Princípio da soldagem a laser
A soldagem a laser envolve direcionar um feixe de laser de alta intensidade sobre uma superfície metálica. O laser interage com o metal, fazendo com que ele absorva a energia do laser e a converta em calor. Esse calor faz com que o metal derreta e eventualmente esfrie e solidifique, resultando em uma junta soldada.
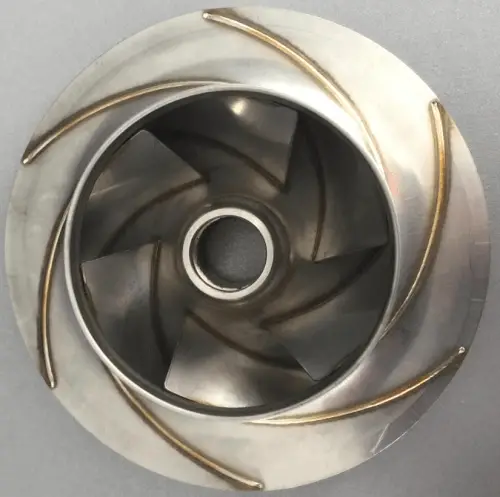
Existem dois mecanismos de soldagem a laser:
1. Soldagem por condução de calor:
Quando um laser é direcionado para uma superfície de material, parte da energia do laser é refletida enquanto o restante é absorvido pelo material. Essa energia absorvida é convertida em calor, o que faz com que o material aqueça e derreta.
O calor da camada superficial do material continua a ser transferido através da condução de calor para as camadas mais profundas do material até que as duas peças soldadas sejam unidas.
Máquinas de soldagem a laser pulsado são comumente usadas para este processo, e a relação profundidade/largura é normalmente menor que 1.
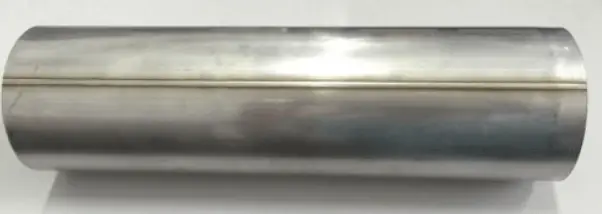
Soldagem de tubos de estiramento – soldagem contínua
2. Soldagem de penetração profunda a laser
Quando um feixe de laser de alta densidade de potência é direcionado para a superfície de um material, o material absorve a energia luminosa e a converte em energia térmica. Como resultado, o material aquece, derrete e vaporiza, produzindo uma grande quantidade de vapor metálico.
A força de reação do vapor que sai empurra o metal fundido, criando buracos. Com a irradiação contínua do laser, os poços penetram mais profundamente no material.
Quando o laser é desligado, o metal fundido ao redor dos poços flui de volta e se solidifica, resultando na soldagem das duas peças.
Este processo é comumente usado em máquinas de soldagem a laser contínua e a relação profundidade/largura é normalmente maior que 1.
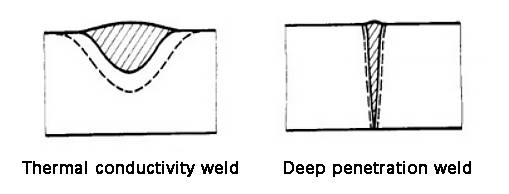
Características da soldagem a laser
- A soldagem a laser é conhecida por sua rápida velocidade de soldagem, grande profundidade de soldagem e deformação mínima dos materiais a serem soldados.
- A soldagem a laser pode ser realizada à temperatura ambiente ou sob condições específicas, e o equipamento necessário é relativamente simples. Por exemplo, quando um laser passa através de um campo eletromagnético, o feixe não se desloca. Além disso, a soldagem a laser pode ser realizada em ambientes de vácuo, ar e alguns gases, e pode até soldar através de materiais transparentes, como vidro.
- A soldagem a laser pode soldar materiais refratários como titânio e quartzo, bem como materiais diferentes com excelentes resultados.
- Com máquinas de solda a laser de alta potência, a densidade de potência é muito alta e a relação profundidade/largura pode chegar a 5:1.
- A soldagem a laser é capaz de microssoldagem devido à sua capacidade de produzir um pequeno ponto focado que pode ser posicionado com precisão. Esta característica o torna ideal para montagem e soldagem de micro e pequenas peças produzidas em grandes quantidades.
- A soldagem a laser pode atingir partes inacessíveis para soldagem de longa distância sem contato, proporcionando maior flexibilidade às operações de soldagem.
- Os feixes de laser podem ser divididos em termos de energia e tempo, permitindo soldagem simultânea em múltiplas estações e soldagem com compartilhamento de tempo, o que melhora muito a eficiência da produção e a utilização do equipamento.
Classificação de soldagem a laser
Existem dois tipos de soldagem a laser: soldagem a laser pulsado e soldagem a laser contínuo de fibra, que são classificadas com base no tipo de laser utilizado.
Aqui estão as diferenças entre os dois métodos:
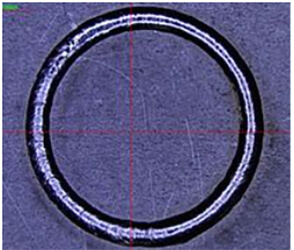
Padrão de soldagem contínua
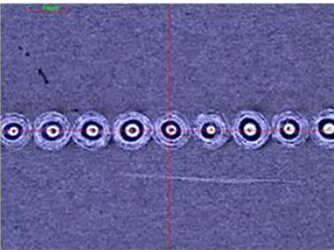
Soldagem por pulso
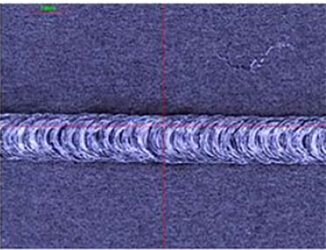
Superposição de ponto de soldagem por pulso
Modo de soldagem | Soldagem por pulso | Soldagem contínua |
---|---|---|
Penetração | Pequeno | Grande |
Consumo de energia | Grande | Pequeno |
Qualidade e aparência da solda | Normal | Bem |
Soldagem a laser classificada pelo método de soldagem a laser
De acordo com a combinação do produto, é dividido em:
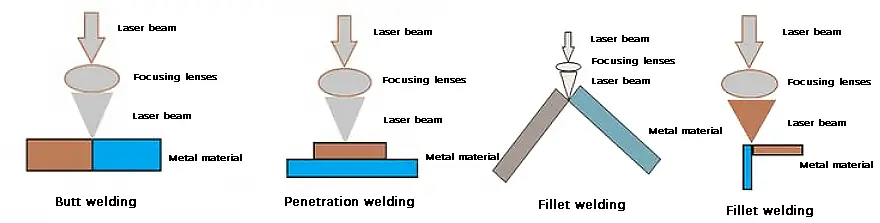
A soldagem de topo normalmente não requer folga ou, se necessário, uma folga inferior a 0,05 mm. Quanto mais fino for o produto a ser soldado, mais rigorosos serão os requisitos para a folga.
No caso da soldagem por penetração, é importante garantir uma ligação firme entre as camadas superior e inferior. À medida que o material da camada superior se torna mais fino, é necessário um ajuste mais apertado para alcançar o resultado desejado.
Comparação entre soldagem a laser e outros métodos de soldagem
Modo de soldagem | Soldagem a laser | Soldagem a arco de argônio | Soldagem por resistência | Brasagem | Soldagem por feixe de elétrons |
Zona afetada pelo calor | Mínimo | Mais | Geralmente | Mais | Menos |
Deformação térmica | Menos | Mais | Geralmente | Mais | Menos |
Ponto de solda | Menos | Mais | Geralmente | Mais | Menos |
Qualidade e aparência da solda | Bem | Geralmente | Geralmente | Geralmente | Preferencialmente |
Se adicionar solda | Não | Não | Não | Sim | Não |
Ambiente de soldagem | Nenhum requisito | Nenhum requisito | Nenhum requisito | Nenhum requisito | Vácuo |
Consumíveis | / | Fio de soldagem ou substituição do eletrodo de tungstênio | Eletrodo de cobre | Solda | Mais rápido |
Velocidade de soldagem | Mais rápido | Lento | / | / | / |
Grau de automação | Alto | Geralmente | Geralmente | Geralmente | Geralmente |
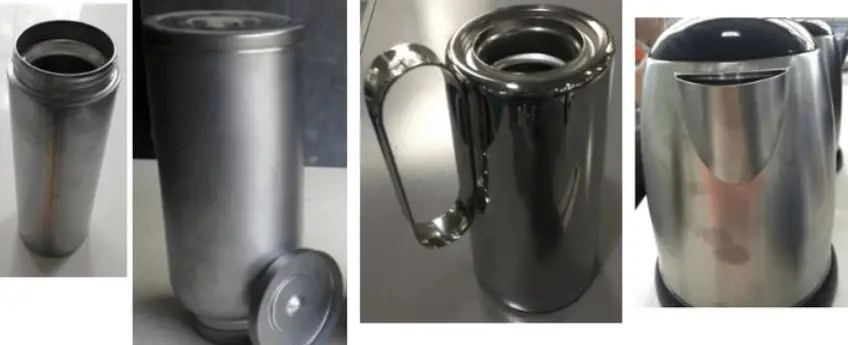
Soldagem pulsada/contínua
Características de soldagem de materiais metálicos
Dificuldade | Aço inoxidável | Morrer aço | Aço carbono | Liga de aço | Níquel | Zinco | Alumínio | Ouro | Prata | Cobre |
Aço inoxidável | fácil | |||||||||
Morrer aço | fácil | fácil | ||||||||
Aço carbono | fácil | fácil | fácil | |||||||
Liga de aço | fácil | fácil | fácil | fácil | ||||||
Níquel | fácil | fácil | fácil | fácil | fácil | |||||
Zinco | fácil | fácil | fácil | fácil | fácil | fácil | ||||
Alumínio | duro | duro | duro | duro | um pouco difícil | duro | fácil | |||
Ouro | duro | duro | duro | duro | duro | duro | duro | um pouco difícil | ||
Prata | duro | duro | duro | duro | duro | duro | duro | duro | duro | |
Cobre | um pouco difícil | duro | duro | duro | um pouco difícil | duro | um pouco difícil | duro | duro | fácil |
Características de soldagem do aço
O aço é uma liga de ferro e carbono, com teor de carbono variando entre 0,04% e 2,3%. Para garantir a tenacidade e a plasticidade do aço, o teor de carbono normalmente não excede 1,7%.
O aço-liga é produzido pela adição intencional de elementos de liga, como Mn, Si, Cr, Ni, Mo, W, V, Ti, etc., durante o processo de fundição. Esses elementos de liga podem ser usados para melhorar as propriedades mecânicas, propriedades de processo ou outras propriedades especiais do aço, como resistência à corrosão, resistência ao calor e resistência ao desgaste.
Classificação por composição química:
(1) Aço carbono:
a. Aço baixo carbono (C ≤ 0,25%);
b. Aço médio carbono (C ≤ 0,25 ~ 0,60%);
c. Aço de alto carbono (C ≤ 0,60% ~ 2,11%).
Quanto maior o teor de carbono, mais fácil será produzir buracos de explosão na poça de fusão.
(2) Liga de aço:
a. Aço de baixa liga (teor total de elementos de liga ≤ 5%);
b. Aço de liga média (teor total de elementos de liga > 5 ~ 10%);
c. Aço de alta liga (teor total de elementos de liga > 10%).
A soldabilidade do aço-liga depende dos elementos da liga, e a soldabilidade semelhante às características de ponto de fusão do aço inoxidável é boa.
(3) Aço inoxidável
O aço inoxidável refere-se a um tipo de aço que é resistente a meios corrosivos fracos, como ar, vapor, água e meios quimicamente corrosivos, como ácidos, álcalis e sal. É dividido em diferentes tipos, incluindo aço martensítico, aço ferrítico e aço austenítico.
O aço inoxidável martensítico é normalmente um aço de baixo ou alto carbono com um teor de cromo variando entre 12% e 18%, e os principais elementos de liga são ferro, cromo e carbono. No entanto, possui a pior soldabilidade entre todos os aços inoxidáveis. As juntas soldadas são frequentemente duras e quebradiças, com tendência a fissuras a frio. Para reduzir a probabilidade de trincas e fragilização, recomenda-se pré-aquecimento e revenimento ao soldar aço inoxidável com teor de carbono superior a 0,1%, como 403, 410, 414, 416, 420, 440A, 440B e 440C.
O aço inoxidável austenítico, por outro lado, refere-se ao aço inoxidável com estrutura austenítica à temperatura ambiente. Este tipo de aço contém cerca de 18% de cromo e níquel e possui uma estrutura de austenita estável quando o teor de cromo está entre 8% e 10% e o teor de carbono é de cerca de 0,1%. Geralmente tem bom desempenho de soldagem a laser. Porém, a adição de enxofre e selênio para melhorar suas propriedades mecânicas aumenta a tendência de fissuração por solidificação.
O aço inoxidável austenítico possui menor condutividade térmica que o aço carbono, com taxa de absorção ligeiramente superior à do aço carbono. A profundidade de penetração da soldagem é apenas cerca de 5-10% daquela do aço carbono comum. No entanto, a soldagem a laser, que possui um pequeno aporte de calor e alta velocidade de soldagem, é adequada para soldagem de aço inoxidável da série Cr Ni. Alguns tipos comuns de aço inoxidável austenítico incluem 201, 301, 302, 303 e 304.
No geral, o aço inoxidável tem boa soldabilidade, com uma poça de soldagem bem formada.
(4) Série 200 – Cr Ni Mn
Aço inoxidável austenítico, série 300 – cromo-níquel
O significado de cada letra:
- CR significa cromo
- Ni significa níquel
- Mn significa manganês
- 1 indica conteúdo de carbono (0 em 304 não é isento de carbono, mas o conteúdo de carbono é inferior a 0,1%, pertencente a baixo carbono)
- 201: 1Cr17Mn6Ni5N, indicando aço inoxidável austenítico 201 contendo 1% de carbono, 17% de manganês, 17% de cromo e 6% de níquel;
- 304: 0Cr19Ni9 (0Cr18Ni9), indicando aço inoxidável austenítico 304 contendo menos de 0,1% de carbono, 18%/19% de cromo e 9% de níquel;
O aço inoxidável 201 contém manganês, o que o torna propenso à oxidação e ferrugem em ambientes úmidos, salgados e mal conservados (embora ainda seja muito melhor que os produtos de ferro e possa ser tratado com trefilação ou polimento após oxidação e ferrugem).
Ao contrário dos produtos de ferro, a camada superficial de galvanoplastia não pode ser tratada após a corrosão.
Por outro lado, o aço inoxidável 304 não contém manganês, mas possui maior teor de cromo e níquel, o que o torna mais resistente à oxidação e ferrugem.
O preço do aço inoxidável 201 é 3-4 vezes maior que o dos materiais de móveis à base de ferro (cromados ou pulverizados), enquanto o preço do aço inoxidável 304 é mais da metade ou quase o dobro do preço do aço inoxidável 201.
A superfície do aço inoxidável 304 é branca com brilho metálico, semelhante a uma placa de plástico.
O aço inoxidável ferrítico, com uma estrutura cristalina cúbica de corpo centrado, normalmente contém 11% a 30% de cromo e não contém níquel (embora possa conter pequenas quantidades de Mo, Ti, Nb e outros elementos).
Este tipo de aço possui alta condutividade térmica, baixo coeficiente de expansão, boa resistência à oxidação e excelente resistência à corrosão sob tensão.
Um exemplo é o aço inoxidável 430.
Comparados aos aços inoxidáveis austeníticos e martensíticos, os aços inoxidáveis ferríticos têm menos tendência a produzir trincas a quente e a frio quando soldados a laser.
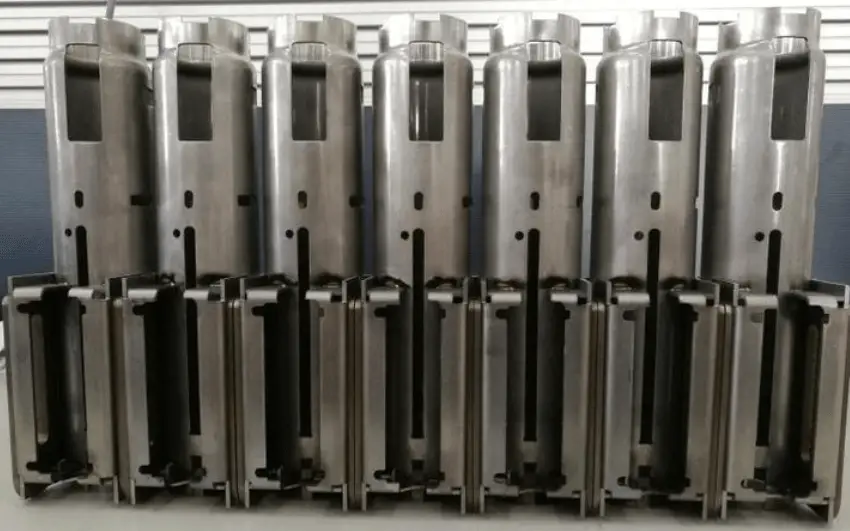
Soldagem da estrutura do sistema de direção automotiva – soldagem contínua
Características de soldagem da liga de alumínio
Devido à alta refletividade superficial e alta condutividade térmica, a soldagem de alumínio requer alta densidade de potência, o que dificulta a formação de uma poça fundida estável.
Muitas ligas de alumínio contêm elementos voláteis como silício e magnésio, levando à formação de muitos poros na solda.
A baixa viscosidade e a tensão superficial do alumínio líquido facilitam o transbordamento do metal líquido na poça de fusão, afetando a formação da solda.
Algumas ligas de alumínio podem apresentar trincas a quente durante a solidificação, o que está relacionado ao tempo de resfriamento e à proteção da solda.
Quanto maior a pureza do alumínio, melhor será a qualidade da soldagem.
A soldagem no alumínio da Série 3 é geralmente aceitável, enquanto a soldagem de alumínio de baixa pureza pode produzir furos de explosão e rachaduras.
Características do processo de soldagem a laser
Existem vários parâmetros de processo que afetam a qualidade da soldagem a laser, incluindo densidade de potência, características do feixe, desfocagem, velocidade de soldagem, forma de onda de pulso de laser e fluxo de gás auxiliar.
1. Densidade de potência
A densidade de potência é um parâmetro crítico na soldagem a laser.
Uma alta densidade de potência pode aquecer rapidamente o metal até seu ponto de fusão em microssegundos, resultando em uma solda de alta qualidade.
A densidade de potência é determinada pela potência de pico e pela área da junta de solda.
Densidade de potência = potência de pico ÷ área de junta de solda
Ao soldar materiais altamente refletivos, como alumínio e cobre, é necessário aumentar a densidade de potência. Isto pode ser conseguido usando uma corrente ou potência mais alta e soldando o mais próximo possível do ponto focal.
2. Forma de onda de pulso de laser
A forma de onda do pulso de laser é um fator crítico na soldagem a laser, especialmente na soldagem de chapas.
Quando o feixe de laser de alta intensidade interage com a superfície do material, 60% a 90% da energia do laser é perdida devido à reflexão, e a refletividade muda com a temperatura da superfície.
A refletividade do metal muda significativamente durante um pulso de laser.
Quando o metal está no estado sólido, a refletividade do laser é alta.
Porém, quando a superfície do material derrete, a refletividade diminui e a absorção aumenta, permitindo uma redução gradual da corrente ou potência.
Portanto, a forma de onda do pulso geralmente é projetada para acomodar essas alterações, como:
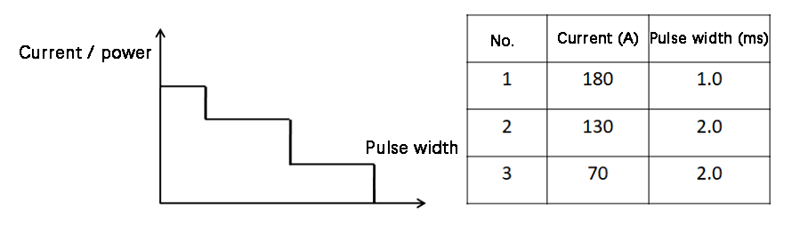
3. Quantidade de desfocagem
O termo “quantidade de desfocagem” refere-se ao desvio da superfície da peça de trabalho em relação ao plano focal.
A posição da desfocagem impacta diretamente o efeito de buraco de fechadura durante a soldagem sob medida.
Existem dois modos de desfocagem: positivo e negativo.
Se o plano focal estiver localizado acima da peça de trabalho, é considerado desfocagem positiva, e se estiver localizado abaixo da peça de trabalho, é considerada desfocagem negativa.
Quando as desfocagens positivas e negativas são iguais, a densidade de potência do plano correspondente é aproximadamente a mesma, mas a forma da poça fundida é diferente.
A desfocagem negativa pode resultar em maior penetração, o que está relacionado com a formação da poça fundida.
Resultados experimentais mostram que quando o aquecimento do laser atinge 50 a 200 μS, o material começa a derreter, formando metal em fase líquida e vaporizando parcialmente para formar vapor de alta pressão. Isso resulta em um spray de alta velocidade de luz branca deslumbrante.
Ao mesmo tempo, o gás de alta concentração move o metal líquido para a borda da poça de fusão, criando uma depressão no centro da poça.
Durante a desfocagem negativa, a densidade de potência interna do material é superior à da superfície, conduzindo a uma fusão e gaseificação mais fortes. Isso permite que a energia luminosa seja transmitida para a parte mais profunda do material.
Portanto, em aplicações práticas, a desfocagem negativa deve ser usada quando é necessária uma penetração profunda, e a desfocagem positiva deve ser usada ao soldar materiais finos.
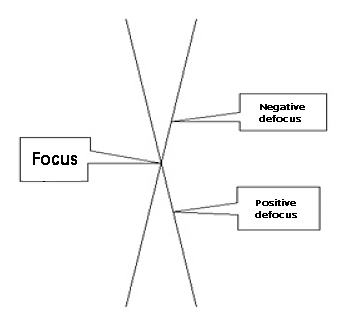
Posição de foco:
O menor ponto com a maior energia pode ser alcançado através da soldagem a ponto. Por outro lado, quando um ponto pequeno é necessário e a energia é baixa, a soldagem por pontos também pode ser usada.
Posição de desfocagem negativa:
Um ponto ligeiramente maior é apropriado para soldagem contínua de penetração profunda e soldagem por pontos de penetração profunda. À medida que a distância do foco aumenta, o tamanho do ponto aumenta.
Posição de desfocagem positiva:
Um ponto ligeiramente maior é adequado para soldagem contínua de vedação de superfície ou situações onde é necessária baixa penetração. À medida que a distância do foco aumenta, o tamanho do ponto também aumenta.
4. Velocidade de soldagem
A qualidade da superfície de soldagem, penetração, zona afetada pelo calor e outros fatores são determinados pela velocidade de soldagem.
A penetração pode ser melhorada reduzindo a velocidade de soldagem ou aumentando a corrente de soldagem.
A redução da velocidade de soldagem é comumente usada para melhorar a penetração e aumentar a vida útil do equipamento.
5. Sopro auxiliar
O sopro auxiliar é um processo crucial na soldagem a laser de alta potência.
Em primeiro lugar, ajuda a evitar que a pulverização metálica contamine o espelho de focagem através da utilização de gás de proteção coaxial.
Em segundo lugar, evita o acúmulo de plasma de alta temperatura gerado durante o processo de soldagem e impede que o laser atinja a superfície do material através do sopro lateral.
Em terceiro lugar, utiliza gás protetor para isolar o ar e proteger a poça de soldagem da oxidação.
A escolha do gás auxiliar e o volume de ar soprado influenciam muito os resultados da soldagem, e diferentes métodos de sopro também podem ter um impacto significativo na qualidade da soldagem.
6. Configuração de fibra óptica e junta de soldagem
Por exemplo, se o diâmetro da fibra óptica for 0,6 mm e a distância focal de focagem for 120 mm com uma focagem de colimação de 150 mm, o diâmetro do foco pode ser calculado da seguinte forma:
Diâmetro do foco = 0,6 x 120/150 = 0,48 mm
A configuração específica é determinada com base no material, espessura, penetração e folga de ajuste do produto.
Recursos do foco longo:
- A distância de trabalho é considerável, o que permite evitar interferências do aparelho, reduz o impacto das oscilações de altura do produto e minimiza a contaminação de respingos nas lentes protetoras.
- Para atingir o mesmo nível de penetração, os requisitos de potência do equipamento serão maiores.