Programação
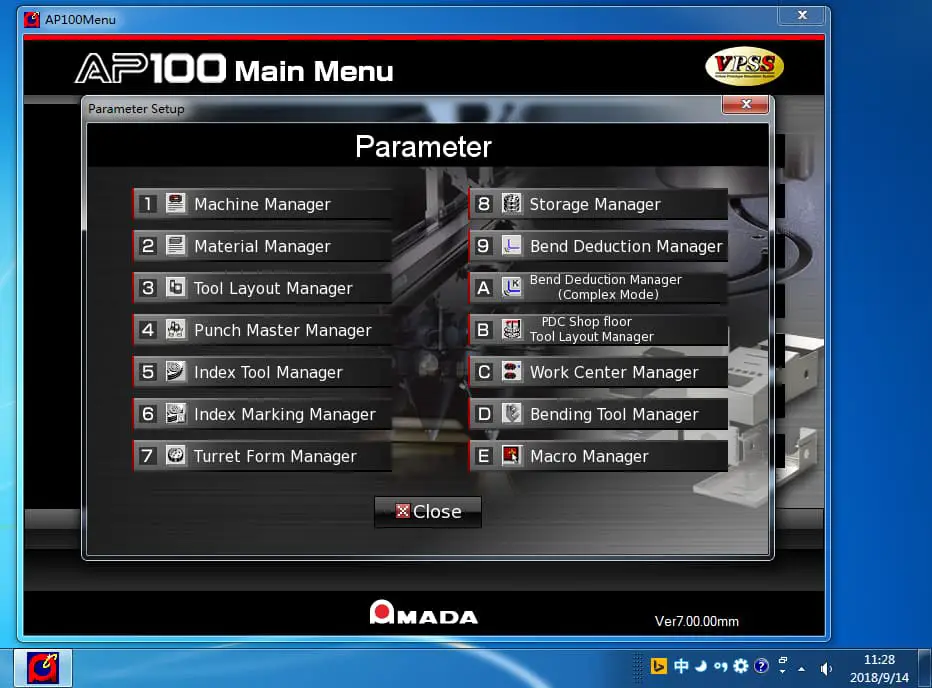
1. Familiarização com formatos de matrizes comuns e especializados:
Conhecer as matrizes disponíveis torna a programação mais conveniente e eficiente.
2. Aplicação racional de folgas na matriz:
Anteriormente, as folgas padrão eram 0,1 vezes a espessura da placa para alumínio e cobre, 0,15 vezes para ferro e 0,2 vezes para aço inoxidável. Agora, a AMADA propõe um novo padrão de folga de matrizes para puncionadeiras hidráulicas (todas as três prensas de nossa fábrica são hidráulicas).
A folga da matriz pode ser aumentada adequadamente em 0,05 vezes a espessura da placa com base no padrão original.
Isso ocorre porque as puncionadeiras hidráulicas têm uma velocidade de corte instantânea mais lenta e o aumento da folga da matriz não afetará a aparência da seção cortada, ao mesmo tempo que evita que o material salte durante o processo de corte.
3. Quantidade de corte e vinco:
Durante o processo de layout de corte, é essencial calcular a quantidade de corte de cada golpe da matriz. Geralmente, o comprimento do material cortado pela matriz não deve ser inferior a 2/3 do comprimento da matriz; caso contrário, pode haver restos.
As formas retangulares são propensas a restos, principalmente nos quatro ângulos retos, enquanto as formas circulares são as menos propensas a ter restos. Portanto, é fundamental prestar atenção à sequência de puncionamento durante o processo de layout de corte.

No exemplo acima, a Figura 1 mostra que perfurar primeiro a forma circular e depois a forma quadrada pode facilmente causar rachaduras nos quatro cantos da forma quadrada. Se a sequência de puncionamento for alterada para a da Figura 2, o desgaste da matriz será muito menor.
Durante o processo de layout de corte, é imprescindível utilizar a borda mais longa da matriz para o corte das bordas, conforme exemplo a seguir:
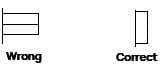
4. Cálculo de comprimento em programação:
(1) No corte em linha verdadeira:
Ao cortar arestas continuamente, o programa interno da própria máquina calculará esta aresta dividindo o comprimento total da aresta cortada menos o comprimento do primeiro corte, em vez do comprimento total dividido pelo comprimento da lâmina como podemos imaginar.
É essencial observar que quando a puncionadeira corta bordas continuamente, ela não conecta com precisão cada corte ao seguinte. Em vez disso, a puncionadeira assume automaticamente como padrão uma sobreposição de 0,2 mm entre os dois cortes. Devemos prestar atenção a isso ao calcular.
Por exemplo, ao cortar uma borda de 240 mm com uma lâmina retangular RE80x5, podemos pensar que são necessários exatamente três cortes.
No entanto, se utilizar o corte em linha verdadeira, na realidade serão feitos quatro cortes, o que afeta significativamente o desgaste da matriz e a vida útil.
Existem duas soluções para isso: primeiro, podemos usar uma abordagem de lâmina única, cortando uma de cada vez; segundo, com base na situação real, podemos deixar um nó de 0,4 mm no primeiro corte.
(2) Mordiscar:
Nem todas as matrizes redondas ou quadradas podem ser usadas para mordiscar. Em nossa fábrica, usamos matrizes redondas φ10, φ11, φ12 e matrizes quadradas RE6x3 para mordiscar. É melhor não usar outras matrizes para mordiscar, principalmente as menores. O corte é adequado apenas para chapas finas, pois causa desgaste rápido nas matrizes quando usado em chapas grossas.
Ao usar um molde redondo para cortar um círculo, primeiro perfure o centro com um molde redondo maior e depois prossiga com o corte. Não deixe nenhum nó. Ao mordiscar com uma matriz quadrada, é melhor deixar três nós menores e uniformemente espaçados ao longo da circunferência.
5. Saindo dos nós
Durante o processo de programação, os nós não devem ser deixados muito grandes ou muito pequenos; além disso, não devem ser deixados a mais ou a menos. Se os nós forem muito grandes, o produto será difícil de remover ou ficará deformado após a remoção. Se os nós forem muito pequenos, o produto poderá cair.
Qual é o tamanho mais apropriado para nós?
Não existe um padrão definido; depende da situação real. O tamanho ideal do nó é aquele em que o produto não cai durante o processo de puncionamento e se desprende do material devido ao seu peso quando o operador puxa a chapa da mesa de trabalho.
Aqui estão alguns valores de referência para sua consideração:
Metais | <1.0 | 1.0-1.6 | 1.6-2.5 | 2,5-3,0 | ||||
---|---|---|---|---|---|---|---|---|
Nós de canto | Nós intermediários | Nós de canto | Nós intermediários | Nós de canto | Nós intermediários | Nós de canto | Nós intermediários | |
Alumínio, Cobre | 0,35 | 0,4 | 0,4 | 0,5 | 0,5 | 0,5 | 0,5 | 0,6 |
Ferro | 0,3 | 0,4 | 0,4 | 0,4 | 0,4 | 0,5 | 0,4 | 0,5 |
Aço inoxidável | 0,3 | 0,35 | 0,3 | 0,35 | 0,4 | 0,4 | 0,4 | 0,4 |
Os valores acima são alguns valores de referência para deixar nós em espessuras de placas comuns, mas os valores reais dependem da situação específica. Quanto a quantos nós são apropriados, geralmente devemos deixar um nó entre cada 350-400 mm. Por exemplo, se houver um diagrama retangular desdobrado de 50x1200mm, podemos dividi-lo em três seções e deixar dois nós no meio. Tente deixar nós simetricamente no produto para manter o estresse equilibrado.
Nota: Durante o processo de composição, os nós devem ser adicionados adequadamente em determinados pontos.
Composição
Coloque diferentes produtos do mesmo material e espessura de placa em uma única folha para processamento único para obter economia de material, tempo e esforço.
- Familiarize-se com as especificações do material:
- Placa de alumínio: t(espessura) * 1220*2440
- Placa de cobre: t(espessura) * 600*1500
- Placa fria (SPC): t(espessura) * 1250*2500 (t(espessura) * 1220*2440)
- Placa decapada (SPHC/SPHD): t(espessura) * 1250*2500 (t(espessura) * 1220*2440)
- Placa eletrolítica: t(espessura) * 1220*2440
- Placa de aço inoxidável: t (espessura) * 1220 * 2440
Estas são algumas especificações comuns de materiais em folha. Especificações personalizadas podem ser solicitadas com base nos requisitos de tamanho do produto desdobrado.
- Zona de Segurança: Preste atenção à zona de segurança durante a composição. Geralmente, a aresta de corte da estação D é definida para 1580, e a aresta de corte da estação E está definida para 20110. Não inclua a matriz dentro da zona de segurança para evitar danificar a matriz e a braçadeira.
- Distância entre layouts: Durante a composição, a distância mínima entre os produtos não deve ser inferior à largura da matriz. Por exemplo, usando RE45*5 para corte, a distância mínima não deve ser inferior a 5 mm.
- Composição de borda compartilhada: O AP100 possui comando automático de borda compartilhada, mas também pode ser feito manualmente. Ao compor com bordas compartilhadas, certifique-se de aumentar o tamanho dos nós ou deixar mais.
- Seleção de matrizes na composição tipográfica: Use o mínimo de matrizes possível na composição tipográfica. Na sequência de puncionamento, a última matriz de corte deve ser puncionada do lado oposto do grampo em direção ao grampo.
- Perfuração de matriz de formação especial: Para matrizes de conformação como flangeamento, semi-desenho, veneziana e prensagem de ponte, preste atenção especial à sequência de puncionamento. Se estiver formando para baixo, deixe nós maiores e coloque a matriz de conformação por último na sequência, puncionando do grampo em direção ao outro lado ao longo da direção X e saindo para fora. Se for formar para cima, certifique-se de que as matrizes subsequentes não pressionem a posição de formação, para que não seja necessário colocá-las por último na sequência.
Problemas comuns na composição de programação
Existem vários problemas comuns na composição tipográfica de programação:
- Gravação:
a) Material em si: Para materiais macios e leves, como placas de alumínio, a gravação em relevo pode ocorrer facilmente durante o processo de puncionamento. Devido ao peso leve da placa de alumínio, os resíduos de corte em si são muito leves na mesma velocidade de puncionamento e, quando os resíduos ainda não caíram completamente, são levantados pela matriz superior e a gofragem ocorre quando os resíduos são prensados na placa durante o próximo corte.
b) Velocidade de puncionamento: Durante o processo de corte, se a velocidade for muito rápida e os resíduos ainda não tiverem caído completamente, a matriz superior levanta os resíduos e a gofragem ocorre quando os resíduos são pressionados na placa durante o próximo corte.
c) Quantidade de corte insuficiente: Durante o processo de puncionamento, se a quantidade de corte for inferior a 2/3, a matriz pode levantar os resíduos.
- Arrastar material:
a) Profundidade insuficiente da matriz superior: Se o material não for completamente perfurado, a matriz superior provavelmente arrastará o material ao ser levantada.
b) Folga excessiva da matriz: Se a folga inferior da matriz for muito pequena, é fácil prender o material e a placa provavelmente arrastará o material durante o movimento.
c) Aresta de corte da matriz não afiada: Se o material não for completamente perfurado, a matriz superior provavelmente arrastará o material ao ser levantada.
d) Velocidade de puncionamento da prensa: Se a velocidade for muito rápida e o material não for completamente cortado ou derrubado, pode fazer com que o material seja arrastado.
e) Força de ejeção insuficiente: A pressão da mola não é suficiente.
f) Punção desalinhado, distribuição desigual de forças.
- Morre residual:
a) Quantidade de corte insuficiente: Quando for inferior a 2/3 do comprimento da matriz, pode ocorrer matriz residual.
b) Durante a erosão, se o passo for muito pequeno, é provável que ocorra uma morte residual grave. Ajuste o tom adequadamente de acordo com os requisitos reais.
- Produto caindo:
a) Os nós são muito pequenos, poucos ou não estão posicionados de maneira razoável.
- Deslocamento de meio desenho e arranhões:
Quando a placa se move, o meio desenho fica arranhado no disco da faca. Quando o meio desenho se move no disco da faca, ele fica preso na matriz inferior. Quando a placa se move, o meio desenho é arrastado à força, causando deslocamento do material e fazendo com que outros meios desenhos sejam deslocados.
Para evitar esses problemas, considere os fatores que os causam e leve em consideração a programação e a operação no local para resolver os problemas com mais rapidez e precisão.