CO2 o corte a laser emprega uma lente de foco para direcionar os feixes de laser de CO2 para a superfície do material, fazendo com que ele derreta.
Simultaneamente, o material derretido é removido por um fluxo coaxial de gás comprimido, permitindo que os feixes de laser e o material se movam um em relação ao outro ao longo de um caminho definido, resultando em um formato de corte preciso.
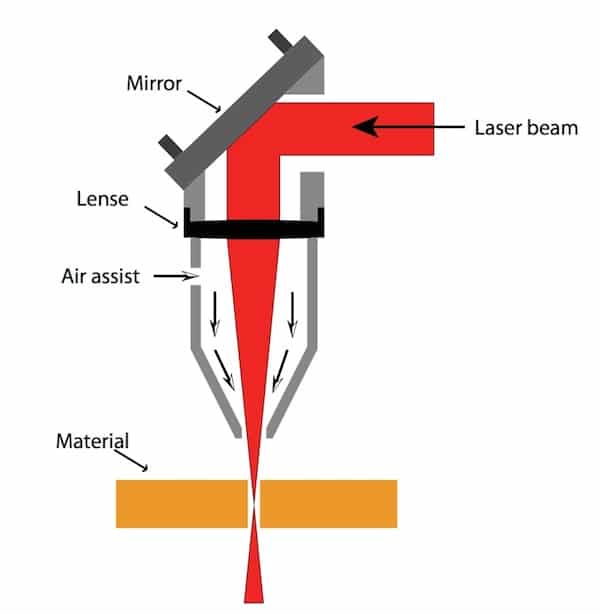
Desde a década de 1970, o desenvolvimento de lasers de CO2 e tecnologia de controle numérico tornou o corte a laser de CO2 um método altamente avançado para corte de chapas.
Nas décadas de 1950 e 1960, os métodos de corte de chapas incluíam:
- Corte com chama oxiacetileno para chapas de espessura média
- Corte e corte para chapas finas
- Estampagem para produção em massa de componentes complexos
- Corte vibratório para peças individuais
Na década de 1970, para melhorar a qualidade dos cortes com chama, o corte com chama de precisão com oxietano e o corte a plasma tornaram-se populares.
Para reduzir o tempo do ciclo de fabricação de moldes de estampagem em grande escala, foram promovidas a estampagem CNC e a tecnologia de eletroprocessamento.
Cada tipo de método de corte e corte tem suas próprias limitações e é usado em aplicações específicas de produção industrial.
Vantagens óbvias da tecnologia de corte a laser CO2 sobre outros métodos:
Boa qualidade de corte:
- Largura de incisão pequena (geralmente 0,1-0,5 mm)
- Alta precisão (o desvio geral do centro do furo é de 0,1 a 0,4 mm, enquanto o desvio do contorno é de 0,1 a 0,5 mm)
- Boa rugosidade superficial da incisão (geralmente Ra 12,5-25 mícrons)
- As vigas cortadas podem ser soldadas sem processamento adicional.
Alta velocidade de corte:
Por exemplo, um laser de 2KW com velocidade de corte de 1,6 m/min pode cortar aço carbono com 8 mm de espessura, enquanto uma velocidade de corte de 3,5 m/min pode ser alcançada em aço inoxidável com 2 mm de espessura. O processo de corte a laser resulta em uma pequena área de influência térmica e deformação mínima.
Limpo, seguro e não poluente:
O uso do corte a laser CO2 melhora significativamente o ambiente de trabalho dos operadores. Embora possa não superar o eletroprocessamento em termos de precisão e rugosidade superficial dos cortes, e possa ter limitações na espessura de corte em comparação com o corte por chama e plasma, suas vantagens levaram à substituição de técnicas de corte tradicionais, especialmente para corte de materiais não metálicos. materiais.
Na China, desde a década de 1990 e o desenvolvimento da economia de mercado socialista, tem havido intensa competição entre as empresas, fazendo com que cada empresa escolha cuidadosamente tecnologias de produção avançadas que atendam às suas necessidades específicas, a fim de melhorar a qualidade do produto e a eficiência da produção. Como resultado, a tecnologia de corte a laser CO2 teve um rápido crescimento na China.
Aplicação industrial de corte a laser CO2
O primeiro CO2 A máquina de corte a laser foi inventada na década de 1970. Nas últimas três décadas, a máquina passou por melhorias contínuas à medida que seus campos de aplicação se expandiam.
Atualmente, muitas empresas nacionais e internacionais produzem vários tipos de CO2 máquinas de corte a laser para atender à demanda do mercado, incluindo máquinas de corte de chapas 2-D, máquinas de corte de curva espacial 3-D e máquinas de corte de tubos.
Empresas estrangeiras proeminentes neste campo incluem Trumpf (Alemanha), Prima (Itália), Bystronic (Suíça), Amada e MAZAK (Japão), NTC (Japão) e HG Laser Lab (Austrália).
De acordo com o Relatório Anual de 2000 da “Industrial Laser Solution”, uma importante revista americana da indústria de laser, as vendas totais de sistemas de corte a laser em todo o mundo (principalmente CO2 sistemas de corte a laser) em 1999 eram 3.325, totalizando US$ 1,174 bilhão.
Na China, quase 100 CO2 máquinas de corte a laser são produzidas a cada ano, totalizando 150 milhões de RMB, mas seu uso no país é relativamente baixo em comparação com os países desenvolvidos. Em 2003, o número de CO2 os sistemas de corte a laser utilizados na produção industrial na China atingiram cerca de 500, representando aproximadamente 1,5% do total mundial.
Dois tipos principais de CO2 comprador de sistema de corte a laser
Existem dois tipos principais de organizações que utilizam CO2 tecnologia de corte a laser: grandes e médias empresas de manufatura e estações de processamento.
As grandes e médias empresas industriais possuem fortes recursos económicos e técnicos e necessitam de corte e corte para muitos dos seus materiais.
As estações de processamento, também conhecidas como Job Shops no exterior, são especializadas na prestação de serviços de processamento a laser a terceiros e não possuem produtos próprios dominantes. Estas estações podem satisfazer as necessidades das pequenas e médias empresas e também desempenhar um papel na promoção da adoção precoce da tecnologia de corte a laser.
Em 1999, havia 2.700 estações de processamento a laser nos Estados Unidos, sendo 51% delas especializadas em corte a laser.
Na década de 1980, as estações de processamento a laser na China concentravam-se principalmente no tratamento térmico a laser. No entanto, desde a década de 1990, o número de estações de corte e processamento a laser aumentou.
À medida que as reformas no sistema de grandes e médias empresas da China continuam e a força económica do país cresce, espera-se que cada vez mais empresas adoptem o CO2 tecnologia de corte a laser.
Internamente, CO2 o corte a laser é amplamente utilizado para cortar placas de aço de baixo carbono com espessura de 12 mm ou menos, placas de aço inoxidável com espessura de 6 mm ou menos e materiais não metálicos com espessura de 20 mm ou menos. Também tem sido utilizado nas indústrias automobilística e de aviação para cortar curvas espaciais tridimensionais.
Atualmente, os produtos adequados para corte a laser CO2 podem ser categorizados em três grupos:
- Peças de chapa metálica que não são economicamente ou tecnicamente viáveis de serem fabricadas através de outros métodos, especialmente aço de baixo carbono com formas complexas, tamanhos de lote pequenos e espessuras inferiores a 12 mm, e aço inoxidável com espessuras inferiores a 6 mm, a fim de economizar no custo e tempo de fabricação do molde. Exemplos de tais produtos incluem componentes de elevadores, painéis de elevadores, máquinas-ferramenta e carcaças de máquinas, gabinetes elétricos, gabinetes de distribuição, peças de máquinas têxteis, peças de máquinas de engenharia e grandes chapas de aço silício para motores.
- Aço inoxidável (geralmente com menos de 3 mm de espessura) ou materiais não metálicos (geralmente com menos de 20 mm de espessura) usados em indústrias de decoração, publicidade e serviços, como padrões em álbuns de fotos artísticas, logotipos de empresas, organizações, hotéis e lojas shoppings e fontes em chinês e inglês em locais públicos como estações e docas.
- Peças especiais que exigem corte preciso, como placas utilizadas nas indústrias de embalagens e impressão. Eles exigem o corte de ranhuras com largura de 0,7 a 0,8 mm em gabaritos de madeira com espessura de 20 mm, que são então usados para cortar uma variedade de caixas de embalagem impressas. O corte a laser CO2 também é usado em tubos de triagem de óleo para evitar a entrada de sedimentos nas bombas e no corte de vigas de tamanhos uniformes com larguras inferiores a 0,3 mm em tubos de liga de aço com espessuras de parede de 6 a 9 mm. O diâmetro da perfuração deve ser superior a 0,3 mm, o que é difícil de conseguir, tornando o corte a laser CO2 uma solução popular para muitas empresas.
Além das aplicações mencionadas acima, o corte a laser CO2 está sendo utilizado em um número crescente de indústrias. Por exemplo, sistemas de corte a laser 3D ou robôs industriais são usados para cortar curvas espaciais e software especializado foi desenvolvido para agilizar o processo desde o desenho até o corte das peças.
Os pesquisadores estão focados em melhorar a eficiência da produção através do desenvolvimento de sistemas de corte especializados, sistemas de transporte de materiais e sistemas de acionamento de motores lineares. As velocidades de corte já ultrapassaram os 100 m/min.
A fim de ampliar seu uso nas indústrias de máquinas de engenharia e construção naval, a espessura de corte do aço de baixo carbono foi aumentada para mais de 30 mm, e há um interesse crescente na tecnologia de corte de aço de baixo carbono com gás nitrogênio para melhorar a qualidade da incisão na placa.
Assim, ainda é muito importante que os técnicos de engenharia na China expandam o uso do corte a laser CO2 e resolvam alguns problemas técnicos em aplicações práticas.
Os parâmetros do feixe de laser e o desempenho e precisão da máquina e do sistema CNC têm impacto direto na eficiência e qualidade do corte a laser. Tecnologias-chave, como aquelas exigidas para peças com alta precisão de corte ou materiais mais espessos, devem ser dominadas e solucionadas.
As tecnologias devem ser dominadas
1. Tecnologia de controle de posição de foco
Um dos benefícios do corte a laser é a alta densidade de energia dos feixes, que geralmente é superior a 10W/cm2. A densidade de energia é inversamente proporcional a 4/πd^2, portanto o diâmetro do ponto focal é mantido o menor possível para produzir uma fenda estreita.
O diâmetro do ponto focal é diretamente proporcional à profundidade focal da lente, o que significa que quanto menor for a profundidade focal, menor será o diâmetro do ponto focal. No entanto, o corte pode causar respingos e se a lente estiver muito próxima da peça de trabalho, ela poderá ser facilmente danificada.
Portanto, o corte a laser CO2 de alta potência normalmente usa lentes com distância focal de 5″ a 7,5″ (127 a 190 mm). O diâmetro real do ponto focal está entre 0,1 e 0,4 mm.
A profundidade focal efetiva também depende do diâmetro da lente e do material que está sendo cortado. Por exemplo, ao cortar aço carbono com uma lente de 5″, a profundidade focal deve estar dentro de uma faixa de +2% da distância focal, ou cerca de 5mm, para obter uma qualidade de corte ideal.
Para garantir os melhores resultados de corte, o foco é fundamental e depende da espessura do material. Para materiais metálicos com menos de 6 mm, o foco deve estar na superfície. Para aço carbono com espessura superior a 6 mm, o foco deve estar acima da superfície. Para aço inoxidável com espessura superior a 6 mm, o foco deve estar abaixo da superfície, mas o tamanho exato deve ser determinado através de experimentação.
Três métodos simples para localizar a posição de foco na produção industrial:
Existem três métodos para determinar o foco da máquina de corte a laser CO2:
- Método de impressão: Neste método, a cabeça de corte é movida de cima para baixo e o feixe de laser é impresso em uma placa de plástico. O menor diâmetro do feixe indica o foco.
- Método de placa inclinada: Neste método, a placa de plástico é colocada em uma determinada inclinação em relação ao eixo vertical e movida horizontalmente. O menor feixe de laser indica a localização do foco.
- Método de faísca azul: Este método envolve remover o bico, soprar ar e atingir uma placa de aço inoxidável com um laser pulsado. A cabeça de corte é movida de cima para baixo até que uma faísca azul atinja o seu limite, o que indica a localização do foco.
Para máquinas de corte de trajetória luminosa voadora, a determinação do foco é mais complexa, pois o ângulo de divergência dos feixes de laser causa diferenças na distância entre a extremidade próxima e a extremidade distal, levando a diferenças no tamanho do feixe antes da focagem. Quanto maior o diâmetro do feixe incidente, menor será o ponto focal.
Para minimizar a variação no tamanho do ponto focal causada por alterações no tamanho do feixe antes da focagem, os fabricantes de sistemas de corte a laser oferecem alguns dispositivos especiais para os usuários escolherem:
- Tubo de luz paralelo: Este é um método comumente usado que envolve a adição de um tubo de luz paralelo na saída do feixe de laser de CO2 para expandir os feixes. Isso aumenta o diâmetro do feixe e diminui o ângulo de divergência, tornando os tamanhos das extremidades próxima e distante do feixe mais semelhantes antes da focagem.
- Lente móvel: Outra opção é adicionar uma lente móvel separada à cabeça de corte que seja independente do eixo Z e controle a distância do bico à superfície do material. Quando a bancada ou o eixo de luz se move, o feixe também se move simultaneamente da extremidade próxima até a extremidade mais distante do eixo F, garantindo que o diâmetro do ponto focal do feixe permaneça consistente em toda a área de processamento.
- Controle de pressão da água: Alguns sistemas controlam a pressão da água da lente de foco, que normalmente é um sistema de foco de reflexão de metal. Quando o tamanho do feixe de foco diminui e o diâmetro do ponto focal aumenta antes de focar, a pressão da água é ajustada automaticamente, alterando a curvatura focal e diminuindo o diâmetro do ponto focal.
- Compensação de trajetória óptica: Um sistema que adiciona compensação de trajetória óptica nas direções x e y da máquina de corte de trajetória de voo. Isto significa que o caminho de compensação óptica é encurtado quando a distância óptica na extremidade distal do corte aumenta, e aumentado quando a distância óptica na extremidade próxima do corte diminui, mantendo a distância do caminho óptico consistente.
2. Tecnologias de perfuração de corte
A tecnologia de corte a laser, exceto em alguns casos, normalmente requer a perfuração de um pequeno furo no material. No passado, as máquinas de estampagem a laser usavam primeiro um punção para fazer um furo e depois um laser para cortar o furo. Para máquinas de corte a laser sem estampagem, existem dois métodos básicos de perfuração:
- Perfuração com explosão: Após exposição contínua ao laser, forma-se um buraco no centro do material, que é rapidamente removido por um fluxo coaxial de oxigênio, formando um buraco. O diâmetro médio do furo é aproximadamente metade da espessura do material, portanto, para chapas mais espessas, a perfuração por jateamento cria furos não circulares com diâmetro maior, tornando-a inadequada para peças com requisitos elevados (como tubos de peneiramento de óleo), mas adequada para materiais residuais. A pressão do oxigênio usada na perfuração é a mesma do corte, o que causa muitos respingos.
- Perfuração de pulso: Lasers de pulso de potência máxima fazem com que alguns materiais derretam ou vaporizem, normalmente usando oxigênio ou nitrogênio como gás auxiliar para reduzir a expansão do furo causada pela oxidação exotérmica. A pressão do gás é inferior à pressão do oxigênio usada no corte, e cada pulso de laser produz apenas pequenas partículas que são ejetadas em profundidade, fazendo com que demore alguns segundos para perfurar placas mais espessas. Uma vez concluída a perfuração, o gás auxiliar é imediatamente substituído por oxigênio para corte. Isso resulta em um diâmetro de perfuração menor e melhor qualidade de perfuração em comparação com a perfuração com explosão.
Para perfuração por pulso, o laser utilizado não deve apenas ter alta potência de saída, mas também altas características de tempo e espaço dos feixes. O processo de perfuração por pulso também deve ter um sistema confiável de controle do caminho do gás para controlar o tipo de gás, a comutação da pressão do gás e o tempo de perfuração. A transição da perfuração pulsada para o corte contínuo do material também deve ser enfatizada para obter cortes de alta qualidade.
Na produção industrial, é mais prático alterar a potência média do laser, como alterar a largura do pulso, a frequência ou ambos simultaneamente. O terceiro método demonstrou ter o melhor efeito.
3. Projeto do bico e técnica de controle do fluxo de ar
Ao cortar aço com laser, o oxigênio e o feixe de laser são direcionados através de um bico para o material para formar um fluxo. Para que o corte seja eficaz, o fluxo de ar precisa ser grande e rápido para produzir oxidação e reação exotérmica suficientes no material cortado. Além disso, o fluxo de ar deve ter impulso suficiente para remover o material fundido. O design do bico e o controle do fluxo de ar, como a pressão e a posição do bico e da peça, são fatores cruciais que afetam a qualidade do corte.
Atualmente, os bicos utilizados no corte a laser têm design simples, consistindo em um cone com um pequeno orifício na parte superior. O projeto do bico geralmente é feito através de experimentos e métodos de derivação. No entanto, como o bico geralmente é feito de cobre e é pequeno e vulnerável, ele requer substituição frequente e normalmente não é considerado em cálculos e análises de mecânica dos fluidos.
Quando em uso, o gás com pressão Pn entra no bico e cria pressão no bico. O gás sai do bico e atinge a superfície da peça após uma certa distância, formando uma pressão de corte Pc. Finalmente, o gás se expande para formar a pressão atmosférica Pa. A pesquisa mostrou que à medida que Pn aumenta, a velocidade do fluxo de ar e Pc também aumentam.
A fórmula para calcular a velocidade do fluxo de ar é:
V = 8,2d ^ 2 (Pg + 1)
onde:
V = velocidade do fluxo de ar em L/min
d = diâmetro do bico em mm
Pg = pressão do bico (pressão superficial) em bar
Quando a pressão do bocal excede um determinado valor, o fluxo de ar pode passar de subsônico para supersônico e se tornar uma onda de choque oblíqua normal. O valor limite depende da relação entre a pressão do bocal (Pn) e a pressão atmosférica (Pa) e o grau de liberdade (n) das moléculas do gás. Por exemplo, quando n=5 para oxigênio e ar, o limite Pn é 1,89 bar.
Se a pressão do bocal for maior, ou seja, Pn/Pa > 4 bar, a onda de choque oblíqua normal do fluxo de ar pode se transformar em um choque normal, fazendo com que a pressão de corte (Pc) diminua, a velocidade do ar diminua e um vórtice formar-se na superfície da peça, o que enfraquece o efeito do fluxo de ar na remoção do material fundido e afeta a velocidade de corte.
Para evitar isso, a pressão do bocal de oxigênio é frequentemente mantida abaixo de 3 bar quando se utiliza um bocal com um cone e um pequeno orifício na parte superior.
Para aumentar a velocidade do corte a laser, um bocal convergente-divergente chamado bocal Laval foi projetado com base em princípios aerodinâmicos. Este bico aumenta a pressão sem causar ondas de choque normais. A estrutura do bico está representada na Figura 4 para facilitar a fabricação.
O centro de laser da Universidade de Hanover, na Alemanha, conduziu experimentos emparelhando um laser de CO2 de 500 W (com uma distância focal de 2,5) com um bico cônico e um bico Laval. Os resultados dos experimentos estão representados nas figuras, que mostram a relação entre a rugosidade superficial (Rz) e a velocidade de corte (Vc) para os bicos nº 2, nº 4 e nº 5 sob diferentes pressões de oxigênio.
Conforme mostrado nas figuras, quando a pressão (Pn) é de 400 Kpa (ou 4 bar), a velocidade de corte do bico furo nº 2 atinge apenas 2,75 m/min (para uma chapa de aço carbono com 2 mm de espessura). Porém, em Pn de 500 Kpa ou 600 Kpa, a velocidade de corte dos bicos Laval nº 4 e nº 5 atinge 3,5 m/min e 5,5 m/min, respectivamente.
É importante observar que a pressão de corte (Pc) depende da distância entre a peça e o bico. A onda de choque oblíqua é refletida repetidamente no limite do fluxo de ar, fazendo com que a pressão de corte flutue periodicamente.
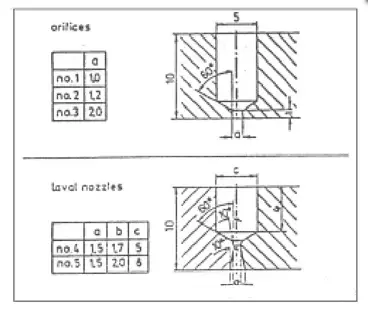
A primeira zona de alta pressão de corte está localizada próxima à saída do bico, sendo a distância entre a superfície da peça e a saída do bico de aproximadamente 0,5 a 1,5 mm. Isso resulta em pressão de corte (Pc) alta e estável, tornando-a um parâmetro amplamente utilizado na produção industrial.
A segunda zona de alta pressão de corte fica a aproximadamente 3 a 3,5 mm de distância da saída do bico e também apresenta alta pressão de corte, contribuindo para bons resultados de corte e proteção da lente, melhorando assim sua vida útil.
Entretanto, outras zonas de alta pressão de corte nas curvas estão muito distantes da saída do bico para se alinharem com o feixe focalizado.
Concluindo, a tecnologia de corte a laser CO2 está sendo cada vez mais utilizada na produção industrial da China. No exterior, esforços estão sendo feitos para estudar tecnologias e equipamentos de corte que possam atingir maiores velocidades de corte e manusear chapas de aço mais espessas.
Para atender às crescentes demandas por uma produção industrial de alta qualidade e aumento de eficiência, é importante focar na resolução de questões tecnológicas fundamentais e na implementação de padrões de qualidade, tornando esta nova tecnologia mais amplamente adotada em nosso país.