Cortar placas de aço abaixo de 10 mm não é um problema com um cortador a laser. No entanto, para placas mais espessas, muitas vezes é necessário um laser de alta potência com potência superior a 5 kW. Isso resulta em uma diminuição significativa na qualidade do corte.
O alto custo do equipamento laser de alta potência torna o modo de saída de corte a laser menos favorável. Como resultado, os métodos tradicionais de corte a laser não apresentam vantagem no corte de chapas grossas.
Os desafios técnicos no corte de chapas grossas com uma máquina de corte a laser para metal são:
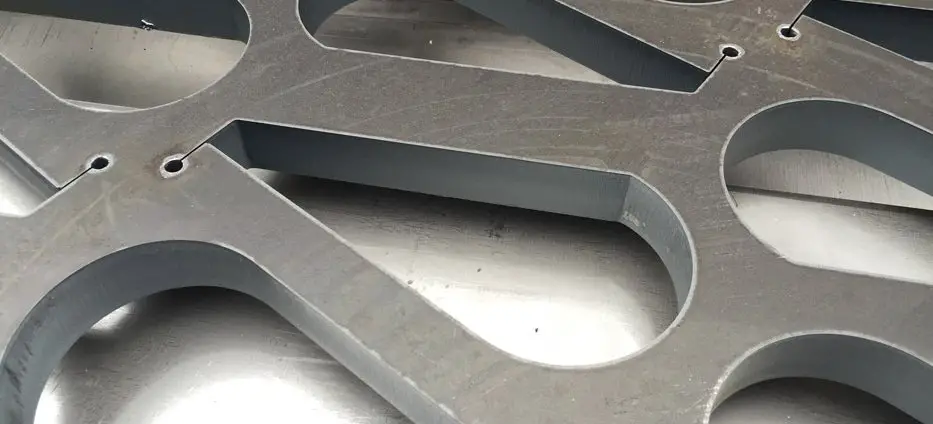
O processo de combustão no estado quase estacionário é difícil de manter.
O cortador a laser de metal tem limitações quanto à espessura das placas que podem ser cortadas durante o processo de corte real. Isto está ligado à instabilidade da combustão da lâmina de ferro.
A temperatura no topo da fenda deve atingir o ponto de ignição para manter o processo de combustão contínuo. A energia liberada pela reação de combustão do óxido de ferro por si só não garante a continuação do processo de combustão.
Por um lado, a temperatura da aresta de corte diminui pelo resfriamento constante do fluxo de oxigênio do bico de corte. Por outro lado, a camada de óxido de ferro formada após a combustão cobre a superfície da peça, bloqueando a difusão do oxigênio. Quando a concentração de oxigênio diminui a um certo nível, o processo de combustão será extinto.
No corte a laser por feixe convergente tradicional, o feixe de laser concentra-se em uma pequena área da superfície. A alta densidade de potência do laser faz com que a temperatura da superfície da peça atinja o ponto de ignição não apenas na área de radiação do laser, mas também em uma área mais ampla devido à condução de calor.
O diâmetro do fluxo de oxigênio na superfície da peça é maior que o diâmetro do feixe de laser, resultando em uma forte reação de combustão não apenas na área de radiação do laser, mas também fora dela.
Ao cortar chapas grossas, a velocidade de corte é lenta. A superfície da peça queima mais rápido do que a velocidade de movimento da cabeça de corte. Após algum tempo de queima, o processo de combustão se extingue devido à diminuição da concentração de oxigênio. Quando a cabeça de corte se move para essa posição, a reação de combustão recomeça.
O processo de queima da aresta de corte ocorre periodicamente, levando a oscilações de temperatura e má qualidade da incisão.
A pureza e a pressão do oxigênio na direção da espessura da placa são difíceis de manter constantemente.
A diminuição da pureza do oxigênio também desempenha um papel crucial na determinação da qualidade de corte de chapas grossas usando um cortador a laser. A pureza do fluxo de oxigênio tem um impacto significativo no processo de corte.
Uma diminuição na pureza do fluxo de oxigênio em 0,9% leva a uma diminuição de 10% na taxa de combustão ferro-oxigênio. Uma diminuição na pureza em 5% resulta em uma diminuição de 37% na taxa de combustão. Esta diminuição na taxa de combustão reduz grandemente a entrada de energia na costura cortada e diminui a velocidade de corte.
Além disso, o teor de ferro na camada líquida da superfície de corte aumenta, fazendo com que a viscosidade da escória aumente e dificultando a descarga da escória. Isto resulta num acúmulo significativo de escória na parte inferior da incisão, tornando a qualidade da incisão inaceitável.
Para manter a estabilidade do corte, a pureza do fluxo de oxigênio de corte na direção da espessura e da pressão da placa deve ser mantida constante.
No corte a laser tradicional, é usado um bico cônico convencional, adequado para cortar chapas finas. No entanto, ao cortar chapas grossas, uma onda de choque é formada no campo de fluxo do bico à medida que a pressão de alimentação aumenta. A onda de choque representa vários riscos ao processo de corte, como reduzir a pureza do fluxo de oxigênio e afetar a qualidade da incisão.
Existem três soluções para este problema:
(1) Adicionar uma chama de pré-aquecimento ao redor do fluxo de oxigênio de corte.
(2) Adicionar um fluxo auxiliar de oxigênio ao redor do fluxo de oxigênio de corte.
(3) Design razoável das paredes internas do bocal para melhorar o campo de fluxo de ar.