Guia
O controle de qualidade do processo de corte é crucial na primeira etapa de produção das empresas. Como o corte por chama é o principal método de corte e blanking, garantir a qualidade da produção terá um grande impacto no processo geral de corte e blanking.
Este artigo enfoca os fatores que influenciam a qualidade do corte por chama e fornece soluções para problemas comuns de corte por meio de métodos de processo.
Apesar de sua importância como principal método de corte para pequenas, médias e grandes empresas, o corte por chama tem seus desafios.
Ao longo dos anos, o corte por chama evoluiu e os equipamentos de corte CNC tornaram-se avançados e sofisticados. Como resultado, vários métodos e técnicas de processo para melhorar a qualidade do corte por chama foram desenvolvidos.
Neste artigo, usamos o software de agrupamento automático XSuperNEST para examinar os fatores que afetam a qualidade das peças cortadas por meio de corte a chama e formas de melhorar seu rendimento.
Fatores que influenciam o equipamento de corte
Atualmente, o mercado oferece uma variedade de métodos e equipamentos de corte, como corte a laser, plasma e água, que oferecem melhor qualidade de corte e eficiência de produção do que o corte por chama. Apesar disso, o corte à chama continua popular devido ao seu menor custo e ainda é amplamente utilizado como método de corte primário.
As máquinas de corte por chama CNC estão sendo cada vez mais utilizadas no processo de produção de corte. Essas máquinas oferecem a vantagem da programação sem interferência, mas esse recurso também impossibilita que os trabalhadores compensem a deformação térmica durante o processo de corte, levando a desvios na precisão dimensional.
Além disso, alguns fatores relacionados à própria máquina de corte CNC também podem impactar a qualidade do corte.
Fatores que afetam a qualidade do corte
(1) Seleção de gás de corte
A escolha do gás de corte tem um impacto significativo na qualidade dos cortes das máquinas de corte por chama. Atualmente, os gases disponíveis são acetileno, propileno, propano e MPS. Cada gás possui características de combustão únicas, levando a diferentes cenários de corte, e a escolha do gás apropriado pode maximizar os benefícios do corte a gás, levando a um corte eficiente e econômico.
A chama de acetileno é caracterizada por seu calor concentrado, alta temperatura, curto tempo de pré-aquecimento, baixo consumo de oxigênio, alta eficiência de corte e mínima deformação dos componentes. Isto o torna adequado para cortar chapas finas e peças curtas.
Por outro lado, a chama do propano possui calor disperso, baixa temperatura e maior tempo de pré-aquecimento em comparação ao acetileno. Também resulta em uma borda superior lisa e plana do corte e menos escória na borda inferior, que é mais fácil de remover. Além disso, seu custo relativamente baixo o torna uma opção econômica para o corte de grandes peças de chapas grossas.
A chama do propileno tem temperatura mais alta e tempo de pré-aquecimento mais curto em comparação ao propano, ligeiramente superior ao do acetileno. Seu alto teor de calor na chama externa o torna adequado para cortar grandes peças de chapas grossas.
(2) Concentração de oxigênio, velocidade e seleção da altura do bico de corte
Além da seleção apropriada do gás, a pressão do oxigênio de corte, a velocidade e o ajuste da altura do bico também são fatores cruciais que afetam a qualidade do corte com chama.
Observou-se que o aumento da concentração de oxigênio diminui o tempo de corte e reduz a demanda de oxigênio, com a mesma pressão de oxigênio.
A escolha da velocidade de corte é especialmente importante. Se a velocidade for muito alta, poderá causar defeitos de qualidade, como “flameout”, corte áspero e redução da eficiência de corte. Por outro lado, se a velocidade for muito lenta, pode resultar na adesão da escória de oxidação e na superfície de corte irregular.
Com base na experiência prática, a melhor velocidade de corte deve estar na faixa média-superior a média-superior da velocidade nominal do bico de corte. Por exemplo, ao usar um bico nº 5 para cortar uma placa de aço de 40 mm, a faixa de velocidade nominal é de 250 ~ 380 mm/min, com uma velocidade média de 315 mm/min. Ao dividir a faixa em 10 níveis, a melhor velocidade fica entre 336,6 ~ 358 mm/min, sendo 340 mm/min a escolha ideal.
A escolha da altura do bico de corte também afeta a qualidade do corte. Se o centro da chama estiver muito baixo, poderá entrar em contato com a superfície da peça, causando o colapso do corte, respingos de escória bloqueando o bico ou até mesmo revenido. Por outro lado, se a altura for muito elevada, a chama não consegue aquecer totalmente o corte, reduzindo a capacidade de corte e dificultando a remoção da escória. Geralmente é recomendado manter uma distância de 3 a 5 mm entre o centro da chama e a superfície de trabalho para obter melhores resultados.
(3) Ordem de corte e aplicação de chumbo
Uma ordem de corte razoável promove o aquecimento uniforme da chapa de aço e compensa as tensões internas, reduzindo a deformação térmica das peças.
Ao cortar o contorno das peças, recomenda-se seguir o princípio de primeiro dentro e depois fora, primeiro pequeno e depois grande, primeiro redondo e depois quadrado, salto cruzado, primeiro complicado e depois simples, para evitar deslocamento, deformação e desvio de tamanho das peças.
Uma posição e forma apropriadas do avanço podem manter a integridade do entalhe da peça e melhorar a estabilidade do corte, garantindo a qualidade do contorno.
Na produção prática, a posição de introdução do contorno externo está normalmente localizada no lado direito da parte inferior do contorno, e a forma do contorno interno é melhor representada por um arco circular.
Processo otimizado
Mesmo após perfeita configuração e depuração dos parâmetros do equipamento de corte por chama, não há garantia de que as peças serão cortadas sem defeitos. O formato da peça, a espessura da placa, a posição do material de agrupamento e o método de corte podem afetar a qualidade do corte.
Por exemplo, placas cortadas à chama podem ser divididas em placas finas (espessura <20 mm), placas de espessura média e placas grossas.
Placas finas são fáceis de perfurar durante o processo de corte, mas são propensas à deformação térmica. Para reduzir a deformação térmica e o arqueamento das peças, recomenda-se cortar de dentro da chapa de aço em vez de na posição da borda. Isto ajuda a manter a integridade da estrutura externa da chapa de aço.
Usar o processo de “corte contínuo” pode reduzir o número de perfurações, enquanto o processo de “corte permanente” pode efetivamente reduzir a deformação térmica.
Para chapas grossas e médias, a deformação térmica é mínima durante o processo de corte, mas as perfurações podem causar escória e danos ao bico de corte. Para reduzir as perfurações, recomenda-se utilizar o pré-aquecimento das bordas antes de iniciar o corte. A Figura 1 mostra o método convencional de corte com pré-aquecimento de borda.
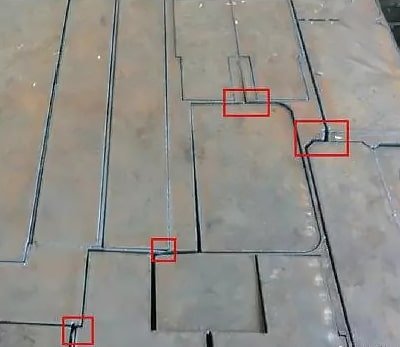
Figura 1 Método convencional de corte de chumbo com pré-aquecimento de borda
(1) Redução da perfuração de pré-aquecimento usando o processo de “perfuração I”
O método convencional de corte com chumbo de pré-aquecimento de borda pode resolver efetivamente o problema de perfuração do corte de chapas grossas e médias, mas requer muito ajuste humano na descarga e requer pessoal de assentamento de alta qualidade e precisão da máquina de corte.
Para resolver esse problema, o software XSuperNEST oferece um novo “processo de perfuração em I” para otimizar o caminho de corte e perfuração.
O método de corte com chumbo de pré-aquecimento da borda de perfuração I encontra automaticamente um local adequado para cortar um furo circular inferior com base no contorno externo da peça cortada e usa o furo circular para introduzir a próxima peça para pré-aquecimento, reduzindo as perfurações.
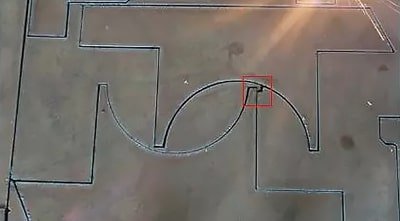
Figura 2 I Método de corte de chumbo com pré-aquecimento de borda perfurada
(2) Usando o processo de “corte contínuo” para melhorar a eficiência de corte
Para melhorar a utilização do material, as peças pequenas são frequentemente aninhadas dentro do contorno interno de peças maiores, e o caminho de corte geralmente envolve cortar primeiro a peça do contorno interno, depois pular para cortar a próxima peça do contorno interno e, finalmente, cortar os dois contornos internos separadamente. Isto resulta numa baixa eficiência de corte, uma vez que a máquina de corte tem de levantar a pistola várias vezes e perfurar o furo várias vezes.
Para resolver esse problema, o caminho de corte pode ser otimizado usando o processo de “corte contínuo” para reduzir o processo de perfuração e esvaziamento. A Figura 3 mostra a sequência de corte otimizada após usar o processo de “corte contínuo”.
Na Figura 3, cada parte dentro do contorno interno é cortada em uma fileira, seguida pelo corte do contorno interno em uma fileira. Isto permite cortar as peças dentro do contorno interno e do contorno interno com apenas uma perfuração, melhorando significativamente a eficiência do corte.
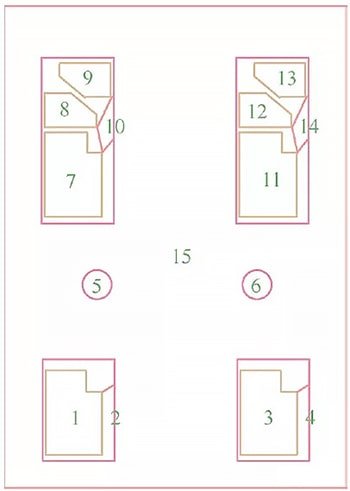
Figura 3 Sequência de corte após otimização do processo de “corte contínuo”
(3) Usando o processo “stay cut” para reduzir a deformação térmica das peças
No processo de corte do contorno interno de uma peça, pode haver uma incompatibilidade entre o tamanho real e o tamanho teórico entre os contornos interno e externo.
Por exemplo, conforme mostrado na Figura 4, as dimensões teóricas marcadas para uma peça com espessura de 50 mm são 610 mm, mas as dimensões reais após o corte são 3 a 5 mm menores.
Isto se deve ao acúmulo de calor ao cortar o contorno interno, que aumenta ainda mais ao cortar o contorno externo. Como não há suporte no contorno interno durante o corte do contorno externo, o contorno externo é extrudado para dentro pelo calor, causando deformação da peça.
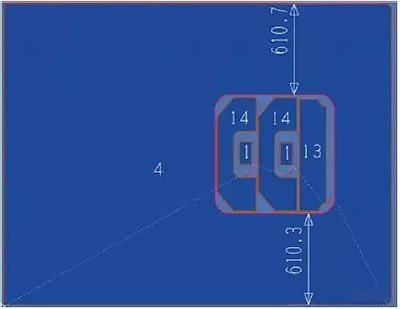
Figura 4 Diagrama de agrupamento de peças
Nesta situação, adicionar um processo “stay cut” pode ser uma solução.
Conforme mostrado na Figura 5, o “corte fixo” é adicionado ao redor do contorno interno para manter o contorno da moldura do contorno interno e fornecer suporte para a peça.
Este método reduz efetivamente os erros de corte e melhora a precisão do corte, mas a desvantagem é que o contorno interno requer polimento.
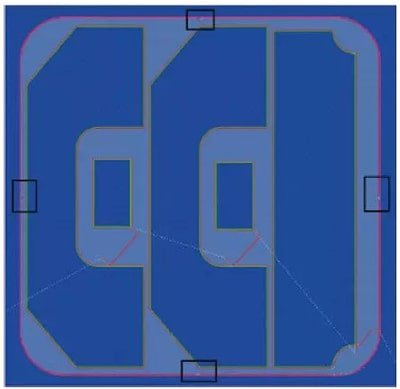
Figura 5 Caminho de corte após otimização do processo “stay cut”
(4) O uso da introdução de arco para reduzir a queima excessiva do furo redondo interno
O método de introdução tradicional envolve cortar o contorno da peça usando uma linha reta ao longo da borda reta do contorno e, em seguida, ao longo da borda reta da introdução. Isto não afeta a qualidade do corte desde que o início da introdução da peça seja reto.
No entanto, ao cortar o furo circular interno, o método de introdução tradicional leva à falta de transição suave ao cortar diretamente no contorno, resultando em queima excessiva do contorno e afetando a qualidade do corte, conforme mostrado na Figura 6.
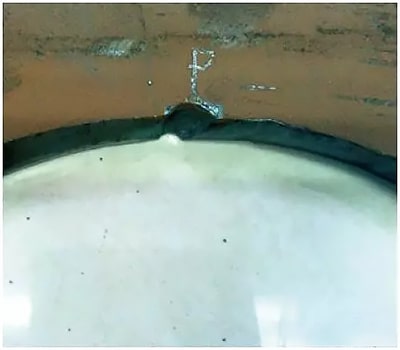
Figura 6 Queima excessiva do furo redondo interno
Durante o processo de pesquisa, o XSuperNEST introduziu o método de introdução de arco para evitar a queima excessiva do arco e melhorar a qualidade do corte do furo circular interno da peça.
O método de corte por introdução de arco, mostrado na Figura 7, usa um arco tangente ao furo circular interno para criar uma transição suave, deixando uma lacuna com o ponto inicial de introdução e conectando-se suavemente com um arco circular.
Este método foi verificado e confirmado como eficaz através da produção real, conforme mostrado na Figura 8.
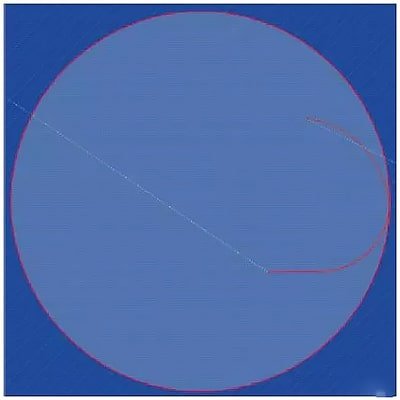
Figura 7 Arco circular conduzindo ao corte
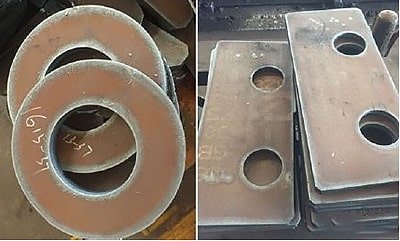
Figura 8 Usando arcos circulares para conduzir peças cortadas
Conclusão
A moldagem, como etapa inicial da produção, é crítica para o sucesso de uma empresa. O corte por chama, sendo o principal método de corte, tem impacto direto na qualidade e produtividade da produção.
Portanto, é imperativo controlar efetivamente a qualidade do corte por chama.
Existem vários fatores que afetam a qualidade do corte, incluindo o próprio equipamento, a escolha do gás, a velocidade de corte, a altura do bico, a sequência de corte e muito mais.
Ao usar os parâmetros apropriados com base nas condições reais de produção, a qualidade do corte pode ser melhorada e a taxa de peças qualificadas pode ser aumentada.
Além disso, ao otimizar o caminho de corte através do uso do processo de corte apropriado com base na espessura, formato do contorno e outras características das peças, o erro de produção das peças pode ser reduzido, a eficiência e a qualidade do corte das peças podem ser melhoradas, e, em última análise, a eficiência da produção da empresa pode ser aumentada.