Nos últimos anos, temos visto uma proeminência crescente das máquinas de corte a laser no crescimento da indústria de chapas metálicas. O processo de corte envolve seis funções práticas que, quando utilizadas, podem aumentar significativamente a eficiência do processamento e o desempenho de corte da máquina de corte a laser.
1. Salto
Leapfrog é um termo usado no corte a laser para descrever o movimento da cabeça de corte entre os cortes. Neste processo, após cortar o furo 1, a cabeça de corte se move do ponto A ao ponto B para cortar o furo 2. Durante esse movimento, o laser é desligado e a máquina funciona sem realmente cortar, o que é conhecido como funcionamento ocioso.
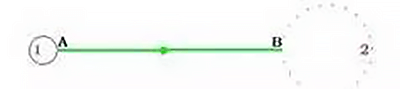
Os primeiros cortadores a laser tinham um processo específico de operação ociosa, conforme ilustrado abaixo. A cabeça de corte executou três ações sequenciais durante o funcionamento em marcha lenta: subiu até uma altura segura, nivelou-se para chegar acima do ponto B e depois desceu.
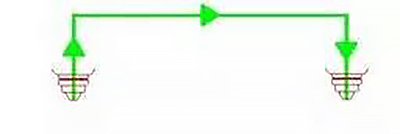
Reduzir o tempo ocioso pode aumentar a eficiência da máquina. Para conseguir isso, as três ações de marcha lenta (subir, nivelar e descer) podem ser executadas simultaneamente. Durante o movimento do ponto A ao ponto B, a cabeça de corte sobe e se aproxima do ponto B e, ao mesmo tempo, desce. Essa execução simultânea de ações reduz o tempo ocioso, conforme mostra a figura abaixo.
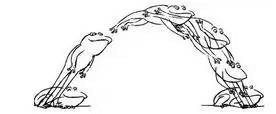
O movimento ocioso da cabeça de corte é semelhante a um arco desenhado por um sapo saltando. Isto é considerado um avanço técnico notável no desenvolvimento de máquinas de corte a laser. A ação de salto do sapo leva apenas o tempo do movimento plano do ponto A ao ponto B, eliminando o tempo de subida e descida. Assim como um sapo salta para capturar seu alimento, a função de “captura” para a função de salto do sapo em máquinas de corte a laser é de alta eficiência. Atualmente, as máquinas de corte a laser sem a função de salto de sapo não são mais consideradas convencionais.
2. Auto-foco
Ao cortar vários materiais, é crucial que o foco do feixe de laser caia em diferentes seções da seção transversal da peça de trabalho. Para conseguir isso, a posição do ponto focal deve ser ajustada, o que é conhecido como ajuste de foco.
Anteriormente, as máquinas de corte a laser eram focadas principalmente manualmente. Porém, hoje, muitos fabricantes oferecem máquinas com foco automático.
Algumas pessoas podem pensar que ajustar a altura da cabeça de corte é suficiente para alterar a posição do foco. No entanto, este não é o caso. A distância entre o bico e a peça (altura do bico) permanece constante em torno de 0,5 a 1,5 mm durante o processo de corte, o que significa que a cabeça de corte não pode ser elevada ou abaixada para ajustar o foco.
Além disso, a distância focal da lente de foco não pode ser alterada, portanto não pode ser usada para ajustar o foco. A única maneira de alterar a posição do foco é alterando a posição da lente de foco. Se a lente de focagem for baixada, a posição de focagem também será baixada e vice-versa. Este método de ajuste de foco é realizado usando um motor para movimentar a lente de foco para cima e para baixo, permitindo o foco automático.
Outra forma de obter foco automático é usar um refletor de curvatura variável ou lente ajustável colocada antes do feixe entrar na lente de foco. Ao alterar a curvatura do refletor, o ângulo de divergência do feixe refletido é alterado, alterando assim a posição do foco, conforme ilustrado na figura.
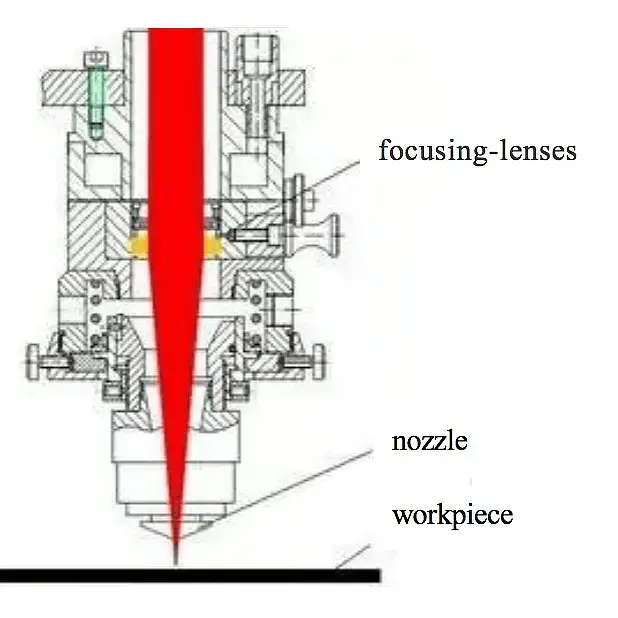
Com a função de foco automático, a eficiência das máquinas de corte a laser pode ser significativamente melhorada. O tempo de processamento para chapas grossas pode ser bastante reduzido, pois a máquina pode ajustar rápida e automaticamente o foco para a posição mais adequada para peças de diversos materiais e espessuras. Isso resulta em maior produtividade e cortes mais precisos.
3. Localização automática de bordas
Conforme mostrado na ilustração, quando uma folha é colocada sobre uma mesa, se estiver inclinada, pode resultar em desperdício durante o processo de corte. Contudo, se o ângulo de inclinação e a origem da chapa puderem ser detectados, o processo de corte poderá ser ajustado para corresponder ao ângulo e à posição da chapa, reduzindo assim o desperdício.
Para resolver isso, um recurso chamado “localização automática de bordas” foi desenvolvido. Quando ativado, o cabeçote de corte começa no ponto P e detecta automaticamente três pontos nos dois lados verticais da chapa, P1, P2 e P3, e então calcula o ângulo de inclinação (A) e a origem da chapa.
Graças a esta função, a eficiência da máquina é melhorada, pois elimina a necessidade de ajuste manual da peça, o que é uma tarefa demorada, principalmente considerando o peso da peça (centenas de quilogramas).
Uma máquina de corte a laser de alta potência é um sistema complexo que combina luz, maquinário e eletricidade, e geralmente apresenta complexidades sutis. Vamos dar uma olhada mais de perto nesses aspectos sutis.
4. Perfuração concentrada
A perfuração concentrada, também conhecida como pré-perfuração, é um processo separado das funções da máquina.
Ao cortar chapas mais grossas com laser, cada contorno do processo de corte passa por duas etapas: perfuração e corte.
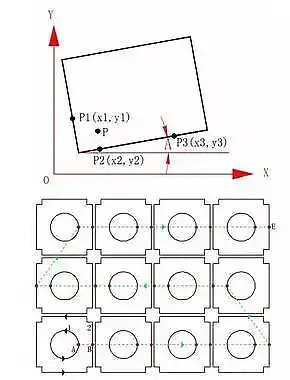
Processo convencional (perfuração do ponto A → perfil de corte 1 → perfuração do ponto B → perfil de corte 2 →…).
A perfuração centralizada envolve a execução do processo de perfuração em toda a chapa de aço de forma centralizada antes de prosseguir com o processo de corte.
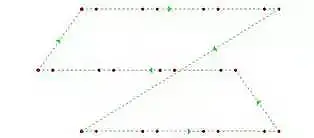
Processo de perfuração concentrado (perfuração completa de todos os contornos → retornar ao ponto inicial → cortar todos os contornos).
O comprimento total do caminho da máquina é maior quando se utiliza perfuração concentrada em comparação com métodos de usinagem tradicionais.
Então, por que é usado o piercing centralizado? Um dos motivos é evitar o superaquecimento.
Durante o processo de perfuração em uma placa grossa, o calor se acumula ao redor do ponto de perfuração. Se o corte for realizado imediatamente após a perfuração, poderá ocorrer superaquecimento.
Com o processo de perfuração centralizado, o calor tem tempo suficiente para se dissipar antes que o corte seja realizado novamente após a conclusão de toda a perfuração. Isso ajuda a evitar o fenômeno de superaquecimento.
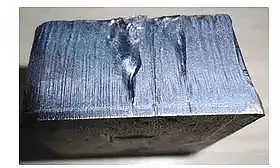
A perfuração centralizada pode aumentar a eficiência do processamento. Atualmente, ainda existem muitas máquinas de corte a laser que não possuem foco automático.
Ao cortar chapas grossas, os parâmetros do processo (como modo laser, potência, altura do bico, pressão do gás auxiliar, etc.) são diferentes durante as etapas de perfuração e corte. A altura do bico é maior durante a perfuração do que durante o corte.
Com processos tradicionais (por exemplo, perfuração do perfil 1, depois corte do perfil 1, depois perfuração do perfil 2, depois corte do perfil 2 e assim por diante), o foco do feixe de laser deve ser ajustado manualmente para a posição ideal de corte, a fim de garantir qualidade e eficiência. Este ajuste manual pode ser um pesadelo porque o foco deve ser alterado da posição de perfuração para a posição de corte várias vezes ao longo do processo. Como resultado, o tempo de perfuração é maior porque o foco não está na posição ideal.
No entanto, com a perfuração centralizada, o foco pode ser ajustado primeiro para uma posição de perfuração adequada. Após a conclusão da perfuração, a máquina pode ser pausada e a posição de foco pode ser alterada para a posição de corte ideal. Isto pode reduzir o tempo de perfuração em mais da metade, melhorando significativamente a eficiência. Se necessário, outros parâmetros do processo podem ser ajustados ou alterados entre perfuração centralizada e corte (por exemplo, ar e onda contínua podem ser usados para perfuração, enquanto oxigênio pode ser usado para corte, com tempo suficiente para completar a troca de gás entre eles).
A lente de foco é frequentemente chamada de eixo F. É possível chamá-lo de “zoom” do eixo H (Mão) se o zoom manual for usado para perfuração e corte centralizados.
O piercing centralizado também apresenta riscos. Se houver uma colisão durante o corte que faça com que a folha se desloque, a parte não cortada poderá ser desperdiçada. Este processo requer o apoio de um sistema de programação automática.
5. Mmicro-conexão
Durante o processo de corte a laser, a folha é fixada por uma barra de suporte serrilhada. Se as peças cortadas forem muito pequenas, podem não passar pela abertura da barra de suporte. Se forem demasiado grandes para serem suportados pelas barras de suporte, podem ficar desequilibrados e empenados. Isto pode resultar numa colisão da cabeça de corte a alta velocidade, causando paragem ou danos na cabeça de corte.
Este problema pode ser resolvido através do “processo de corte de ponte (microjunta)”. Ao programar o corte a laser em gráficos, o contorno fechado é intencionalmente quebrado em vários lugares para que após o corte as peças permaneçam presas ao material circundante sem cair. Essas quebras são conhecidas como “locais de ponte”.
Este processo também é conhecido como “pontos de interrupção” ou “microjuntas” (um termo derivado de uma tradução literal de MicroJoint). A distância da ruptura, que fica em torno de 0,2 a 1mm, é inversamente proporcional à espessura da chapa.
Diferentes terminologias são usadas com base em diferentes perspectivas:
- Com base no contorno, se estiver quebrado, é chamado de “ponto de interrupção”.
- Dependendo da peça, se ela aderir ao material de base, é chamada de “localização de ponte” ou “microconexão”.
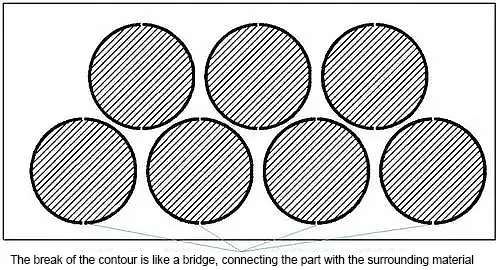
As pontes conectam a peça ao material circundante e o software de programação avançado adiciona automaticamente o número apropriado de pontes com base no comprimento do perfil.
É possível diferenciar entre contornos internos e externos e determinar se devem ser adicionadas localizações de pontes. Os contornos internos (sucata) sem locais de ponte cairão, enquanto os contornos externos (peças) com locais de ponte permanecerão presos ao material de base e não cairão, eliminando a necessidade de classificação.
6. Corte de borda comum
Se os contornos das peças adjacentes tiverem bordas retas e o mesmo ângulo, eles poderão ser combinados em uma única linha reta e cortados apenas uma vez. Isso é conhecido como “corte de borda comum”.
O corte de borda comum reduz o comprimento do corte e melhora significativamente a eficiência do processo. Não exige que as peças tenham formato retangular, como mostra a ilustração abaixo.
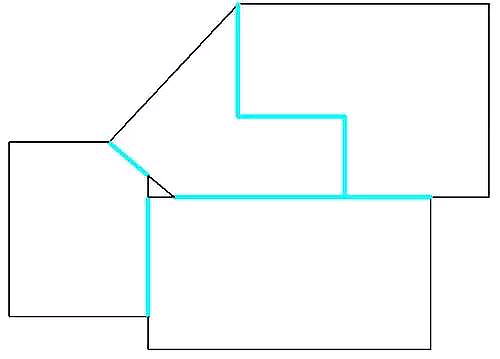
As linhas azuis na ilustração são bordas comuns.
O corte de borda comum não só economiza tempo durante o processo de corte, mas também diminui o número de perfurações. Os benefícios são evidentes.
Por exemplo, se o corte de arestas comuns economiza 1,5 horas por dia, isso equivale a aproximadamente 500 horas por ano. A um custo combinado de US$ 100 por hora, isso equivaleria a US$ 50.000 adicionais por ano.
O corte de arestas comuns requer o uso de software de programação automática inteligente.