O laser é criado misturando hélio de alta pureza, CO2 e nitrogênio de alta pureza na unidade de mistura de gás. O gerador de laser gera o laser e um gás de corte, como N2 ou O2, é adicionado para processar o objeto. A energia do laser é altamente concentrada e pode derreter e gaseificar instantaneamente o material.
Este método resolve efetivamente as dificuldades de processamento de materiais duros, quebradiços e refratários, oferecendo alta velocidade, precisão e deformação mínima. É ideal para processar peças de precisão e microcomponentes.
Vários fatores podem afetar a qualidade do corte a laser, incluindo velocidade de corte, posição do foco, pressão do gás auxiliar, potência de saída do laser e outros parâmetros do processo. Outros fatores, como caminho da luz externa, características da peça (refletividade e estado da superfície do material), tocha de corte, bico e fixação da placa também podem afetar a qualidade do corte.
Esses fatores são particularmente significativos no processamento de chapas de aço inoxidável, resultando em problemas como grandes nódulos e rebarbas no verso da peça, baixa circularidade quando o diâmetro do furo é 1-1,5 vezes a espessura da placa e linhas retas que são não direto nos cantos. Esses problemas continuam a desafiar a indústria de chapas metálicas no processamento a laser.
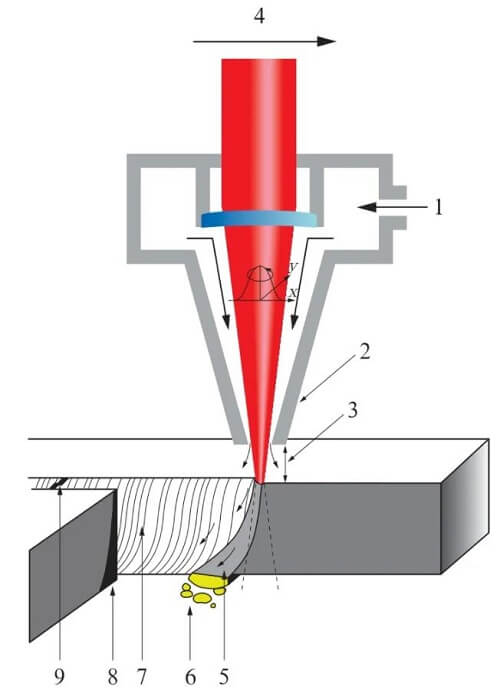
Figura 1 Princípio de fusão do corte a laser
- Gás Auxiliar
- Bocal
- Altura do bico
- Velocidade de corte
- Derretido
- Escória
- Rugosidade de corte
- Zona afetada pelo calor
- Largura da fenda
Problema de acúmulo de tumor
Realizamos testes repetidos e descobrimos que o suporte de corte equipado com a máquina de corte a laser não é adequado para o processamento de chapas metálicas.
Os principais motivos são:
(1) Se o ângulo R for grande, haverá uma grande área de contato entre o topo do suporte e a placa processada, levando a uma maior probabilidade de reflexão por respingo se o feixe de laser for cortado apenas no topo do suporte. Por outro lado, se o ângulo R for pequeno, a probabilidade de reflexão por respingo será baixa ao processar chapas finas.
(2) Se a distância for pequena e a inclinação for baixa, o espaço disponível para o feixe de laser penetrar ainda mais será limitado. Quanto menor o espaço de reflexão, maior a força de reflexão, fazendo com que o tumor cortante adira mais firmemente ao lado oposto da placa.
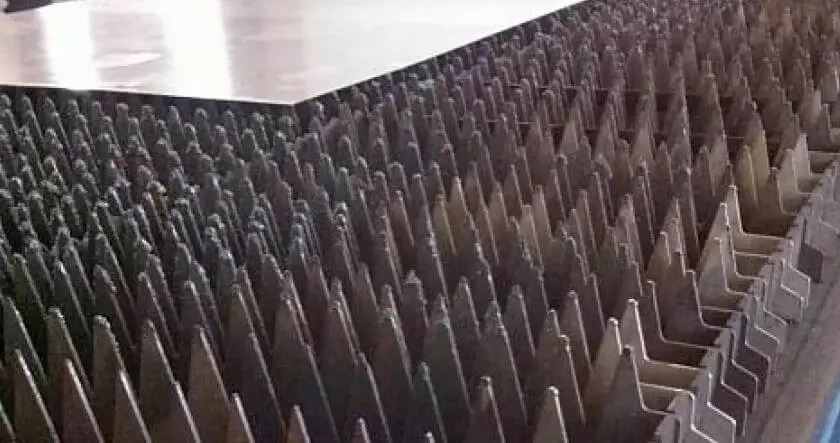
Fig. 2 Suporte aprimorado
Com base nas considerações acima, melhoramos o suporte de corte equipado com a máquina:
(1) Reduzir o ângulo R e aumentar a distância do topo do suporte à superfície de base, bem como aumentar a inclinação. Isto reduz significativamente os respingos e o tumor no verso da peça de trabalho, permitindo que o tumor caia facilmente com um toque suave de uma ferramenta.
(2) Durante o processo de corte, descobriu-se que a aplicação de óleo na superfície da placa reduz a aderência dos respingos de corte. O óleo forma uma película protetora na superfície da placa, dificultando a adesão do respingo à placa.
Além disso, a película de óleo é mais eficaz na orientação do feixe de laser, especialmente na usinagem de placas com superfícies extremamente lisas, como aço inoxidável espelhado. Isso ocorre porque o filme de óleo é mais fácil de absorver o feixe de laser em comparação com uma superfície lisa da placa, o que facilita a penetração e o posicionamento do feixe.
Portanto, começamos a revestir uniformemente a parte frontal e traseira da placa com óleo para laminação de metal, que possui um alto ponto de ignição. Isto levou a uma redução significativa de respingos e acúmulo de tumor na peça processada, especialmente no verso, que é muito melhor do que antes.
(3) Após repetidos ajustes na posição do foco nos parâmetros de corte, os técnicos descobriram que a melhor posição do foco do laser para cortar a chapa é um pouco menor que 1/2 da espessura da chapa.
No entanto, com a deformação da placa ou pressão excessiva do ar de corte, a qualidade do corte torna-se instável quando a placa fina vibra ligeiramente ou é afetada localmente pela alta pressão do gás.
Mas, quando o foco é ajustado para cerca de 2/3 da espessura da placa (corrigindo o desvio de foco causado por deformação ou vibração), evita efetivamente a formação de rebarbas finas sob as mesmas condições de placa e pressão de ar.
Como resultado, a qualidade de corte da peça foi bastante melhorada.
Problema de redondeza de furo pequeno
Ao usar uma máquina de corte a laser, pode ser um desafio produzir furos de alta qualidade com cerca de 1 a 1,5 vezes a espessura da placa, especialmente para furos redondos.
O processo de corte a laser envolve perfuração, introdução e corte, o que requer alteração de parâmetros intermediários. Isso resulta em um atraso durante a transição, fazendo com que os furos redondos no produto acabado fiquem distorcidos.
Para superar esse problema, otimizamos o tempo de perfuração e introdução para melhor alinhamento com o processo de corte. Isso elimina a mudança perceptível nos parâmetros e resulta em um resultado de maior qualidade.
Problema de retidão de canto
No processamento a laser, vários parâmetros importantes (como fator de aceleração, aceleração, fator de desaceleração, desaceleração e tempo de residência de canto) desempenham um papel crucial no processamento de peças de chapa fina, que estão fora da faixa de ajuste convencional.
Durante o processo de usinagem de peças de chapa fina com formatos complexos, geralmente ocorrem cantos frequentes. O feixe de laser deve desacelerar em cada canto e depois acelerar novamente. Estes parâmetros determinam o tempo de pausa do feixe laser em cada ponto.
(1) Se o valor de aceleração for muito alto e o valor de desaceleração for muito baixo, o feixe de laser pode não penetrar bem na placa nos cantos, resultando em baixa permeação e aumento na taxa de refugo.
(2) Se o valor de aceleração for muito baixo e o valor de desaceleração for muito alto, o feixe de laser penetrará na placa nos cantos, mas o valor de aceleração baixo faz com que o feixe de laser permaneça no ponto de troca de aceleração e desaceleração por muito tempo , fazendo com que a placa derreta e vaporize continuamente sob a influência do feixe de laser contínuo, levando a uma linha não reta nos cantos. (Outros fatores convencionais que afetam a qualidade do corte, como potência do laser, pressão do gás e fixação da peça, não são considerados aqui).
(3) Ao processar peças de chapa fina, é recomendado reduzir o poder de corte tanto quanto possível sem comprometer a qualidade do corte, para que não haja diferença de cor óbvia ou queimadura na superfície da peça de trabalho.
(4) A pressão do gás de corte deve ser minimizada, o que pode reduzir bastante os micro tremores locais da placa sob forte pressão de ar.
Com base na análise acima, quais valores devem ser definidos para aceleração e desaceleração adequadas? Existe uma relação proporcional entre os dois que deve ser seguida?
Para determinar os valores ideais, os técnicos ajustam continuamente a aceleração e desaceleração, marcam cada peça cortada e registram os parâmetros de ajuste. Através de repetidas comparações de amostras e exame cuidadoso das mudanças nos parâmetros, descobriu-se que ao cortar aço inoxidável na faixa de 0,5 a 1,5 mm, o valor de aceleração apropriado está entre 0,7 a 1,4g, e o valor de desaceleração está entre 0,3 a 0,3 a 1,4g. 0,6g. Existe uma regra geral de que o valor da aceleração é aproximadamente duas vezes o valor da desaceleração.
Esta regra também se aplica a chapas laminadas a frio com espessura semelhante, mas para chapas de alumínio com espessura semelhante os valores devem ser ajustados de acordo.
Conclusão
Ao abordar com sucesso os fatores que afetam a qualidade do corte, a qualidade dos produtos de chapa de aço inoxidável processados por nós melhorou significativamente em termos de redução de tumores de corte e melhoria da sutileza do corte.
Como trabalhadores técnicos modernos, é importante assumir o compromisso com a aprendizagem, ter a coragem de explorar novas soluções e aderir ao princípio da “excelência na produção”. Esta abordagem garante a produção de produtos de alta qualidade e o sucesso numa intensa competição económica.