1. Principais causas de erro dimensional de peças causadas por corte a chama
As principais causas de erros no corte e blanking NC incluem deformação térmica da chapa de aço, técnica do operador, planicidade da plataforma de suporte, precisão do equipamento e grau de corrosão na superfície da chapa de aço.
2. Análise de erros dimensionais de peças produzidas por corte a chama e medidas direcionadas
O corte por chama de chapas de aço sempre envolve deformação a quente. No entanto, os erros dimensionais em peças de deformação a quente podem ser significativamente reduzidos. A velocidade de corte e a qualidade da peça são afetadas pelas habilidades do operador.
O nivelamento da plataforma de suporte e a precisão do equipamento têm maior impacto no tamanho das peças. Muitas vezes, imprecisões podem resultar no descarte direto de peças. Além disso, a corrosão da superfície da placa de aço pode afetar tanto a qualidade quanto a velocidade de corte.
2.1 Erro dimensional de peças causado por deformação térmica de chapa de aço
A deformação térmica em chapas de aço é perceptível principalmente em peças delgadas. Com base em anos de prática e análise de corte, foi determinado que os erros dimensionais em peças causados pela deformação térmica podem ser minimizados concentrando-se nos três aspectos a seguir:
2.1.1 Desenho de gráficos de peças
Ao criar gráficos para peças, certifique-se de incluir uma quantidade adequada de compensação de expansão térmica na direção do comprimento da peça. O valor da compensação deve ser selecionado com base nas características específicas de cada parte individual.
Vantagens: compensa diretamente o erro dimensional das peças causado pela dilatação térmica;
Desvantagens: só é aplicável a peças quadradas e outras formas não são fáceis de compensar.
2.1.2 Dprocesso de quitação detalhado
Começando pelo aspecto da descarga, refine o processo de descarga e formule um processo de descarga especial para peças voláteis.
2.1.2 vocêse de borda comum
A utilização de uma aresta comum pode diminuir o tempo de corte, minimizar a entrada de calor pela chapa de aço, diminuir a expansão da chapa de aço e consequentemente diminuir os erros dimensionais das peças.
Conforme ilustrado na Figura 1, quando uma aresta comum não é criada, AB e CD em dois lados adjacentes de duas peças precisam ser cortados separadamente.
Por outro lado, após utilizar uma aresta comum, apenas a aresta AB precisa ser cortada e a aresta CD não requer corte.
Isso não apenas reduz erros nas peças, mas também aumenta a eficiência de corte e a utilização da chapa.
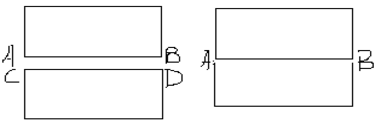
2.1.2 Rdireção de corte razoável
Determine a direção de corte razoável da peça de acordo com a situação real, primeiro corte o furo, depois corte a forma e primeiro corte a borda próxima à borda da placa de aço.
Tente garantir que deve haver rigidez de conexão suficiente entre a peça e a placa de aço antes que a peça seja cortada próximo ao ponto de conclusão, de modo a garantir o tamanho de corte e a precisão da peça.
Por exemplo, na Fig. 2, corte primeiro o furo interno (1-6) e depois corte o contorno externo na ordem A, B, C, D e A.
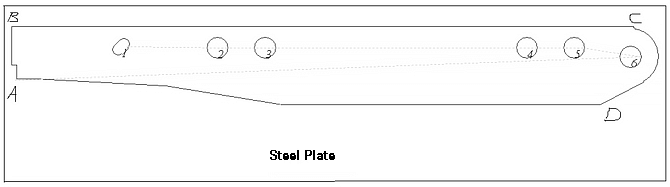
2.1.3 Rlayout de peça e caminho de corte fáceis
O erro causado pela deformação da placa de aço pode ser minimizado através do layout adequado das peças e do ajuste do caminho de corte.
Conforme ilustrado na Figura 3, as peças em forma de T que são suscetíveis à deformação devem ser combinadas com peças menores que têm menos probabilidade de deformar. Isto ajuda a reduzir o aquecimento excessivo em áreas localizadas, minimiza a deformação térmica e garante a precisão das dimensões da peça.
Para minimizar a deformação em peças delgadas, o corte por deslocamento deve ser utilizado ao descarregá-las.
Conforme mostrado na Figura 4, após o corte da parte 2, a segunda coluna deve ser usada para cortar a parte 3. Depois que a parte 2 esfriar por um certo tempo, ela deve ser virada para cortar a parte 4.
Devem ser feitos esforços para evitar o aquecimento localizado excessivo da chapa de aço, minimizar a deformação térmica e garantir ao máximo a precisão das dimensões da peça.
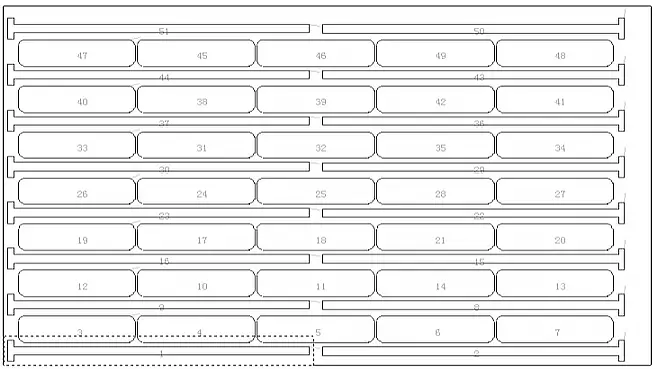

2.1.2 Sintervalo de configuração
Para reduzir o erro causado pela deformação da chapa de aço (conforme mostrado na Fig. 5), recomenda-se definir intervalos. Observe que as seções A, B, C e D não devem ser cortadas temporariamente, mas sim durante a limpeza da plataforma.
Vantagens: reduz direta e eficazmente a deformação da peça;
Desvantagens: a configuração do intervalo aumenta o número de perfurações de corte, aumenta o tempo de corte e aumenta o consumo do bico de corte.
Cortar a lacuna (conforme mostrado na Fig. 6) pode resultar em cicatrizes deixadas pelo pessoal de limpeza da plataforma.
Serão necessários reparos subsequentes, soldagem e retificação.
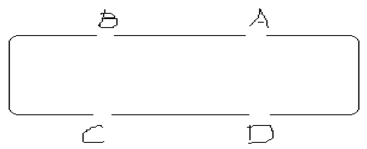
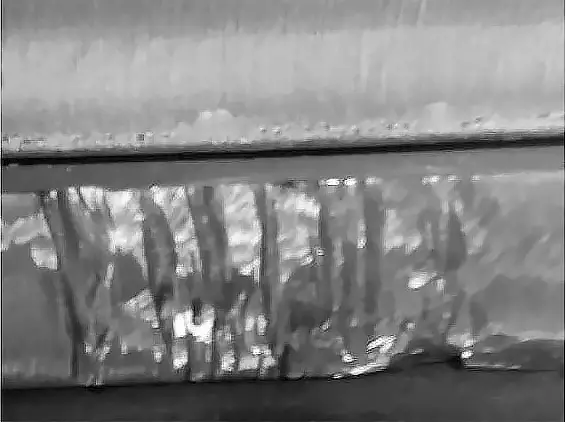
De acordo com diferentes situações, a escolha e utilização de métodos adequados ou uma combinação de vários métodos para controlar a deformação da chapa de aço pode desempenhar um papel óbvio.
2.2. Erro dimensional de peças causado pela tecnologia do operador NC
Em teoria, ao utilizar o mesmo equipamento e programa NC, as peças a serem cortadas deveriam ser idênticas. Contudo, na realidade, nem sempre é esse o caso.
Mesmo com o procedimento correto, peças cortadas por diferentes operadores podem apresentar variações de tamanho e erros, e algumas podem até precisar ser sucateadas.
Para garantir que as peças sejam cortadas corretamente, o bico de corte adequado deve ser escolhido com base na espessura da chapa de aço. A chama deve ser ajustada adequadamente e a compensação de fenda correspondente deve ser definida para garantir que as peças sejam de alta qualidade.
Para referência, consulte a tabela abaixo, que fornece os parâmetros do processo de corte a gás.
Parâmetros do processo de corte |
|||||||
Número do bico de corte |
Corte o diâmetro do furo de oxigênio/mm |
Espessura de corte /milímetros |
Velocidade de corte mm/min |
Tempo de pré-aquecimento/s |
Pressão de oxigênio Mpa |
Pressão do gás Mpa |
Valor de compensação de fenda /mm |
1 |
1,0 |
5-10 |
700-500 |
5-12 |
0,6-0,7 |
>0,03 |
2 |
2 |
1.2 |
10-20 |
600-380 |
15-25 |
0,6-0,7 |
>0,03 |
2,5 |
3 |
1.4 |
20-40 |
500-350 |
25-30 |
0,6~0,7 |
>0,03 |
3 |
4 |
1.6 |
40~60 |
420-300 |
35-50 |
0,6-0,7 |
>0,03 |
3.5 |
5 |
1,8 |
60-100 |
320-200 |
50-80 |
0,6-0,7 |
>0,03 |
3.5 |
6 |
2,0 |
100-150 |
260~140 |
80-120 |
0,7-0,8 |
>0,04 |
3.5 |
Nota: a pureza do oxigênio está acima de 99,5%.
2.3. Erro dimensional de peças causado pela plataforma de suporte
A principal razão para erros dimensionais em peças causados pela plataforma de suporte é devido ao plano da plataforma de suporte não ser paralelo à superfície do trilho-guia da máquina de corte NC.
A plataforma de trabalho da placa de aço de suporte é frequentemente impactada e batida na plataforma de carga e descarga, fazendo com que seu plano se torne irregular e não paralelo à superfície do trilho-guia da máquina de corte NC.
Se o desnível for significativo, pode fazer com que a tocha de corte da máquina de corte fique não perpendicular à chapa de aço, resultando na inclinação da direção da espessura de toda a peça.
Devido ao corte a chama de longo prazo, a placa de inserção da plataforma de suporte pode sofrer danos de corte e adesão de escória, levando ao desnível local da plataforma de suporte.
Durante o processo de corte da peça, a peça pode ficar parcialmente suspensa, resultando em inclinação parcial da direção da espessura da peça.
Quando a espessura da placa de aço é relativamente grande, o tamanho da peça apresentará um erro significativo.
2.4. Erro dimensional de peças causado pela precisão do equipamento
A precisão do trilho guia do equipamento tem impacto direto na precisão das peças cortadas. Para minimizar erros causados pela precisão do trilho-guia, é essencial manter e verificar regularmente o paralelismo e o nivelamento do trilho-guia.
Proteger os parâmetros do equipamento é crucial. Quaisquer alterações feitas nos parâmetros verticais e horizontais do equipamento podem resultar no sucateamento de um número significativo de peças.
Os operadores devem realizar uma autoinspeção completa das peças, especialmente as grandes, e relatar imediatamente quaisquer problemas encontrados. Esta abordagem ajudará efetivamente na identificação de tais questões.
3. Conclusão
Vários métodos podem ser combinados para reduzir efetivamente os erros e melhorar a qualidade do produto com base nas causas dos erros em diferentes peças.