A seleção dos parâmetros do processo de corte para máquinas de corte a plasma CNC é crucial para a qualidade, velocidade e eficiência dos resultados de corte.
Para usar corretamente uma máquina a plasma CNC para um corte rápido e de alta qualidade, é essencial ter um profundo conhecimento e domínio dos parâmetros do processo de corte.
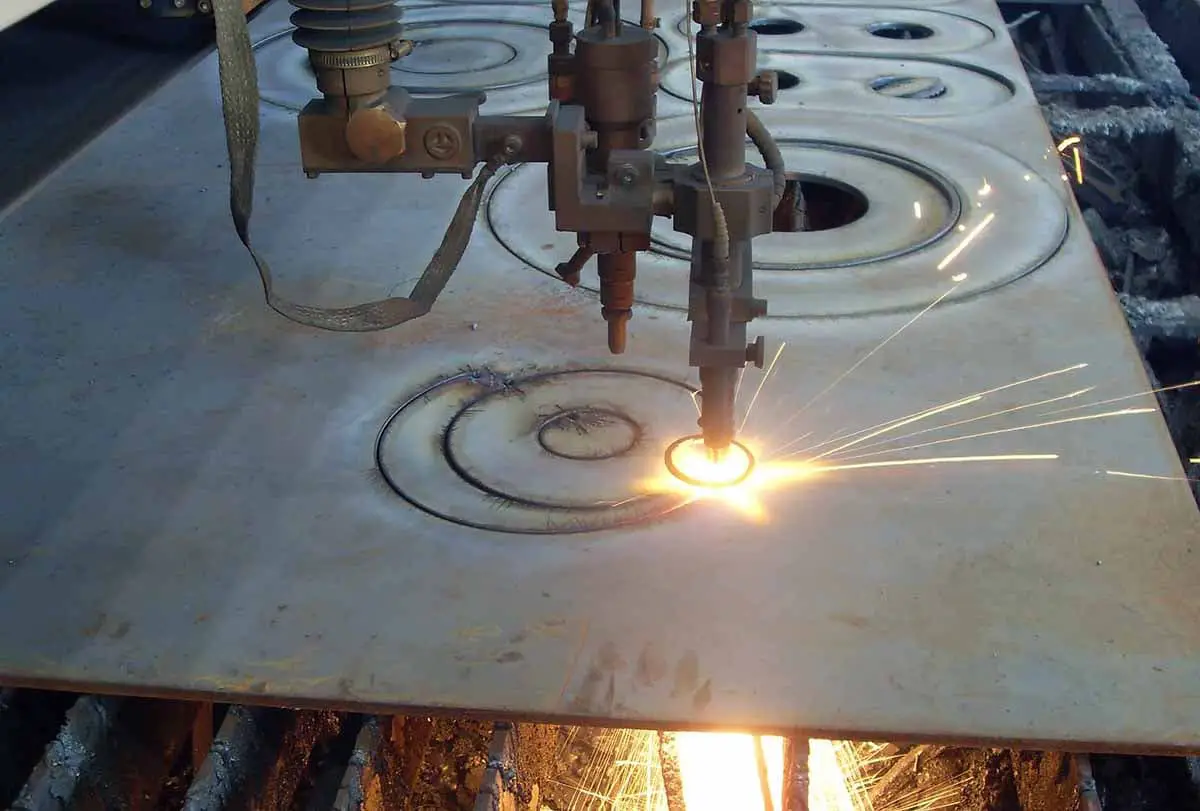
I. Corte de corrente
É o parâmetro mais importante do processo de corte que determina diretamente a espessura e a velocidade do corte, ou seja, a capacidade de corte. Seus efeitos são os seguintes:
1. À medida que a corrente de corte aumenta, a energia do arco também aumenta, resultando em maior capacidade de corte e maior velocidade de corte.
2. À medida que a corrente de corte aumenta, o diâmetro do arco também aumenta, tornando o corte mais largo.
3. Se a corrente de corte for muito alta, o bico superaquecerá, causando danos prematuros e diminuição da qualidade do corte, ou até mesmo impedindo a ocorrência do corte normal. Portanto, é necessário escolher a corrente de corte adequada e o bico correspondente com base na espessura do material antes do corte.
II. Velocidade de corte
A faixa ideal de velocidade de corte pode ser determinada de acordo com as instruções do equipamento ou por experimentação.
Devido a fatores como espessura do material, tipo de material, ponto de fusão, condutividade térmica e tensão superficial após a fusão, a velocidade de corte também muda de acordo. Seus principais efeitos são os seguintes:
Aumentar moderadamente a velocidade de corte pode melhorar a qualidade do corte, ou seja, estreitar ligeiramente o corte, tornar a superfície de corte mais lisa e reduzir a deformação.
Se a velocidade de corte for muito rápida, a energia da linha de corte será menor do que o valor necessário, e o jato não poderá soprar o derretimento de corte derretido imediatamente, resultando em uma maior quantidade de arrasto e escória pendurada no corte, causando uma diminuição na qualidade da superfície de corte.
Quando a velocidade de corte é muito baixa, como a posição de corte é o ânodo do arco plasma, para manter a estabilidade do próprio arco, o ponto anódico ou área anódica deve encontrar um local para conduzir a corrente próximo ao corte mais próximo, o que transferirá mais calor radialmente para o jato.
Portanto, o corte fica mais largo e o material fundido em ambos os lados do corte se acumula e solidifica na borda inferior, formando escória de difícil limpeza. Além disso, a borda superior do corte forma um canto arredondado devido ao aquecimento e derretimento excessivos.
Quando a velocidade é extremamente baixa, o arco pode até extinguir-se. Assim, boa qualidade de corte e velocidade de corte são inseparáveis.
III. Tensão do arco
A tensão normal de saída da fonte de alimentação é geralmente considerada como a tensão de corte.
As máquinas de corte por arco de plasma geralmente têm alta tensão sem carga e tensão de trabalho.
Ao usar gases com alta energia de ionização, como nitrogênio, hidrogênio ou ar, a tensão necessária para um arco plasma estável é maior. Quando a corrente é constante, um aumento na tensão significa um aumento na entalpia do arco e na capacidade de corte.
Se o diâmetro do jato for reduzido enquanto aumenta a taxa de fluxo de gás ao mesmo tempo que aumenta a entalpia, isso geralmente resulta em velocidade de corte mais rápida e melhor qualidade de corte.
4. Gás de trabalho e taxa de fluxo
Os gases de trabalho incluem gás de corte, gás auxiliar e alguns equipamentos também requerem gás de partida. Normalmente, o gás de trabalho apropriado deve ser selecionado com base no tipo, espessura e método de corte do material.
O gás de corte precisa garantir a formação do jato de plasma enquanto remove o metal fundido e os óxidos do corte.
O fluxo excessivo de gás pode retirar mais calor do arco, encurtar o comprimento do jato, levar a uma diminuição na capacidade de corte e ao arco instável; fluxo de gás insuficiente pode fazer com que o arco de plasma perca a retilineidade necessária, resultando em cortes superficiais e também causando facilmente suspensão de escória.
Portanto, a taxa de fluxo do gás deve ser bem coordenada com a corrente e a velocidade de corte.
A maioria das modernas máquinas de corte a arco de plasma controlam a vazão pela pressão do gás porque quando a abertura da pistola é fixa, o controle da pressão do gás também controla a vazão.
A pressão do gás utilizada para cortar uma determinada espessura de material geralmente precisa ser selecionada de acordo com os dados fornecidos pelo fabricante do equipamento.
Se houver outras aplicações especiais, a pressão do gás deverá ser determinada através de testes de corte reais.
Os gases de trabalho mais comumente usados são argônio, nitrogênio, oxigênio, ar e H35, gás misto argônio-nitrogênio, etc.
1. O gás argônio quase não reage com nenhum metal em altas temperaturas, e o arco de plasma do gás argônio é muito estável.
Além disso, o bico e o eletrodo utilizados têm uma vida útil relativamente longa. No entanto, a tensão do arco plasma de argônio é mais baixa e o valor de entalpia não é alto, resultando em capacidade de corte limitada.
Comparado com o corte a ar, a espessura do corte diminuirá aproximadamente 25%.
Além disso, num ambiente protector de árgon, a tensão superficial do metal fundido é maior, cerca de 30% mais elevada do que num ambiente de azoto.
Portanto, pode haver mais problemas de suspensão de escória.
Mesmo ao cortar com uma mistura de argônio e outros gases, haverá uma tendência à formação de escória pegajosa. Assim, o gás argônio puro raramente é usado sozinho para corte a plasma.
2. O gás hidrogênio é geralmente usado como gás auxiliar misturado com outros gases.
Por exemplo, o conhecido gás H35 (fração volumétrica de hidrogênio de 35%, o restante é argônio) é um dos gases mais fortes na capacidade de corte por arco de plasma, que se deve principalmente ao gás hidrogênio.
Como o gás hidrogênio pode aumentar significativamente a tensão do arco, fazendo com que o jato de plasma de hidrogênio tenha um alto valor de entalpia. Quando misturado com gás argônio, a capacidade de corte do jato de plasma é bastante melhorada.
Geralmente, para materiais metálicos com espessura superior a 70 mm, argônio + hidrogênio é comumente usado como gás de corte. Se usar jato de água para comprimir ainda mais o arco de plasma de argônio + hidrogênio, uma eficiência de corte ainda maior pode ser alcançada.
3. O nitrogênio é um gás de trabalho comumente usado.
Sob condições de alta tensão de alimentação, o arco de plasma de nitrogênio tem melhor estabilidade e maior energia de jato do que o gás argônio.
Mesmo ao cortar materiais com alta viscosidade, como aço inoxidável e ligas à base de níquel, a quantidade de escória pendurada sob a incisão também é muito pequena. O nitrogênio pode ser usado sozinho ou misturado com outros gases.
No corte automatizado, o nitrogênio ou o ar são frequentemente usados como gás de trabalho, e esses dois gases se tornaram gases padrão para corte em alta velocidade de aço carbono. Às vezes, o nitrogênio também é usado como gás inicial do arco no corte a plasma com oxigênio.
4. O oxigênio pode aumentar a velocidade de corte de materiais de aço de baixo carbono.
Ao usar oxigênio para corte, o modo de corte é semelhante ao corte com chama. O arco plasma de alta temperatura e alta energia torna a velocidade de corte mais rápida, mas deve ser usado em conjunto com eletrodos resistentes à oxidação em alta temperatura.
Ao mesmo tempo, o eletrodo deve ser protegido contra impactos durante a iniciação do arco para prolongar sua vida útil.
5. O ar contém cerca de 78% de fração volumétrica de nitrogênio, portanto a situação de suspensão de escória formada pelo uso de ar para corte é semelhante àquela ao usar nitrogênio para corte.
O ar também contém cerca de 21% de fração volumétrica de oxigênio e, devido à presença de oxigênio, a velocidade de corte de material de aço de baixo carbono usando ar também é alta. Ao mesmo tempo, o ar é também o gás de trabalho mais económico.
No entanto, quando o ar é usado apenas para corte, há problemas com suspensão de escória, bem como aumento de oxidação e nitrogênio na incisão. A baixa vida útil dos eletrodos e bicos também pode afetar a eficiência do trabalho e reduzir custos.
V. Altura do bico
refere-se à distância entre a face final do bico e a superfície de corte, que constitui uma parte de todo o comprimento do arco. Como o corte por arco de plasma geralmente utiliza corrente constante ou fontes de energia com características de queda acentuada, a corrente muda muito pouco depois que a altura do bico aumenta.
No entanto, aumentará o comprimento do arco e fará com que a tensão do arco aumente, aumentando assim a potência do arco. Mas, ao mesmo tempo, também aumentará a perda de energia da coluna de arco exposta ao meio ambiente.
Sob o efeito combinado destes dois fatores, o efeito do primeiro é muitas vezes completamente compensado pelo último, o que pode reduzir a energia de corte efetiva e diminuir a capacidade de corte.
Isso geralmente se manifesta como enfraquecimento da força do jato de corte, aumento da escória residual na parte inferior da incisão e arredondamento da borda superior.
Além disso, considerando o formato do jato de plasma, o diâmetro do jato se expande para fora após sair da pistola, e o aumento na altura do bico causará inevitavelmente um aumento na largura da incisão.
Portanto, escolher a menor altura possível do bico é benéfico para melhorar a velocidade e a qualidade do corte.
No entanto, quando a altura do bico é muito baixa, podem ocorrer arcos duplos. O uso de bicos externos de cerâmica pode definir a altura do bico para zero, ou seja, a face final do bico entra em contato direto com a superfície de corte, o que pode alcançar bons resultados.
VI. Reduzindo a densidade de potência
A fim de obter um arco de plasma de alta compressão para corte, o bico de corte utiliza uma pequena abertura do bico, um comprimento de furo mais longo e um efeito de resfriamento reforçado. Isto pode aumentar a corrente que passa pela área efetiva da seção transversal do bico, ou seja, aumentar a densidade de potência do arco.
No entanto, a compressão também aumenta a perda de potência do arco, de modo que a energia real utilizada para o corte é menor que a potência de saída da fonte de energia e sua taxa de perda é geralmente entre 25% e 50%.
Alguns métodos, como o corte a plasma por compressão de água, podem ter uma taxa de perda de energia mais alta. Esta questão deve ser considerada na concepção dos parâmetros do processo de corte ou na contabilização económica dos custos de corte.
Por exemplo, a espessura da placa metálica comumente usada na indústria é geralmente inferior a 50 mm.
Dentro desta faixa de espessura, o corte convencional por arco de plasma geralmente forma um corte com uma borda superior maior e uma borda inferior menor, e a borda superior do corte pode causar uma diminuição na precisão do tamanho da incisão e aumentar o trabalho de processamento subsequente.
Ao usar o corte a arco plasma de oxigênio e nitrogênio de aço carbono, alumínio e aço inoxidável, quando a espessura da placa está na faixa de 10-25 mm, o material é mais espesso, a verticalidade da borda é melhor e o erro de ângulo da aresta de corte é de 1 grau a 4 graus.
Quando a espessura da placa é inferior a 1 mm, à medida que a espessura da placa diminui, o erro angular da incisão aumenta de 3-4 graus para 15-25 graus.
Geralmente, acredita-se que a causa desse fenômeno se deva à entrada irregular de calor do jato de plasma na superfície de corte, ou seja, a liberação de energia do arco de plasma na parte superior da incisão é maior do que na parte inferior.
Este desequilíbrio na liberação de energia está intimamente relacionado a muitos parâmetros do processo, como o grau de compressão do arco plasma, velocidade de corte e distância do bico à peça.
Aumentar o grau de compressão do arco pode estender o jato de plasma de alta temperatura para formar uma área de alta temperatura mais uniforme e, ao mesmo tempo, aumentar a velocidade do jato, o que pode reduzir a diferença de largura das bordas superior e inferior do a incisão.
Porém, a compressão excessiva dos bicos convencionais muitas vezes provoca arcos duplos, que não só consomem eletrodos e bicos, impossibilitando a continuidade do processo de corte, mas também levam à diminuição da qualidade da incisão.
Além disso, a velocidade de corte excessiva e a altura do bico também podem aumentar a diferença de largura entre as bordas superior e inferior da incisão.
VII. Tabela de parâmetros do processo de corte a plasma
Plasma de ar de aço de baixo carbono/corrente de corte de proteção de ar 130A
Selecione o gás | Definir fluxo de ar de corte | Espessura do material | Tensão do arco | Distância da tocha de corte à peça de trabalho | Velocidade de corte | Altura inicial da perfuração | Atraso de perfuração | |||
Plasma | Gás protetor | Plasma | Gás protetor. | milímetros | Tensão | milímetros | mm/min | milímetros | Coeficiente % |
Segundo |
Ar | Ar | 72 | 35 | 3 | 136 | 3.1 | 6.000 | 6.2 | 200 | 0,1 |
4 | 137 | 3.1 | 4930 | 6.2 | 200 | 0,2 | ||||
6 | 138 | 3.6 | 3850 | 7.2 | 200 | 0,3 | ||||
10 | 142 | 4.1 | 2450 | 8.2 | 200 | 0,5 | ||||
12 | 144 | 4.1 | 2050 | 8.2 | 200 | 0,5 | ||||
15 | 150 | 4.6 | 1450 | 9.2 | 200 | 0,8 | ||||
20 | 153 | 4.6 | 810 | 10,5 | 230 | 1.2 | ||||
25 | 163 | 4.6 | 410 | Comece pela borda | ||||||
32 | 170 | 5.1 | 250 |
Plasma de oxigênio de aço de baixo carbono/corrente de corte de proteção de ar 130A.
Selecione o gás | Definir fluxo de ar de corte | Espessura do material | Tensão do arco | Distância da tocha de corte à peça de trabalho | Velocidade de corte | Altura inicial da perfuração | Atraso de perfuração | |||
Plasma | Gás protetor | Plasma | Gás protetor | milímetros | Tensão | milímetros | mm/min | milímetros | Coeficiente% | Segundo |
Oxigênio | Ar | 65 | 48 | 3 | 128 | 2,5 | 6500 | 5,0 | 200 | 0,1 |
4 | 129 | 2.8 | 5420 | 5.6 | 200 | 0,2 | ||||
6 | 130 | 2.8 | 4000 | 5.6 | 200 | 0,3 | ||||
10 | 134 | 3,0 | 2650 | 6,0 | 200 | 0,3 | ||||
12 | 136 | 3,0 | 2200 | 6,0 | 200 | 0,5 | ||||
15 | 141 | 3.8 | 1650 | 7.6 | 200 | 0,7 | ||||
43 | 20 | 142 | 3.8 | 1130 | 7.6 | 200 | 1,0 | |||
25 | 152 | 4,0 | 675 | 8,0 | 200 | 1,5 | ||||
32 | 155 | 4,5 | 480 | Comece pela borda | ||||||
38 | 160 | 4,5 | 305 |