16).
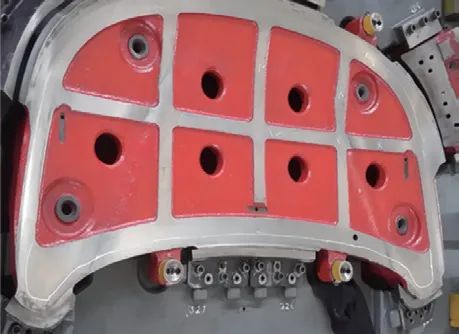
Fig. 15 antes de adicionar o orifício de ventilação ao núcleo de prensagem
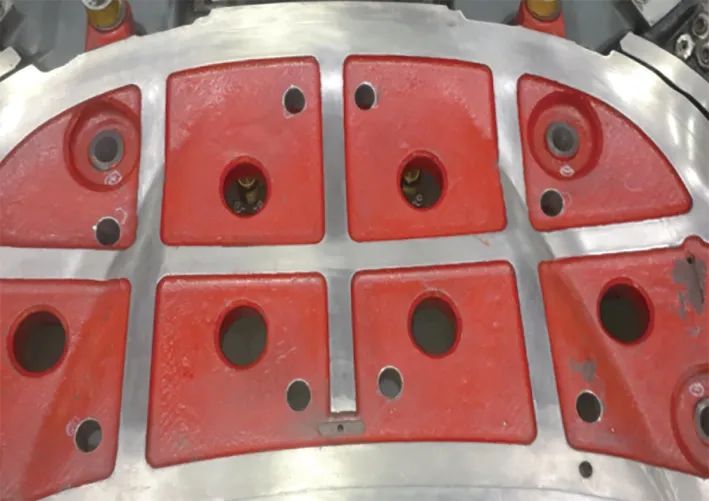
Fig. 16 após adicionar o orifício de ventilação ao núcleo de prensagem
Adicione um orifício de ventilação para perfurar
A otimização e melhoria da adição de orifícios de ventilação no punção incluem:
① Aumentando o número de orifícios de ventilação na superfície do punção de 230 para 290, resultando em um aumento de 26%.
Os orifícios de ventilação estão localizados em áreas com grandes superfícies e transições de arco suaves.
O tamanho dos orifícios de ventilação é de φ6mm, o que é consistente com o tamanho original (conforme mostrado nas Figuras 17 e 18);
② Suavização e polimento da superfície convexa do modelo.
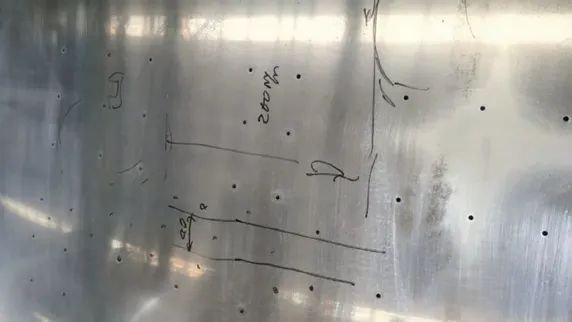
Fig. 17 perfure antes de adicionar o orifício de ventilação
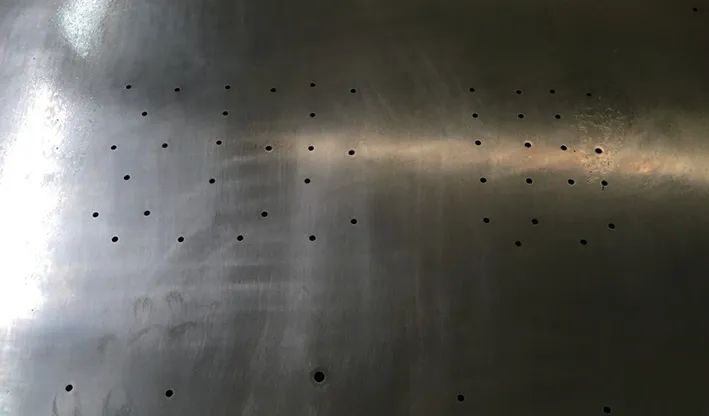
Fig. 18 depois de adicionar o orifício de ventilação ao punção
Conclusão
Ao otimizar e melhorar a aresta de corte, o núcleo de prensagem e a estrutura do punção, os parâmetros do processo atendem aos requisitos do processo de corte e minimizam a geração de escritas de ferro de corte, evitando assim o esmagamento de peças e moldes pelas escritas de ferro.
Nos últimos 8 meses de produção, a taxa de recuo diminuiu de 8,5% para 3,1% e permaneceu estável durante três meses consecutivos com uma clara melhoria.
Para solidificar as conquistas e buscar a melhoria contínua, tomamos duas ações:
Primeiramente, aplicamos os casos de sucesso à etapa de projeto estrutural de novos moldes para minimizar ao máximo o problema de aparas e quedas de escritas de ferro.
Em segundo lugar, estabelecemos diretrizes para a manutenção de matrizes de estampagem com inscrições de ferro caindo das bordas das matrizes, que são controladas através do sistema e processo para garantir a estabilidade das matrizes de estampagem durante a produção e operação e reduzir o número de produtos não qualificados causada por escritas de ferro.